A major independent crude oil refinery in Asia is processing crude oil in two crude distillation units (CDUs) using an alternating-current (AC) desalting system. Because of inefficient desalting, only 60% desalting efficiency was achieved for each train with subsequent low dehydration efficiency. After a holistic review of the entire desalting operation, the service company recommended upgrading the CDU 1 desalter vessel to dual-frequency technology and adding a new dual-frequency desalter at the second stage of the CDU 2 vessel. The complete paper examines the successful project from early engagement through project execution leading.
Refinery Desalters
Overview of Case-Study Refinery. The refinery was operated with a design capacity of 206,000 B/D through CDUs 1 and 2. CDU 1 included two trains of two-stage legacy AC desalters (Trains 1 and 2). Train 1 operated with 40% of CDU 1’s total flow (60,000 BOPD), while Train 2 operated with 60% of CDU 1’s total flow (90,000 BOPD). The AC desalting system desalted and dehydrated crude oil before feeding the crude to preheated trains.
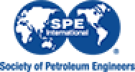