The Hadrian-5 prospect in the US Gulf of Mexico was drilled in approximately 7,000 ft of water as one of the first Gulf of Mexico wells drilled after a deepwater moratorium was imposed after the Macondo disaster. This exploration well was permitted under the new regulatory requirements of the US Bureau of Ocean Energy Management, Regulation, and Enforcement (BOEMRE). In addition to well-design regulations, BOEMRE required operators to calculate a worst-case discharge scenario and to develop containment plans for that scenario. The well was drilled and evaluated in a safe manner with no significant incidents, even though the geologic formations encountered were different than predicted.
Introduction
As a result of the April 2010 Macondo disaster, the US government responded with a moratorium on deepwater drilling, reorganized its regulatory agency, and issued new rules for offshore drilling.
In November 2010, BOEMRE issued the Notice to Lessees and Operators 2010-N10. This notice to lessees and operators (NTL) required operators to certify compliance with all applicable regulations and submit plans to contain a worst-case discharge scenario as part of the drilling permit application.
The Hadrian well is located in Block 919 of the Keathley Canyon in 6,941 ft of water, approximately 220 nautical miles southwest of the shorebase location in Fourchon, Louisiana (Fig. 1). The purpose of this exploration well was to evaluate the potential resource of the subsalt Pleistocene, Pliocene, and Miocene formations. On the basis of seismic data, there were no shallow hazards and no hydrocarbons above the salt structure.
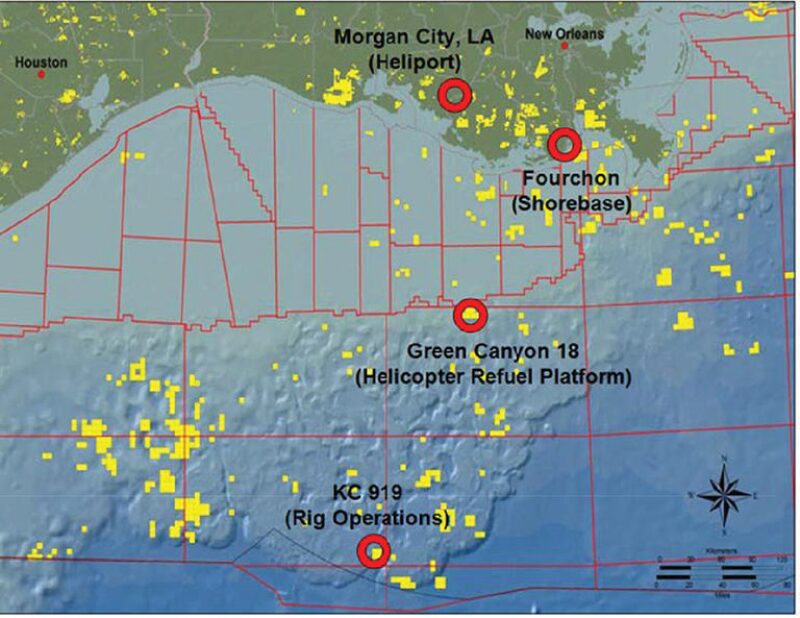
The Hadrian-5 well had an approved permit and a rig on location at the time of the moratorium, but the work was suspended and the rig was released to work on the Macondo spill response. The drill team, in conjunction with the geoscience and regulatory organizations, revised the exploration plan and the application for permit to drill (APD) beginning in July 2010 to meet the new regulatory requirements. BOEMRE approved the revised permit to drill in March 2011.
Planning and Permits
Following the Macondo disaster, BOEMRE issued additional requirements that operators must fulfill before regulatory approval is granted. Additional work was required during the planning and permitting phase to meet these new requirements.
Interim final rules issued by BOEMRE required operators to submit additional details as part of the APD. Blowout preventer (BOP) equipment was one area of focus for the new rules. BOP control system drawings and independent certification of the BOP equipment design and capability must now be submitted. The Hadrian team worked closely with the rig contractor, and an independent agency provided the required documentation.
The BOP stack has six ram-type preventers rated for 15,000 psi and two annular preventers rated for 10,000 psi. The stack has a shear ram capable of shearing and sealing all drillpipe sizes that would be run through it, a casing shear ram capable of shearing the largest diameter casing to be run through it, a variable bore pipe ram, a fixed bore pipe ram, another variable bore pipe ram, and an inverted ram on bottom that serves as the test ram.
The interim final rules now require certification of the well design by a licensed professional engineer. As part of the certification process, the professional engineer reviewed and certified casing, cement, and barrier design. For the Hadrian-5 well, the Hadrian team developed the well design with input from key service providers. The design calculations were reviewed and certified by licensed professional engineers from the operator.
NTL 2010-N10 requires operators to submit plans for containing the proposed well in the event of a worst-case discharge scenario. The Hadrian team worked closely with the Marine Well Containment Company (MWCC) and BOEMRE to develop a capping plan that fulfilled the requirements of NTL 2010-N10.
MWCC provided most of the subsea equipment, including a capping stack (Fig. 2), for the Hadrian-5 containment plan.
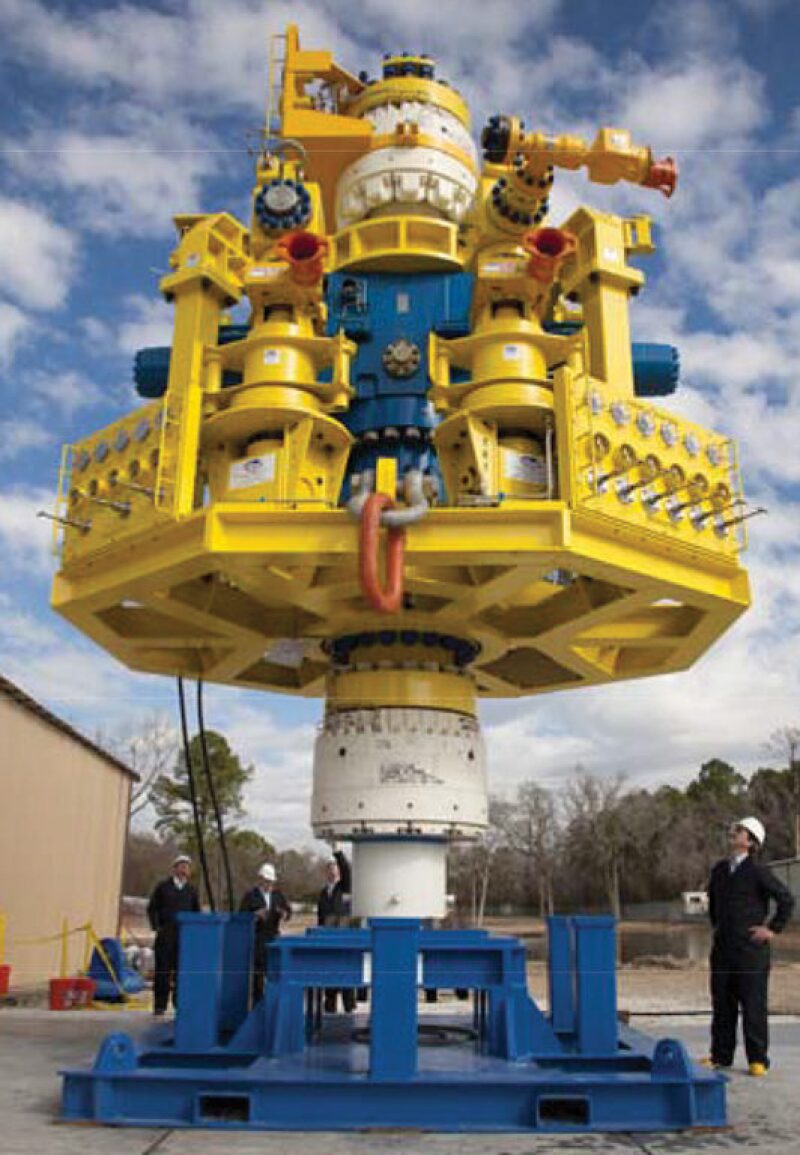
A major component of the Hadrian-5 well capping plan was demonstrating wellbore integrity was sufficient for well capping. If the well’s mechanical and formation integrity are sufficient to withstand the calculated loads with a 1.0 safety factor (assuming American Petroleum Institute or manufacturer ratings for casing and wellhead equipment), then the well design meets the criteria for capping (Level 1).
The Hadrian-5 well design met the Level 1 criteria.
Drilling Rig Features
The Maersk Developer is a sixth generation, dynamically positioned, dual derrick, semisubmersible drilling rig that was used effectively to drill the Hadrian-5 well.
Inverted Test Rams. The rig is equipped with an inverted 18¾-in. pipe ram in the lowest ram cavity. This ram was fitted with 4½×7-in. variable bore ram blocks and packers. This ram was used successfully to test the BOP multiple times during construction of the Hadrian-5 well.
Riser Gas Handler. This well was the operator’s first use of a riser gas handler. In the APD permit, it was agreed that the riser gas handler would be tested and used as designed for riser degassing operations, but, in the event it failed, it would be locked out with no requirement to pull the riser to effect repairs during drilling of the well. The riser gas handler was tested successfully upon initial installation of the riser and operated as designed. The gas handler was used effectively on occasion during well construction to manage gas in the riser.
Remotely Operated Vehicle (ROV) Intervention Capability. Before spud of the Hadrian-5 well, the Maersk Developer ROV intervention hard piping from each intervention panel to all the BOP functions was increased to 1-in.-diameter hard piping. This minimized restrictions and facilitated faster closing of the BOP components with the ROV.
BOP Stack Verification. The BOP was certified by a third-party representative, as required by BOEMRE. Before running the BOP, BOEMRE was notified of the timing for the surface stump test approximately 48 hours before initiating the test. BOEMRE sent three inspectors to witness the test. The BOP was tested successfully nine times on a variety of different drillpipe sizes, as per regulations.
Drilling Program and Execution
The well was spudded by jetting 36-in. structural casing to a depth of 7,348 ft, which was 302 ft below the mudline. A 28-in. tricone drill bit with a mud motor was installed inside the structural casing. After the casing was firmly set, the drill-ahead feature was engaged and the well was drilled to 9,646 ft with seawater and gel sweeps. A string of 22-in. conductor casing was run with a high-pressure wellhead and was landed in the low-pressure wellhead.
The objective of the next section was to drill a 17½-in. hole into the top of salt and set casing in the salt formation. The 13⅝-in. casing was set approximately 500 ft below the top of salt.
A 12¼-in. bottomhole assembly (BHA) was used to drill below the 13⅝-in.-casing shoe. After drilling approximately 2,000 ft of salt, an overpressured oil zone was encountered, resulting in an influx to the wellbore. This was quickly detected by the pressure-
detection team and rig crew, and the well was shut in with the BOP.
This section was redrilled with a 12¼×14¾-in. hole opener assembly to a depth of 14,797 ft, or approximately 650 ft below the oil zone. An 11⅞-in. liner was run and cemented back to the 13⅝‑in. casing.
A 10⅝-in. pilot hole was drilled below the 11⅞-in. liner to provide an optimum hole size for logging while drilling (LWD) tools. The base of salt was encountered at 15,574 ft, and drilling continued for another 1,500 ft, where an extremely abrupt pore pressure increase was encountered. For the second time, the pressure-detection team and rig crew responded promptly and shut in the well.
A rotary steerable BHA was successful in bypassing the original hole section, and three 90-ft cores were collected. The hole was enlarged with a 10⅝×12¼-in. hole-opener BHA. A 9⅝-in. liner with semiflush connections was run to a depth of 17,020 ft and cemented.
The 8½-in. hole section was drilled and encountered a steady increase in pore pressure as measured with connection gas units (pumps off), shale resistivity decrease, and the LWD formation pressure tool. A 7-in. liner was run and cemented at 18,249 ft.
A 6⅛-in. hole section was drilled to total depth of 19,631 ft. The drillstring consisted of three sizes: 5⅞, 5, and 4½ in. The 5⅞-in. drillpipe was run inside the riser and 13⅝-in. casing, the 5-in. drillpipe was run inside the 11⅞-in. liner, and the 4½-in. drillpipe was run inside the 9⅝-in. liner and the 7-in. liner (as well as the open hole).
Challenges
During drilling operations, the well presented some challenges not typically experienced while operating in the Gulf of Mexico. The Hadrian team and rig crew responded successfully to these challenges.
Narrow-margin drilling proved to be a more significant issue than originally anticipated. As operations progressed, it was determined that the pore pressure experienced below salt was higher than planned, which compounded the challenge.
The well construction was revised to include only liners below the 13⅝‑in. intermediate casing. Structurally, the 13⅝‑in. casing was robust enough to withstand the pressures needed to drill to total depth. Running only liners below the 13⅝-in. casing increased the circulating area around the drillstring and reduced the equivalent circulating density (ECD) while drilling.
The team understood and took advantage of the compressibility effects of the nonaqueous drilling fluid (NADF). NADF is more compressible than water-based fluids and exerts a greater equivalent hydrostatic pressure downhole than recorded at surface. Taking this into consideration, the team was comfortable running surface mud weights at or slightly above expected pore pressures, knowing that the NADF compressibility would provide the extra trip margin necessary to pull out of the hole safely without the risk of swabbing in formation fluids.
Underreaming was used in the tight clearance intermediate hole sections, primarily to improve casing running and the subsequent cement job but also to reduce ECD while drilling these hole sections. In this drilling program, there were no failures with any of the underreamers.
Plug and Abandonment
Hadrian-5 was temporarily plugged and abandoned after drilling to preserve the capability to be re-entered later. Cement plugs were placed across all openhole hydrocarbon zones and across all liner tops, and the final cement plug was placed within approximately 100 ft of the mudline (Fig. 3). BOEMRE now requires a professional engineer to certify the plugging and abandonment plans and procedures. Also, a negative test is required before displacing kill-weight mud from the wellbore in preparation for unlatching the BOPs and riser.
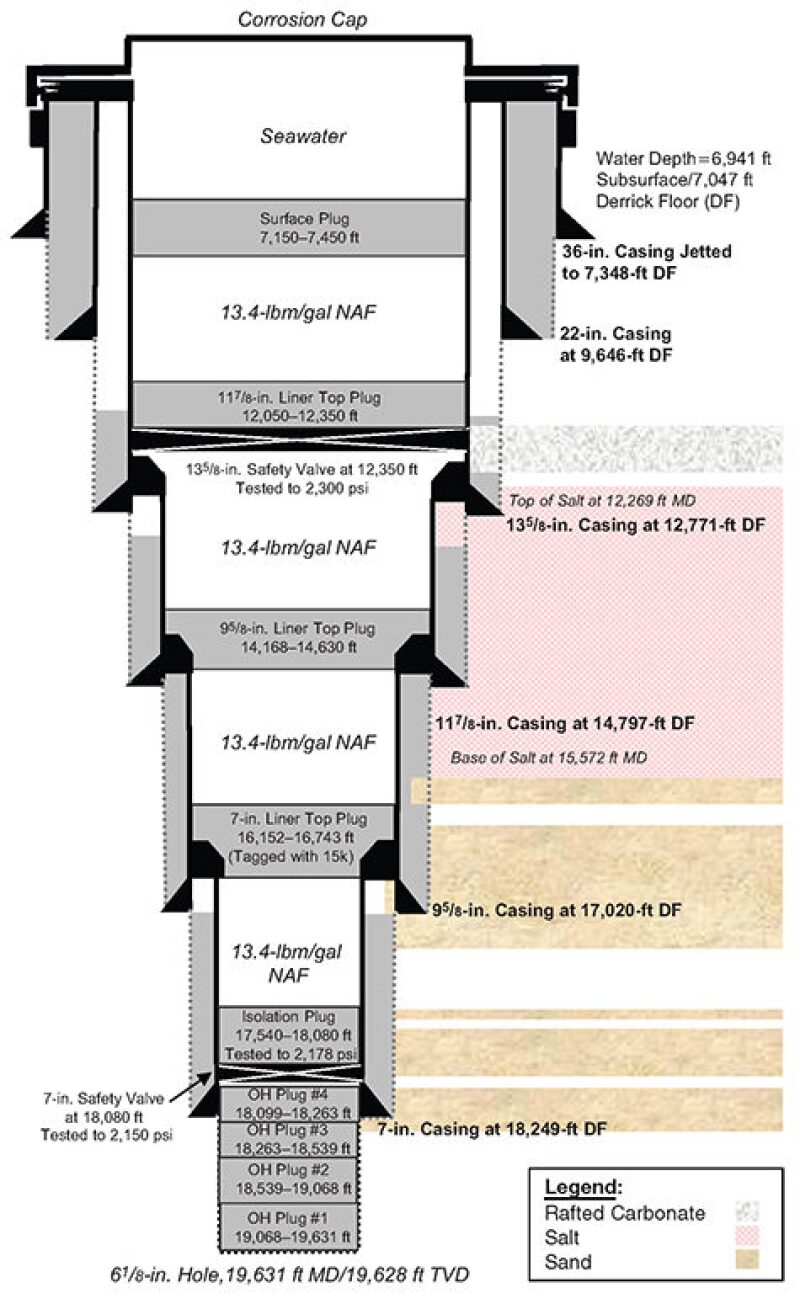
The plan on Hadrian-5 was to displace the well with seawater after a conclusive negative test, so the negative test was conducted by displacing seawater down the drillstring. When the entire drillstring was displaced with seawater, the inverted BOP test rams (designed to hold pressure from above for testing other BOP components) were closed to isolate the hydrostatic pressure exerted by the column of weighted NADF in the riser. Next, the surface pressure was slowly released from the drillstring in stages until it was bled down to zero and returns were monitored through the topdrive to the trip tank. A successful test was observed when the trip tank was static (no gains) over the period of 1 hour, indicating that the downhole barriers were sufficient to counteract formation pressures deeper in the well.
Conclusions
- Early collaboration with the rig contractor and key service providers is critical to developing an effective well plan and obtaining regulatory approval.
- Well-control expectations need to be clearly communicated before the start of the well, and an overall emphasis on pressure detection and response must be maintained throughout the program.
- The industry is capable of safely drilling exploration wells in deep water even when the downhole conditions are not fully known.
- MWCC should be an effective organization to support the industry in the event of a deepwater well-control incident in the US Gulf of Mexico.
- Plugging and abandonment regulations should allow for casing annuli not to be sealed with cement, provided that adequate cement is pumped to cover the hydrocarbon zones and a permanent liner top packer is installed and tested; this will alleviate trapped annular pressure and improve the chances of a successful well capping in the event of a worst-case discharge scenario.
This article, written by Editorial Manager Adam Wilson, contains highlights of paper SPE 154928, "Challenges Associated With Drilling a Deepwater, Subsalt Exploration Well in the Gulf of Mexico: Hadrian Prospect," by Mark C. Moyer, SPE, Scott B. Lewis, SPE, Mike T. Cotton, SPE, and L. Miles Peroyea, SPE, ExxonMobil, prepared for the 2012 SPE Deepwater Drilling and Completions Conference, Galveston, Texas, 20-21 June. The paper has not been peer reviewed.