As the towering Olympus tension leg platform (TLP) entered service in July, it marked the beginning of a mission to extend one of Shell’s most productive deepwater projects in the US Gulf of Mexico (GOM) to at least 2050. The oil company said this is the first time an additional deepwater production facility has been added to an existing field in the GOM.
Shell expects to begin first production from the newly commissioned Olympus TLP at the Mars field next year. The Olympus is the largest TLP the company has deployed in the GOM. The Mars field is located about 100 miles south of New Orleans in approximately 3,100 ft water depth. With 24 well slots, the Olympus TLP will produce up to 100,000 BOEPD from Shell’s West Boreas, South Deimos, and Deimos discoveries. The reservoirs are located at depths ranging from 10,000 ft to 22,000 ft.
When the Mars field began production in 1996, Shell estimated up to 700 million BOE of recoverable reserves. Since then, the field has produced more than 770 million BOE, and it is estimated that there may be 1.1 billion BOE yet to be produced. Shell is calling the field extension project Mars B.
Shell has gone to great lengths to plan for a decades-long development that ties in new innovations with lessons learned from five other TLPs that Shell operates in the GOM. “It is a next-generation [TLP] just in the sheer size and capability we have with this rig,” said Arno van den Haak, Shell’s well delivery team lead for the GOM.
At 126,000 tons, the Olympus TLP is more than twice the displacement of the neighboring Mars TLP located only a mile away. The Olympus TLP’s drilling rig has a 2-million-lbm hook load, double the load of the Mars TLP rig, giving it the capability to drill and complete wells at depths of up to 35,000 ft—the deepest for a Shell platform.
An improvement over previous TLPs deployed by Shell is the full integration of the power unit into all aspects of the floating facility. Putting the drilling rig module on the same power grid as the rest of the TLP optimizes the drilling process and enhances overall energy efficiency of the facility.
In prior designs, Shell had placed its ballast pumps inside the TLP columns. On the Olympus TLP, the pumps have been placed on top of the 205-ft-tall columns where they are easier to access and maintain. The total height of the Olympus TLP, from the hull to the top of the derrick, is 406 ft and the air gap between the lowest deck and average sea level is 112 ft.
One driver for designing a larger, taller TLP was the new criteria for 100‑year storms in the GOM that were adopted after Hurricane Katrina hit the Gulf Coast in 2005. In the event of a major storm, the rig portion of the TLP will be held down with heavy-duty hurricane clamps, using an updated design based on lessons learned.
Van den Haak emphasized that not only is the rig a leap forward for Shell in terms of safety and operational efficiency, but also the field itself will be an improved undertaking compared with the existing infrastructure.
“When I look at our [original Mars] wells and calculate the amount of steel that is on the ground for these wells and then I compare it to the Olympus wells, we’re going to be using about three times as much steel,” he said.
Seventeen of the 24 well slots are reserved for production risers from the existing Mars reservoir wells and the other seven well slots are reserved for the deeper Deimos higher-pressure reservoir. In addition, the project is also developing in parallel the West Boreas and South Deimos fields as a subsea tieback to the Olympus TLP, which will be the first wells to be completed with FMC Technologies’ new 15,000-psi subsea Christmas trees.
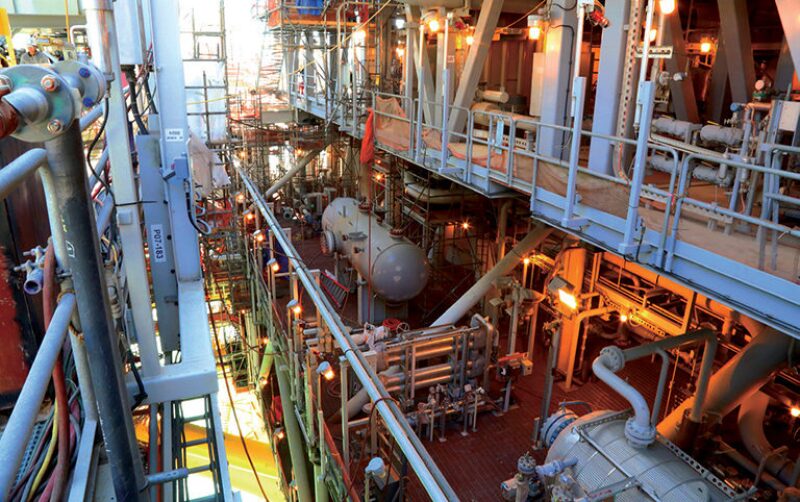
Metal-to-metal hangers will be installed inside the Olympus TLP wellbores because they have longer service life than conventional elastomer hangers.
Working ahead of the Olympus TLP’s arrival since last year, the Noble Bully One drillship has recently finished drilling the 24 top holes to a maximum depth of 6,100 ft for the 70 wells that will eventually develop the Mars field. The Noble Bully One represents a new class of compact drillships designed to be 160 ft to 260 ft shorter than the newest sixth-generation drillships. Shell codeveloped the drillship with Frontier Drilling, later acquired by Noble.
The Olympus TLP is equipped with an integrated managed pressure drilling system, which will reduce operational time typically used to rig up temporary drilling equipment to the rig and improve safety conditions.
Shell anticipates that enhanced technologies will allow the Olympus TLP to increase its overall production capacity without increasing the weight load on the hull. For example, advances in lightweight composite technology that reduce payload for risers and topsides facilities could allow expansion of the current 100,000 BOPD capacity.
“We have this pool of space and payload that we can choose to use in different ways and that opportunity increases as technology advances,” said Mark Lindsay, the Mars B project manager at Shell.
Part of the future plans for the Olympus TLP include adding a waterflooding facility as the field’s rate of production declines, thus demanding higher pressures to be reintroduced to the reservoirs.
Shell says the project goes farther than current regulations call for regarding planning for well control by drafting detailed relief well and containment plans for every well scheduled to be drilled for the Mars B project. Operators in the GOM are only required to show how they can achieve “cap and contain” on a subsea well after a blowout. They must also list the rigs available to drill a relief well and the time needed to drill the relief well, but not its borehole trajectory.
“The density of the TLP wells, the requirements for equipment access, ranging, positioning and borehole surveying are becoming more critical,” van den Haak said. “So the key is to plan those details well ahead and not when there is a real emergency.”