The inaugural SPE Permian Basin Production Management Symposium was a 1-day gathering held at the Midland Petroleum Club in April. The purpose of the event was to share operators’ updates on completions diagnostics, flowback strategies, water management, and artificial lift strategies. Nine Permian Basin operators and three technology companies presented at the symposium, covering case studies in the Midland and Delaware basins. Takeaways discussed below only cover content from presentations that were agreed to be released to the public.
George King of Viking Engineering kicked off the symposium by discussing the necessary geomechanical, geological, and well construction data needed for optimal completion designs. They include:
Locate “sweet spots”
Land wellbores should be in zones of highest quantities of mature organic carbon
Locate and map natural fractures. Are there trends that help or hurt?
Well construction should be suited to all expected (possible?) operations
Need well-to-well communication control (impact, time, remediation, prevention)
Design flexible completions to allow for artificial lift, refracs, long life, maximum up-time, and possible repair of the production casing if casing is compromised
Parsley Energy presented a study on the effectiveness of diverters in the Delaware Basin Wolfcamp Shale (SPE 191600), including opportunities to be cost neutral or lower cost through completion time reduction and testing alternate diversion methods. By using an engineered completion design that investigated the initial fracture geometry, diversion was effective in 85% of the stages in the wells of interest.
The water management session covered several perspectives. Frank Zamora, senior vice president of Premier Oilfield Group, addressed common issues in the Permian such as supply and disposal of water, the chemical changes of produced water with exposure to the atmosphere, chemical interaction of produced water with surface waters that might be blended in before re-injection, bacterial growth and kill studies to establish proper biocide treatment, scaling potential studies, and an assessment of water treatment requirements at surface facilities. To mitigate these issues, operators are using various testing and cost-cutting measures to better understand the formation mineralogy and the downhole sensitivities to re-injection of chemically altered produced water and blends with frac flowback water and possible surface water blends.
Cimarex Energy presented a Delaware Basin case study on its current “frac on the fly” recycling operations, along with a discussion of shortcomings and lessoned learned while working with a dynamic disposal system.
Below is an example of dynamic flow rates and pressures as well as the various learnings covered:
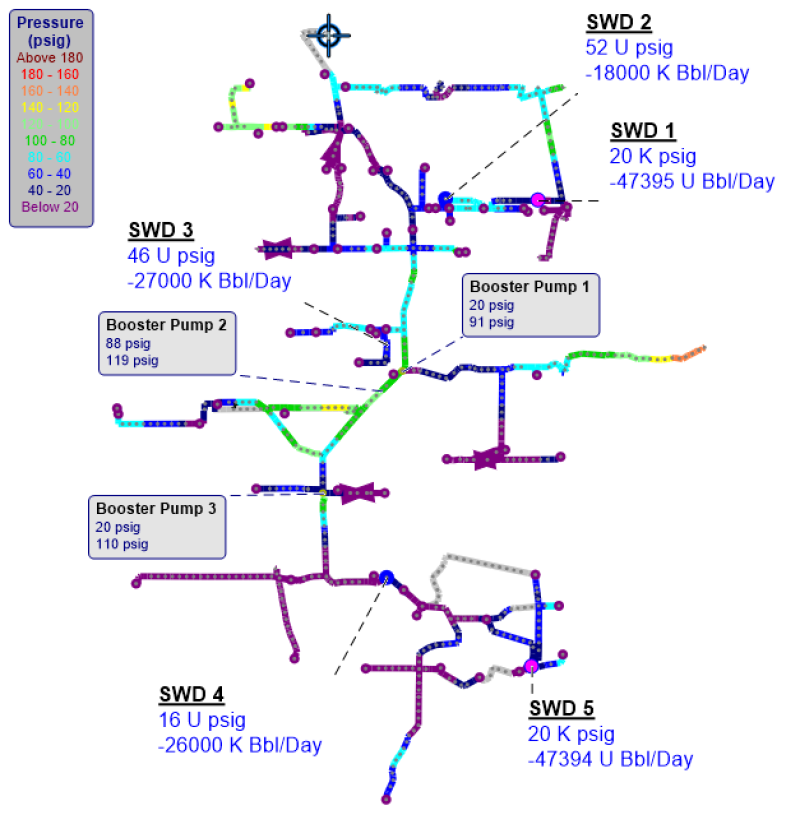
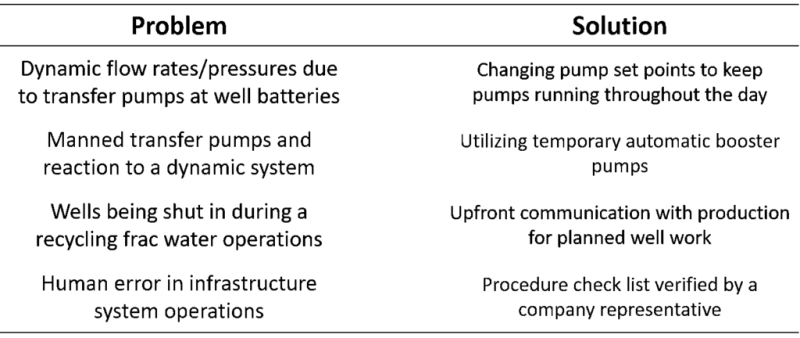
Source: Hudson Baab
The water management session also included a presentation by Karen Olson, director of technology for Southwestern Energy, on managing water use and giving back to the environment. Olson discussed how to optimize frac designs and operations to use less water, a hazards assessment tool for all chemicals used during hydraulic fracturing, advance completions and water treatment technologies, and various conservation projects to create long-term benefit to the environment and communities (SPE 187123-MS). Key components are:
Getting commitment from company leadership and support across all operations
Setting achievable, operational goals
Accounting for all water used
Applying new completion designs and technologies
Increasing the use of alternative, non-fresh water
Supporting research in groundwater protection and water-treatment technologies
The flowback session covered new technologies and drawdown management strategies in the Delaware and Midland Basins. Cole Paxson, facilities engineer at Anadarko, discussed the company’s current approach to flowback in the Delaware Basin, which includes flowing through cyclonic sand traps and sand filtration directly to a permanent tankless wellsite facility. Paxson covered flowback equipment, personnel strategy, choke schedule objectives, and associated best practices.
Below summarizes the concept of the tankless facility and the optimal time to release flowback.
Tankless facility concept:
Well flows straight from separator to gathering
Liquids pumped directly off of the separator
No tanks or flares on location
No trucking of liquids
Elimination of tanks removes settling space for sand
Increases sand separation efficiency needs
Flowback management best practice through tankless facilities:
Release equipment as quickly as possible to minimize rental cost
Identify point where periodic sand cleanouts at separator is more economic than daily rental cost
Utilize sand equipment bypass tests drive this decision
Thermal imaging of separator determines success of bypass
Shad Frazier, vice president of operations at Endeavor Energy Resources, covered his company’s Midland Basin flowback strategies in the Wolfcamp and Lower Spraberry formations. Initial data gathering, especially from diagnostic fracture injection tests (DFIT), helped the team get guidance on flowback strategies for both targets.
Frazier said that despite the initial artificial lift installation for either unconventional target, the critical component of flowback is sand recovery. Flowback is tested by the hour to determine how much sand is being lifted to the surface. If there are heavy sand returns, personnel will cut back on the fluid guidelines until the sand recovery lessens.
The artificial lift session covered ESP applications in the Midland Basin and gas lift applications in the Delaware Basin. Levi Harris, production engineer for Diamondback Energy, and Greg Stephenson, senior engineering advisor in artificial lift for Occidental, detailed root cause failure analyses for ESPs and gas lift applications for Permian operators.
Stephenson discussed the major challenges of artificial lift strategies in unconventional shale reservoirs are to maximize drawdown in an initial high-productivity index zone and decrease the operational expenditures for the life of a well (SPE 190959-MS). Below are some criteria the team used as an initial screening for which artificial lift to use:
High deviation or doglegs
Solids production
Varying production volumes over time
Ability to maximize drawdown
Overall suitability over the life of the well
Operational risk
Safety and simplicity of design
Capital expenses associated with lift method
Anticipated maintenance and/or intervention costs
The presentation covered the following conclusions on the usage of gas lift throughout the life of a well:
Due to the wide variation in production rates with time, multiple lift revisions are required to produce unconventional shale oil wells effectively throughout their producing lives.
Gas lift was found to be the most suitable lift method for producing the subject population of wells, due to its flexibility, tolerance to the anticipated producing conditions, and options for cost-effective deployment in the field.
While annulus flow provides improved production early in a well’s life, it becomes increasingly inefficient as production declines with time, requiring the well to be converted to tubing flow.
To optimize production later in a well’s life, some form of intermittent gas lift will be required.
It is possible to complete wells using readily available equipment in a manner that will enable the transition from one lift method to the next by means of slickline-based interventions.
As production declines, tubing flow gas lift is best achieved using a combination of EC-ported side pocket mandrels and reverse flow injection pressure-operated gas lift valves.
To ensure reliable performance, pay as much attention to the sizing of surface injection equipment and production equipment as to the downhole gas-lift installation.
Effective surveillance can be achieved through a combination of up-to-date well models, real-time data, and standard diagnostic tools.
The ability to perform slickline interventions greatly reduces intervention costs and improves overall project economics.
Participants took years to culminate these learnings within their teams and share with their local peers. With an increase in activity and attention to the Permian Basin, operators and service companies continue to develop and implement new technologies to optimize production strategies. The local section’s study group plans to continue this symposium for the next iteration of learnings in this world-class basin.
References
Greaves, R., Hartstein, R., Lincicome, D., Beck, P., Boothe, M., & Olson, K. E. (2017, October 9). Fresh Water Neutral: Managing Water Use and Giving Back to the Environment. Society of Petroleum Engineers. doi:10.2118/187123-MS
Harpel, J., Ramsey, L., & Wutherich, K. (2018, September 24). Improving the Effectiveness of Diverters in Hydraulic Fracturing of the Wolfcamp Shale. Society of Petroleum Engineers. doi:10.2118/191600-MS
Latif, B., McKenzie, K. S., Rodgers, W. M., Stephenson, G. B., & Wildman, S. L. (2018, August 20). Life-of-Well Gas Lift Installations for Unconventional Resources. Society of Petroleum Engineers. doi:10.2118/190959-MS