The SPE workshop, “Separation Technology and Challenges for the Low-Carbon Future,” was a collaborative effort comprising members from across the energy industry, including oil and gas producers/operators, technology providers, service companies, contractors, and consultants. It was the first separation technology workshop organized by SPE together with the Separations Technology Technical Section (STTS). This workshop aspired to be an interactive and collaborative effort to
- Share state-of-the-art separator design and troubleshooting methods.
- Develop future separation needs and gap statements.
- Propose a forward path to close the gaps.
More than 74 delegates had opportunities to share knowledge about separation problems and the future challenges the industry faces as part of the energy transition. Presentations were made on a variety of technical topics including
- Design and modeling.
- Energy transition.
- Case histories.
- Alternative technologies and applications.
- Reducing environmental impact and sustainability.
- Produced-water separation challenges.
It was an interactive event, with breakout sessions where delegates engaged in discussions and brainstorming.
We would like to thank our sponsors, Wolf Process Technologies, SouthWest Research Institute, and TechnipFMC, for making this workshop successful.
Keynote Speaker
The workshop was kicked off by keynote speaker Ken Arnold, who has worked in the oil industry for many decades. This session was about the challenges and lessons learned in the deployment of new separation technologies including the successes, failures, and hardships experienced by a variety of companies over several decades.
The Workshop
Session 1 focused on design and modeling, highlighting the design and modeling of separators. The presentations covered advancements in modeling techniques, computational tools, and empirical approaches. They also discussed the limitations of existing approaches and explored potential areas for future breakthroughs.
- Entrainment Modeling—Logan Grim, Saudi Aramco senior oil process engineer
- A Predictive Methodology To Determine Gas Evolution Kinetics for Improved Separator Design—Clint Aichele, associate professor and Ward Faculty Fellow at Oklahoma State University
- Combining Analytical and Empirical Models With CFD Results for Enhancing Performance Prediction of Separators—Henri Witteveen, Kranji Solutions lead process engineer. Field examples of insert screen installation and challenges during deployment.
Session 2 on energy transition focused on the role of separation processes, exploring designs, applications, and challenges related to hydrogen, carbon capture and storage (CCS), low-carbon fuels, and other areas.
- De-Risking CO2 Capture With Amine Solvents—Fred Closmann, research engineer at University of Texas
- Overview of CO2 Capture Technologies for Separation of CO2 From Exhaust Gas Streams—David Bahr, manager CCUS & Future Energies at Wood
- Making Carbon Capture More Viable—James van der Lee, VP, technology, at DexPro
Session 3 presentations focused on reducing environmental impact and promoting sustainability and included low-pressure gas capture topics, such as eliminating venting, avoiding water overboarding, and managing waste streams like CO2, H2S, N2, and sand. The session also highlighted strategies for minimizing filter and adsorbent waste in water-treatment processes.
- Navigating Emission Capture: Unveiling the Good, the Bad, and the Ugly in Operating Experiences—Juan Montes, chief technology officer, Transeparation S.A.
- Reducing Emissions Through Innovative Design (in the Permian)— Julia Spadaccini, Permian GHG program manager at ExxonMobil
- Methane Emissions—Tanks Are Not a Source (Process Issues Are)—Roy Hartstein, founder and president, Responsible Energy Solutions.
- Selecting Optimum Sand Control/Completion Strategy.
Session 4 focused on alternative technologies and applications, highlighting how innovative solutions, such as inline or compact separation and membranes, can outperform traditional processing equipment in overall cost, size, performance, and reliability. The session examined the successful use of these technologies in specific oil and gas applications and explored the challenges limiting their broader adoption, as well as strategies to overcome these gaps.
- Membrane Technologies Are Key Enablers of the Energy Transition—Ryan Lively, director, Center for Understanding and Control of Acid Gas-Induced Evolution Materials for Energy, an Energy Frontier Research Center of the US Department of Energy, Georgia Institute of Technology
- Achieving New Efficiencies With an Integrated Low-Pressure Separator and Intermediate Heating System—Sander Baaren, technical manager decarbonization surface, TechnipFMC
- Inline/Compact Separation for Low-Carbon Future—Natallia Shutsina, global product manager, Sulzer, and global product manager—inline, cMIST, hydrocyclones
Session 5 covered practical aspects of troubleshooting and case histories. The presentations focused on troubleshooting techniques, including carryover measurements, CFD studies, and digital twins, highlighting their current applications and limitations. The discussion also featured examples and case histories for deeper insights.
- Unleashing the Power of Edge Software and Digital Twins for Emissions Reduction in Onshore Shale Production and Separation Processes—Ryan Malone, operations manager, TechnipFMC, Methane Solutions: Surface E-Mission
- Impact of Proper Separator Design on LTS Performance and Overall Emissions: Test-Run and Equipment Redesign—Federico Petracci, lead process engineer and CAE specialist, Transeparation S.A.
- Separation Issues Addressed via Digital Twin—Ed Hernandez, senior consultant, MySep
Session 6 covered produced water and separation challenges. The presentations focused on bulk-fluid-handling challenges in two- and three-phase separation such as slugging, increasing produced-water fraction, and sand handling. They also explored how inlet/outlet configurations and internal components impact the effectiveness of oil/water separation.
- Separation Challenges in Deepwater Developments—Graeme Smith, process engineer, GOM operations, Murphy Oil Corp.
- Using HDPE in Place of Stainless Steel for Cyclonic Jetting Systems—Mark Wolf, CEO, Wolf Process
- Designing Separators for High Water-Cut Production—Ted Frankiewicz, consultant–engineering advisor (retired)
Breakout sessions featured discussions between different groups on future separation challenges.
Attendees split into groups of 10 or less to discuss future separation needs and gaps and forward paths to close the gaps. The groups reported back to the workshop their summary of gaps and paths.
The organizers of the workshop posed a set of seven questions regarding gaps between the separation technologies and practices currently in use for oil and gas production and those that will be needed for low-carbon and energy transition needs, in either traditional oil and gas production or in new areas. Each of the approximately 50 attendees were asked to identify a gap area as the most important to address.
The seven questions and the number of votes each question received are as follows.
1. What gaps are present in current design methodologies and tools for traditional oil and gas carbon footprint reduction? What design methodologies and tools are most needed to meet energy transition/low-carbon needs? What work is needed to enhance or develop these methodologies and tools? (14 votes)
2. What design methodologies and tools are most needed to meet energy transition/low-carbon need? What work is needed to enhance and/or develop these methodologies? (0 votes)
3. What separation focuses are the best places to reduce oil and gas operations' carbon footprint? What are the constraints on these? How can we address these constraints? (0 votes)
4. What separation focuses are needed to progress low-carbon energy? Where should the industry put its effort into addressing these areas? (1 vote)
5. What separation lessons from traditional oil and gas production are most applicable to energy transition/low-carbon energy separation? (3 votes)
6. What separation gaps are most pressing for traditional oil and gas production? What are the options to address these gaps for industry? (5 votes)
7. What separation technology gaps are most pressing for energy transition or low-carbon energy needs? What are options to address these gaps for industry? (9 votes)
The attendees were divided into three groups to discuss the gaps described in Questions 1, 6, and 7 and to define possible paths to closing the gaps. Each group presented a summary of their findings and recommendations to the entire workshop.
Synopses of these summary presentations are provided below.
Q1. What gaps are present in current design methodologies and tools for traditional oil and gas carbon footprint reduction? What design methodologies and tools are most needed to meet energy transition/low-carbon needs? What work is needed to enhance or develop these methodologies and tools?
Presenter: Henri Witteveen (Kranji Solutions/MySep)
1. Technology Gaps
- It is common practice to develop a basic system design without engaging EPCs and vendors early in the design process. This can lead to implementation problems and costly refitting of separation units.
- Generally, the current approaches for the early design stage only rely on “checklists” with criteria for separator design (e.g., K-value limits), but these are not necessarily good indicators of performance.
- Incomplete links between researchers and developers of operational separation systems.
- The availability of field data for improving models (for example by joint industry programs) is lacking.
2. Paths to Closure
- Initiate a comprehensive team approach to design from the beginning.
- Separators and the components upstream and downstream form a system of interacting devices. Improving the overall performance of the system and reducing its carbon footprint may require a different type of interaction between operators and the EPCs during the entire span of system conceptual design to system startup than is currently in place.
- Consider the carbon footprint of the entire chain of fabrication and shipping of the components (especially the separator vessel). Rely as much as possible on the standard plate sizes (thickness, width, length) when sizing a vessel.
- Develop more complete performance models applicable to field conditions.
- More field data are required to validate/support separator design tools. Field data and field-realistic data are being collected but the ability to share these data is slowing its broader usage.
- Better understanding of separator internals and their performance over the life of the system can reduce the size of the separator and the need for expensive and wasteful future equipment changes.
- The updated API 12J and efforts to align GPSA and Norsok are attempts to close the gaps in design methodologies.
- There are many more variables affecting liquid/liquid separation than in the case of gas/liquid separation. More and better design tools that take into account such things as emulsions, demulsifiers, and surfactants are needed. This will likely require more basic types of testing to quantify the interactions in liquid/liquid separation.
- Improve the links between university research and operators.
- More and better integration between universities and industry could/should enhance research into separation performance.
- Explore ways to make the research relevant to real systems and to provide a path to research publication.
- This will also enhance the flow of trained process engineers into key industries.
Q6. What separation gaps are most pressing for traditional oil and gas production? What are the options to address these gaps for industry?
Presenter: Jay Stell (Schultz Processes)
1. Technology Gaps
- Instrumentation
- Missing technology
- There is a lack of liquid carryover instrumentation for gas/liquid separators.
- There is a need for low-cost and safe level instrumentation that can measure foams and emulsions.
- Similarly, there is a need for instruments that can detect and quantify sand and other solids in separator vessels.
- Generally, there is a lack of integration of the instrumentation and operational control scheme during the separator design phase.
- Missing technology
- New technologies are needed for treating high water flows. For example, membranes look promising as a replacement for walnut shells, but handling of backwash could be a problem.
- There is a lack of integration of all the teams or departments during the separator design phase.
- There is a need for more robust internals for removing and handling sand, waxes, and other solids.
- There is a need for the development of designs and design guidelines for mist elimination for challenging nontraditional fluids (e.g., CO2).
2. Paths to Closure
- A cultural change is needed to recognize the importance of developing essential instrumentation and how it is deployed. Possibly a JIP-based on the FRI model could be created to address industrywide needs. Similarly, project execution must change to have stakeholders include an instrumentation and automation team early and throughout project development.
- Find ways to increase the pace of advancing the TRL of membranes into the realm of field-like fluids and applications. In particular, develop water-treatment technologies that do not rely on consumable materials or internals.
- Similar to the instrumentation-focused gap, a cultural change is needed to bring all stakeholders into the early design stages of a project.
- Develop internals that can assist in the separation of solids (i.e., not gravity alone, and possibly on a continuous basis). The benefits of these approaches must be quantified to justify the investment.
- Develop multiphase fluid property and databases for fluids that we are now seeing in the energy transition and low-carbon arena. Define what improvements are needed in mist-elimination equipment and communicate the need for their development to the vendors and EPCs.
Additional gaps were identified but the session time limit prevented them from being addressed.
- Flare and relief valve design guidelines.
- The real impacts, pro and con, of chemicals.
- Implementation of low-grade energy recovery could reduce the carbon footprint of a system.
Q7. What separation technology gaps are most pressing for energy transition or low carbon energy needs? What are options to address these gaps for industry?
Presenter: Kevin Supak (Southwest Research Institute)
1. Technology Gaps
- Lack of validation data for equations of state and process models.
- Lack of understanding of new energy transition and low-carbon processes.
- Lack of multiphase models and operational experience with nontraditional fluids.
2. Paths to Closure
- There are fluids and fluid combinations that are of interest to the energy transition and low-carbon areas, e.g., CO2, NH3, H2, biofuels, fatty acids.
- Improvements in the equations of state for these fluids are needed. For example, the complexities of CO2 behavior near its critical point.
- Research into production of biofuels from widely different feedstocks is needed to advance the TRL of those systems.
- New processes should lean on existing oil and gas experience.
- There is a need for improved connection with process developers to advance the TRL of new processes.
- The models for separation processes in oil and gas operations need to be extended and validated for different applications.
- Explore ways to extend the experience with H2 in traditional oil and gas refineries and chemical plants to the "new" hydrogen technology.
- Explore ways to extend the experience with water treatment in traditional oil and gas production operations to geothermal energy extraction to deal with CH4 separation and chlorides.
- Multiphase models
- Multiphase CO2 presents different flow behavior due to its lower density ratio when compared to traditional oil and gas fluids.
- Research into the effects of fouling and pipeline integrity is needed to understand the long‑term effects of handling these fluids individually and in combinations.
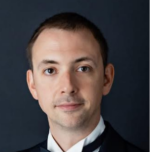
Logan Grim is a senior oil process engineer at Aramco, based in Dhahran, Saudi Arabia. He started his career with the engineering contractor Foster Wheeler, now Wood, where he worked on the process design and construction of refining, petrochemical, LNG, and upstream facilities before moving into process systems engineer.
In 2019, he joined Aramco in Saudi Arabia work as an oil processing engineer, as part Aramco’s central engineering services organization. In this role he is responsible for the process aspects of capital projects, operational troubleshooting and consultation for oil facilities across Saudi Arabia.
In these roles he has developed numerous applications for equipment sizing and rating and physical property prediction. Logan is a chartered member of the IChemE and was Chairman of the Separation Technology Technical Section (STTS) from 2020-2023.
He holds an MEng in chemical engineering from Imperial College London.
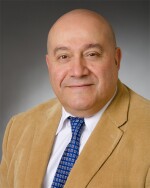
Wally Georgie has over 4 decades of experience in the oil and gas industry, namely in oil and gas operation, processing, separation, fluid handling and system integrity, hands-on in operation troubleshooting, debottlenecking, oil/water separation, process verification, technology evaluation, corrosion control, system monitoring, water injection and enhanced oil recovery processing, and all other fluid- and gas-handling issues including handling sand and solid production in process systems, production chemistry, flow assurance, and integrity management.
He worked initially in the service sector in the US, UK, different parts of Europe, and Middle East between 1979 and 1987. This was followed by a career with Statoil (Equinor) in Norway from 1987 to 1999, focusing mainly on daily operation, new field project developments and production systems related to oil and water separation issues, gas treatment sweetening and dehydration systems, produced water management, and handling solid-production issues. He has been working as an independent consultant globally since March 1999 in similar areas of oil gas production.
In addition, Georgie has also been working as an expert witness in legal oil and gas cases in the UK, US, and Australia. He served as SPE Distinguished Lecturer in 2016–2017 and currently serving as the Chairman of the SPE STTS technical group from 2023.
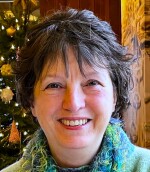
Peggy Lane's engineering career spanned over 30 years in contracting and oil and gas, with 24 years working for bp. Lane was bp Upstream's subject matter expert for gravity separation and sand handling and is a former chair of the SPE Separations Technology Technical Section.
During her career she held process and production engineering roles in the US, UK, and Middle East. She also has extensive experience in produced water handling and waterflooding.
She holds a degree in chemical engineering from California State Polytechnic University, Pomona.
She retired from bp in 2021 and now volunteers time to a variety of causes. She lives in Oregon with her husband Doug and their cat Buster.
Mark Wolf is the founder and CEO of Wolf Process Technology. He has designed and built process equipment and facilities for over 30 years and has eight granted and two pending patents. With an extensive background in both produced water treatment and solids handling, he started Wolf Process in 2020 to provide cost effective systems for handling oilfield solids.
Wolf is active in the Society of Petroleum Engineers, and the Produced Water Society serving on the SPE Production and Facilities Technical Advisory Committee, the SPE Distinguished Lecturer Committee, and is a regular speaker at Produced Water Society events.
He holds a BSc in petroleum engineering from Texas Tech University.