Field testing is beginning to confirm laboratory work that indicates it is possible to achieve significant spurts in unconventional oil production using cocktails of chemicals.
BHP Billiton has pumped a blend of chemicals along with low-salinity brine to pressure-up shut-in wells. The result of these jobs, intended to reduce the risk of damage due to fracturing nearby, has been higher production lasting for months, including an estimated 20,000 barrels of oil from one well (SPE 187420).
Apache used its chemical blend to speed recovery of wells that had production bashed by frac hits. Positive results led to tests on underperforming wells that delivered strong, but short-lived, production gains (SPE 187192).
“You have a chance of getting your well back,’ said Michael Rainbolt, completions engineer, senior advisor for Apache Corp. who presented the findings at the 2017 SPE Annual Technical Conference and Exhibition.
Early tests using familiar chemicals and delivery methods have been reported in which the cost and the technical challenges associated with running a test are relatively low.
“Chemicals are something to do in the here and now that can potentially offer quick results,” said David Schechter, a Texas A&M University associate professor who has been hearing from operators and chemical makers interested in reliable information on how chemical treatments work, and how to adapt them to local conditions.

Operators are looking at ways to increase production using everything from large-scale gas injection to surfactants that free oil from the rock and ease its passage through ultratight pores.
Simulations run using rock testing data from Schechter’s lab predicted a significant production uptick with the right surfactant (SPE 187176).
“The gain is really strong initially, up to 24% early and up 8% over 3 years,” said Johannes Alvarez, who was a PhD student at Texas A&M University when he did the research trying to find an effective, affordable way to add production while fracturing without more water, sand, or pumping power.
Schechter is doing lab work for companies that are running field tests. One of them has performed trials that monitored approximately 50 wells based on lab work analyzing the influence of chemical additives and their likely effect in those reservoirs, Schechter said.
“It is giving them 15–20% greater EUR [estimated ultimate recovery]. Improved production is observed early in the well life during the initial production phase but the decline curve tends to remain higher for longer periods of time resulting in incremental EURs above that observed on wells with no chemicals,” he said.
The paper from BHP reported significant production gains in tests using a chemical blend developed in partnership with the University of Texas at Austin, said Chammi Miller, a research associate at the university who presented the paper at the SPE annual conference.
“Folks have been doing stuff in the labs for a few years, but I’ve only been hearing about people actually trying it in the field over the last few months,” said James Sorensen, principal geologist for the University of North Dakota’s Energy and Environmental Research Center, which is following the work to identify ways to add production in the Bakken formation.
While early reports show positive results, experience with chemical EOR indicates that there is a steep learning curve, typically requiring a multiwell program costing several hundred thousand dollars per well to identify the formulations and the delivery methods that work where their wells are producing, Schechter said.
Engineers familiar with stimulating wells by breaking up rock using hydraulic force have a lot of questions about how adding about 2 gallons of chemicals for every 2,000 gallons of water can make a difference.
“Operators are asking, why does this work?” Schechter said, adding, “Chemical companies are saying, we do not know how to explain it to operators.”
Those working on chemical treatments say the potential is great, but many companies remain focused only on maximizing production by drilling new wells. “As an industry we are not paying much attention to restoring our old wells,” Rainbolt said.
Apache quickly restored production lost in a well in the Woodford that had been hit during fracturing using its formula for treating wells with unspecified problems. It includes:
- Solvent to remove emulsions and remaining acid and its byproducts
- Hydrochloric acid to remove calcium chloride scale
- Hydrofluoric acid to remove fines from flow pathways
- Ammonium chloride and nano-fluid surfactant to reduce high capillary pressure
Quicker Comebacks
A frac hit sounds like a blunt force that can collapse the casing of a well or fill it full of sand. While there are incidents where that sort of damage occurs, more often the pressure from fracturing nearby interferes with production in subtler ways where it is hard to pinpoint the cause, according to Apache’s deep look at this problem (SPE 187192).
To speed recovery from these unspecified conditions, Apache developed a four-chemical mix to treat multiple problems limiting the flow in older fractures, including a surfactant to promote flow by reducing interfacial tension, and others to deal with fine particles of clay.
The goal is to quickly restart production in wells that otherwise could take years to recover. In one example, injecting the mix into a well in the Woodford Shale in Oklahoma soon restored production where the daily output had dropped 65% after a frac hit and had increased little over the next 100 days. The ingredients were evenly delivered along the lateral using coiled tubing.
Apache also tried the mix on underperforming wells. In one case, also in the Woodford, production quadrupled to better than the initial production after the mix was injected in a well though the gains were short-lived.

Its technical paper suggested that the job may have offered a short-term remedy for the problem that had limited production from the start—sand production early on had removed needed proppant from nearby fractures. If that left little sand to hold open the fractures, the treatment likely revived production but the poorly propped fractures closed soon after.
Rainbolt said the company is experimenting with new blends to help maximize production from older wells.
Starting Stronger
For anyone looking for a way to increase production from unconventional reservoirs using chemicals, surfactants are an obvious choice.
This class of chemicals has long been used for EOR because of its unique ability to free oil by changing reservoir rocks that attract oil—oil-wet—into ones that attract water—water-wet.
In ultratight unconventional rock, surfactants have the added value of reducing the interfacial tension—the force that resists the flow of oil when the rock surface is oil-wet. Adding a surfactant can create a water-wet surface on the wall of tight passageways to help expel oil and imbibe water-containing surfactant.
This will help improve recoveries, said Alvarez, who is now a reservoir engineer for Chevron. Schechter’s lab at Texas A&M tested multiple types of surfactants and they all delivered “better results than water alone.” The next question was: Which one worked best? With thousands of surfactants to choose from, and many effective blends, that is a tough one to answer.
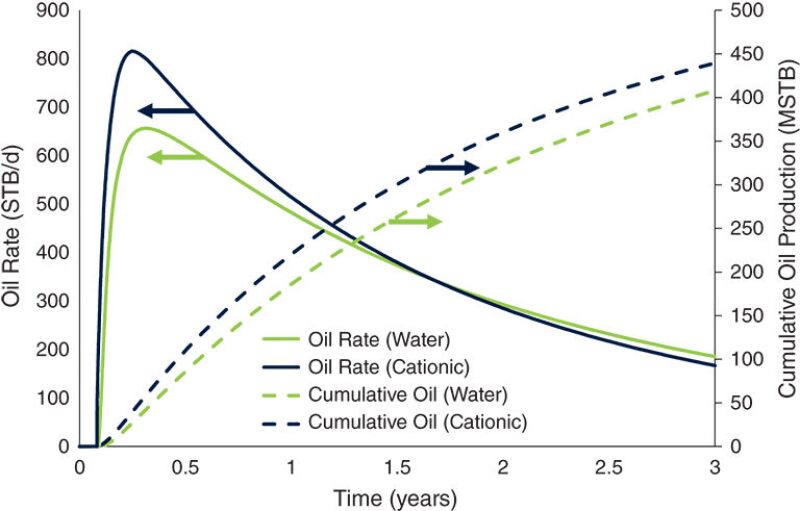
A recent paper on its testing program highlighted the lab tests it uses to measure how particular surfactants alter the wettability prior to core tests and how much oil each surfactant can remove from a rock sample.
In that round of testing, the most effective surfactants were the ones classified as cationic—the head of the molecule attaches to oil-wet surfaces, displacing oil, while its tail attracts water. Others tested were anionic with the head and tail functions reversed. Inject enough surfactant and the surface’s wettability flips from oil-wet to water-wet. What works best depends on the sort of rock and reservoir conditions. And the amount delivered to the reservoir has to be sufficient.
Equal concentrations of each surfactant—2 gallons of surfactant per 1,000 gallons of water—were compared using a handful of tests to measure their results.
That concentration was used because Schechter said it is generally effective. Using more than that is not likely to be cost-effective and using less (0.5/1,000 gal) is useless. “If they are cutting corners, they might kill the whole process” by ensuring the experiment will fail, Schechter said.
Defense Pays
After working 3 years to develop a chemical blend to increase production from unconventional wells, BHP found an opportunity to piggyback on another job for a first look at what it can do in the ground.
A blend was mixed into 20,000 barrels of brine (20,000 ppm NaCl) that was injected into an Eagle Ford well to preload it—raising the pressure in a well in hopes of reducing the risk of damage when fracturing is in progress nearby.
The ingredients tested in the lab were chosen to treat multiple problems that limit flow—reducing the interfacial tension to push oil out and bring water in, changing the rock surface chemistry to free oil, and dissolving calcite scale narrowing tight passages. They also had to make sure the acid in the fluid mix did not soften the rock reducing conductivity. Also, the chemicals chosen needed to be low-cost and environmentally acceptable, Miller said.
The paper said such a blend has been used in producing horizontal wells in the Eagle Ford and “strong well performance with significant uplift was realized as result of treatment on a dozen wells.”
The paper indicated the test parameters varied significantly from well to well. The preload fluid volume ranged from 3,000 to 20,000 bbl, shut-in times ran from 2 to 5 weeks, and the chemical mix injected varied from the one developed in the lab.
In one of the Eagle Ford wells, described as typical, the “incremental cumulative oil and water production were 20,000 bbl and 12,000 bbl, respectively,” over 8 months, the paper said. In that case, the well was soaked with the chemical mix for 5 weeks.
The paper indicated that BHP and UT are working toward further testing to allow more accurate simulations and to ensure the injections are executed effectively with the fluid mix and delivered evenly along the lateral.
The ultimate goal is to develop methods that periodically boost production at various stages of the life of the well.
For Further Reading
SPE 187192 Frac Hit Induced Production Losses: Evaluating Root Causes, Damage Location, Possible Prevention Methods and Success of Remedial Treatments by George E. King, Michael F. Rainbolt, Cory Swanson, Apache Corporation.
SPE 187483 Improving Oil Recovery in Unconventional Liquid Reservoirs by Soaking-Flowback Production Schedule with Surfactant Additives by Johannes Alvarez, Francisco Tovar, David Schechter, Texas A&M University.
SPE 187420 Improved Hydrocarbon Recovery using Mixtures of Energizing Chemicals in Unconventional Reservoirs by Kishore K. Mohanty, Songyang Tong, Chammi Miller, University of Texas at Austin et al.
SPE 187147 Aggressive Fracturing Treatments in Horizontal Wells: Benefits and Pitfalls by Ali Daneshy, Daneshy Consultants International.