Innovation in oil extraction, particularly around water, has made the concept of “peak oil” a distant memory. New extraction methods propelling the future of oil and gas depend heavily on water as a critical input—shale developments and waterflood enhanced oil recovery (EOR) are two examples. Extraction using water has opened up substantial new hydrocarbon resource plays. However they can produce four times more salty water byproduct than oil. Operators have become experts at reusing this water, in some cases over 95% of it. As a result, water technologies entering the market over the past 10 years have seen little uptake in oil and gas.
Two real opportunities to lower costs and improve production through water technology, specifically desalination, remain. These are important niche markets that benefit from these new techniques:
Shale-gas produced water in disposal-constrained regions, where reuse volumes are less than produced volumes and disposal costs exceed $4/bbl ($25/m3).
Polymer-flood EOR where injection viscosity targets exceed 10 cP, resulting in costly polymer addition that increases with salinity.
In 2019, Saltworks Technologies completed two field pilots, in both niches, with two different technologies. The objective to lower operator cost of production was successfully achieved, in rugged and fully automated plants with over 97% uptime, including periods of unattended operation. This article introduces the two opportunity areas, the two technologies, and summarizes the pilot results.
Pilot 1: Shale-Gas Produced-Water Volume Reduction via a New Class of Evaporator
Shale-gas development involves injecting high-pressure water, sand, and chemicals to “frack” the reservoir. After a short flowback period, underground saline water is produced alongside the hydrocarbons. This produced water varies in salinity from 20,000–300,000 mg/L total dissolved solids (TDS), typically in the 150,000–240,000 mg/L range (for reference, seawater is 35,000 mg/L TDS). Operators are well versed at safely storing, transporting, sharing, and reusing produced water in subsequent fracking. However, when fracking in a region slows but production continues, excess produced water must find a home, often disposal in an injection well, sending the water deep underground. Disposal well capacity is becoming increasingly challenged in certain regions, driving up costs as the water must be trucked to more distant disposal wells.
Two examples of disposal-challenged areas are America’s highly productive Marcellus Shale, centered around Pennsylvania, and Canada’s Western Montney Shale near the Rocky Mountains. Disposal challenges may include “tight” geology preventing high-volume injection or resulting in short disposal well life, regulatory curtailment for reasons such as seismicity, and high costs and risks to develop disposal wells since their capacity and permeability may be unknown until tested and all capital sunk.
A solution is needed to economically and safely reduce the volume of produced water in regions where poor disposal capacity and produced-water imbalance overlap. For shale produced waters less than 60,000 mg/L TDS, lower-cost membrane-based volume reduction options now exist such as those presented in the EOR study below. However, most shale produced waters exceed this TDS, meaning that the water must be “boiled” in higher-cost evaporative processes in order to be concentrated.
Until now two types of evaporators have existed:
Open to atmosphere: Boils water and associated volatiles to atmosphere. These lower-cost, compact evaporators have been trialed, with great regulator and stakeholder concern regarding emissions, plume, and possible radiative particulate release known as “saline drift.” The three failure points for past open-to-atmosphere evaporator trials have been methanol release exceeding Hazardous Air Pollutants (HAP) regulations, saline drift exceeding PM2.5 and PM10 particulate regulations, and sufficient reliability to remain operational.
Closed to atmosphere: Recondenses water with volatiles to prevent atmospheric release; however the water must then be post-treated and find a home. Permitting for release into the environment can be a lengthy process, and closed evaporators are more expensive with less capacity per unit footprint. These evaporators have not succeeded commercially owing to their high cost and poor portability.
The authors developed a new third type of evaporator (trade named AirBreather) with no direct contact of produced-water to atmosphere and no freshwater byproduct. This technology was designed for portability with site mobilization and demobilization limited to 4 weeks. The result is a low-cost evaporator suited for shale that ensures no emissions of concern with no freshwater byproduct to manage. Five substantial oil and gas companies, including one supermajor, have either pilot tested or reviewed the technology, and are investing in full-scale plants after two successful field pilots.
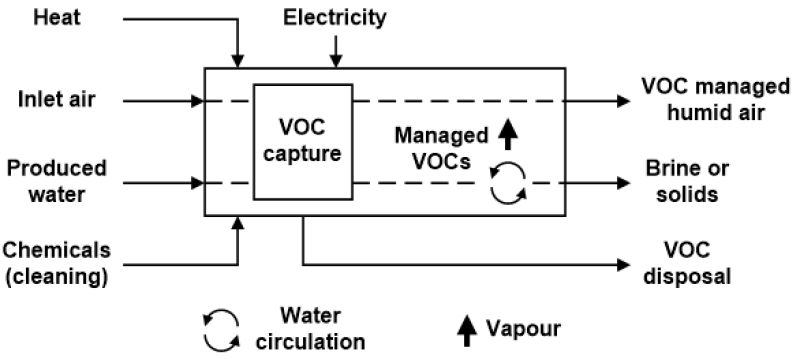
Fig. 1—Evaporator conceptual process diagram. Inlet air does directly contact produced feedwater, removing emissions concerns. Volatile organic compounds (VOCs) and other Hazardous Air Pollutants (HAP) are removed by the VOC management system.
This process (Fig. 1) was developed on the shoulders of the Saltworks’ low-temperature evaporator-crystallizer and altered for use in shale while employing the core technology’s parts bin, corrosion-free fiberglass modules, scaling free design, and intelligently automated systems including self-cleaning.
To prove reliable operations and provide emissions data to regulators, a pilot of the novel evaporator technology was deployed to West Virginia and Pennsylvania to treat a variety of ultra-saline shale-gas produced waters (140,000 to 340,000 mg/L TDS). The only outputs were a concentrated brine near saturation (400,000 mg/L TDS) and clean vapor to atmosphere, which if in liquid form would meet both US and Canadian freshwater discharge standards. Following are key pilot results (Fig. 2):
96% uptime, operating 24/7 during 30-day pilot trial period across two sites.
Operated on produced water with highly variable inlet chemistry, including methanol; benzene, toluene, ethylbenzene, and xylene (BTEX); iron; and normally occurring radioactive materials (NORMs).
Reduced produced-water volume by a factor of 400,000 divided by the input TDS (i.e., 200,000 mg/L TDS produced water achieved a 2X volume reduction).
NORMs remained in the concentrated brine solution which was sent to disposal, and the concentrated saturated brine remained stable during disposal (one must be careful to not mix high-barium and high-sulfate disposal waters at the same facility—the authors have developed online real-time sensors to manage this).
Demonstrated technical feasibility in producing and recovering solids, but this is not seen as economic compared to brine disposal.
Demonstrated zero hazardous air emissions with analytical data obtained through accredited third-party labs.
Economic analysis for full-scale systems demonstrated that today sites with disposal costs greater than $4/bbl ($25/m3) can achieve returns, and with increased roll out this cost will reduce to $2.50–$3.00/bbl ($16–19/m3).
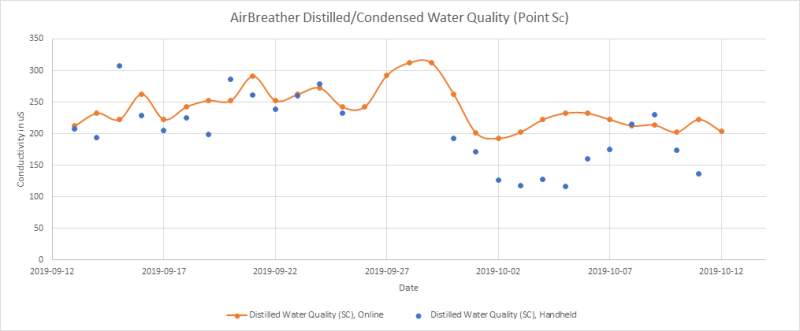
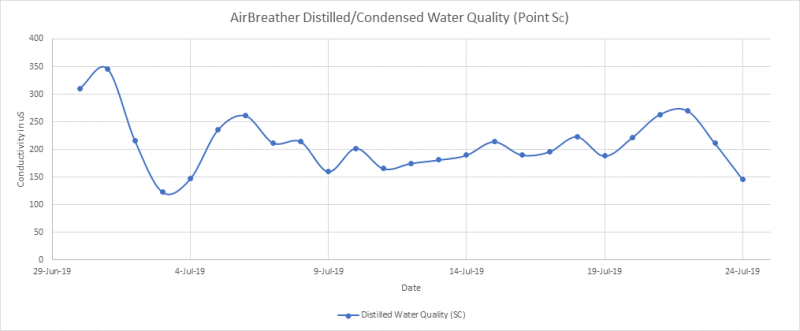
Fig. 2—Online conductivity data obtained during 24/7 pilot operation, demonstrating 99.9%+ reduction in TDS when comparing treated-water quality to produced-water feed.
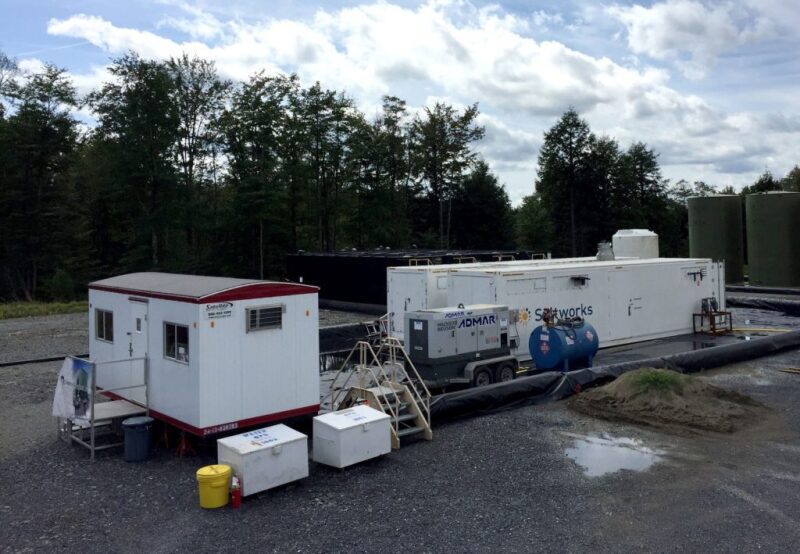
Evaporator pilot operating at Pennsylvania shale-gas site.
Pilot 2: EOR Produced-Water Desalination via a New Class of Membrane Technology
Oil companies are increasingly turning to EOR to boost production from existing fields. EOR involves pumping water underground to push out more oil. This limits environmental surface impacts since well life can be extended, instead of drilling new wells. However, water traveling through the reservoir picks up underground particulate and salts, becoming saline. When produced water is reinjected to recycle it, removing particulate prior to injection can be beneficial to prevent reservoir plugging. In some instances, desalinating and tuning the ionic chemistry of reinjection water can release more oil (for example, to TDS ~2,000 mg/L and with low hardness). In other instances, adding polymer increases water viscosity, preventing it from “fingering” through the reservoir and bypassing the oil it is supposed to push out. Polymer is expensive, however, and its usage increases dramatically with salinity if produced water is recycled.
A membrane-based EOR produced-water field pilot in August 2019 demonstrated a pathway to achieving the following goals: (1) providing high-quality injection water without particulate; (2) desalinating water to ~2,000 mg/L TDS with hardness substantially removed; and (3) reducing polymer consumption through desalination. The following advancements made this pilot possible:
An economic, robust pretreatment system (trade named XtremeUF) usable on any produced water to remove particulate, oils, and grease while leaving largely only soluble organics in the liquid. This is beneficial for both reinjection or ocean discharge (soluble organics can be removed by another step). This technology is a filtration platform developed using commodity low-cost ceramic ultrafiltration elements now emerging, with filtration cut-offs of 0.01, 0.05, 0.1, 0.5, and 1.2 microns. The system’s process and smart controls keep the membranes clean and producing.
Reverse osmosis (RO) and nanofiltration (NF) process plant engineering and controls which prevent insoluble organics from precipitating on membrane surfaces (a common cause of membrane damage in oil and gas applications), coupled with robust automated design suited for oilfield applications.
RO and NF anti-fouling coatings, which repel organics to prevent membrane damage, further reducing risk.
Images below show the pilot plant, a simplified mass balance, and the reduction in dissolved ions between inlet and outlet. Concentrated brine reject was sent to disposal while the desalinated product water was used for polymer makeup and injected (Figs. 3, 4, and 5). This particular client targeted an injection salinity of 2,000 mg/L TDS.
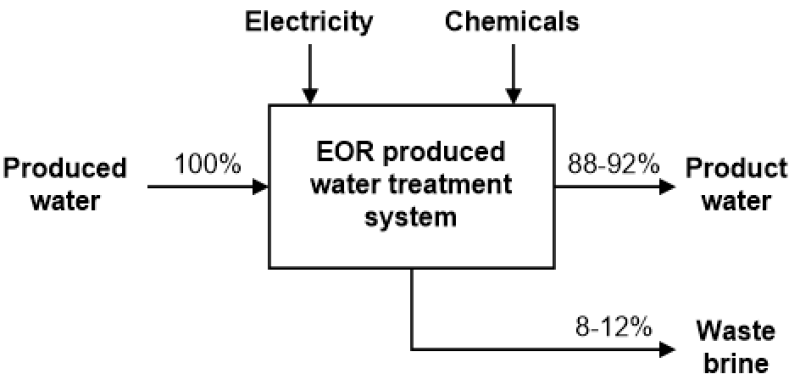
Fig. 3—Process flow diagram of EOR produced-water treatment system (recovery depends on produced-water salinity).
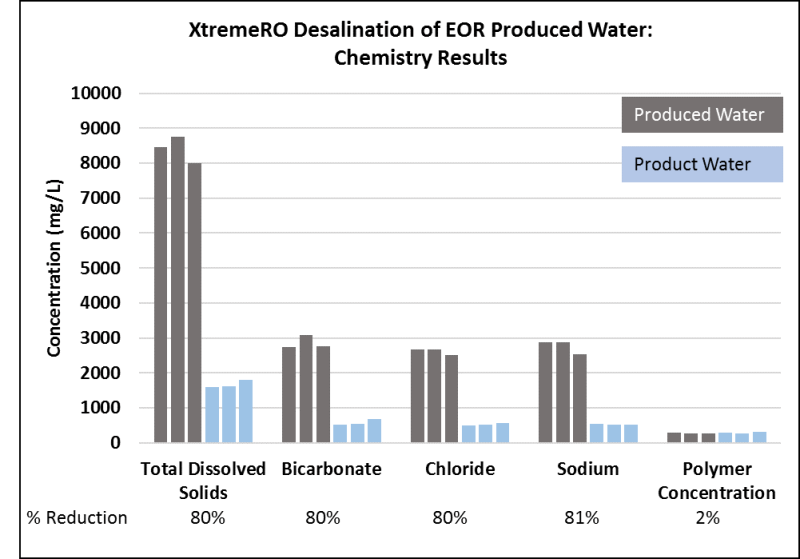
Fig. 4—EOR field pilot chemistry showing reduction of major ions. Residual polymer in the produced water is maintained in the treated water.

Fig. 5—EOR field pilot chemistry showing reduction of additional ions. Hardness and scaling ions such as calcium, magnesium, and barium are significantly reduced.
EOR desalination for increased oil production applies to specific reservoirs, whereby injecting the correct salinity liberates more hydrocarbon. Injection water with too low a salinity can swell certain formations, closing down passages. Conversely, if injection water is too saline or has high hardness, release of hydrocarbon may be curtailed. The EOR desalination system above gives operators a tool to tune their injection water.
The EOR polymer-flood desalination application best fits where viscosity of injected water must be high, for higher viscosity oils. This results in more substantial polymer savings as polymer consumption increases with both salinity and viscosity target. Polymer costs can exceed $19–$31/bbl ($3–$5/m3) injected water, and results have consistently shown a 50% reduction in polymer usage, which pays for the desalination system.
In addition to cost savings, the following additional benefits can result:
Water is recycled in a closed loop, rather than discarded, reducing both water loss to disposal wells and freshwater withdrawal from the environment.
Higher-quality water is reinjected, with lower hardness and fewer suspended solids that could otherwise plug the formation.
Less trucking and greenhouse gases associated with chemical delivery to site and hauling waste produced water offsite.
Although the membrane system pilot was focused on EOR, it equally applies to other produced waters (such as shale gas) provided salinity is less than 80,000 mg/L TDS. Brines can be further concentrated to 130,000 mg/L through ultra-high-pressure RO (1,800 psi) technology.
Conclusion
Two new technical approaches are now available to add value to a number of produced water treatment needs:
Volume reduction of high-salinity waters without harmful air emissions nor the need to manage freshwater byproduct via AirBreather evaporator technology.
Remove particulate, oils, and grease in a lower-cost, smart, ultrafiltration package making use of commoditized and robust ceramic membranes.
Desalinate produced waters using lower-cost membrane systems via RO so long as TDS is less than 80,000 mg/L.
Save operating cost in polymer-flood EOR.
Ben Sparrow is chief engineer and Joshua Zoshi is the COO at Saltworks Technologies. To learn more about these treatment approaches, contact projects@saltworkstech.com.