Introduced earlier this year by Schlumberger, a trio of hydraulic fracturing systems represent one of the latest steps toward a more automated oilfield.
This new hardware is already working in the North American unconventional sector where the world’s largest service company says the growing intensity of horizontal well programs demands that the next wave of fracturing technology come loaded to bear with sensors and real-time data streaming capabilities.
Dubbed an “automated stimulation delivery system,” its three main pieces are a vertical silo system for sand or proppant management, a process trailer for blending and hydration, and a missile manifold that channels pressurized fracturing fluids into the wellhead. Prototypes of each system spent a year in the field before entering commercial service, and during that time, helped send almost a billion pounds of sand down horizontal wells.
This new product line will form part of the recently announced joint venture between Schlumberger and Weatherford that combines their fracturing fleets. And notably, it rolls out just months ahead of the expected launch of Schlumberger’s first automated land drilling rig.
The large extent to which automation technologies will assist in the operation of these advanced assets means oil and gas producers using them will need fewer people and less time to drill and complete their wells.
By Schlumberger’s calculation, the automated features of the missile manifold trim up to 15 minutes from the job times of each fracturing stage. That may not sound like precious time, but because today’s horizontal wells average more than two dozen stages each, the company reports that those minutes could add up to 2 days a month.
Terence Goettsch, an equipment portfolio manager of well services at Schlumberger, explained that such gains exemplify what the company was aiming for when it launched an effort 4 years ago to identify inefficiencies in its field operations.
That work involved examining “every single minute or second that’s spent on location, and understanding why we’re not being productive at any point in time,” he said. “What we found out was that the vast majority of issues that we started seeing in 2012 and 2013 were centered around the backside of the equipment.”
Specifically, Goettsch said problems with the blending and hydration units, used to mix sand with fluids and fracturing chemicals, were causing significant delays. To a lesser extent, Schlumberger also saw room for improvement with sand management and logistics.
One change made in the name of increased reliability is that the units are all electrically powered vs. older systems that depend on hydraulic controls or diesel motors. This move, and extensive use of sensors and analytics software, show how Schlumberger is keen on improving the life span of its capital intensive assets.
In the past, the operational strategy for fracturing equipment was to rely on statistical data for maintenance schedules, or to simply “run it until it breaks,” said Oscar Javier Rodriguez, the vice president of well services coiled tubing and stimulation at Schlumberger. Now, with a host of “health monitoring” technologies for large equipment readily available to service companies, it has become easier and more cost effective to adopt real-time performance analysis and preventive maintenance strategies.
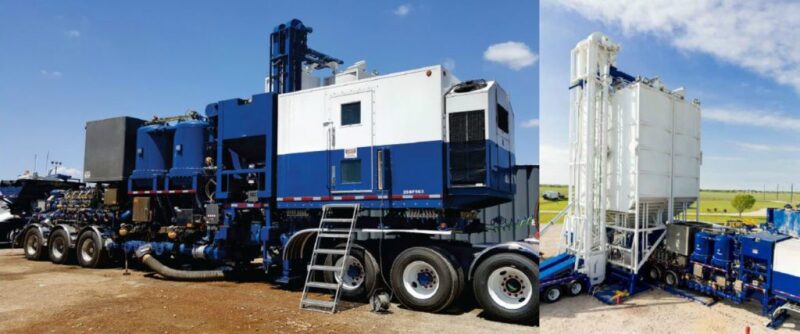
Two Become One
To improve the blending and hydration units, Schlumberger redesigned them as a single system that instead of requiring two people to run only needs one. That worker is aided by software that controls the processing systems, ensuring the proper fracturing fluid recipes are being sent downhole. Sensors embedded inside the unit report performance data, which is fed back to Schlumberger’s new 24-hour asset monitoring center that opened last year in Dallas, Texas.
If a critical component is showing signs of fatigue, which may be indicated by higher-than-normal temperatures, analytics software alerts maintenance experts at the monitoring center. “At that point, we can start to plan ahead,” Goettsch said, adding that might mean “we need to either bring in another unit or have our mechanic and electronics tech go look and see what the actual issue is, because it could be something as simple as a valve that was incorrectly closed.”
The main driver for the redesigned missile system was to address the safety risk introduced whenever a pumping truck fails. When this happens, companies typically send someone to close a valve and bleed pressure from the line connected to the downed pump.
But Schlumberger’s safety rules forbid this due to the risk of someone becoming confused and opening the wrong valve, which means the entire pumping operation must shut down prior to an inspection.
“We wanted to eliminate all the personnel from ever having to walk into the area, but in conjunction with that, we didn’t want to have to terminate the job,” said Goettsch. To get there, Schlumberger put actuators on the valves so crews can remotely open or close them from the safety of a control cabin.
The system’s software also removes any doubt about which valve is connected to which line by automatically pairing them as they are hooked up. And with no need to manually turn the valves, the pressure pumping units can be primed up faster in preparation for a fracture stage.
This work only takes a few minutes to complete with conventional equipment, but that time stacks up since the average horizontal well today has 28 stages—a 220% increase since 2008 when many contemporary fracturing systems were designed.
Rodriguez emphasized that this particular efficiency gives meaningful time back to operators. “When you shave 10 to 15 minutes off before every stage, you are saving on the order of 2 days per month to your fleet—which is going to allow you to pump more jobs,” he said.
Inventory Management
The silo system—composed of four separate silos—stands about 60 ft. tall and has a maximum capacity of 1 million lbs., which comes out to about 20 truckloads of sand. With automated systems moving the sand up and into the silos and sensors taking weight measurements, operators know where it is going and exactly how much of the sand it purchased is actually being delivered.
Trucks are also weighted before and after they unload to add another layer of inventory control. Rodriguez related that sand is sometimes delivered to a location wet, which makes it hard to unload it all and could result in a truck driving off site with as much as 30% left inside.
Silo systems, which have been in use for years by other service companies, are known to have a few benefits including the alleviation of pad site congestion and the reduction of silica dust exposure to crews. The conventional alternative is to use pneumatically compressed air units called sand chiefs to blow sand from a truck, through a hose, and into storage containers.
Not only does this process tend to generate silica dust, it may also take from 30 minutes to an hour to complete for a single truck. Sand chiefs have another downside in that they demand the involvement of several workers, some who are just waiting around for the sand transfer to be completed. By contrast, Schlumberger’s silo system is operated by just one person.
And at a rate of 5,000 lbs. per minute, a truck can drop a full load of sand into the system in just 10 minutes and then quickly exit the well site. With two loading sides, that rate jumps to 10,000 lbs per minute.