We often observe scale deposited in tea kettles or water pipes in our daily routine. This phenomenon also occurs downhole. Scaling buildup inside wellbores is a serious production problem that dramatically reduces the well productivity index. This issue has a significant cost across the industry, mostly associated with loss of production or additional operations such as well intervention. Scale deposition can reduce porosity or permeability of the near wellbore, and it can accumulate in components of the completion string (Fig. 1), leading to blockage and poor productivity.
Several mechanical and chemical methods are available to remove scale plugging the wells. Some of these methods have been tested successfully. The success of each method, however, varies and is subject to
- Reservoir conditions (pressure and temperature)
- Chemistry of reservoir fluids
- Petrophysical properties of production zone (rock mineralogy, porosity, and permeability)
- Type of operation applied on a well (compatibility of injected water with the reservoir brine for injection processes)
Therefore, understanding the sources of scale and driving forces for scale deposition are imperative before selecting any treatment method.
The disturbing of thermodynamic equilibrium is potentially a trigger point for scale initiation. Thermodynamic equilibrium at the reservoir conditions is disturbed when a well is placed in production. This results in exceeding the upper limit of solubility of one or more minerals in water, leading to the scale formation. Mineral solubility is a function of several parameters, including temperature and pressure. Fig. 2 shows the solubility of some minerals vs. temperature. Note that not all minerals follow a similar temperature trend. For instance, the water solubility of siderite and calcite increases by increasing the temperature while that of gypsum, anhydrite, and strontium sulfate decreases by temperature.
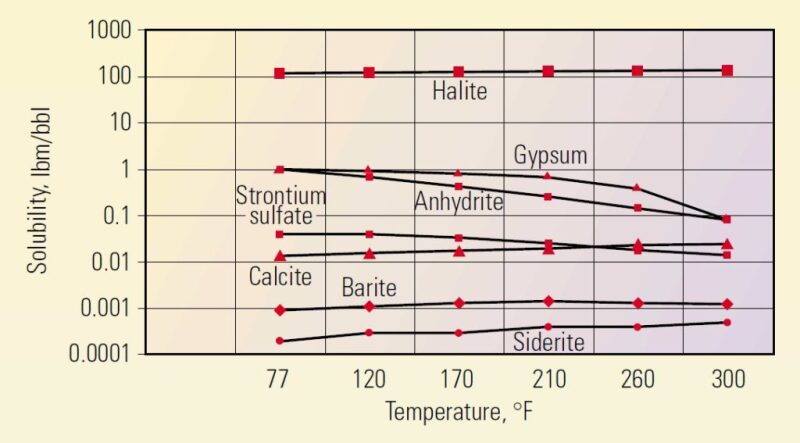
Fig. 2—Solubility of minerals versus temperature.
Saturation tendency (ST) is defined to quantify the scaling potential of minerals in water as ST = IAP/Ksp, where IAP and Ksp are ion-activity product and thermodynamic-solubility product, respectively.
The scaling potential is ST > 1 is oversaturated, ST = 1 is equilibrium, and ST < 1 is undersaturated.
A scaling potential does exist when a solution is oversaturated with a mineral. However, ions remain dissolved in the aqueous solution when scaling tendency is less than 1. More details about the calculations of ion-activity product are presented elsewhere. Kan et al. (2019) summarized current advancements for accurately modeling the aqueous ion activities at high temperature, high pressure, and mixed electrolytes conditions. They also proposed a new predictive model for the scale control at the reservoir conditions based on the Pitzer theory and equation-of-state (EOS) vapor/liquid/liquid-equilibrium calculations.
The next step is to identify the location of the scale deposited. Production tubing, surface facilities, near-wellbore region, and injector wells are the most common places for scale deposition. Moreover, the diagnostic time for scaling formation matters as the scale can build up in 24 hours or less. The severity of damage and cost of treatments will be less when the scaling is recognized early.
After predicting the composition and location of scale deposited on downhole facilities or in the pore space near the wellbore region, scale-removal techniques should be applied to unplug the well. These techniques are categorized into three main groups: mechanical, chemical, and jet-blaster tools. Table 1 lists advantages and disadvantages of these cleaning methods. More details about the application of these methods are reviewed by Crabtree et al. (1999). In addition to cleaning techniques, other methods are used to prevent the scale formation. Dilution is the simplest way to prevent scale formation in the tubing. The next method is using scale inhibitors for blocking the growth of scale particles. These scale inhibitors are mainly composed of inorganic phosphates, organic phosphate esters, organic phosphates, organic aminophosphates, and organic polymers. A successful practice at the field scale depends on the inhibitor placement and lifetime. Bullheading can be a proper operation to place scale inhibitors for heterogeneous formations. Moreover, inhibitors can last more than a year if they are properly designed.
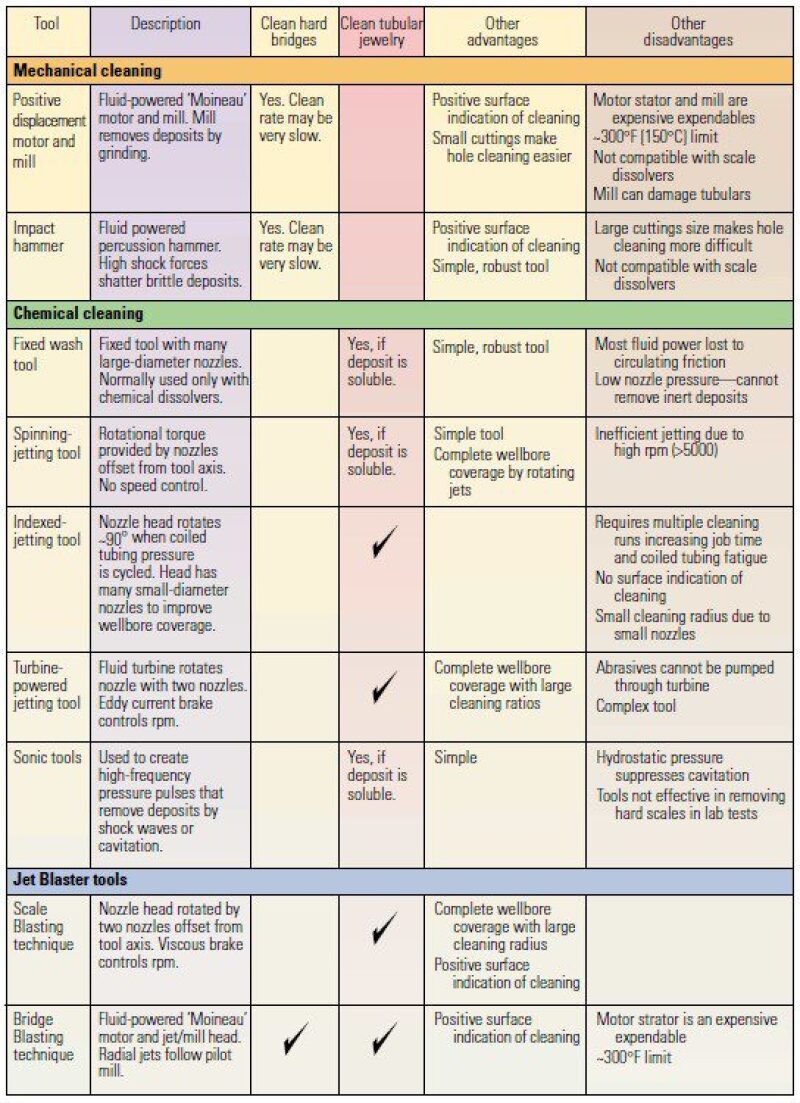
Table 1—Proposed techniques in the literature for scale removal.
Summary
During the past decades, several methods and materials have been proposed for inhibiting scale formation or removing the deposited scale. Each method, however, is field-specific and addresses limited aspects of the chemistry and, therefore, is limited and has disadvantages. To start, an accurate predictive tool is required to estimate the scaling potential of different minerals at reservoir conditions. Then, a comprehensive strategy should be considered for scale control by preventing scale formation using specific chemical inhibitors and periodically removing the scale deposited on the production tools.
References
Kan, A.T., Dai, J. (Zhaoyi), Deng, G., et.al. 2019. Recent Advances in Scale Prediction: Approach and Limitations. Society of Petroleum Engineers. https://doi:10.2118/190754-PA.
Crabtree, M. Eslinger, D., Fletcher P., Johnson, A., and King, G. 1999. Fighting Scale—Removal and Prevention, Oilfield Review.
Sandengen, K. 2006. Prediction of Mineral Scale Formation in Wet Gas Condensate Pipelines and in MEG (Mono Ethylene Glycol) Regeneration Plants. PhD dissertation, NTNU.
Frenier, W.W. and Ziauddin, M. 2008. Formation, Removal, and Inhibition of Inorganic Scale in the Oilfield Environment. ISBN: 978-1-55563-140-6, Society of Petroleum Engineers.

Ali Habibi is a PhD degree candidate in petroleum engineering at the University of Alberta, Canada. His research interests include wettability evaluation of unconventional resources, application of enhanced-oil-recovery techniques in tight oil formations, and application of nanotechnology in formation-damage prevention. Habibi holds bachelor’s and master’s degrees in chemical engineering and reservoir engineering from the University of Tehran, Iran.