The COVID-19 pandemic has caused unprecedented circumstances affecting production and facilities. Restrictions in mobility between sites and reduction in manpower challenged the business continuity of several operations. This accelerated the development and implementation of various technological solutions. We can see many examples in the works submitted this year: drone surveillance, inspection robots, digital twins, and automated systems.
The digitalization tendency brought by the fourth industrial revolution continues to be the dominant topic of the works submitted. Approximately 28% were on simulation and modeling, of which one-third used machine learning. A total of 9% addressed intelligent management systems, 5% robotics and drones, 3% 3D printing, and 1.5% digital twins and augmented reality. The main topics addressed were inspection and maintenance (20%), flow assurance (7%), corrosion (6%), drilling (6%), nonmetallic materials (3%), and debottlenecking (2%). A few papers were on clean energy subjects, such as hydrogen energy and wind turbines (2%).
I would like to highlight the following works as promising technological developments for production and facilities: innovative measurement techniques, such as the development of a new adjustable cone meter that adapts automatically to flow conditions of wet and dry gas (paper SPE 207505); improvements to drilling safety, such as the design of a new casing connector that significantly reduces rig time and health, safety, and environmental exposure risks (paper OTC 31075); new developments in piping inspection, such as the combination of direct-response spectroscopy with microwave for inspection of hard-to-inspect piping with coatings and overwraps (paper IPTC 21799); and a very interesting study of triangular vs. circular cross-sectional pipes, which shows that triangular pipes and elbows have significantly less erosion, better heat transfer properties, and reduced slug frequencies for multiphase flow (paper SPE 208101).
In the matter of optimizing production, debottlenecking continues to be a challenge. Whether it is for increase of production needs or for handling greater water cuts from aging wells, new technological solutions are arising to make production facilities increasingly efficient. Paper IPTC 22365 discusses dual-frequency AC/DC desalting technology. It shows a reduction in costs and energy requirements while achieving superior basic sediment and water removal.
One of the topics becoming more relevant is the reduction of CO2 emissions. At least 5% of the abstracts I reviewed addressed lowering CO2 emissions as their main topic. Energy harvesting is an economically interesting way to reduce emissions because the energy consumption of the facility is reduced. The study shown in paper OTC 31724 describes energy harvesting from hydraulic pressure drops as an example of the circular economy applied to oil-production facilities. In this study, the energy and costs savings were evaluated at different pressure-drop points of a gas/oil separation plant. Paper SPE 207096 uses pinch analysis to perform a detailed heat-exchange-network retrofitting study of a crude distillation unit, predicting 8% of energy savings. I sincerely hope that we can see more developments in this area in coming years.
This Month’s Technical Papers
Study Investigates Multiphase Flow in Circular and Triangular Pipes
Adjustable Cone Meter Adapts Automatically to Wet-Gas Conditions
Dual-Frequency Desalting Technology Breaks Bottlenecks, Lowers Cost of Ownership
Recommended Additional Reading
IPTC 21799 Effectiveness of Dynamic-Response Spectroscopy and Microwave-Inspection Technology for Substrate Pipe and Composite Wraps by Rehan Ahmed, Petronas, et al.
OTC 31075 Premium Antirotation Casing Connector With Metal-to-Metal Seal Optimized for High‑Fatigue Performance To Meet Market Needs by Reducing Operational Expenditure and Risk Exposure by Scott Patrick Ellisor, Dril-Quip, et al.
SPE 207096 A Practical Approach to Energy Optimization Using Pinch Analysis: A Case Study of an Oil Refinery by Paschal Uzoma Ndunagu, Honeywell, et al.
OTC 31724 Circular Economy Initiatives at Upstream Surface Facilities by Ahmed Khalid Bu Ali, Aramco, et al.
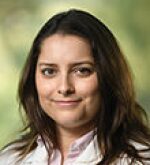
Débora Salomon Marques, SPE, is an associate research scientist for Dow Industrial Solutions in the Netherlands. Previously, she worked as a laboratory scientist in Saudi Arabia. Marques’ research there was focused on oil processing in gas/oil separation plants, particularly the chemical and physical aspects involved in emulsion-mitigation processes. She contributed significantly to advances in nuclear magnetic resonance for the characterization of light-oil emulsions. Marques holds a bachelor’s degree in physics from the State University of Campinas and master’s and PhD degrees in materials science and engineering from the King Abdullah University of Science and Technology. She is a member of the JPT Editorial Review Board and can be reached at dmarques@dow.com.