The management of water used for fracturing oil and gas wells is all over the map.
In Pennsylvania, most of the produced water is treated so it can be used again for fracturing, but some is cleaned to the point at which it meets the stringent requirements for river disposal.
In Texas, fracturing fluids generally use fresh water, and what flows back to the surface is injected into a deep disposal well.
A 2012 report, prepared by the Bureau of Economic Geology for the Texas Oil & Gas Association, titled Oil & Gas Water Use in Texas, puts the percentage of produced water recycled for fracturing in the Eagle Ford shale at 0%, and in the Permian Basin near Midland at 2%. In these arid regions fresh water is used by a wide margin. In the Eagle Ford, 20% of the water for fracturing came from brackish aquifers, and 30% in the Permian around Midland used water too salty to be potable.
Things change fast in these booming plays. But the lead author of the report, Jean-Philippe Nicot, a research scientist at the Bureau of Economic Geology of The University of Texas at Austin, said: “I don’t think those numbers have changed much. There is likely some reuse/recycling in all plays, so 0% is probably not correct, but close to it.”
For Michael Dunkel, director of sustainable development at Pioneer Natural Resources, past performance in places like the Permian is not a useful indicator of the future in an area where so many are looking for alternatives. “I am confident what we are seeing today is just at the starting gate and it will continue to evolve,” he said.
Given the thousands of unconventional wells drilled, this may seem to be a slow evolution, but the staggering scale of these formations, particularly in the Permian, means operators such as Pioneer are just moving from scattered exploration drilling to concentrated development.
“We will be drilling for 30-plus years out there,” Dunkel said. While he is confident the industry will change how it manages water for unconventional development, there are a lot of ways it can go from here.
The decisions hinge on a complex mix of variables, which can be boiled down to a simple imperative: What is the lowest-cost option? The correct answers will vary from region to region, and from company to company depending on factors such as the scale of a company’s operation.
Chesapeake Energy treats most of the water produced in its wells in Pennsylvania for reuse in fracturing with a small amount sent for disposal, said Rick McCurdy, manager of chemicals and water reclamation at Chesapeake Energy Corp. In south Texas most of the water is pumped from freshwater aquifers and produced water is injected into disposal wells.
The difference is the cost. In Pennsylvania the nearest disposal wells are in Ohio, so the high cost of that long haul pushed the cost of injection disposal there to USD 12–15 per bbl, he said. In Texas, disposal wells are generally a short trip away and charge little—often USD 1 per bbl to inject produced water into the ground.
Still, both Pioneer and Chesapeake are looking for alternatives for the future. Pioneer is testing a variety of ways to process produced water, but its big idea is turning to using water from brackish aquifers for fracturing in the Permian. Other companies operating in that area, such as Laredo Petroleum, are also developing brackish water supplies.
For this to be a lower-cost option long term, Pioneer will need to make a larger investment in building a pipeline system to deliver the water, which would reduce the single biggest cost for water management—the cost of hauling it in trucks at 100 bbl per load.
Pioneer is also considering a plan to use reverse osmosis to desalinate the water, to reduce damage if there is a spill. This could inspire others to try things that are different, but could be a difficult example to follow. Pioneer is scaling up for a huge development in the Permian—a 900,000-acre lease covering a relatively compact area—with multiple zones that can be tapped from a single location.
Increasingly, companies are clustering wells on pads for intensive development. It helps justify investments in treating produced water for reuse on site, and other infrastructure such as pipeline networks.
Sometimes the plan is driven by water shortages. Chesapeake fractured more than 36 wells using high-salt-content produced water because fresh water was not available then in that part of Oklahoma.
Severe droughts the past 2 years in western Oklahoma reduced surface water supplies normally used for fracturing. As a result McCurdy said Chesapeake increased its programs to find alternative sources of water for fracturing and test new water recycling methods and chemicals suited for the resulting water.
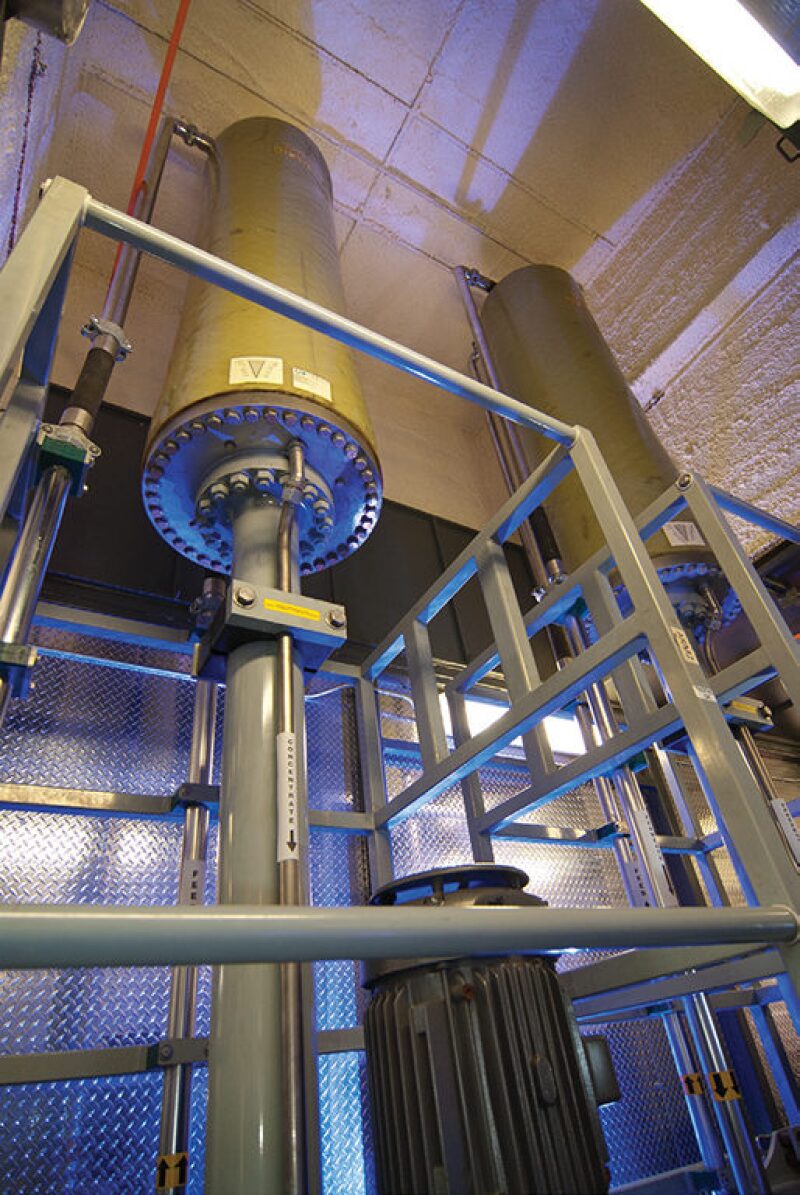
“Doing things the way you have always done them is the biggest competition to this,” said Dale Pierce, manager of new business development at NOV Brandt, which works on water processing using membranes. “I think a lot of that will change. It still gets down to economics.”
Water Variables
Fracturing-water economics can get complicated. When PacWest Consulting Partners, which monitors and analyzes fracturing and water use issues, was hired to study what clients spend on water over the life of a well, it found the spending was scattered among the units doing drilling, completions, and production, and no one was adding it all up, said Alexander Robart, a principal in PacWest Consulting.
When these expenses were totaled and analyzed, the consulting firm found they could save money by investing in water reuse or building pipelines to reduce transportation cost, which is by far the biggest expense in produced-water management.
PacWest’s projections for produced-water processing show how external factors, including the weather and new regulations, can shape the future.
It predicted that the business, which had estimated 2012 revenues of USD 2.8 billion in the United States and Canada, will grow by the year 2017 to one that ranges in size from USD 3.8 billion to USD 7.2 billion. The low number is based on current growth rates and conditions, while the top number assumes water reuse growth accelerates due to water scarcity and regulations limiting water disposal or making water more expensive.
“It is not clear how it will evolve. My personal viewpoint is it will grow. Not in every instance but in most instances,” Robart said.
Water use economics depends on one’s point of view. When Chesapeake started drilling in the Eagle Ford it considered water reuse because even in the best years it is an arid region; and severe drought has recently been the norm. Plus it is between two growing metropolitan areas where future water supplies are a worry.
But when negotiating mineral rights leases with ranchers, Chesapeake learned that a water well was often part of the deal.
“It is more than good relations. In many instances, landowners get that written into the leases,” said McCurdy, of Chesapeake. “Many of our leases in the Eagle Ford mandate we drill a Carrizo aquifer well and buy the water from the landowner. When we are finished with that well, or wells, it is ceded back to the landowner.”
Another cost variable is the quality of the water flowing out of the ground. The impact of water supplies is evident in the place in Texas with the highest level of produced-water recycling. In the Anadarko—an enormous basin in Oklahoma that extends west into the Panhandle of Texas—20% of the water used for fracturing in 2012 was recycled, plus 30% was pumped out of aquifers with brackish water.
Two likely explanations for those numbers are short water supplies in Oklahoma, and the relatively low levels of dissolved solids in the produced water, McCurdy said. High concentrations of these salts and minerals make the water harder to treat, can interfere with chemicals used in fracturing fluids, and cause scale deposition that may hurt production.
A stronger force for change would be regulation aimed at requiring oil and gas companies to reuse water for fracturing, or draw water from brackish aquifers.
So far there has been talk in Texas about forcing reuse, but little action. Two bills were introduced earlier this year in the Texas legislature that would have required recycling. Neither passed, but severe droughts in key oil-producing areas in south and west Texas combined with growing legal battles over water rights will keep this issue alive in Texas and other states where unconventional reserves are plentiful and water is not.
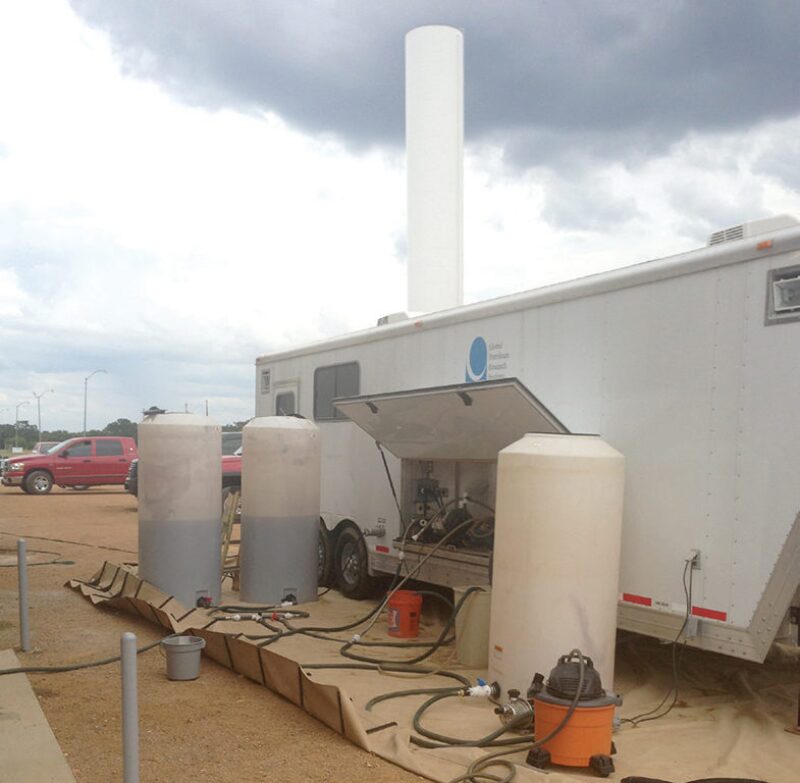
Operators are concerned about rules that could limit water-use options, raising the cost of fracturing which could limit development and the economic benefits of greater production, McCurdy said.
“All those in the business accept that more rules are coming,” on produced-water use, Robart said. “From a water services perspective that is a good thing. There is more market for them. Operators do not want more rules. The rules will come; it is just not clear how or when.”
Texas Fracturing Water Sources |
Little of the water for hydraulic fracturing in Texas is from recycled water, or brackish water from nonpotable aquifers. |
Play/Region | Type | Current (2011) % |
Permian Far West | Recycled/Reused | 0% |
Brackish | 80% | |
Fresh | 20% | |
Permian Midland | Recycled/Reused | 2% |
Brackish | 30% | |
Fresh | 68% | |
Anadarko Basin | Recycled/Reused | 20% |
Brackish | 30% | |
Fresh | 50% | |
Eagle Ford Shale | Recycled/Reused | 0% |
Brackish | 20% | |
Fresh | 80% | |
East Texas Basin | Recycled/Reused | 5% |
Brackish | 0% | |
Fresh | 95% |
Source: Oil & Gas Water Use in Texas: Update to the 2011 Mining Water Use Report |
Treat or Dispose? |
The decision of whether to dispose of produced water in an injection well, or treat and use it, is an economic one that is affected by local factors:
|
What to Do?
Another variable over time is the standard for care needed for produced water that will be used again for fracturing. The simple answer is, “Do not take out what you do not need to,” said David Burnett, a Texas A&M University professor who is director of technology for the Global Petroleum Research Institute at Texas A&M.
Generally what must go are suspended solids, organic materials, and bacteria. Burnett, who has spent years working on membrane-filtration methods for produced water, is trying to convince the industry that removing the bacteria entirely using filtration is better than poisoning them with a biocide, because the dead remains can turn into slime.
Some things people generally agree on, others they do not. All those interviewed agreed that suspended solids plus oil and other organic materials need to be removed, and bacteria killed.
What is left are dissolved solids. These include common salt—sodium chloride is only a problem if the concentration is really high and that can be remedied by diluting it with fresh water. But there are arguments about what to do, if anything, about barium, calcium, and boron.
“There are four things you can remove in water. Three things are relatively easy to do—the last one is dissolved solids,” Pierce said. “All the arguments are over dissolved solids. Those are the hardest things to remove.”
For example, certain minerals such as barium and strontium can combine with sulfates to cause scale, which can hurt future production.
These can be removed using a long-used method called flocculation. Chemicals are added to a tank full of produced water, forming larger molecules that settle out. But that leaves large mounds of solids to get rid of.
“The precipitant volume is so big that you have an engineering problem … What do you do with it?” Burnett said.
His research is aimed at using membranes to process produced water, so that about 80% can be used and the concentrated fluid left over can be disposed of in an injection well. But he is not for removing all the dissolved solids.
For one, it is costly. Evaporation-based methods are used in parts of Pennsylvania where the water is not needed for fracturing; elsewhere, the water can be reused with less expensive treatment. Dissolved solids can also be removed using nano-filtration membranes, but in the past reliability has been an issue because of the high level of dissolved solids present and the damage that can be caused by even small amounts of oil.
McCurdy said that putting barium-rich water back in a reservoir where there are high levels of minerals is not a problem if you control sulfates, which react with it to create a difficult-to-remove scale. Chemicals added to Chesapeake’s formula for fracturing water also reduce the risk of scale.
Boron is another element that is a source of debate. It has become a concern as more operators have turned to adding cross-linked gels to fracturing fluids to carry large-size proppants deeper into fracture networks to create larger avenues for oil production.
In cross-linked gel formulations, borates are widely used to trigger the chemical reaction that thickens the fracturing fluid as it flows down the well. Produced water with boron can prematurely cause gelling, while the fluid is being prepared in a blender, making it harder to pump the jobs.
Service companies have a solution—cross-linked gels activated by other chemicals—but they cost more, Pierce said.
For those in the business of creating water-treatment equipment, the complex array of problems and solutions, plus the lack of agreement on what water is suitable for fracturing, makes it hard to identify lasting markets.
“Producers all want something different.” said Charles Solomon, president of Global Industrial Water, which is developing water-treatment equipment using membranes.
No Silver Bullet
A phrase that bubbles up over and over in conversations about produced water treatment is “There is no silver bullet.”
The point is that in a business where a lot of companies jump in promising game-changing technologies, for a number of reasons the game is not likely to change so much.
In the realm of produced-water processing, the new technology is improved versions of current technologies, adapted for hard-to-treat produced water. There are physical limits to what is possible. New evaporation technology is more efficient, but it will always take a certain amount of heat to boil water.
The list of companies competing for a piece of this business is long, with big names in oil services, water treatment, and waste management included. The likely winner will need to be able to consistently deliver an effective mix of proven treatment techniques on a large scale.
“It is not about the technology. It is about the ability to deploy services,” Robart said. He sees the companies now selling flowback services as well positioned for the role.
Low-cost options are needed. In Texas, water treatment for reuse is up against injection wells charging about USD 1 per bbl, but that varies widely based on the location.
But when PacWest broke down the cost of produced-water management, by far the highest item was transportation, at 43% of the expense. A common rule of thumb is it costs USD 1 per bbl per hour to haul water using a tank truck.
There are a lot of ways of attacking this problem. Pioneer is working on reducing truck trips by planning to build a network of water pipes to move water. Another development initiative is to reduce evaporation. The company has found that in windy, sunny, hot west Texas, an open water storage pit can lose a lot of water. “You lose 6 ft of water out of a pond per year. Do the math. That is a lot of water,” Dunkel said. In some places the savings on transporting water to make up for evaporation will justify using a cover.
Companies are looking outside for ways to reduce water supply and disposal costs, Robart said. Because each operator is managing its water operations, decisions are often based on limited information and choices for action.
The goal for water-management companies is to offer operator managers who see water supply and disposal possibilities nearby the opportunity to find out if there is a lower-cost option, and make a deal if that is true.
Based on client feedback, PacWest started up a separate new company to trade water, Digital H2O. It has been building a database for water-supply information and cost analysis, which will support the next step, trades among member companies.
“There is a poor understanding of what water assets are nearby,” said Piers Wells, chief executive officer for Digital H2O. “The big idea is creating a business-to-business water market for oil and gas operators and service companies.”
How New Ideas Filter Into Produced-Water Processing
A sign at the entrance of the Tishomingo Industrial Park says this is “where progress is taking place.” In a metal building in the park outside the small southern Oklahoma place, there are signs of just that, but it is easy to miss.
Clustered at one end of a machine shop was a group of workers testing new ways to treat water produced from oil wells.
Two companies with devices to remove the last bit of oil left after conventional separation methods were competing to see which one could do it better.
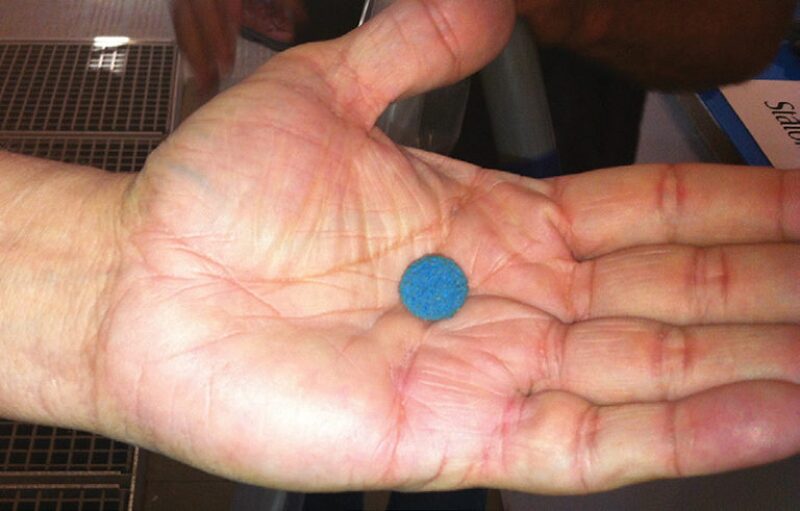
Nearby was a device built to remove oxygen from seawater to be injected in a reservoir, waiting to be shipped off to a Shell production platform in the Gulf of Mexico.
Just outside was a trailer where researchers from Texas A&M University were creating an increasingly concentrated brine by repeatedly running produced water through a filter to see how far they could push it before it failed.
This informal gathering of competitors and academics is an indication of the many companies that see an opportunity in treating produced water, and the advances in membranes and related technology that could change how the oil industry treats water. Membranes can do a wide range of things. Shell said it is testing membrane technology for offshore produced-water treatment, ranging from a pilot test to produce lower-salinity water used to improve production from water injection in offshore fields, to cleaning up tailing ponds filled with water left after oil sands processing.
Technical experts spending weeks in a town so small there is no motel are trying to build up a body of evidence that will allow their companies to stand out in a brutally competitive field.
“There are a lot of people who think they have the silver bullet and they can make a billion dollars,” said Charles Solomon, president of Global Industrial Water, who is the animating force in this informal gathering. While he said Global Industrial is an original equipment maker—it created the oxygen-removing unit—he said the future will go to those who build components for integrated systems.
The complex, unpredictable nature of the water treated commonly requires multiple processing steps, with equipment from multiple suppliers integrated into trains.
And competing companies are seeking test data that will be widely accepted as they seek out new business. Cetco Oilfield Services has units removing the last bits of oil on more than 50 offshore platforms around the world, but it was doing a head-to-head test to help persuade more users.
“Otherwise we will be doing pilots for the rest of our life,” said Elliot Halphen, an assistant manager in research and development at Cetco, whose device removes the oil left after normal separation. Polymer fibers attract tiny oil droplets which collide, coalescing into larger drops that flow out and up to the top of the unit.
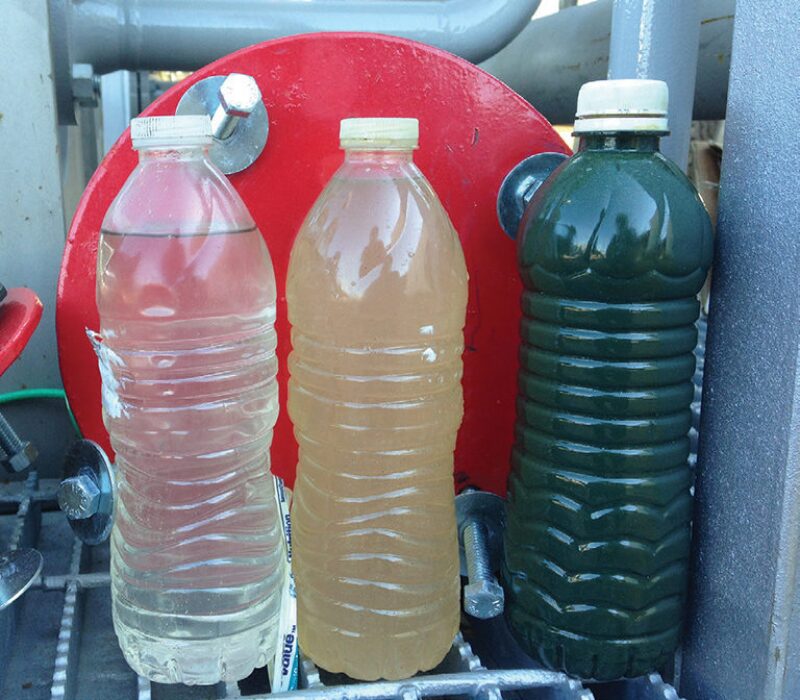
Face-to-Face Competition
There is no sign identifying the produced-water test site, which would require someone to decide on a proper name. A handful of workers in jeans are sharing a hot open space with a crew building portable flare stacks for the building owner, Nitro-Lift Technologies, which provided its space in hopes of learning something from the stream of visitors it has attracted to Tishomingo.
Nitro-Lift makes and operates portable, nitrogen-generating units that are used to pressurize formations to speed water flowback, among other things. It would like to add produced-water processing service, said Danny Daniels, the company’s chief technology officer.
Outside the north side of the open building are two tanks, one for processing produced water from nearby Woodford shale wells, and the other for the output after processing. To the south is a trailer used by Texas A&M University to test an ever-changing array of filtration and metering equipment.
The work in progress also includes recently established technology—Cetco Oilfield Services is showing what its 1,000-B/D processing unit can do. It has been selling them for about 5 years.
Water flowing out of Cetco’s unit was being compared with the output of a small test unit from Pentair, a large water-treatment company expanding into exploration and production. Pentair’s pilot unit running that day was based on the same design as one field tested in west Texas.
This process to remove the last bits of oil—Halphen said the unit was taking processed water contaminated with about 1,000 ppm of oil and grease and reducing it to less than 10 ppm—adds income and eliminates solids and organic materials suspended in the produced water that are normally removed before reinjection. This can also serve as a pretreatment if further filtering is needed because oil can be fatal for membranes.
In a field test in west Texas, a Pentair unit processing 8,000 B/D of water, a USD-200,000 unit that cost USD 200,000 to operate annually, produced USD 300,000 worth of oil at USD 85 per bbl, said Paul Osmundson, director of engineering and technical services, process technologies, at Pentair.
“Produced water is something we just have come in to. We were selling to refineries to clean up water,” Osmundson said. Experience separating oil from water in a refinery using membranes is useful, but produced water is a more complex, unpredictable mix.
The water being tested varies based on when it was produced, the well, and where it resided in the storage tank, which is a fact of life in produced water. “It always changes. It is never the same,” he said.
Membrane Innovations: |
There are many ways to treat water produced from oil wells. Membranes are an example of how the growing interest in produced-water processing is creating new applications aimed at old problems. |
Mobile Oil Treatment Using Membranes Aqua-Ves made by National Oilwell Varco Job: Processing up to 2,500 B/D of produced water for reuse in the field. Problem: Building a reliable unit able to deal with relatively high levels of oil without failing due to fouling. Details: Inside an expandable van are two cylinders each the size of a tall water heater with membranes stacked inside that can be cleaned in place. And: To resist oily buildup, filters are Teflon coated to resist buildup and stand up to the chemicals present, and are vibrated to keep oil from adhering to their surface. |
Oxygen Removal for Seawater Injection Portable offshore test unit from Global Industrial Water Job: Removing virtually all the Oxygen from seawater injected into offshore fields, reducing the risk of corrosion damage and bacterial growth. Problem: Current methods require large units plus chemicals to reach the required oxygen content. Details: A vacuum inside membranes in the shape of tubes pulls oxygen out of the water, leaving only 10 parts per billion (ppb). The unit is 70% lighter and can fit in tight spaces. And: Current methods can reach from 100 to 500 ppb. That is further reduced by scavenger chemicals that bond with the remaining oxygen. |
Removing Residual Oil Cetco Oilfield Services Hi-Flow Coalescing System Job: removing small amounts of oil left after conventional separation. Problem: Pulling out residual oil adds to production, reduces oil in water released into the sea, and is required for other treatments because even small amounts of oil can destroy membranes. Details: Small oil droplets are slowed as they flow through the thick media, causing collisions forming larger drops that are pushed out by the water flow and float to the top of the vessel. And: Cetco said it is able to reduce the oil and grease content from 50 ppm or more to about 7 ppm. |
Membrane Pigging Foam rubber balls to clean out tubular shaped membranes from Membrane Specialists. Job: Regularly flow inside tubes used for water processing to remove buildups like a pipeline pig. Problem: Membranes made to remove the smallest elements have been dogged by performance problems due to buildups left by produced water. Details: A foam rubber ball is regularly sent through tubes, using friction to remove oils and heavy particles. And: It is a new design now being evaluated outside the company. |
Membranes Evolving
The white trailer from Texas A&M is the traveling face of a program created as a test center for new ways to treat produced water, and increasingly to do a quick analysis of it.
Those working inside have seen the rapid evolution of membranes, since the early days when they were using ones created for businesses other than exploration and production, such as dairies or drug makers.
“There are new membranes. People are beginning to market membranes to oil and gas. That is different from when I first started,” said David Burnett, a professor at Texas A&M and director of technology for its Global Petroleum Research Institute. “It took a while for commercial membrane manufacturing to think of oil and gas as a real industry.”
As a result there are filters requiring far less energy to push the water through the filter. Tasks that once required 1,000-psi pressure can be done with 200 psi, or less, which significantly reduces the electric power needed to drive the process.
There are improved designs that resist fouling, improved glues that stand up to the chemicals in produced waters, and new membrane materials made from polymers and ceramics.
“Two years ago there were probably only a few small entrepreneurial companies pushing it. Now we are seeing a lot of people,” Burnett said. Those companies include the big membrane makers—GE, Dow, Koch, and Pentair.
One indication of the change is the changing lineup of equipment inside. When it started in 2011, one end of the trailer was filled with a water-processing unit that was nearly “as big as a Volkswagen” said Frank Platt, a research engineer with the Texas A&M Engineering Research Institute. Now the same amount of filtration work can be done in a tube clipped on the wall that is 8 in. in diameter and 18 in. long, he said.
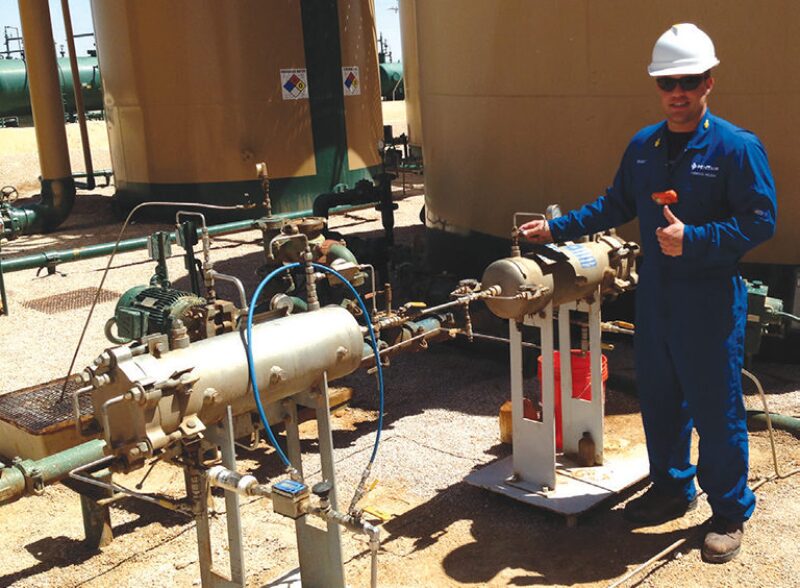
The original device had components they do not need—such as a pumping system—but much of the difference is in the fact that membranes have been adapted to the needs of the oil industry. And the industry has learned from hard experience that pretreatment to reduce the hydrocarbons present to extremely low levels is critical for reliable, long-lived membrane performance.
Much of their work has been related to membrane treatments, but they are looking for other useful technologies for water treatment. That day they were talking about a small company in central Texas that might have built an improved unit for using electrical charges to remove solids and oil from water using electro-coagulation. Increasingly Burnett is interested in trying out devices able to do real-time water analysis.
From what they can see, it is too early to say how water will be processed 5 years from now. “The technology is in a constant state of flux,” Platt said.
For More
Texas A&M University offers two short classes a year on water and wastewater issues.
In April 2014 a 2-day class will cover issues, solutions, and new technologies in the field and is aimed at a broad audience of those in water treatment, including new employees.
Note: This course was offered this past August.
The classes will be held on the main campus in College Station and can be taken online.
Course information and registration at: www.gpri.org.
Search Online
Oil & Gas Water Use in Texas: Update to the 2011 Mining Water Use Report by Jean-Philippe Nicot, P.E., P.G., Robert C. Reedy, P.G., Ruth A. Costley, and Yun Huang, P.E.
For Further Reading
SPE 158396 New York Field Trial of Ultrahigh Salinity Brine Pretreatment: Environmentally Friendly Drilling Technology for the Marcellus Shale by David B. Burnett, C.A. Vavra, F.M. Platt, Texas A&M University
SPE 166113 A Day in the Life of a Barrel of Water: Evaluating Total Life Cycle Costs of Hydraulic Fracturing Fluids by Robin Watts, Linde
SPE 157108 Using Advanced Water Treatment Technologies to Treat Produced Water From the Petroleum Industry by Raul Dores, Altaf Hussain, Mary Katebah, Samer Adham. ConocoPhillips—Global Water Sustainability Center