Carbo Ceramics and Saint-Gobain Proppants are headed for a battle for crush test supremacy. At the recent 2013 SPE Annual Technical Conference and Exhibition (ATCE), the two large proppant makers rolled out a new class of ultraheavy proppant built to stand up to the extreme stresses found on the frontiers of deepwater exploration.
By next year, both companies plan to be mass producing ceramic grains that they said will be the strongest in the market, able to withstand stresses of 20,000 psi or more. The new materials and manufacturing methods used to raise the crush test limit from around 15,000 psi will influence how they produce higher performing proppant for use in lower stress environments.
“On the process side, this will allow us to change everything we do,” said Gary Kolstad, chief executive officer and president of Carbo.
Called Kryptosphere, Carbo’s new product is strikingly uniform in size and shape, with each grain looking like a tiny pingpong ball. The material and the look are a break from sintered bauxite, which has long been used in the most extreme conditions.
At its ATCE booth, Saint-Gobain Proppants played up its new high-performance product, named Titan, which it said could stand up to pressures as high as 30,000 psi.
Both new proppants are made of new materials put together using different manufacturing methods—neither company would offer details. Their customers are operators in places such as the Lower Tertiary trend in the US Gulf of Mexico, where fracturing is required in wells that can go more than 30,000 ft below the mudline in water approaching 10,000 ft.
There were other indications of proppant innovation at the ATCE. Oxane Materials was presenting its first field test information for the proppant it developed using new materials to create particles it says are significantly stronger per pound and were the first to be so uniformly spherical.
Santrol was showing off its recent acquisition, a buoyant coating for proppant that is supposed to help proppant travel deeper into formations. The subsidiary of Fairmount Minerals acquired the inventor of the self-suspending proppant technology earlier this year and has been working to modify the material activated by absorbing water, so it can be used in humid places. Field tests were set to begin in November to see if it could be an effective alternative to the gels used to thicken drilling fluids for delivering heavy proppant.
The coating was tested by Stim-Lab, which found that it did not interfere with equipment, such as blenders. “Frankly, I was pleasantly surprised it has interesting properties,” said Michael Conway, president of Core Lab’s Stim-Lab division. “We will find out soon if it makes a material difference in production.”
The same can be said of other new products. Even when there are large differences in materials, such as sand versus ceramic in a well, in the field, they do not consistently demonstrate the performance differences that would have been expected based on laboratory results, he said.
Given the large differences in output from well to well and the many variables, it is hard to isolate the impact of the proppant used. “Can our customer see the value of the ceramic proppant we are giving them? That is a challenge for everybody,” said Tim Stephens, research and development director of Saint-Gobain Proppants.
Ceramics makers do best in deep reservoirs demanding higher performance—for example, the Lower Tertiary, where the higher cost is justified by reservoir conditions that would crush lower cost options, particularly sand.
There are many other factors contributing to conductivity, including the shape, surface, and size range, which make a difference when measuring conductivity.
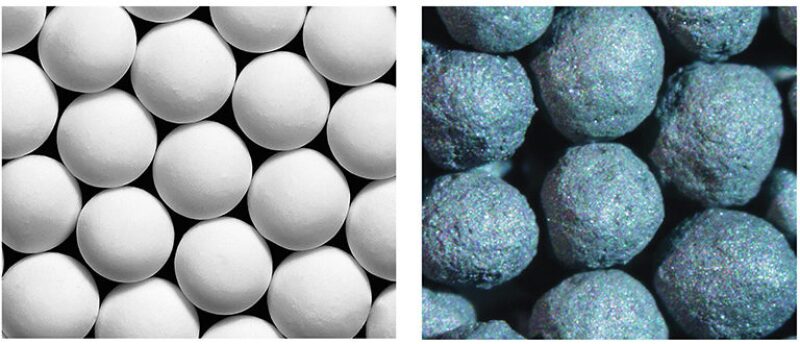
Proppant performance has long been studied by a joint industry consortium that has done testing at Stim-Lab. The group has found that it can be hard to connect cause and effect in the ground.
“In my humble experience, there is far less than we can control about the performance of proppant in a fracture than we would like,” Conway said.
A Clear Need
There is a ready-made market for the new ultrastrong proppants in the Lower Tertiary, where the high-pressure/high-temperature environment demands new completion equipment.
Carbo began the project leading to Kryptosphere after a request by an operator for a proppant that could stand up to the reservoir. “A major wanted a proppant that could deliver twice the conductivity at 20,000 psi,” said Don Conkle, vice president of marketing and sales at Carbo.
Answering that request starting in 2007 required years of work. Carbo first tried to get there by changing the material used. By end of 2009, it was clear that a material change alone would not be enough to reach its goal. That led to 2 more years of work re-engineering the internal structure of the grain. Along with a new material, that change allowed Carbo to reach its goals. Since then, Carbo has been working on mass producing the new proppant at an affordable cost.
Testing by Stim-Lab showed Kryptosphere could exceed the 20,000-psi crush test goal, Conkle said, adding: “We tested it at 22,000 psi and feel comfortable with those closure stresses.”
Saint-Gobain said its ultrastrong proppant has been lab tested up to 30,000 psi. The technology development work dates back to 2003, but product development did not begin until there was customer interest.
Both companies say they will be producing large enough quantities to allow field testing beginning in 2014.
By December, Conkle said Carbo expected to be making 500,000 lb of proppant per month, and that total is expected to rise steadily to 1.5 million lb per month by the end of 2014. Saint-Gobain expected to be making enough of its ultrastrong proppant for field testing by early 2014, Stephens said.
Both proppant formulas likely include alumina, the common name for aluminum oxide, which is used to make aluminum and ceramics.
Conkle said only that the new material has a high alumina content for a proppant, adding that the material and the proprietary production method are known by only a few within Carbo.
Stephens said its new proppant “could be made” of alumina and silica. When asked for specifics, he said only that it is a “patent-protected mineral source.”
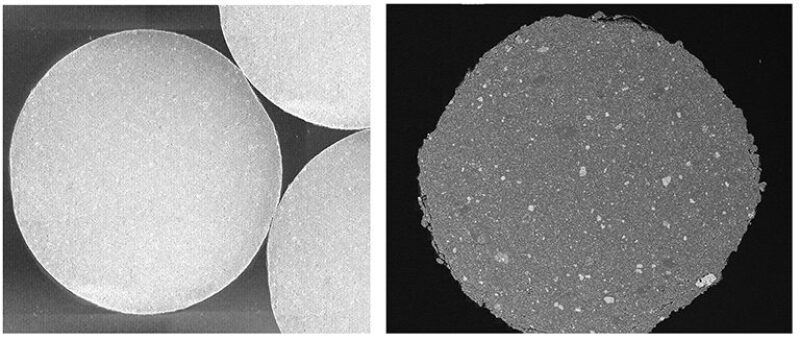
Going Bigger
Creating a proppant that meets the needs of producers in the Lower Tertiary is a technical achievement, but the payoff is limited—up to eight wells will be fractured in 2014 requiring about 40 million lbm of proppant in the Gulf of Mexico, according to Carbo’s presentation.
For high-end producers, one goal is to serve all segments of the market, and the ultradeepwater market is one in which customers drilling wells costing more than USD 200 million are willing to pay for performance.
“Those wells we are looking at are so expensive you cannot afford to have the proppant fail,” said Don Herndon, petroleum technology manager at Saint-Gobain Proppants.
Still, the deepwater market is tiny compared with onshore shale completions, where wells are clustered on pads to increase output from difficult reservoirs. “It (deepwater) is not like running 30-well pads that have 6 million lbm per well, but they are critical wells,” he said.
So both companies expect to apply methods developed for extreme conditions offshore for larger-selling product lines.
For Carbo, extending to the Kryptosphere brand will have a visual impact. The new production method creates uniform grains in a tight size and shape range. A cutaway of the particles shows an even texture without the pore spaces typically found in ceramics.
The spaces inside Kryptosphere represent “1% to 2% of the interior in the new proppant, compared to up to 5% of the space inside Carbo’s current products and up to 25% in low-quality ceramic proppant,” Conkle said.
This can affect performance because more pores increase the potential for fractures that can create small particles, known as fines, which block passages and reduce conductivity.
The uniform look inside and out is also seen in Oxane’s products that also look like tiny white balls.
Stephens said the new production method is aimed at achieving greater strength than Carbo’s newest, and a magnified picture of its interior also shows no pores. But its relatively spherical surface has the look of a rounded rock.
In this battle between smooth spheres and rounded rock, both sides say theirs is better.
“You can show that perfect spheres can generate high contact point mechanisms and can blow up into fines,” reducing flow, Stephens said.
When asked whether a uniformly spherical proppant was more prone to breakage, Oxane’s chief executive officer Chris Coker said, “That is totally false.”
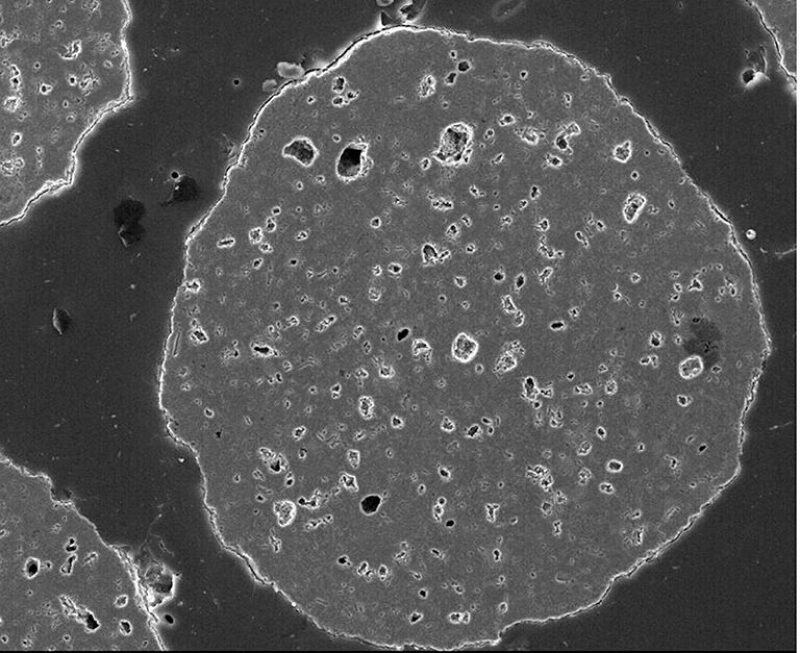
While Conway of Stim-Lab said the stress on a single spot on a sphere should be higher than on a rougher surface, he said the difference is not large.
A more important question, according to Conway, is “Will any operator drilling Lower Tertiary wells be willing to do a controlled comparison test to see if the new, ultrastrong proppants outperform what is now on the market?”
Trade-offs
The new ultrastrong proppants are denser than sintered bauxite proppants that have been used in the deepest wells. Both Carbo’s and Saint-Gobain’s offerings are said to have a specific gravity of 3.9, compared with about 3.6 for sintered bauxite, which has been the strongest proppant.
Higher density makes it more likely to settle out before traveling deep into a fracture network, though particle size looms larger as a variable in the equation used to predict settling.
Both Carbo and Saint-Gobain said they will apply what has been learned to make other lines of proppant stronger. Greater strength per pound is the main selling point for Oxane, whose highest performing proppant, at 15,000 psi, has a specific gravity of 2.9, compared with nearly 3.6 for comparable strength sintered bauxite products.
Next year, Saint-Gobain plans to release a stronger version of its lightweight proppant. The two-layer ceramic particle with a resin coating will have a specific gravity of less than 2, Stephens said.
Frank Syfan, a former SPE Distinguished Lecturer, appeared at the ATCE to offer an introduction on proppant selection. The director of engineering and technology at Go Frac warned against choices based on a single number, such as the rating for a proppant’s maximum closure stress.
The process for finding the proppant offering the best combination of cost and conductivity requires trade-offs for strength, conductivity, price, and logistics. “Ideal proppant does not exist,” Syfan said. “There is no proppant made that is suited for all well needs.”
Fighting for an Edge
Established ceramic proppant makers are rolling out high-performance new products at a time when the market is flooded with low-cost competition.
Explosive growth in proppant demand fueled by unconventional drilling in North America, which caused shortages a few years ago, attracted new competitors from around the globe, especially from China. There are 20 to 30 significant-size proppant makers in China, according to a presentation by Industrial Minerals, which tracks demand for raw materials such as the bauxite used to make proppant. In addition to the many Chinese-owned enterprises, there are international companies such as Carbo Ceramics and Saint-Gobain Proppants.
During the first half of 2013, Carbo reported that the volume of ceramic proppant it sold dropped by 7% from the year before. Its overall proppant sales volume rose on sales of lower-priced resin-coated sand, but that lowered the average price per pound. The company said there was a focus on a reduction in well costs over proppant properties.
The picture changed in the third quarter, when Carbo reported that its ceramic proppant sales volumes jumped 33% compared with the same quarter in 2012. Carbo’s Chief Executive Officer Gary Kolstad said the number reflected gains in its North American market share, and growing use of ceramic proppant in the Bakken and other liquids-rich plays.
Carbo’s international sales were down, in part because of the proppant glut in China, he said. Its top executives frequently criticize the quality of proppant made by its Chinese competitors. The company’s argument is that some Chinese ceramic proppant is weaker because there are large pore spaces inside—up to 25% of the interior space compared with less than 5% of the space inside Carbo’s ceramic proppants, said Don Conkle, vice president of marketing and sales at the company.
The complaints about quality from China are familiar to Mike O’Driscoll, global head of research at Industrial Minerals. But he is also seeing signs of change. Recently, he visited a plant there that was upgrading the equipment used to make and fire the tiny pellets that will be used as proppant.
“What we have seen with other industrial materials is the Chinese are fantastic at spotting markets. They manage to pretty much sell products with minimum specifications to get into the market and get a foothold,” he said. “The end user buys it because it is really cheap, but it is largely ineffective. Then sales tail off and customers buy domestically made products in the US. Then the Chinese come back with better-quality and higher-purity materials.”
Despite the competitive challenges, companies with US operations are aggressively expanding ceramic proppant production capacity, he said. Saint-Gobain is gearing up production at a new plant in Arkansas with a single line able to make 330 million lbm/yr, and is putting in its first line at a plant in Millen, Georgia, with a 250-million-lbm/yr capacity that is expected to start up in 2014, with a second to follow in 2015.
The biggest challenge as ceramic proppant production rises is selling more in the face of competition with sand. The lower-cost material holds roughly 80% of the market, with the rest evenly split between ceramics and resin-coated sand, according to a presentation by O’Driscoll.
Because the price of ceramics is far higher than sand, they need to compete on performance in deeper wells in which the stress inside fractures exceeds the sand’s ability to bear the weight. Even then, it is tough to beat the lower-cost option.
“You end up competing with products that may not be inappropriate for an application,” said Don Herndon, petroleum technology manager at Saint-Gobain Proppants. While that may be a convincing argument for the person designing the fracturing job, sometimes “the engineer cannot convince his management that the cost is worth it,” he said.