Rotary steerable systems (RSS) and steerable motors pose unique challenges when modeling bottomhole-assembly (BHA) directional behavior. The complete paper presents a methodology that aims to allow the anticipation of problems such as mechanically stuck pipe or lockup situations when running in hole (RIH) casing or completion strings. Correctly evaluating the risk of BHA, casing, or completion strings being stuck or locked up when RIH can ultimately provide a template for ultimate reduction of nonproductive time.
Local Doglegs and Downhole Equipment
A pure rotary BHA has no ability to change its directional behavior during the run. Its directional capabilities are defined by stabilizer position and outer diameter, and, although no ability exists to control directional behavior directly, this type of BHA may be sensitive to weight on bit (WOB), mud weight, formation changes [unconfined compressive strength (UCS)], and inclination.
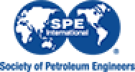