Carbonate reservoirs require effective acid stimulation to improve well productivity. For long horizontal wells, a complicating factor has previously been the difficulty of controlling acid placement along the reservoir section. The Smart Liner (SL) concept solves this problem. It consists of a number of small holes spaced in such a way so as to distribute acid evenly along the reservoir interval.
Fig. 1 shows a schematic of the concept. Without the need of a coiled tubing, acid is bull-headed at a high rate from surface through the production tubing and enters the liner from the left. The liner does not have to be horizontal but very often is. When acid reaches the first hole, which typically has a diameter of 3–6 mm, the pressure drop across the hole is so large that only a small portion of the acid exits the liner through the hole; the remaining acid continues along the liner until it reaches the next hole where the process is repeated. Appropriate hole spacing ensures that acid is distributed with a given acid coverage (dosage) in barrels of acid per foot of reservoir section. The small cross-sectional area of the holes results in focused acid jetting at velocities often exceeding 20 m/s (65 ft/s). The jetting helps promote wormhole formation leading to substantial productivity enhancement.
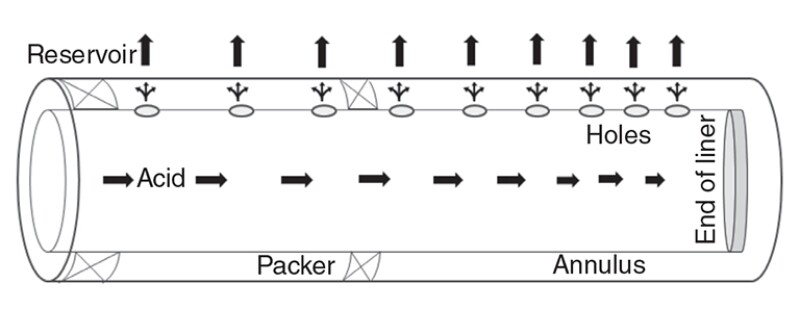
The hole-spacing design requires dedicated software which must take into consideration constraints pertaining to the reservoir, the well, and the pumping equipment while minimizing operational complexity. The tool should also yield a quick answer to enable the user to optimize the final design post drilling and provide a running tally consisting of the sequence of liner joints to be run in hole. In heterogeneous reservoirs, it is typically required to segment the wellbore with swellable packers to isolate sections with different reservoir pressure and/or fluid mobility, and the SL concept readily accommodates that. Also, since the subsequent stimulation relies on matrix acidization, the tool must ensure that fracturing pressures are not exceeded.
The original limited-entry liner (LEL) technique dates to the early 1960s and was proposed for fracturing applications (SPE 530). Reviews by Somanchi et al. (SPE 184834) and Weddle et al. (SPE 189880) suggest that it is still widely applied for such purposes. In the late 1990s, Maersk Oil adapted the concept to effectively stimulate extended-reach wells in its North Sea chalk reservoirs on a large scale. Hansen and Nederveen (SPE 78318) refer to the technology as controlled acid jetting (CAJ). In the following years, the CAJ technique was implemented in more difficult formations such as a 0.1 mD chalk reservoir (SPE 144159) as well as in a tight, gas-bearing formation (SPE 123979). Balsawer et al. (IPTC 17611) designed multizone completions in ultralong wells in a giant field offshore Qatar, which comprised more heterogeneous limestone formations. Other field implementations have been described by Issa et al. (SPE 171779) for a super-giant reservoir offshore Abu Dhabi.
Past deployments have concentrated on extended-reach wells with reservoir temperatures up to 210°F. Over the past year, ADNOC has significantly expanded the operational envelope of the Smart Liner concept. Fig. 2 summarizes the variation in completed reservoir length and average permeability for 80 well designs. Table 1 shows that reservoir temperatures vary from 140°F to 300°F.
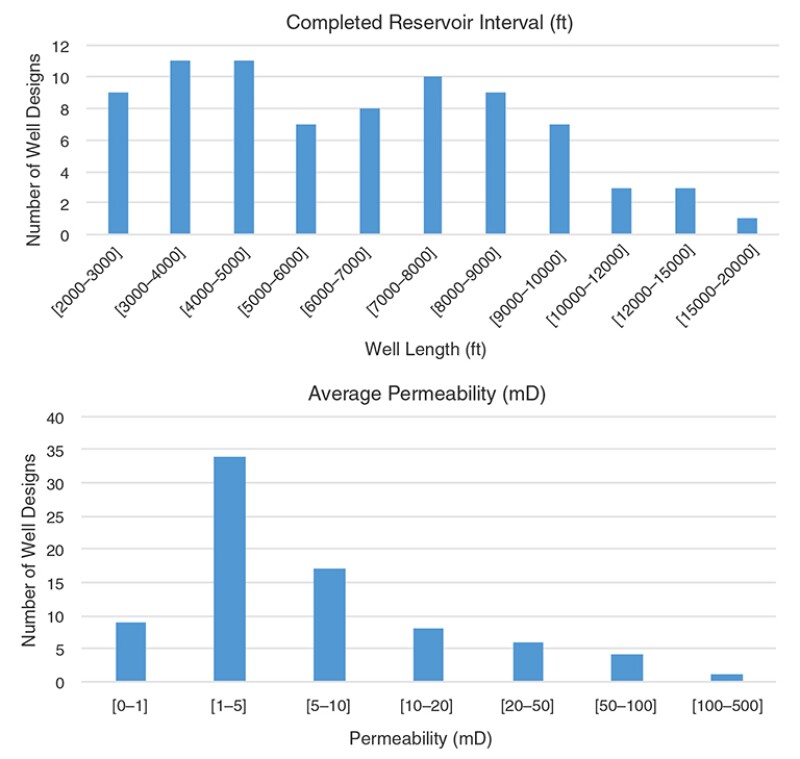
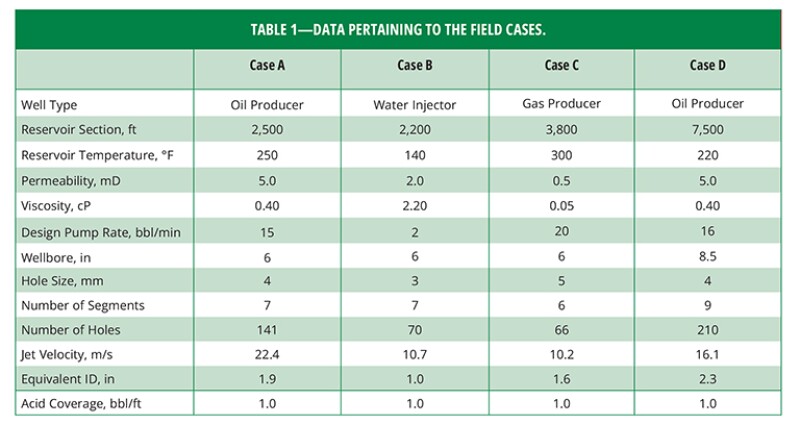
Descriptions of Four Field Cases
Four field cases are presented with relevant data listed in Table 1. The equivalent inside diameter (ID) is defined as the diameter of a pipe restriction which would have the same total cross-sectional area as that of all the holes combined. Details pertaining to general hole-spacing-design guidelines can be found in SPE 207904. For each case, a fine-gridded numerical simulation model was constructed to verify that the desired pump rate could be achieved without fracturing the reservoir and while honoring the maximum allowable surface pressures. Nodal analysis was conducted to assess whether the holes would restrict post-stimulation well performance. The key conclusion was that an equivalent ID larger than 1.0 in. for oil producers and water injectors would not impose any significant pressure drop. The threshold ID for gas producers was slightly higher.
Field Case A—The First Onshore Pilot Well
Field case A represents the first onshore pilot test. The reservoir depth was 8,500 ft and the length of the completed 6-in. reservoir interval was 2,500 ft. The permeability was estimated to be roughly 5 mD, which would enable a pump rate of 15 bbl/min (21,600 B/D). To ensure that the design rate could be achieved, a friction reducer was added, and the actual pump rate reached 17.8 bbl/min.
As shown in Fig. 3, the rate was gradually ramped up in steps, separated by short falloffs to enable calculation of the instantaneous frictional pressure drop pertaining to each rate. These short shut ins made it possible to estimate whether all holes contributed to flow. An important observation is that the surface pressure continued to decrease during the main treatment period conducted at a constant pump rate, apart from a late increase caused by a reduction in friction reducer. This implies that significant skin reduction is achieved throughout the treatment and justifies the use of an acid coverage of 1.0 bbl/ft, which is substantially higher than for conventional coiled-tubing stimulation. The key reason is that the jet velocity is very high, which helps the initial wormholing. Over time, the wormhole tip velocity decreases due to leakoff, and once it drops below the optimum velocity (which has to be inferred from coreflood studies), further wormhole growth quickly stops (for conventional acid systems), maximum skin reduction is reached, and the surface pressure begins to increase.
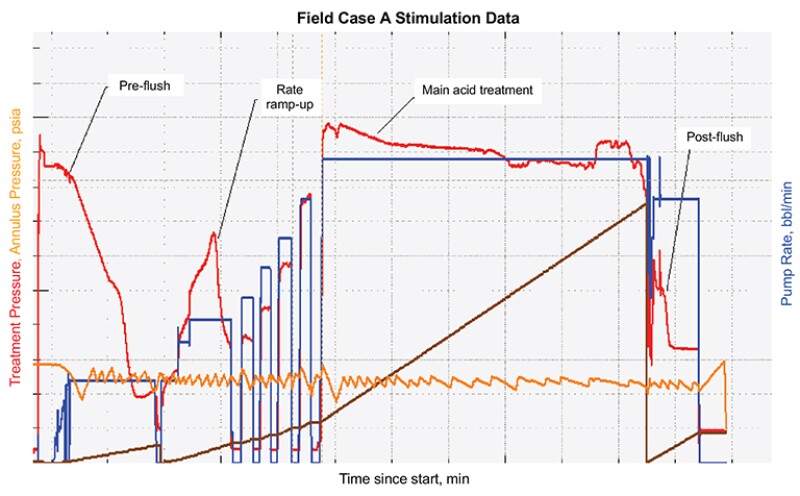
The productivity index more than doubled, as quantified by multirate tests before and after stimulation. The well was put on production for several months before stimulation took place to reduce the impact of transient effects related to the low matrix permeability.
Field Case B—First Water Injection Pilot Well, Low Injectivity, 3-mm Holes
Field case B is a water injection well in a shallow reservoir onshore Abu Dhabi. Due to the tightness of the matrix, implementation of technologies to improve productivity/injectivity is a key factor in the development of this reservoir.
A combination of low permeability, short well length, and high oil viscosity limited the pump rate to 2–3 bbl/min. A number of potential test designs were made for 3-mm and 4-mm holes. For each hole size, the total number of holes was varied and the resulting jet velocity, average distance between adjacent holes, pressure drop across the last hole, and equivalent restriction ID imposed by the holes were tracked (Figs. 4 and 5).
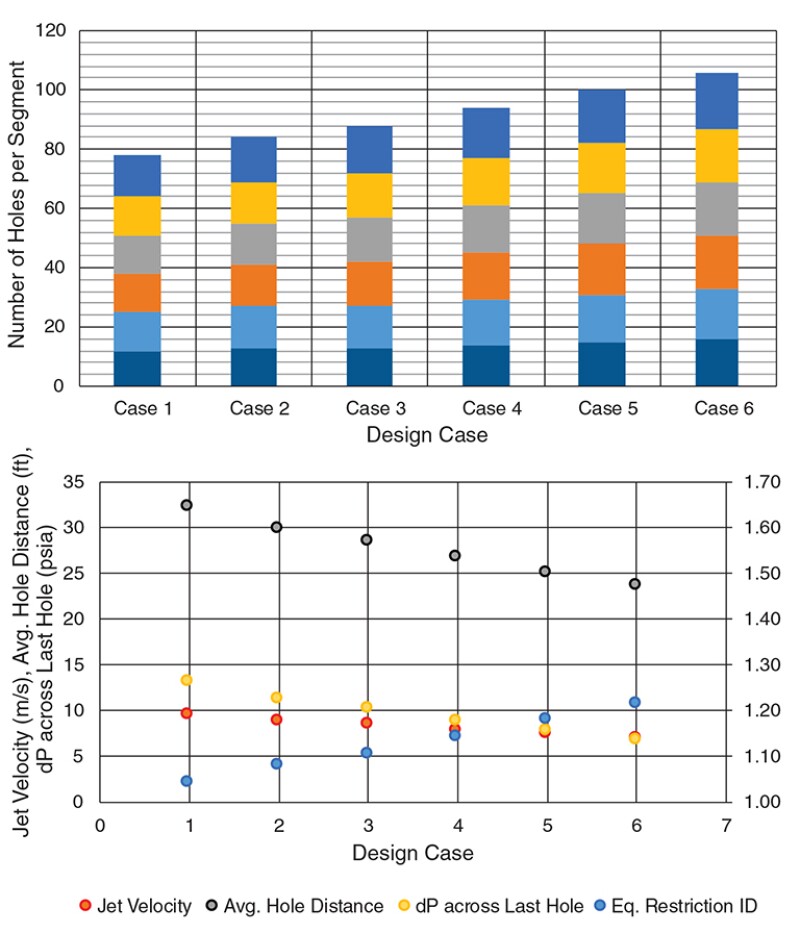
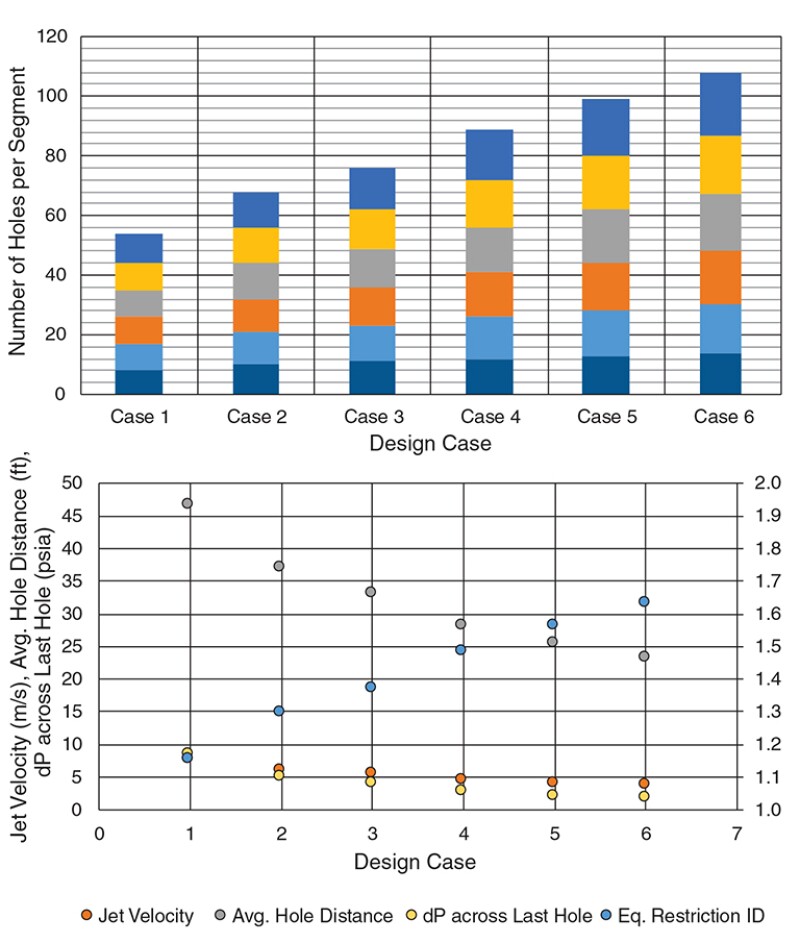
A key point is that a multitude of designs will yield a mathematically uniform distribution of acid along the liner for a particular pump rate. Not all of them are suitable in practice, however. Nodal analysis was applied to eliminate designs where the number of holes would reduce subsequent injection performance. The second important factor relates to the average liner hole distance, which according to recent studies by Schwalbert et al. (SPE 184834) should lie in the range of 30–60 ft. These considerations led to progressing with design cases 3–5 with 3-mm holes. The 4-mm designs yielded a jet velocity which was deemed too low and were discarded. The well was split into seven segments isolated by swellable packers; the first segment covered the distance from the top of the liner to the reservoir entry point and was blanked off. To honor a uniform acid coverage, it was necessary to have a gradual increase in the number of holes along the well since the hole size in the current design was kept constant. The required joints plus some contingencies were then earmarked for machining of the holes prior to drilling the well.
The well was brought on stream 4 months prior to stimulation to establish a solid baseline free from transient effects. The comparatively low reservoir temperature of 140°F, combined with cooling of the rock for 4 months, helped slow down the acid-rock reaction rate and hence promoted deeper wormholing. Operational details can be found in IPTC 22043. A production logging tool (PLT) conducted post-stimulation showed an even injection profile along the horizontal drain, which was a big improvement compared to neighboring wells. A threefold increase in the injectivity index was observed based on the performance exhibited over several months after the job was completed.
Field Case C—The First Gas Well, Ultrahigh-Temperature, Tight Reservoir
After two successful installations in onshore reservoirs, field case C targeted a challenging offshore reservoir, which was deep, hot, very tight, and gas-bearing (SPE 207527). Given the high cost of drilling new wells, it was decided to sidetrack an existing well. After several attempts to lift in the sidetracked well, it proved impossible to establish an initial gas production rate prior to stimulation. Choosing this well as a candidate for Smart Liner deployment brought about a number of concerns. Given the tightness of the matrix, it was not clear whether acid would have time to penetrate deep into the rock. The 300°F reservoir temperature suggested that the 15% HCl acid would react quickly and dissolve only the near wellbore. The main acidizing treatment, however, went smoothly, with pump rates reaching 20 bbl/min. After a prolonged cleanup period, the well achieved a production rate above 30 MMscf/D, far exceeding expectations. It is believed that the low matrix porosity of 5% helped generate a higher interstitial velocity (velocity divided by porosity), beneficial for wormhole propagation.
Field Case D—7,500-ft Reservoir Section, Flow Profiling Pre- and Post-Stimulation
Field case D was from offshore Abu Dhabi. ADNOC was targeting low-permeability reservoirs by drilling longer wells as part of its aspiration to reach a 70% recovery factor while reducing the environmental footprint. One commonly held belief was that incremental production from drilling longer wells gradually tapers off above a certain threshold well length. Therefore, an important mission for this 7,500-ft-long well was to establish whether the toe would contribute just as much as the heel. Due to limited acid-volume capacity offshore, the stimulation had to be split equally into three stages. Although operationally more complex, this method provided the opportunity to test the impact of each stage separately. Fig. 6 shows that although the second and the third stages resulted in similar oil rates, the wellhead pressure (THP) was reduced after the third stage, indicating the acid did have a noticeable effect on the performance. A series of PLTs was performed pre- and post-stimulation to quantify where the incremental oil was coming from. Fig. 7 shows that the outer part of the well did not contribute to flow prior to stimulation, even though a choke increase did manage to deliver slightly more drawdown toward the toe. The post-stimulation results, however, were very encouraging. Even though the flow profile was not perfectly uniform, each interval now delivered substantial production. Instead of yielding just production acceleration, the stimulation was able to unlock additional oil.
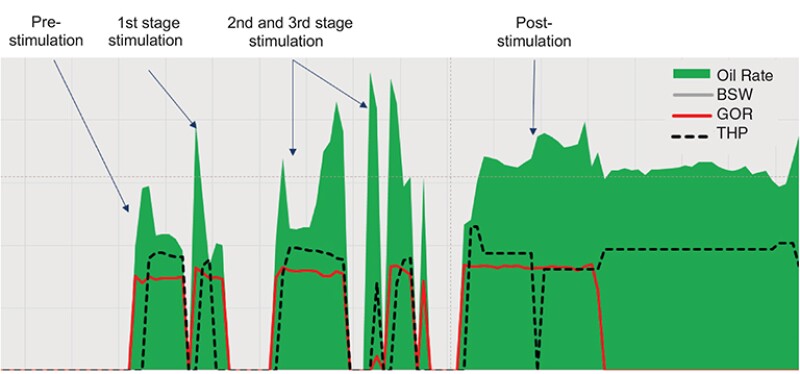
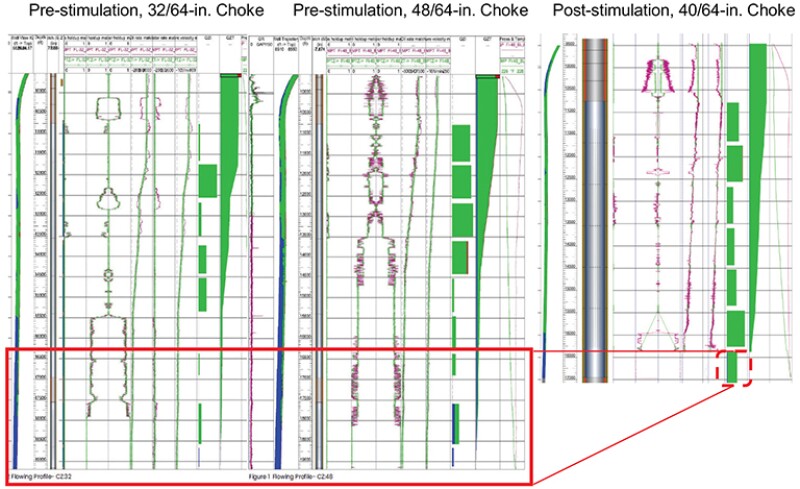
Conclusions
Results from the Smart Liner implementation have been very encouraging so far. The general observation is that productivity is at least doubled, and the entire wellbore contributes to flow, documented by pre- and post-stimulation production logging. The technique has been applied successfully to several oil producers and water injectors and to one gas producer. Although still at the early stages of deployment, a number of points are worth highlighting:
- The technique is well suited for both short- and extended-reach wells. There is, in our opinion, no other matrix-acid stimulation method that can ensure good flow contribution from long drains.
- The technique works for carbonate rocks of different lithology. Heterogeneity can to some extent be mitigated by appropriate placement of swellable packers and adjustment of hole density prior to stimulation.
- All rocks so far have been stimulated with 15% HCl, even though the reservoir temperatures are high. The reason for the successful results is related to the high initial velocity provided by the small holes, providing the right balance between convection and diffusion. For water injectors, pre-stimulation baseline injection helps cool down the near-wellbore region.
- A low pump rate (2–3 bbl/min) may in some cases be acceptable as long as the cross-sectional hole area is adapted to ensure sufficient initial acid jet velocity.
For Further Reading
IPTC 17611 Multizone Completion Design for Long Horizontal ERD Wells in Al Shaheen Field by A. Balsawer, S. Hirani, P. Lumbye, A. Krog, and V. Bonnell,Maersk Oil Qatar AS; M.R. Jaafa, and I. Abul-Hamd, Qatar Petroleum.
IPTC 22043 First Smart Liner Monobore Completion in Giant Carbonate Reservoir in Abu Dhabi Provides New Opportunities for Tight Reservoirs Development by E. Barragan, A. Jimenez, R.V. Rachapudi, R. Albarracin, and F. Quintero, ADNOC Onshore; and K. Mogensen, ADNOC. [Paper was prepared for 2022 IPTC and will be available post-conference.]
SPE 123979 Development of a Thin Low Permeability Gas Field with Spiraling Dual Lateral Horizontal Wells: The Halfdan Northeast Field by L.B. Christiansen, Maersk Oil; and M.W. Jeppesen, P. van Lingen, and M.H. Rod, Maersk Oil and Gas AS.
SPE 78318 Controlled Acid Jet (CAJ) Technique for Effective Single Operation Stimulation of 14,000+-ft-Long Reservoir Sections by J.H. Hansen and N. Nederveen, Maersk Oil and Gas AS.
SPE 171779 Production Optimization of Maximum Reservoir Contact Well by Utilizing Acid Stimulation with Limited Entry Technique by F. Issa, ZADCO; J. Abbott and A. Akbari, Schlumberger.
SPE 207527 First Successful Limited Entry Liner Deployed in a Sidetracked Gas Well, Offshore Abu Dhabi by A. Ladmia and F. Al-Hosani, ADNOC; E. Draoui, ADNOC Offshore; K. Mogensen, F. Al Hosani, and G. Edmonstone, ADNOC; A. Aldhanhani, F. Ballaith, A. Mohamed, and N. Juvarajah, ADNOC Offshore.
SPE 530 A New Development in Completion Methods—The Limited-Entry Technique by K.W. Lagrone and J.W. Rasmussen, Shell Oil Co.
SPE 207904 ADNOC’s Smart Liner Initiative—A Step-Change in Matrix-Acid Stimulation Efficiency by K. Mogensen and G. Edmonstone, ADNOC.
SPE 189486 Skin Factor Equations for Anisotropic Wormhole Networks and Limited-Entry Completions by M.P. Schwalbert, Petrobras and Texas A&M Univ.; and D. Zhu and A.D. Hill, Texas A&M Univ.
SPE 184834 Extreme Limited-Entry Design Improves Distribution Efficiency in Plug-n-Perf Completions: Insights from Fiber-Optic Diagnostics by K. Somanchi, J. Brewer, and A. Reynolds, Shell Canada.
SPE 144159 Return to Basics and Proper Planning Opens the Possibility to Acid Stimulate a Difficult Chalk Formation by M. van Domelen and N. Talib, Maersk Oil and Gas; and G. Glasbergen, Halliburton.
SPE 189880 Mining the Bakken II—Pushing the Envelope with Extreme Limited-Entry Perforating by P. Weddle, L. Griffin, and C.M. Pearson, Liberty Resources.

Kristian Mogensen, SPE, is a senior specialist with ADNOC HQ. He started his career in 1998 with Maersk Oil in Denmark. In 2014, he joined Eni in Milan as EOR technical advisor before joining ADNOC in 2017. His main technical interests include fluid phase behavior, enhanced oil recovery, pore-scale physics, and matrix-acid stimulation. He has more than 50 publications, holds 20 patents, and holds MSc and PhD degrees in chemical engineering from Technical University of Denmark. He is the recipient of the SPE 2020 Regional Reservoir Description and Dynamics Award and is a Distinguished Lecturer for the 2022–2023 season.
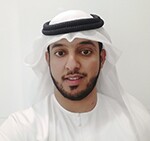
Maged Mabrook Yaslam, SPE, is a manager of reservoir and petroleum engineering at ADNOC HQ where he leads strategic technical streams to unlock subsurface opportunities and leverages advanced technologies in various domains of AI and digitalization, reservoir modeling and management, and petroleum engineering. His areas of interest cover integrated field development planning, reservoir flow dynamics and surveillance, and EOR applications. Yaslam is a certified International Professional Petroleum Engineer, SPE, Project Management Professional, and Chartered Petroleum Engineer, Energy Institute. He holds an MSc degree from Khalifa University and a BSc degree from UAE University. An SPE 2020 Regional Award recipient, he is active within local and regional sections and has contributed to SPE workshops and conferences within technical programs and organizing committees.
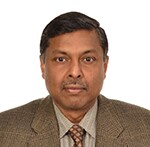
Ram Narayanan, SPE, has more than 30 years of industry experience in technical, commercial, leadership, and JV roles covering field appraisal and development, reservoir management, reserve estimation, reservoir value assurance, economic evaluation, and business planning and strategy. He is currently the vice president of Thamama Subsurface Excellence Center in ADNOC. Prior to that he held various technical and managerial roles for BP Exploration in Gulf of Mexico, Houston; BP-Reliance JV in India; BP-Eni JV in Indonesia; and BP Exploration in the North Sea, Aberdeen, Alaska, and Houston. Narayanan holds a PhD in chemical engineering from the University of Houston and a bachelor’s degree in chemical engineering from the Indian Institute of Technology, Madras, India.