A well in the Southern North Sea was shut in due to clay and proppant production. Before it was shut in, it had been producing 1,199 B/D. The challenge presented by the operator was to clean out the well and reestablish production. The operator wanted to boost sustainability metrics and reduce emissions as much as possible.
Adding further complexity to the project, the platform in use was a normally unmanned installation (NUI). This type of platform meant no crew could stay overnight and resulted in several new challenges being considered upfront.
1. Remote monitoring abilities were crucial.
2. A reliable, accurate information flow was key for planning workflow during the day.
3. The work window was reduced to 12 hours per day, so maintenance and the emptying of solids had to be carried out during the day.
4. Limited crane capacity was available for the rig-up and assembly.
The above considerations, coupled with the ability to remove personnel on board (POB), the efficiency of solids handling, and compact footprint, meant the DualFlow 5K PSI desander was selected as the equipment of choice by the operator.
Advance Planning
A 7-week wellbore cleanup was planned to reinstate production while also removing the clay/proppant solids. During this time, the FourPhase team also monitored the well performance.
Understanding the space constraints offshore was key. To kick off the project, a feasibility report was developed to capture basic well data, which included flow rates, oil/gas properties, pressure, temperature, expected solids production, and expected erosional rates. A site visit was arranged to identify laydown areas, pipework routing, connections, utilities, and rig‑up possibilities. Simulations were also carried out to assess the flow and erosional performance and to ensure the planned work was within the operational window of the desander. By creating a 3D rig-up simulation in advance, it was determined that an efficient rig-up could be achieved. This stage also created logistical efficiencies, as accurate measurements for equipment and piping ensured that minimum excess material was shipped offshore. This approach further boosted the ESG metrics of the projects.
Implementation
The desander contains two patented, single-liner cyclones in one unit. As one vessel is isolated and flushed, production continues through the other, delivering a proven separation efficiency of 99.8% and a dynamic range of 20-μm to 10‑mm solids up to 20,000 B/D and 20 MMscf/D. The result is continuous production and better asset management because the data allow early stages of erosion to be managed. Due to its design, it was uniquely able to tackle the specific challenges posed by this project.
The system was monitored by the operator’s nearby control platform, where the well could be shut in if there was an emergency. The Operations and Technology Centre in Bergen, along with the FourPhase Aberdeen facilities, remotely monitored the system’s key operating parameters.
From a POB perspective, the solution removed traditionally labor-intensive manual operations such as valve manipulation and flushing operations. These operations were run automatically or with a click of a button remotely. Removal of such operations directly reduced POB and associated emissions.
To ensure the remote monitoring was a success, it was imperative that there was a secure remote connection between the control platform and onshore. This meant that bespoke interfaces were required. A human-machine interface was adapted to the customer-specific interface. This included setting alarms to alert for key metrics including solids production, flow, vessel pressure, and air supply. The desander’s central control integrates with any customer interface and, in this case, the customer SCADA (supervisory control and data acquisition) system. This integration enabled remote access to view a page of the operator’s SCADA system. During integration, cybersecurity protocols were followed to ensure read-only access.
The latest generation of the system also includes predictive maintenance as standard. A predictive maintenance program is supported through real-time data gathered from almost 600 I/O (input/output) data points to optimize each cleanup operation. The benefit of this feature is that the risk of erosion is further removed, reducing wear and tear on equipment, and boosting safety metrics.
It was anticipated that there was a high solids production from the well, which would require regular solids flushing and, therefore, frequent trips to the platform. It was predicted that at the estimated solids production rate, trips could be required every 5–6 days.
Once installed, the desander removed the need for permanent crew offshore, resulting in a four-man reduction in POB. During the rig-up and commissioning stage, a walk-to-work vessel was positioned alongside the NUI to cater to the needs of the crew. Afterwards, only periodic visits by a FourPhase supervisor were required for flushing and inspection. The 12-hour daily operations window meant that the crew would be shuttled offshore for the vessel flushing /system inspection.
Since the platform was a NUI, the desander would need to be disassembled in Bergen before being transported for mobilization. This was a first for the system. To achieve this, one cyclonic vessel of the unit had to be removed to meet the weight restrictions of the crane (8 tonnes). Once it was lifted onto the NUI, it was then lowered through a hatch and placed in the well-bay area for reassembly by its crew. There was very tight access to the well-bay laydown area, meaning that the compact footprint of the system (2×2 m or 6.7×6.7 ft) was a key reason that the technology was selected.
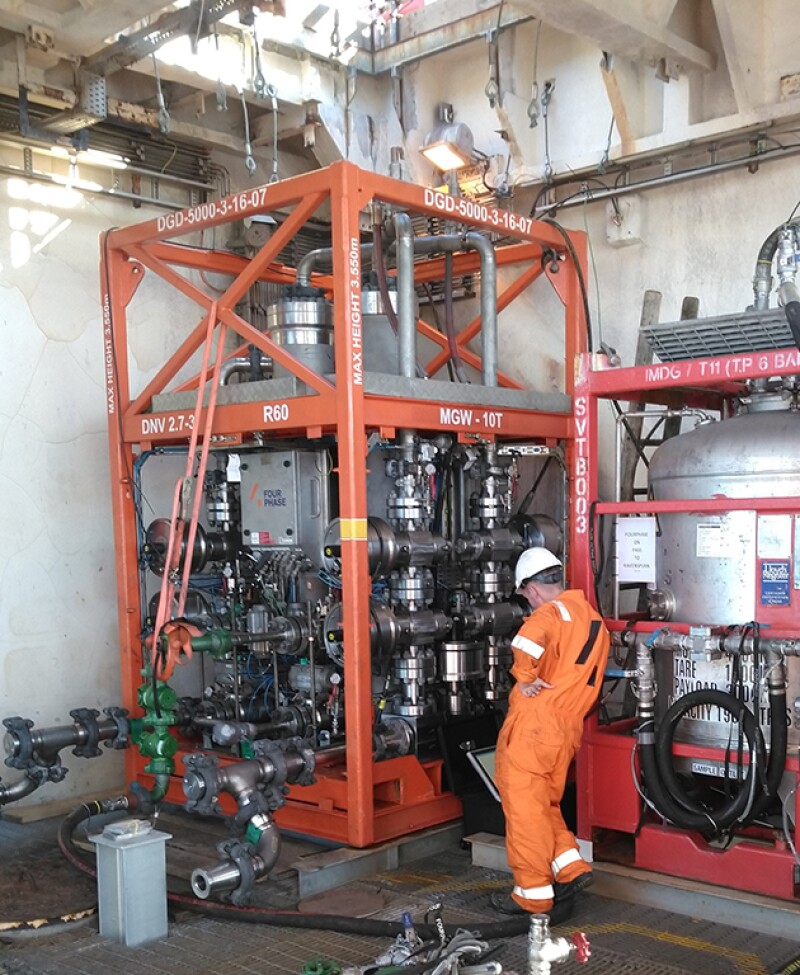
The Result
The system delivered solids-free production flow while also reducing operational costs. It was configured to operate autonomously to remove solids from the production flow, guaranteeing that there were no proppants in the system. Throughout the project, the volume of solids produced was far less than expected. This resulted in no offshore visits to flush the cyclone vessels, thus reducing POB. After 6 weeks, when the well reached a steady state of production, the system was rigged down. The well continues to produce at pre-intervention levels.
A fluid sample taken from the well showed an average particle size of 4 to 100 μm. Over 1,000 hours of remotely monitored continuous production was achieved on the unmanned platform—a first for standalone solids management in the North Sea. By achieving continuous production, the production rate was kept at a higher rate. However, with remote monitoring successfully managed from multiple locations, the headline achievement was a significant reduction in personnel offshore costs and associated travel emissions.
The Next Chapter
The next stage of the project is to further develop the remote monitoring aspects of the system and to deploy it. Remote operations on several platforms are now being planned, both in the UK and Norwegian sectors. The important next step is to integrate third-party systems into the FourPhase ecosystem to permit fully remotely operated production flow recovery. As the first offshore automated solids-management system with remote operation capabilities available on the market, the system has the capability to remove POB completely and be fully remote where the rig’s infrastructure allows. The latest generation of the control system enables remote operation of all FourPhase equipment.
As the industry moves further toward the digitalization of solids management, the technology will open new possibilities with regards to marginal fields and the use of NUIs offshore. The key to these projects’ success is undoubtedly the creation of a secure connection and strong data flow.
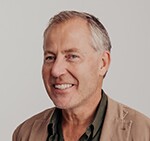
Øyvind Heradstveit is the CEO of FourPhase. He is an experienced mechanical engineer and entrepreneur, with a particular interest in developing a more sustainable oil and gas industry using the power of technology and data. Prior to FourPhase, he worked at Mechanica-Oceaneering and Malm Orstad.