Several themes were evident in this year’s Offshore Technology Conference (OTC). One theme was the fact that in the current industry downturn, operators are increasingly utilizing existing offshore infrastructure to extend the life of existing assets, as well as developing new marginal stranded fields rather than develop new large greenfields. An important enabling technology to achieve this goal is subsea processing.
This article reviews the latest development in subsea processing.
The Case for Subsea Processing
In order to produce a subsea well, the wellhead flowing pressure has to be higher than the hydrostatic pressure of the riser plus the pressure drop due to friction losses in both the flowline and the riser. While many reservoirs have high initial pressure and are capable of producing oil under their own pressure, the reservoir pressure will eventually decline to the point where wells stop flowing.
As the industry moves toward deeper water and longer tiebacks, in order to produce the full potential of a deepwater well, a means is needed to add energy to the well fluids at the seabed.
Therefore, the incentives for subsea processing include (Kondapi 2017):
Increased oil recovery by reducing the backpressure on the subsea wells
Reduced weight of the topside facilities
Transporting well fluids as a single phase reduces or eliminates some of the flow assurance problems associated with subsea production, such as slugging and high pressure drop.
Debottlenecking topside processing facilities
Allows longer tiebacks and makes the potential of developing marginal fields more economical
Enhances HSE aspects: fewer personnel offshore, reduced emissions, and relatively easier decommissioning
Subsea processing still has many challenges:
Subsea equipment must be able to operate for several years without maintenance
High capex
High intervention costs
Technology gaps, such as long-distance transmission of high power subsea.
Subsea Processing Options
There are several options and technologies available for subsea processing. Selecting the right concept for a particular field depends on many factors related to the reservoir and fluid characteristics, location and water depth, and existing offshore infrastructure.
Some of the technology options for subsea processing include the following:
Subsea separation with reinjection of produced water
Multiphase boosting
Single-phase boosting without separation
The merits of each option are briefly discussed.
Subsea Separation with Reinjection of Produced Water
The system configuration for a subsea separator with reinjection of produced water is shown in Fig. 1. Separating out the water and reinjecting it subsea has several benefits including:
- Reducing pipeline and riser pressure drop, as well as the gravitational pressure drop in the riser
- Debottlenecking topside production capacity
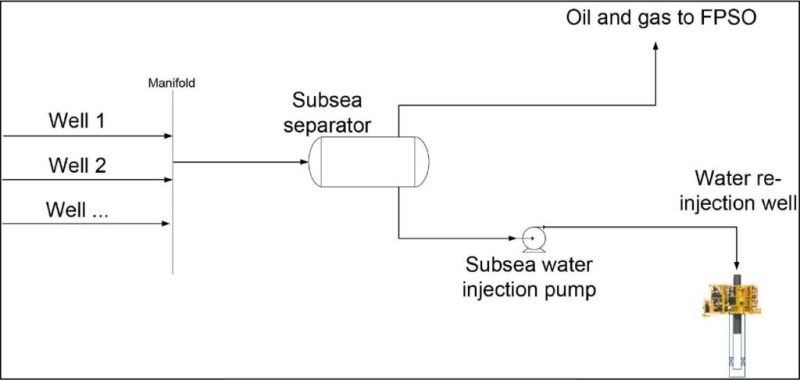
The gas flows through the gas riser to the host topside, where it can be used as fuel for gas turbines and power generation. Oil is pumped using a single-phase pump to the oil riser. The benefits of routing gas and oil through separate risers, combined with a single-phase pump at the seafloor, result in reducing the backpressure on the wells and reducing the risks of hydrate formation and slugging (Gyllenhammar 2017).
One of the challenges in bulk water separation at the seabed and reinjecting it back into the oil formation is treating the produced water to meet injection specifications requirements. Chevron Energy Technology Company and Sulzer performed qualification testing of Sulzer mixed-flow hydrocyclones at multiple pressures and for use in the presence of monoethylene glycol (MEG) (Riesenberg 2017). MEG is a gas hydrate inhibitor which will likely be injected in long subsea tiebacks. The system tested was a two-stage unit consisting of a bulk hydrocyclone and a polishing hydrocyclone.
From the results of the qualification test, it was concluded that although the target oil-in-water specification of less than 100 ppm was not always achievable, separation efficiency remained high under operating conditions
Multiphase Boosting
Multiphase pumping has been used successfully for subsea applications for more than 2 decades. The multiphase pumps (MPPs) installed on the seafloor are either twin-screw pumps or helico-axial type pumps. In a helico-axial MPP pump, kinetic energy is added from the pump rotor to the multiphase flow. The kinetic energy of the flow is then transferred in a diffuser into pressure energy.
Aker Solutions and its joint industry project (JIP) partners developed new multiphase pumping technology, which soon will be ready for the market (Hofstad 2017). The new pump uses a mixed-flow impeller where the flow channel is partly axial and partly radial, referred to as “helico-mixed-flow design” (Fig. 2). The concept of partially radial flow is adopted to use the centrifugal force to generate more pressure from each pump impeller.
Aker already tested a pilot pump. The next step is to design, build, and test a full-size prototype pump. It will be an eight--stage pump designed to generate 100 bar differential pressure at 70% gas volume fraction at a speed of 6,000 rev/min.
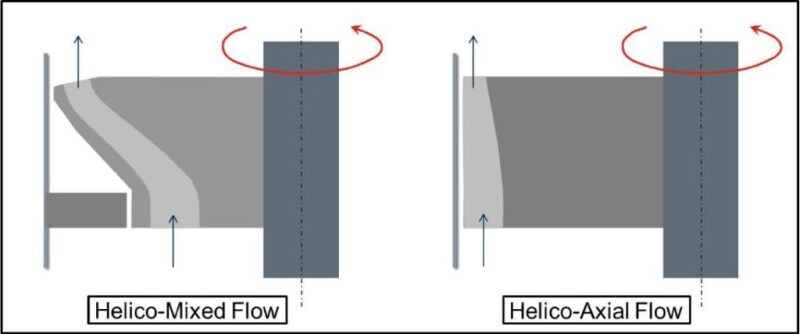
Single-Phase Boosting Without Separation
Subsea liquid pumps can be used to boost the produced fluids to the surface without the need for separation at the seabed. This application is suited for reservoirs that have low gas/oil ration or when the well flowing pressure is above the bubblepoint. Examples of this are the Jack and St. Malo fields in the Gulf of Mexico (Hjelmeland 2017). The fields are located 25 miles apart in the Gulf of Mexico in a water depth of around 7,000 ft.
The subsea boosting pump was designed to pump 20,000 to 60,000 B/D at a minimum inlet pressure of 1,200 psi and a maximum differential pressure of 4,000 psi. The single-phase pump had an exceptionally high shut-off pressure of 13,000 psi. The pump is driven by a 3-MW motor.
An extensive 2-year technology qualification program was implemented to qualify all the components of the subsea boosting system for what is considered the world’s first high-pressure seabed boosting system (Hjelmeland).
The subsea pumps were installed and started continuous operation last year.
Subsea Electric Systems
Having reliable and cost-effective subsea electrical power supply systems is a key factor in the successful implementation of subsea processing applications. As the industry is developing fields in deeper water and using longer tiebacks, conventional power distribution technology and hydraulic control capabilities are reaching their limits.
When transmitting the same power, increasing the voltage will decrease the electric current, which in turn reduces the size of the copper conductors and decreases heat losses. Having smaller conductors means less weight and potentially a smaller installation vessel.
Current industry practice is that subsea electrical loads are typically greater than 1 MW, and existing subsea motors are supplied at voltages ranging from 4.16- to 6.6 kV-motor (Margarida 2017). Operators and suppliers are collaborating in a JIP to develop a high-voltage motor. The program scope comprises the design, components qualification, and prototype build of a permanent magnet subsea motor to operate at 13.6 kV. One of the reasons for choosing this voltage level for subsea motors is that it was considered a low-risk technology because 13.8-kV motors are widely used in topsides offshore.
Leveraging Existing Offshore Infrastructures
Barclays recently published its 2017 E&P Spending Survey which shows that offshore spending is down another 20–25% this year as international oil companies continue to withhold spending (Anderson 2017). Barclays believes the era of megaprojects is over, as operators are now considering more phased-in developments to capture first oil earlier and minimize project risk.
There is a movement toward smaller projects. In response to the prevailing oil price environment, the focus for many companies is on maximizing the value of their existing offshore assets.
Wood Mackenzie also expects a move to subsea tiebacks to be one of many drivers toward a smaller, more efficient profile for the market going forward (Dunnahoe 2017). Operators have the opportunity to develop nearby satellite discoveries into their own infrastructure via tieback at low cost.
Subsea tiebacks and expansion projects can capitalize on the use of existing offshore infrastructure with spare production capacity. By using existing infrastructure, operators can maximize the investment that they have already made
Case studies are presented to demonstrate that brownfield investments in known petroleum basins offer excellent investment opportunities in the current oil price environment (Davalath 2017). BP’s Thunder Horse South Expansion project illustrates this trend of leveraging existing infrastructure to maintain production (Paganie 2017; Musarra 2017).
For Further Reading
OTC 27583. 2017. Two-Stage De-Oiling Testing for Qualification with MEG Presence by J. Riesenberg, Chevron Energy Technology Company, et al.
OTC 27639. 2017. Significant Cost Reduction of Subsea Boosting Systems by Innovative Technologies by J. Davalath, Technip, et al.
OTC 27661. 2017. How Will Subsea Processing and Pumping Technologies Enable Future Deepwater Field Developments? by P. Kondapi, Texas A&M University, et al.
OTC 27747. 2017. Profit Increase With New Subsea Boosting Products by A. Hofstad and H.C. Nilsen, Aker Solutions.
OTC 27800. 2017. Qualification and Development of the World’s First High Pressure Subsea Boosting System for the Jack and St. Malo Field Development by M. Hjelmeland, OneSubsea, et al.
OTC 27873. 2017. Combining FPSO and Subsea Processing for Optimized Field Development by E. Gyllenhammar, Aker Solutions, et al.
OTC 27929. 2017. High Voltage Subsea Pump – A Low Cost Subsea Boosting Enabler by A. Margarida, Petrobras, et al.
Anderson, J.D and Pickup, M. 2017. Evolving Business Models, Concepts Will Drive Offshore Recovery, Offshore 77 (5): 30–35.
Dunnahoe, T. 2017. Deepwater Exploration Seeks Value Over Volume in New Oil Price Environment, Oil & Gas Journal 115 (5): 38–41.
Paganie, D. 2017. Thunder Horse South Expansion Illustrates Industry Trend, Offshore 77 (4): 7.
Musarra, S.P. 2017. Suppliers, Standardization Help BP Realize Success With Thunder