In this Q&A, Giovanni Cristofoli outlines the growing role of bp Solutions and advancements in the oilpatch that have assisted the organization in its endeavors.
For the past 3 years, he has been the senior vice president of bp Solutions, though he has been with the company since 2001. He also serves as vice chair for the International Association of Oil & Gas Producers.
He holds a PhD in thermodynamics from the Università degli Studi di Padova.
JPT: How do you approach the development and implementation of operational strategies within bp Solutions?
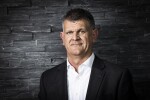
Giovanni Cristofoli: Let me start with the context of what bp Solutions really is. bp Solutions is an organization that was set up in bp around 3 1/2 years ago, and its mission is to partner with the businesses within the company to drive differential performance. We focus on the competitive gap of each of our businesses, whether it's in refining or the upstream business, and really drive solutions to close this competitive gap. We do that in four ways.
Firstly, we have a central team of engineering experts ready to deploy to address complex problems or challenges.
The second thing we do is deliver several end-to-end services that we decided to centralize in Solutions to drive scale, efficiency, and consistency of delivery. Examples are logistics services, site projects, and turnarounds. By centralizing and standardizing these services, we can drive performance and also share best practices for continuous improvement.
The third thing we do is that we own several ways of working, or processes. For example, maintenance, control of work, and the way we deliver site projects.
What do I mean by saying 'we own' these things? I mean we, bp Solutions, own the way of doing it—the processes and standards—and crucially, we help the businesses implement them consistently to deliver the business outcomes we want.
The fourth thing we do is that we own key transformation programs focused on making our performance better. My big learning is that technology brings value; innovation brings value; but you really get a multiplier of value when you combine technology with ways of working.

So, one thing is, you’ve got a problem, and you deploy technology to fix it, because you get value. Quite another is when you take an end-to-end process, for example maintenance or production management, and you digitize it, and you really drive technology adoption to enhance delivery. When you do that, you get a multiplying factor in the business outcome.
In bp Solutions, because we own some of the ways of working, we're well positioned to look at technology to drive that multiplier effect into the outcome we need—be that reducing maintenance costs or improving uptime of our facilities. That's the whole point. We start with a competitive gap that a business may have and build on that.
One good example is our permitting system. To execute work on-site, you need a risk assessment, a plan—what we call control of work. We decided to standardize the way control of work is executed across the upstream, so every facility that we run applies the same process. Then, crucially, we digitized that process on a platform that allows us to do many things, including creating some of the risk assessments and permits remotely.
That allows us to reduce the number of people on site and co-locate them in a collaboration center to work on more value-adding activity. It also gives our managers a better view of what's going on. What are the active work sites? What is the risk? Third thing is it creates a common language. So, if you move from Glen Lyon in the North Sea to Thunder Horse in the Gulf of Mexico, we have the same system. It's easy to share capability. It is also easy to share lessons learned, because you just update one system.
Standardizing the process and digitizing it on a platform also enables us to further enhance usability and efficiency for our teams through mobility. We have now deployed this control-of-work system on something akin to a smartphone or tablet that every technician has. Say you need to close some valves—put an isolation on, as we say. Traditionally, you would close the valve then go back to a computer in the office to update your isolation certificate. Now you can do that in the field using the mobile device, which increases efficiency.
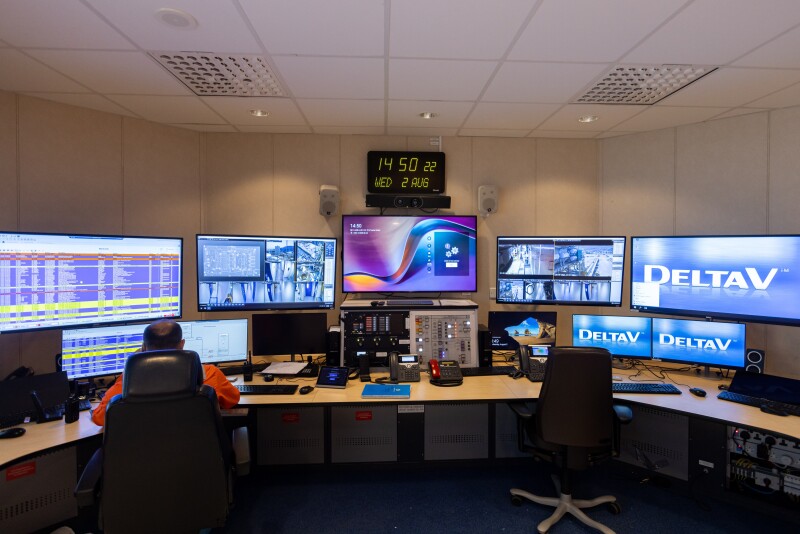
We create thousands of permits every day, and as they are all on a single platform, we’ve got millions of data points we can leverage. The next frontier is to apply artificial intelligence (AI) and machine learning to this rich data to generate insights, trends, and opportunities, helping us better understand near misses or safety issues and other areas of improvement.
Even before applying AI, we have already seen significant benefits of this standardized process implemented on a digitized platform. We have observed our control-of-work-related near misses or incidents reduced by 85% over the past 5 years. This is a great example where Solutions effectively combined an end-to-end process with digital technology to address a business problem, in this case safety, and we delivered a differential outcome.
JPT: How do you handle situations when a project isn't meeting its objectives?
Good question. First, it’s about understanding the problem. We all know that a problem well defined is a problem well solved. Over the past 3 years, we have invested quite a lot in agile ways of working. Traditionally, bp work was organized by department. You had an engineering department, a maintenance department, and for one department to talk to another you went through a manager, and the managers needed to agree before decisions could be taken.
Now, we have designed the organization around agile principles using multidisciplinary squads focused on the business need. It doesn’t matter if your traditional HR reporting lines are to maintenance or to engineering. Basically, when there is a problem, these teams come together in a squad with a mission to resolve a problem. They work together on the problem, and they develop solutions, and by doing that, not only do we increase the clock speed of fixing these problems, but also you get deeper into root causes.
Engineers may have a view, but then you’ve got maintenance, operations, safety specialists—so you have a richer view of the problem by bringing these departments together. Agility is a big game-changer in the way we look at projects that don't meet objectives.
The second piece, bp Solutions was established to support both refining and the upstream, bringing together expertise from both businesses. I think we were amongst the first oil and gas companies to bring together these two departments under one umbrella, if you like.
What we are seeing is a wealth of learning by moving people across teams. For example, at one of our projects in Egypt, we were struggling to start up a plant because of heating-medium-related issues. When we consulted our central team of engineering experts in Solutions, we realized we had an expert on heating medium from the refining business. We deployed their expertise to Egypt and the issue was swiftly resolved.
By bringing our best minds together, we can deploy them to address the biggest challenges in the company and thus achieve great business outcomes. That is the power of centralization at work and is one of the ways bp Solutions delivers its mission.
The final piece is, because we own processes and procedures, it is easy to update them on the back of the learnings from this sort of experience to embed the learning for the future.
JPT: Can you point to one or two advancements that have been introduced over the past decade that have enabled you to do your job better?
Data science, for sure. We have a project going on called Smart-Sized Scope. It is about looking at our maintenance activity and ensuring that it is optimized for the reliability outcome we want. We don't want to do too much maintenance because it can affect safety and cost. We don't want to do too little maintenance because you erode reliability. You need to find a sweet spot.
We'll be working with companies in data science and other sectors to look at the wealth of data we’ve got in the maintenance system and then use machine learning and data science to determine that optimal balance. By doing that, we’ve been optimizing the maintenance build, and taking 1000s of work hours out of the system. That’s an example where data science is really making a big difference.
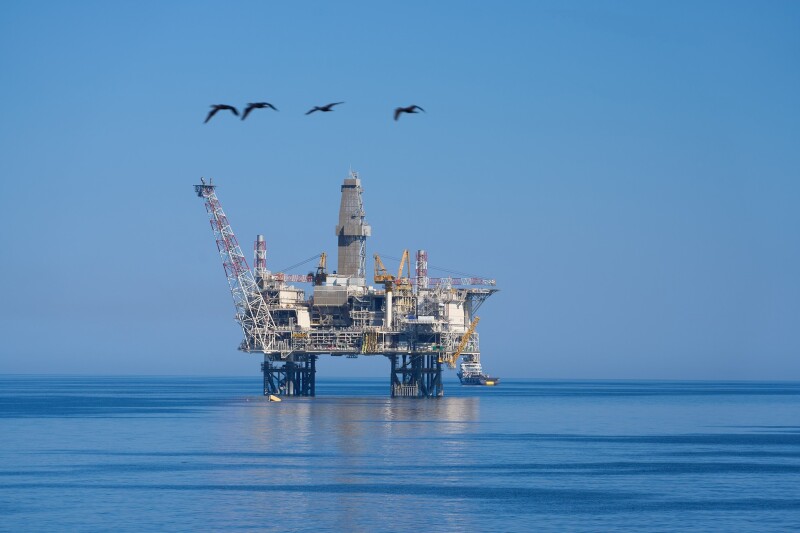
Another big area is remote operations. I'm proud of what we achieved with one of the newest platforms that we started up—the Azeri Central East (ACE) platform in the Caspian Sea. It has numerous features that make it unique: the platform has its control room onshore operated from Baku, and we have a full digital twin of the platform so we can do a lot of the planning remotely. The drilling floor is also highly automated. We also have gas-detection systems that allow us to more effectively monitor the plant and reduce the number of operator rounds required to find leaks and seeps. Remote operations is the other area that has made a massive difference over the past few years with more advances to come.
JPT: Talk a bit about new technology and how bp vets it before implementation. How does bp approach introducing a piece of tech or kit when it is brand new?
The first screening is through the traditional technology readiness level-type of assessment. It's standard industry practice. From when the technology is at idea level you give a score of one, and then as that idea progresses towards maturity and is successfully proven in use, you achieve a score of nine.
What we find is that, like everything, nothing is black and white. So that assessment alone isn’t enough. We also look at things like ‘what if’ scenarios. For example, it is one thing to test a new piece of software, but it’s quite another to spend $100 million on first-of-its-kind subsea equipment for the Gulf of Mexico in 4,000-ft water depth. We ask, what are the consequences of failure from a safety and economic perspective?
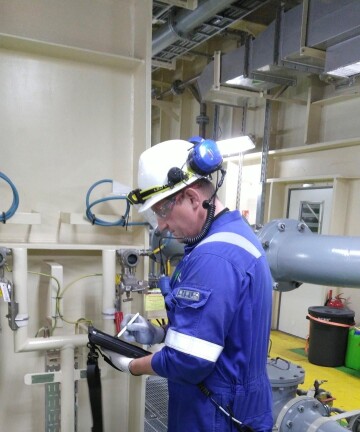
We often look at pilots or test uses where we can to validate the technology and its effectiveness. For example, when we were progressing the Clair Ridge development in the North Sea, we wanted to improve oil recovery, and one way we had studied in bp was to inject low-salinity water into the oil reservoirs—we call this technology LoSal. After completing lab research that showed significant promise, we took the LoSal technology and ran a pilot in a field in Alaska. The pilot worked well and gave us confidence to develop the technology further. We built Clair Ridge, and we got that to work well with LoSal. Then on Argos in Gulf of Mexico, we just replicated that technology—from pilot to implementation to expansion. That's our approach.
JPT: Can you identify some of the key technologies that bp Solutions is utilizing when it comes to sustainability and environmental challenges?
A big area where we are exploring technology is subsea. For example, Kaskida, a project that we recently sanctioned in the Gulf of Mexico, is an important basin for us where we are really expanding our footprint with a sixth operated hub. We're looking at subsea pumping technology. We are looking at subsea electrical valves. Because sending an electrical signal is conceptually easier than sending hydraulic fluid, you need less kit.
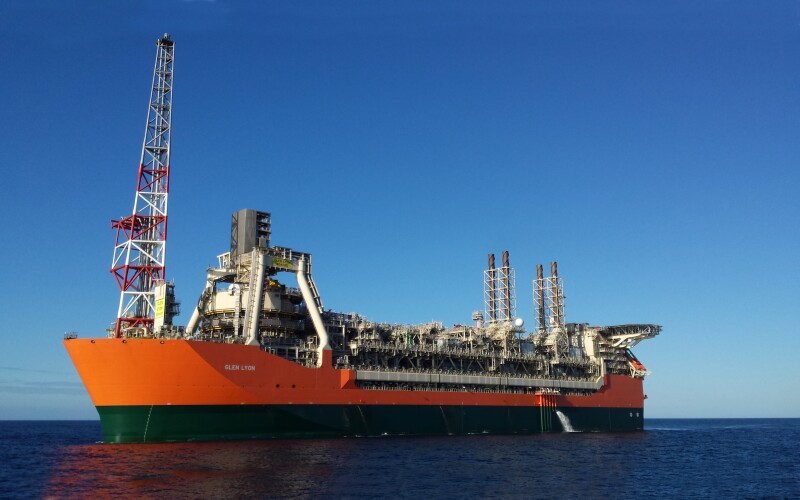
Already in the subsea space, we've been using autonomous vehicles enabled with an array of sensors to carry out inspections, seabed analysis surveys. Vessels without crew means less carbon emissions and less footprint.
Deploying remote and/or autonomous vehicles, digital twins, detection using electrical systems instead of hydraulic systems across subsea is a significant area.
Another area is production management. We’ve seen a big evolution to create a collaborative environment between offshore and onshore. About 15 years ago, we started using cameras whereby the engineering team onshore could talk to the control room offshore and build that relationship of trust. Then you start to see engineers looking at data and helping the facility.
The next evolution, which was probably 5 years ago, was creating a central collaboration center. In Aberdeen and Houston, there is something akin to a control room where we get the data from all rotating machinery equipment across the company. You’ve got a bunch of engineers looking at the data and performance of the equipment, spotting defects before they result in a production impact. This has been immensely valuable on numerous occasions, including on a compressor on a North Sea installation, where we were able to identify a vibration issue and intervene before a trip occurred.
The next evolution is to use AI. Instead of having our engineers monitor this data, we’ll use AI to really pinpoint specific problems before they happen that the engineers can act upon, freeing them up to do the most value-adding work for our assets.
Regarding sustainability, there are two things. One, bp is treating carbon as the fourth fluid. What do I mean by that? Traditionally, in oil and gas, you look at oil, gas, and water—these are the three fluids you manage. We decided to treat carbon emissions as a fourth fluid and treat it with the same rigor as we look at oil, gas, and water. For every oil field, you know what your technical limit in terms of production is, and every day you don't achieve that technical limit, you need to investigate why, and that’s how you push your production.
We're doing the same with emissions now. So, every installation has what we call an ‘installed emissions capacity,’ which is the technical maximum that you should be emitting. Whenever we emit one molecule above the limit, it triggers an investigation with engineers to understand why, and this creates a performance focus. We host and review this data in the same collaboration centers where we monitor equipment for production reliability. Having this integrated view of the asset type is really helping in the emissions space.
The final point, in 2020 we declared that by the end of 2023 we're going to be able to measure methane emissions across our major upstream facilities, and we achieved that. The key piece of technology there was how to measure methane from flares, because flares are never 100% efficient at combustion—you always get some residual methane. How do you measure that?
A company we worked with had software and an algorithm to calculate the amount of methane that leaves the flare uncombusted (Baker Hughes's Panametrics flare.IQ). Then we found that there was a different company that had experimental data in this same area. We connected the experimental company, flare.IQ, and the data. We calibrated the model from the other company, and then we deployed the software to our installation. That's a great example where bp is a bit of a convener of technology. We bring data, software, modeling and our operations together to accurately measure methane.
JPT: What advice do have for petroleum engineering students and young professionals entering and trying to make their way into the industry today?
People like me need to continue to advocate for the industry. I went offshore in the North Sea on the Miller platform for the first time 23 years ago. I remember, I didn't know if I had to take a towel and bed sheets! I was blown away by what I saw.
A couple of trips later, we had a big Heerema vessel install a new module on the platform. It was a 4,000-ton module, and this massive crane lifting it. As a young engineer, you can't not say, 'Wow, we’re really operating at the frontier of what’s possible from an engineering perspective!'
I think we don't do a good enough job of ‘wow-ing’ our young engineers with the things that we do in oil and gas. The first piece is for us to convey that sense of emotion, if you like, to the young engineer. Normally people go into engineering because they want to do exceptional things.
The second piece is—it’s important to talk to people. Get a mentor. Get a role model. Get someone to talk to. I decided to leave Italy to join bp after I spoke with someone who worked in the oil industry for a while, and she told me the sort of careers that are possible. The fact that you can work around the world and enrich yourself culturally, and one day you can be working on a deepwater field and then move to the desert. That, plus having a mentor, can really highlight how you can grow as a person by joining one of the most diverse industries around.
The other thing to bear in mind is that the industry is changing. We have the energy transition, but also, we have the fact that some of the fields we are developing today are far more challenging than in the past. We need innovation. We need creativity. We need people that can think outside the box.
bp just signed a Space Act Agreement with NASA to share technologies and technical expertise. It’s not just pushing pipe on a drill floor. You’ve got to bring your innovation, your creativity. These are some of the things we need to communicate, to give the young students this exciting future to look forward to.
At bp, we created what we call the shadow program, to create more opportunities for people to experience a different career path. There are engineers, for example, that want to become OIMs (offshore installation managers). So, how do you go from being an engineer to being the captain of the ship?
We created a shadow program for people with the right skills, potential, and capability. We give them a job for a year to shadow an existing OIM. Eventually they go through the assessment process, and they need to be successful to proceed, but at the minimum they have got a year where they can really learn and potentially transition.
The other big thing for me is about how diverse our workforce has become. There is such an array of opportunities that young professionals can consider. We have made big efforts to encourage diversity and inclusion throughout our organization. Creating a diverse and inclusive environment is critical, bringing together different people that can contribute diverse perspectives and ways of thinking that come from their different lived experiences.
About bp Solutions
bp Solutions is a global business division created to deploy resources to support bp’s upstream production assets (approximately 50) and seven refineries and to deploy programs to drive safety, process safety, reliability, and efficiency. The division is also charged with delivering end-to-end services (logistics, turnaround, brownfield projects) and defining operating models for low-carbon energies across bp: hydrogen, wind, biofuel, EV.