Oil and gas companies around the world are repositioning themselves to face the energy transition—whether that means embracing the fact that the green economy of the future calls for less hydrocarbon use or something more radical, like Lundin Energy’s (now called Orrön Energy) recent move to sell off its oil and gas assets to become a pure renewables player.
One certainty is that as companies trend away from oil and gas and toward a lower-carbon frontier there will still be plenty of “cleanup” to do while players figure out exactly what to do with more than 100 years of oil and gas infrastructure. Offshore, decommissioning of platforms and pipelines is a capital-intensive business and one that is expected to grow in the coming years.
Last year, IHS Markit released a forecast predicting global offshore decommissioning spending to reach almost $100 billion for the 2021–2030 period, up by more than 200% compared to the previous 10-year period. According to the forecast, nearly 2,800 fixed platforms and 160 floating platforms could be decommissioned. That represents 33% of fixed platforms and 43% of floating platforms currently in operation. Additionally, more than 18,500 wellheads, 2,850 subsea trees, and 83000 km of offshore pipelines and umbilicals currently in operation are subject to decommissioning during the same period. More than 50% of the expected activity is spread across four countries: the UK, US, Brazil, and Norway.
The financial burden and safety liability of marine decommissioning have prompted some to look at the potential for repurposing the hardware and using it in moving toward the drive to net-zero emissions: platforms that could be used to host wind turbines, vessels that could be redesigned to collect hydroenergy, and pipelines that could be repurposed for potential battery storage.
Repurposing offshore pipeline as energy storage (ROPES) is a concept that is being investigated by a partnership of offshore projects and services specialists Subsea 7 and offshore energy storage startup Flasc. Flasc was founded as a spinoff from the University of Malta in 2019 and is based in the Netherlands. The concept was described in a paper presented at the 2022 Offshore Technology Conference in Houston (OTC 31703).
Subsea 7 and Flasc signed a cooperative exclusivity agreement in late 2020 to work toward the commercialization of Flasc’s patented hydro-pneumatic energy storage (HPES) concept offshore. HPES combines pressurized seawater with compressed air to create an efficient, large-scale energy storage device that can be applied across a wide range of offshore applications. Energy is stored by pumping seawater into a closed chamber to compress a fixed volume of precharged inert gas. The energy can be recovered by allowing the compressed gas to push the water back out through a hydraulic turbine generator (Fig. 1).
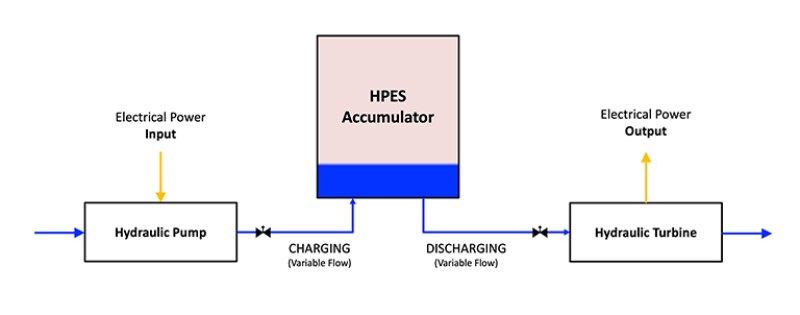
The technology leverages existing infrastructure and supply chains, along with the marine environment itself as a natural heatsink. The first working prototype was successfully tested in 2018, and DNV has granted the technology a Statement of Feasibility based on a technical and commercial assessment.
“The hydro-pneumatic technology is at the core of the ROPES concept, but can also be applied to other embodiments,” said Daniel Buhagiar, co-founder and chief executive of Flasc. “Within this collaboration, we’ve looked at doing some different designs and different products, and ROPES emerged as a very interesting opportunity. Typically, we’re looking at doing new infrastructure, [for instance] installing a bundle or a new piece of kit to store the pressurized fluids. ROPES, we thought, was really the low-hanging fruit because the pipeline infrastructure is already there, and we can create a use case for it beyond the typical applications, such as hydrogen and carbon capture, which are not always possible.”
How It Works
ROPES uses the HPES system which acts like a liquid piston with energy activated by a pump and recovered through a turbine. The energy is stored in a pressurized container. In ROPES’ case, the container is an idle offshore pipeline. The system could be used to improve the economics for offshore wind farms.
“There are two main parts to the technology,” explained Azril Hazim, technology manager—field development group at Subsea 7. “One is the energy conversion unit, which is essentially the brain converting electrical [power] to a mechanical energy system and vice versa. And the other bit is something that we call the pressure containment system. Typically, it would come with a newbuild system, whatever it might be, but essentially what’s required is a structure that is capable of storing pressure. So, the opportunity that we bring with ROPES is that we repurpose existing pipelines instead of building these new structures, thus saving capex.”
In ROPES, the pipeline itself becomes the pressure containment system (PCS) required to store and create the energy. In addition to the PCS, ROPES’ main elements include an energy conversion unit (ECU): a module needed for converting the electrical power into hydraulic power during charging and vice versa during discharging. The ECU includes a pump to move the seawater into the PCS during charging, a turbine to produce electricity from the pressurized seawater moving out of the PCS during discharging, a control system for energy and storage management, and as well as other supporting elements (Fig. 2).
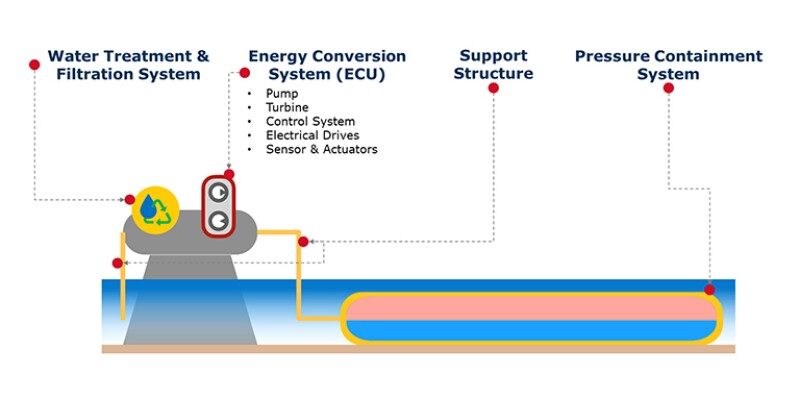
The system also utilizes a water treatment/filtration system that could use UV radiation to eliminate particles from the raw seawater that could otherwise degrade the PCS material, in this case the existing pipeline. A support structure may also be required to house parts of the system, or if available, an existing offshore platform could be used. The ROPES solution is configurable in multiple ways and is optimized following the existing infrastructure layout and constraints.
In the example of using ROPES with an offshore wind farm, the storage system can be used to feed the grid during times of lower winds, keeping the flow of energy uninterrupted. In times of higher winds, excess power can be diverted from the grid and stored in the ROPES system for deployment later.
So, how much power can ROPES store? That is driven by a few factors, including the overall size of the PCS.
“The main two drivers are peak pressure that the structure can handle and the volume, basically,” said Buhagiar. “The peak pressure we select to be within the pressures of standard offshore pipelines, such as 200–220 bar, that’s typically what we target. However, we can also cater that to lower pressures. If we are repurposing pipelines, we can, depending on what the pipeline has to offer, derate the pressure to optimize the use of the existing volume and remaining pipeline lifetime.”
Making a Theoretical Case for ROPES
In the OTC paper, the authors outline a handful of case studies for ROPES application. Fitting the HPES technology in a ROPES solution enables two main energy storage system applications offshore: oil and gas host electrification (off-grid application), or a wind-plus-storage solution for predictable power deliverability (on-grid application). The reference case examined the potential use of the technology off Australia in association with renewable energy to reduce gas usage, increase sales and revenue, and optimize abandonment spend in an off-grid scenario.
“We were looking at it in Australia initially because the decommissioning regulations there are slightly different than elsewhere,” said Alasdair Gray, late life and decommissioning lead at Xodus. “The regulator is driving towards operators having to remove all infrastructure when it is no longer in use, unless an equal or better environmental outcome can be demonstrated, which comes at a significant cost. Fabrication of a new pressure containment device is also costly within a brand-new system. So, in simple terms it appeared that the economics might make sense where both capex in a new system and the cost of abandonment are optimized.”
In this theoretical case study, based on an existing field on the North West Shelf, a 50-km pipeline connects a production platform A to a nonproducing platform B. Platform A requires power between 1 MW (continuous) to 3 MW (peak) to power production modules and has a legacy 33-kV power cable that was previously used to power platform B from Platform A (Fig. 3). Under current regulations, Platform B, the pipeline, and the power cable must be decommissioned by full removal of the infrastructure.
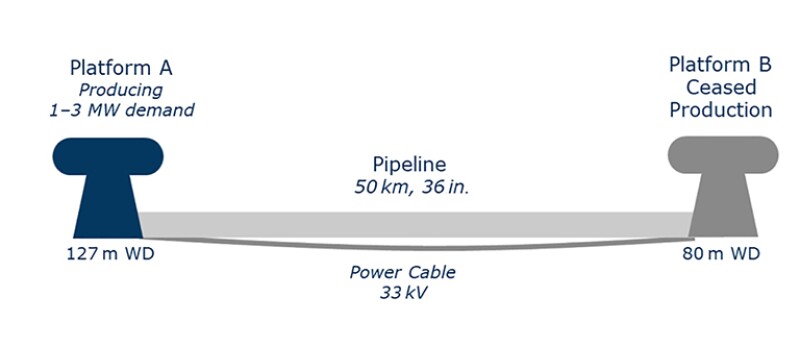
Using the ROPES solution, HPES can be incorporated into the current infrastructure to allow repurposing. An ECU comprising a pump and turbine would be located above water on the existing Platform A. The ECU would also contain a control system for power management. Supporting purging/packing of air on the Platform B side is handled through the existing air package on Platform B and the existing import riser.
The 50-km pipeline becomes the PCS. Additional risers for intake/discharge of seawater are added to Platform A to tie the PCS into the ECU. A water-treatment system is added alongside the ECU to manage long-term corrosion and filter the raw seawater. Unique to the case, a 15-MW wind turbine is installed on Platform B to generate renewable energy.
This application uses a combination of wind power and energy storage to offset gas power generation and to optimize the decommissioning expenditure. With storage, the gas turbine activation can be scheduled in line with expected wind reference and storage capacity. The HPES is used to regulate the wind supply intermittency by discharging uniform power when needed. In periods of high wind, the ROPES system is charged. In low-to-no wind, the system would discharge power.
The systems installed provided economically positive results, with the system installation saving the system owner approximately $12 million which is gained by deferring the infrastructure abandonment plus the theoretical storage of 36.5 MWh of energy. The net cost would make this one of the cheapest energy storage solutions on the market, comparable to industrial-scale onshore batteries.
Flasc believes the HPES is scalable to more than 100 MWh, capable of up to 70–75% roundtrip efficiency, and having the potential of an operational lifetime of more than 3 decades.
“Energy storage at scale is still developing and this is particularly apparent in an offshore environment,” said Gray. “We do know that wind is intermittent, so in theory you don’t have power on demand. What the HPES does is try and plug that intermittency and improve the efficiency of the wind turbine(s).”
Currently, the partners are moving forward with a demonstration of HPES within a floating wind solution offshore Greece that is a part of an EU-funded project. The system is utilizing newbuild PCS and not old pipelines. In 2024, the Subsea 7/Flasc consortium aims to launch a large-scale PowerBundle demonstrator in the UK. Again, the PCS and the accompanying systems will be built new. Funding for the FEED and mobilization stage of this demo, approximately $565,000, came from the UK BEIS Long-Duration Energy Storage Competition. The competition recognizes the transition to increasing wind-generated renewable energy, which presents opportunities for storage systems that support a secure, flexible, and reliable electrical power supply.
“One of the things we’re trying to do with this technology as HPES, but also as ROPES, is show that the building blocks are established offshore technologies, such as hydraulic pumps and steel pipelines,” said Buhagiar. “It is innovative, but when we talk to developers, asset owners, and operators, the building blocks are already very well understood.”
For Further Reading
OTC 31703 Repurpose Offshore Pipeline as Energy Storage ROPES: Opening a New Market Segment Offshore by Azril Syazwan Hazim, Subsea 7; Daniel Buhagiar, Flasc BV; Alasdair Gray, Xodus.