Europe’s largest onshore oil field, the Patos-Marinza in southern Albania, has been given a new lease on life after seeing production soar from 600 B/D just over a decade ago to more than 20,000 B/D this year. The field’s sole operator, Canadian-based Banker’s Petroleum, set up shop in the country in 2004 and has also more than doubled the estimated reserves from 98 million BOE to 220 million BOE. The Patos-Marinza, which holds an estimated 5 billion bbl of oil in place, has undergone a transformation from a heavily polluted oil field with outdated technology to one that exemplifies modern operations and environmental practices.
Chris Thompson, a production engineering manager at Banker’s, said the company has deployed a number of strategies to achieve its production goals. They include the wholesale replacement of existing artificial lift systems, infill drilling with horizontal wells, and the recent initiation of enhanced oil recovery (EOR) pilot programs using polymer and waterflooding. “With the way the field is set up, there seems to be unlimited opportunities,” Thompson said.
From the onset, Banker’s strategy has centered on introducing Albania to heavy oil engineering expertise and modern technologies from Alberta, Canada. Though similar in some ways, there are plenty of differences between the two areas that make the Patos-Marinza a much different operating environment.
For starters, the gravity of the oil is as low as 4 °API and an average of 8 °API. In Canada, oil this heavy would require the use of steam to get flowing. But because the Albanian reservoir is deeper, the higher pressures and temperatures allow the viscous oil to flow on its own into the wellstream.
By using pad drilling, Banker’s is able to tap into multiple horizons at different depths with as few as one and in some cases more than 20 horizontal wells from a single site. Depths for the horizontal wells range from approximately 1,100 m in the shallow end of the field to 1,600 m in the deeper part and have an average lateral section of approximately 600 m in length. The target formations are made up of unconsolidated sands that allow the oil to migrate into the wellstream. This means that unlike a tight shale resource play, in this field hydraulic fracturing is not needed to stimulate the reservoir.
And since the European oilfield service market is not set up to support onshore heavy oil development, Banker’s imports most of its equipment from Canada, which can take months in some cases. So to avoid project delays, the company has made supply chain operations a big focus of its strategy.
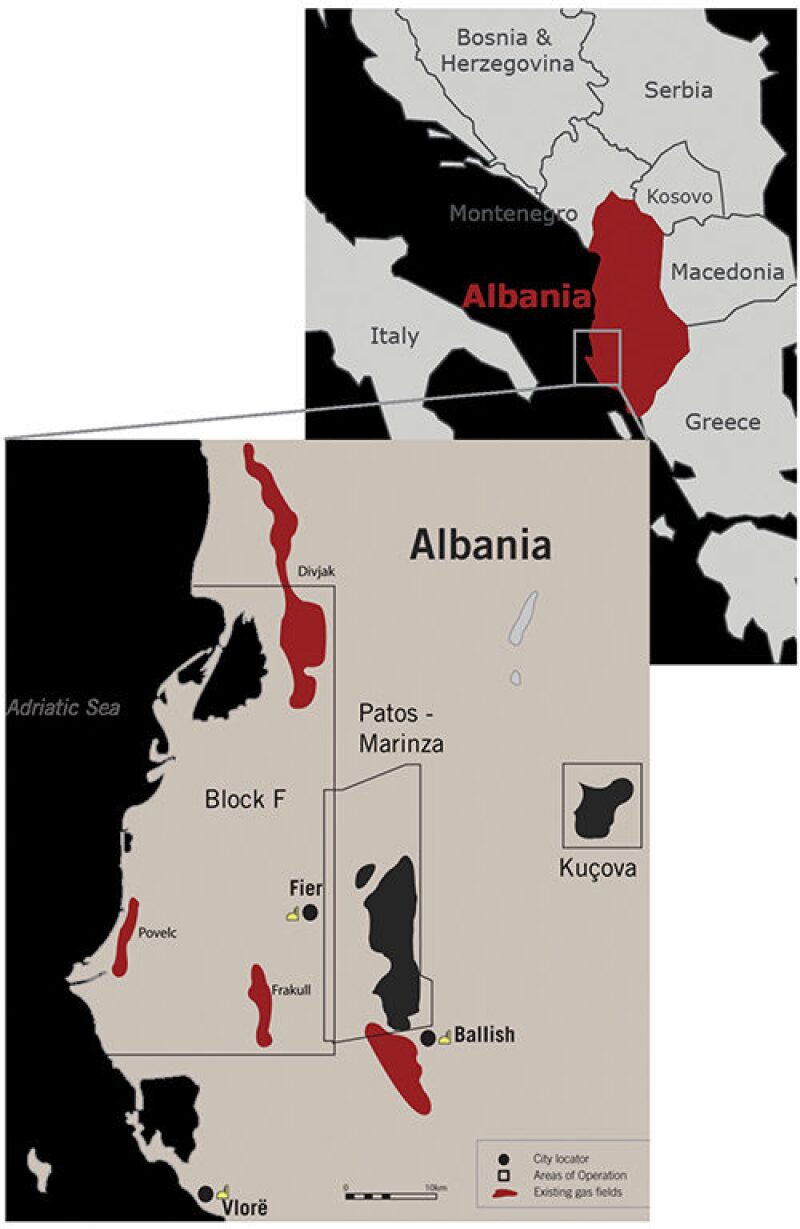
Old Wells, New Problems
The 2,400 vertical wellbores drilled long before Banker’s arrival have been both a blessing and a curse. When it began operating the field, one of the company’s first tasks was to pull out all the older pump jacks and derrick equipment on the producers, clean out the wellbores, and install new progressive cavity pumps. “That worked to an extent,” Thompson said. “We got it up, but of course, when you are working with old wellbores, there are a lot of issues trying to maintain and keep them on production.”
Of the field’s 500 producing wells, only 70 vertical wells are left operating. Due to low oil prices, the company laid down half of its rig fleet at the beginning of the year and with three rigs still running, it expects to complete an additional 80 horizontal infill wells this year. The infill program has been partly guided by the old log data from the vertical wells. Thompson said that since most of them were never surveyed accurately, the exact trajectories of the wellbores are unknown.
“The anticollision portion of the drill plan is the hardest part for the group,” he said. “We get fairly close to them because there are so many out there and as we drill them on, those vertical wells sort of die off as the horizontal wells take over.”
One of the problems with infill drilling near the old wellbores is that many of them are filled with water. This is largely the result of the poor cementing practices of preceding operators that did not sufficiently isolate the water zones from the production zones. In some cases, the wellbores have simply fallen apart, letting water flow in freely.
Thompson said this leads to “extremely high” water cuts in some of the newly drilled horizontal wells. The company has combatted the problem by going back into the older wells and isolating the water producing zones. The oil production was brought back up substantially in the horizontal wells, but the dewatering rates have varied. “The water cuts over time will drop down; sometimes it takes a couple of weeks and sometimes it takes a year plus,” Thompson said.
The company has redesigned its horizontal wells after finding that its original liners were too weak to handle the reservoir pressure. It also learned that the liner’s slot holes were too big and the amount of sand flowing in was overwhelming production equipment.
When they first encountered the sand problems, the engineers debated on whether the larger slots promoted flow by opening up wider channels and if using smaller slots would hold production back. After opting for the smaller 4½-in. diameter slotted liners, the company saw a drastic drop in sand production, which has lowered service costs. “We are getting a little bit of sand but it’s producible and it is not really hurting our inflow performance in the wells, which is the key,” Thompson said.
Because of the high viscosity of the oil, pumps must be placed deep inside the wellbore during the original completion to bring it to the surface. In its early horizontal wells, engineers realized they were placing the pumps too high in the vertical section. This allowed sand to settle and accumulate at the well’s heel, which was impeding optimum production. The pumps are now installed quite a bit lower in the heel section where they are closer to the reservoir and can pump the sand to the surface, keeping the wellbore clean.
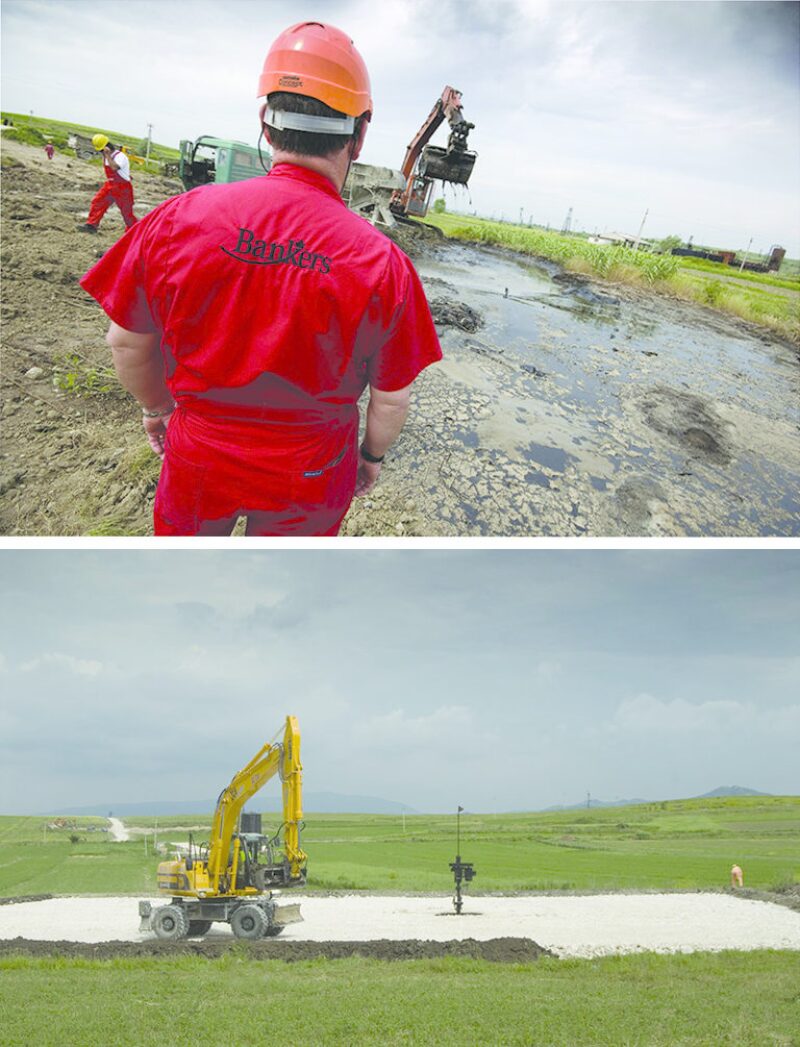
Thompson said that the polymer and waterflooding EOR projects are doing better than expected, but final results of the pilot programs will not be determined for the next few years. Historically, the ultimate recovery rate in the field has been 9% with vertical wells, and the company estimates 8% to 10% more can be extracted with horizontal wells. Through EOR, Banker’s hopes to achieve an additional recovery of 10% to 15%.
The company recently completed a fieldwide 3D seismic survey to gain new scientific data. After processing, the data will be used to assess the success of Banker’s EOR projects and to identify any missed opportunities for oil recovery and new reserves in areas the company has yet to drill out.
The company is also exploring the idea of starting a cyclical steam injection project, also known as the huff and puff method. Compared with steam-assisted gravity drainage, cyclical steam injection relies on a single wellbore that serves as both the injector and producer well. Steam is pushed through in cycles that typically do not last longer than 30 to 60 days after which, the oil will be hot enough to flow.
The Big Cleanup
While not a major global producer of oil, Albania nonetheless has a longer history of hydrocarbon production than most countries. Ancient Romans once mined the countryside for bitumen, but it was not until 1928 that oil was discovered in the Patos-Marinza field.
Banker’s said that oil production from the Patos-Marinza field first peaked in the 1960s at around 15,000 B/D. Production began falling shortly after with the most precipitous period coinciding with the decline of European communist governments in the late 1990s. During this time, the field fell into a state of disrepair and environmental damage went largely unmitigated.
Wellheads were allowed to leak for years and production practices resorted to funneling produced water into open pits, which seeped into nearby water canals. Thompson said when Banker’s came to Albania, it had no liabilities for the pollution caused by previous operators but moved forward with a multi-million dollar environmental restoration project, which continues to this day.
In some cases, the company was able to suck up the oily water and reprocess it. This helped to offset some of the cleanup costs. Thompson said there are still pockets of pollution left in the field, but the majority of areas are now remediated.
At one point, the company invited the field’s former workers for a tour of the revamped field. Thompson said many of them had not been on the sites in more than a decade and were awestruck by the improved working conditions and overall state of the field.
“We take a lot of pride in what we’ve done with this field environmentally,” he said. “You can still make money by doing the right things.”