During summer 2017, the authors’ company was invited by BP to bid for the construction of a concrete caisson breakwater protecting an offshore liquefied natural gas (LNG) floating terminal at a water depth of 33 m on the Mauritanian/Senegalese maritime border. As a result of subsequent front-end engineering design (FEED) studies, including 3D model testing, the company was able to reduce the amount of concrete required by 40% compared with the initial design, leading to financial and environmental benefits.
Introduction
The BP Tortue development comprises a subsea production system tied back to a pretreatment floating, production, storage, and offloading (FPSO) unit, which transfers gas to a near-shore hub for LNG production and export.
Phase 1 will provide sales gas production and domestic supply and will generate approximately 2.5 mtpa of LNG to Mauritania and Senegal. The Phase 1 FPSO, in 100–130 m of water, will process inlet gas from the subsea wells located across several drill centers by separating condensate from the gas stream and exporting conditioned gas to a hub, where LNG processing and export will occur.
The hub, 10 km from shore, comprises a breakwater to protect marine operations, including LNG processing and carrier loading. A single floating LNG vessel will condition the gas for LNG export.
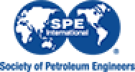