A fixed polycrystalline-diamond-compact (PDC) cutting element creates an inherent limitation because only a small portion of the diamond table contacts the formation; as the cutter wears or chips, drilling efficiency declines. A research initiative was launched to investigate different methods to enable a PDC shearing element to fully rotate while drilling to increase overall cutting efficiency and bit life. The recent introduction of a new rolling-cutter PDC bit that uses 360° of the diamond edge has delivered positive results in field trials.
Introduction
When drilling with a conventional PDC bit, the percentage of cutter that contacts the formation will vary depending on several factors. However, in most cases, only 10 to 40% of the cutter will be used to actually shear the formation. The remaining 60 to 90% of the cutter is locked into the bit body and remains unused during the run. The resulting wear generates a high degree of frictional heat, which breaks down the diamond bond; the increased temperature then induces more abrasive wear. The mechanical wear combined with the thermal effect damages the cutter’s edge. As wear progresses through the synthetic-diamond table into the tungsten carbide substrate, shearing efficiency is reduced dramatically, lowering the rate of penetration (ROP). A driller’s typical reaction to the reduction in ROP is to increase drilling parameters. This worsens cutter wear further until the ROP drops below an acceptable level, resulting in a short run and a premature trip for a new bit. An analysis of more than 45,000 worldwide bit runs with conventional fixed-cutter-only PDC bits indicated that worn and chipped cutters account for 60% of the dull-grade characteristics reported on bit records.
A finite-element-analysis (FEA) -based software system was used to study the effects of frictional heat at the cutter tip as it engaged and sheared the rock. The study clearly indicated concentrated heat buildup at the cutting edge. Comparing the modeled cutter with an actual dull cutter used in a hard/abrasive application verified the concept.
Developing a Rolling-Cutter Solution
To manage frictional heat at the cutting edge, a new design was developed that would enable the diamond table to fully rotate while drilling. The 360° approach has the potential to solve the localized-wear-flat problem by keeping the cutter’s edge cool and sharp, thereby increasing durability. Engineers investigated several different retention methods and developed a specialized fixed housing that is brazed into the bit blade. The PDC cutter is mounted on a circular shaft and fitted within the housing, allowing cutter rotation. The robust system holds the cutter/shaft assembly securely in the housing for superior reliability.
The rolling cutter’s orientation in the bit blade relative to its contact angle with the formation creates a rotational force that efficiently drives cutter rotation. This side-rake modification ensures smooth and continuous rotation of the cutter in the housing. The side-rake angle is relatively small and does not reduce overall cutting efficiency or hinder drilled-particle evacuation. As the cutter rotates, it shears formation in a continual motion. The resulting wear is evenly distributed around the periphery of the cutter.
Laboratory Analysis
A vertical-turret lathe (VTL) was used to determine the effectiveness of the rolling-cutter concept and evaluate its ability to increase resistance to abrasive wear in hard formations (for a description of the testing process, please see the complete paper).
The VTL was calibrated to measure a variety of forces on the cutter. To evaluate cutter durability and changes in efficiency, multiple passes were performed. To maintain a constant depth of cut during the test, the vertical loading force, or weight on cutter, was increased. This approach is analogous to applying more weight on bit to maintain ROP during an actual bit run. A premium fixed cutter was tested against the new rolling cutter (Fig. 1). The fixed cutter (orange line) required increased weight on cutter to maintain the same depth of cut. Force required increased rapidly from 200 to more than 1,200 lbf at approximately 90 passes. At this point, the test was terminated because the diamond edge was entirely worn and the tungsten carbide substrate was beginning to engage the granite block. The rolling cutter (green line) required a relatively low increase in weight to maintain a consistent depth of cut. Weight started at approximately 200 lbf and was increased gradually to 600 lbf, where it remained virtually unchanged for the duration of the test. A force increase was required only after a significant number of cutting passes. The test clearly demonstrated that the rolling cutter significantly improves shearing efficiency with less force compared with a conventional fixed cutter.

Comparison of Dull Cutters. After the VTL runs, engineers performed a dull-grade analysis to ascertain the amount of cutter wear. After only 90 passes, the fixed cutter had developed a significant wear flat, with damage extending into the tungsten carbide substrate. The test was terminated at this point so that diamond wear could be measured accurately. The rolling cutter was examined after 120, 300, 480, and 540 passes. Examination revealed that the diamond edge had remained relatively sharp and that wear had been distributed evenly around the entire circumference of the cutter as expected.
Modeling Cutter Orientation and Placement
Once the rolling cutter was validated in the laboratory, its design characteristics were incorporated into an FEA-based modeling system to investigate how to extract the maximum benefit from increased durability in a PDC cutting structure. The key goals were to position the rolling cutter to produce the optimal amount of durability, rolling force, and aggressiveness. Next, the software system was used to identify the cutters most susceptible to fail because of abrasive wear. On a conventional fixed-cutter bit, it is common for large wear flats to develop in the shoulder area. The accelerated degradation is caused by the cutters’ high radial velocity and the relatively large volume of rock they remove. The knowledge gained from the analysis was used to position rolling cutters strategically in specific locations to maximize overall bit durability. The precise location and number of rolling cutters per bit depend on several variables, including bit size, blade count, and the nature of the lithologies to be drilled. It was determined that placing rolling cutters in low-wear areas, such as the cone region, would not improve bit performance measurably.
Field Testing—Granite Wash (GW) Horizontal
Engineers selected the GW horizontal play as the primary field-test area. The eastern edge of the GW fairway is concentrated in western Oklahoma, where it is known as the Colony Wash. As the play trends west, the formation is known as the Texas Panhandle GW. The GW is present in several different-age formations and is generally encountered at depths between 11,000 and 12,500 ft. In the area, the term GW is the name applied to the extremely abrasive sandstone created by rocks eroded from the ancestral Wichita/Amarillo uplift. The GW, which produces both crude oil and natural gas, is being developed in many cases with a steerable-motor bottomhole assembly (BHA) to drill a long lateral borehole to increase reservoir exposure.
The initial area targeted was in western Oklahoma’s Colony Wash play, drilled with a 6⅛-in., six-bladed bit with 13-mm cutters on a motor BHA. The 5,000‑ft horizontal section typically required multiple runs. Bits in the area were pulled in generally poor dull condition with excessive cutter wear in the shoulder region (Fig. 2 above).
A 6⅛-in. base design was fitted with the new rolling-cutter technology and run on a motor BHA with four other fixed-cutter PDC bits in a lateral application. The rolling-cutter-equipped bit drilled 20% more footage than the best fixed-cutter bit run at comparable ROP, and it was pulled in better dull condition (Fig. 3).
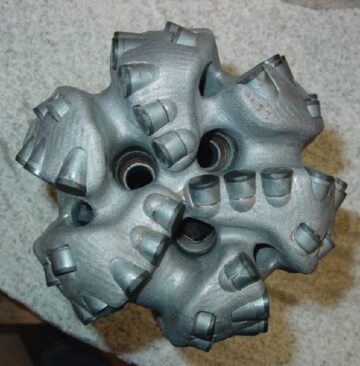
Predicted vs. Actual Wear. To validate the accuracy of the modeled wear patterns, a comparison was made between the predicted abrasion scars and actual cutter damage. The comparison would help evaluate the rolling cutters’ degree of abrasion resistance. In the test bit, Cutters 18, 19, and 20 were placed in sequential order in a similar radial position in the bit’s cutting structure (Fig. 4). The modeling system accurately predicted the extent and position of the wear flat on all three cutters. In the actual bit, Cutter 19 was a rolling cutter. Both the leading cutter (18) and following cutter (20) showed good correlation to the wear-flat prediction from the modeling system. As expected, the rolling cutter (19) showed a smooth and evenly distributed wear around the entire circumference of the cutter. In the center column of Fig. 4, Cutter 19 shows predicted wear expected from a fixed shearing element in this position. Analysis of the dull rolling cutter showed clear evidence of rotation while the bit was drilling.
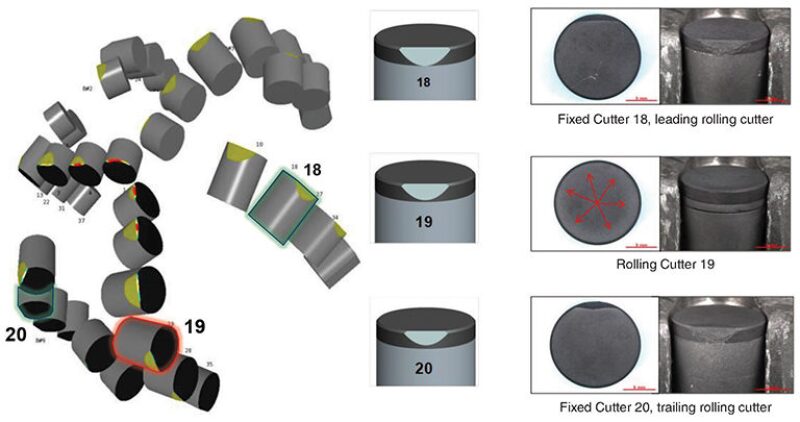
For a description of a second GW field test that also demonstrated the effectiveness of the rolling-cutter bit, please see the complete paper.
Case Study 1 (Single-Lateral Comparison)
Efficiently drilling the lateral-hole section through the abrasive Colony Wash reservoir sand in western Oklahoma creates a unique challenge. The highly heterogeneous formation was causing inconsistent PDC-bit performance while constructing the 6⅛-in. horizontal, thus damaging project economics. A study determined the advantages achievable by extending bit life in areas where poor drilling performance was expected. A detailed forensic analysis showed extensive cutter damage, with abrasive wear being the most common dull characteristic. This cutter wear was causing short runs and frequent trips for bit change-out. An operator was experiencing difficulty drilling the required long lateral section with PDC bits through the abrasive reservoir sand. The difficult formation was causing extensive PDC-bit damage. The damage to the cutting structure was reducing ROP below an acceptable level, forcing the operator to trip for a new bit, in some cases after drilling less than 64 ft.
To solve the problem, a 6⅛-in. PDC bit equipped with seven rolling cutters was run in a GW lateral. The bit successfully drilled out the casing shoe, then made 1,562 ft of horizontal-hole section through the abrasive GW reservoir at a high ROP of 24.79 ft/hr. Seven additional fixed-cutter PDC bits with various blade counts were required to reach lateral total depth at 5,113 ft; however, none were able to match the performance of the bit equipped with rolling-cutter technology. A performance analysis revealed that the rolling-cutter bit drilled 57% more footage than the longest subsequent run of 996 ft and achieved 44% higher ROP compared with the fastest standard-PDC bit. The rolling-cutter bit came out of the hole in good condition and was dull-graded 3-1. Average dull condition of the seven fixed-cutter bits was 6-3.
Case Study 2 (Regional GW Analysis)
Since January 2012, there have been more than 450 fixed-cutter-PDC-bit runs (6⅛‑in.) in the greater GW play. A performance analysis was conducted with this relatively large data set to determine if the rolling-cutter-equipped bits were delivering increased footage and ROP compared with standard fixed-cutter bits. The statistical study showed that 70 bits fitted with rolling cutters drilled 56% more footage than in the 450 offset runs drilled with fixed-cutter bits. A more detailed analysis shows the rolling-cutter-equipped bits achieved 36% more footage at a greater depth than “Bit A” at a 7% faster ROP. Compared with “Bit B” at a similar depth, the rolling-cutter-equipped bit drilled 79% more formation at a 26% faster ROP.
This article, written by JPT Technology Editor Chris Carpenter, contains highlights of paper SPE 166465, “Fully Rotating PDC Cutter Gaining Momentum: Conquering Frictional Heat in Hard/Abrasive Formations Improves Drilling Efficiency,” by Youhe Zang, Yuri Burhan, Chen Chen, Sandeep Tammineni, Bala Durairajan, Siva Mathanagopalan, and Robert Ford, Smith Bits, a Schlumberger Company, prepared for the 2013 SPE Annual Technical Conference and Exhibition, New Orleans, 30 September–2 October. The paper has not been peer reviewed.