The efficient management of increasing water cuts in oil fields is paramount for sustaining profitability and minimizing environmental impact. This article presents a comprehensive case study conducted by Saudi Aramco, focusing on the integration of hybrid flotation technology into a gravity water/oil separator (WOSEP) to enhance deoiling efficiency and reduce operational costs and carbon emissions.
The retrofit involved merging enhanced gravity separation with induced gas flotation (IGF) within the same vessel, resulting in significant improvements in deoiling capacity, outlet oil-in-water content reduction, and operational efficiency. Detailed insights into the design, operation, and performance of hybrid flotation systems are provided, offering valuable guidance for similar initiatives in the petroleum industry.
Introduction
Petroleum production facilities face escalating challenges with increasing water-production rates during crude-oil extraction, particularly in waterflooding operations for secondary oil recovery. This trend not only escalates operational costs but also intensifies environmental concerns, particularly regarding energy consumption and carbon emissions associated with water-handling processes.
In response to these challenges, Saudi Aramco embarked on a pioneering initiative to enhance water-deoiling efficiency by integrating hybrid flotation technology into a conventional gravity WOSEP.
This case study presents a comprehensive analysis of the design, implementation, and outcomes of this transformative project, offering valuable insights for the broader petroleum industry.
Methodology
The upgrade process commenced with an assessment of the existing WOSEP system and its operational challenges.
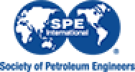