The BC-10 asset, located in deep water offshore Brazil, produces heavy oil in the range of 16 to 24 °API. Mudline caisson separators with electrical submersible pumps (ESPs) are used to process fluids from multiple wells and boost them to the receiving floating production, storage, and offloading (FPSO) vessel. There are significant flow-assurance challenges in operating the asset. In this paper, two examples of production optimization for this field will be provided (further examples are available in the complete paper).
BC-10
BC-10’s production comes from four fields located in water depths ranging from 1650 to 1920 m and is dependent on artificial lift. This summary focuses on optimizations involving the Ostra field.
×
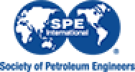
Continue Reading with SPE Membership
SPE Members: Please sign in at the top of the page for access to this member-exclusive content. If you are not a member and you find JPT content valuable, we encourage you to become a part of the SPE member community to gain full access.