For drillers, The Geysers is a unique sort of hell.
It is one of the only places on Earth where a shallow well can reach a highly fractured reservoir so hot that it only produces steam.
That steam powers 18 power plants generating 835 MW of electricity, making this 45-square-mile area the world’s most prolific geothermal power producer.
High drilling costs there also stand out. Drilling a well requires 60 days or so and generates a lot of damaged drill bits and drillpipe.
The drilling rigs have the size and power of modern onshore rigs, but a close look reveals there’s no topdrive. Below the rig floor there is a rotary table, known as a Kelly drive because it can spin drilling pipe without being in the line of fire of the steam flowing out when running slotted casing into the steam-production zone.
When they get to that zone, they switch from drilling fluid and mud to injecting a high-pressure stream of air because of the enormous fluid losses anticipated when they reach that highly fractured level.
A drill bit that lasts 500 ft in this harsh, highly fractured rock has had a long run.
And the rugged terrain—mountains to a Texan but hills to a Californian—makes this a hard place to move a rig.
“The Geysers is its own animal, for sure,” said Sam Noynaert, a Texas A&M professor who was a key member of a team of drilling experts and scientists that drilled a well in The Geysers to test if faster drilling methods from the oil business could work there.
The two upper sections went pretty well, considering. As they went deeper, they repeatedly had to deal with severe fluid losses. Still, they had shaved nearly 6 days off the average drilling time.
But when they reached the highly fractured steam-producing payzone and their drilling method changed to air drilling, things got worse with drill bits failing after runs as short as 21 ft.
As a Geysers drilling paper presented at the Stanford Geothermal Workshop earlier this year delicately put it: “The air section proved to be more challenging.”
The Blob
The Geysers has a long history. The heat source is “a large blob of silica-rich magma (which) forced its way through Earth’s crust beneath the Coast Range,” according to the description of an image from NASA.
That flow about 1.3 million years ago from deep within the earth heated the overburden, making the rock brittle and prone to fracturing. Over time, water seeped into those hot fissures, creating hot springs that were awed by Native Americans and later attracted tourists to a nearby resort hotel.
By the 1960s drillers were tapping the steam in those payzones for commercial power generation, which peaked at 2,000 MW in 1987. It declined from there as steam production depleted the reservoir. Eventually, the output was stabilized at its current level by injecting water from sewage-treatment plants into the production zone.
The goal of the two-well test funded by the US Department of Energy (DOE) was to reduce the high cost of drilling wells for production and water injection at The Geysers, as well as less-challenging conventional geothermal resources.
Before The Geysers’ test, the method developed by Fred Dupriest, a retired Texas A&M professor who worked at ExxonMobil, has been used to slash the time needed to drill wells in hot granite reservoirs for geothermal innovators where they are creating fractured systems to heat injected water.
Those gains have been extended by a geothermal pioneer Fervo Energy which is drilling an array of wells at the DOE-funded Frontier Observatory for Research in Geothermal Energy (FORGE) geothermal research site in southern Utah to power a 400-MW power plant.
Bill Rickard, president of the Geothermal Resource Group that drilled the wells for testing at FORGE, said drilling in what is known as hot, dry rock, is far different from The Geysers, where he began his geothermal drilling career many years ago.
His explanation of how drilling fluid cannot be used in the steam-production zone is an example of how the factors that make for a great well can also lead to great trouble.
Air drilling is required because if you pumped drilling fluids, “there would have been huge losses. Every one of those fractures was filled with steam, and those are production intervals so you cannot plug them to stop it without plugging off production.”
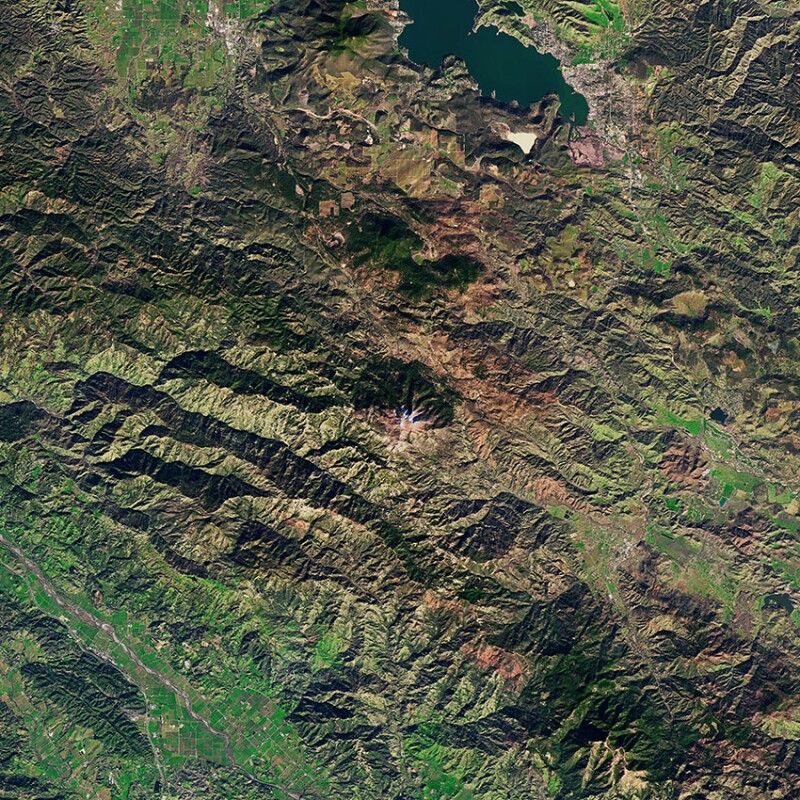
Plugging Away
The Geysers’ test began as usual with a training program by the Texas A&M team for all those involved.
Noynaert, who has long worked with Dupriest on faster drilling, taught those drilling the well how to identify drilling performance limiters and find ways to overcome them.
Over the first two sections, the on-bottom time required to drill the 14.5-in. and 11.5-in. sections was 150 hours faster than the average for similar wells, and 100 hours faster than the fastest.
The phrase “on-bottom” drilling is significant because as they went deeper, they had to frequently pull off-bottom to deal with major fluid losses. They initially tried to set cement plugs with “mixed results in preventing lost circulation,” the Geysers paper said.
“We were unable to execute a single continuous 500-ft run with a bit due to the multiple trips for the cement plugs for lost circulation,” the paper’s authors wrote.
“In the end, the team decided to drill through the losses and was able to reach the end of the interval using a mix of roller-cone (insert) bits and PDC (polycrystalline diamond compact) bits,” the Geysers paper said.
Dealing with lost circulation is on the list of problems to address in the next test. They will be reviewing the decision-making process when faced with either plugging or drilling forward. And they are seeking improved plugging materials, according to the paper.
Fractures were a significant problem in the middle zone that loomed larger in the production zone where conditions got considerably more difficult.
Drilling on Air
When the well depth exceeded 3,200 ft, they reached the steam-production zone where they had to begin clearing out the drilling cuttings with compressed air rather than fluid and mud.
Using three compressors to inject air into the hole successfully cleared out the cuttings, but unlike fluid and mud, it was unable to reduce the friction of drilling or the heat of the formation, shortening the life of the drill bits and pipe.
Rickard said that the high-pressure flow of sharp-edged cuttings was “sand-blasting the drillpipe.”
With no fluid to power a mud motor, they rotated the drillpipe using the Kelly drive.
To test whether they could improve performance using solid-body PDC bits, they alternated them with roller-cone bits, which are the standard for geothermal.
The roller cones lasted longer. But the average runs—299 ft for roller cones, which were pulled after a time limit was reached, vs. 201 ft for PDC bits which just wore out.
Noynaert said they should be able to significantly improve PDC performance because “the average rate of penetration for the roller cones was below what the team knew was possible with PDC bits.”
Rickard has used both and has managed to drill faster with PDC bits. In his experience, “once a PDC bit starts to fail in hard rock, they fail completely in a relatively short interval.”
On the other hand, the wear can cause the cones in an insert bit to fall out and sometimes get stuck in the hole. “One of the great advantages of PDC bits is that there are no cones to lose in the hole,” he said.
A look at a table covering the performance of the 11 PDC bits shows the runs generally were shorter as they went deeper (Fig. 1). Those used at depths from 3,500 and 6,400 ft averaged 217 ft. Those used at depths from 7,700 to 8,900 ft averaged 117 ft.
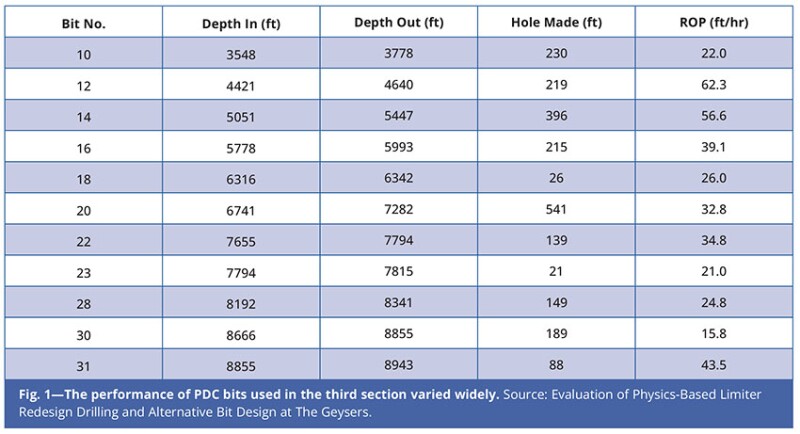
But in between those two groups was the sixth bit that had the longest run, 541 ft. The fact that the PDC used before it lasted just 26 ft and the one used after it went 139 ft suggests that the trend is more complex than simply going deeper and hotter leading to shorter bit life.
Certainly air-drilling is damaging. “Air-drilling is very abrasive on the entire drillstring, and typically bits are dulled after less than 24 hours of drilling. With round trips to change bits averaging about 20 hours, bit life becomes a significant value driver in addition to the rate of penetration,” the Geysers paper said.
But those factors don’t explain the sudden, extreme damage to PDC bits they pulled after runs as short as 21 ft.
“The PDC bit dulls, showing obvious shearing of cutters. That indicates the limiter is not a gradual wearing trend seen in some high-strength rocks but instead is effectively an instantaneous event,” according to the paper.
The damage resembled bits pulled from certain zones in the Delaware Basin.
“In the west Texas scenario that most people are familiar with you’re in a low-strength rock and you hit high-strength rocks,” Noynaert said. At that instant, the load on the cutters is magnified on the harder rock, leading to a sudden failure due to “interfacial severity.”
This effect was magnified in The Geysers by the extreme “strength transition” from hard rock to air in the fractures, he said.
“With interfacial severity it happens nearly instantaneously, just a few revolutions, so it’s a real challenge to identify in real time,” Noynaert said.
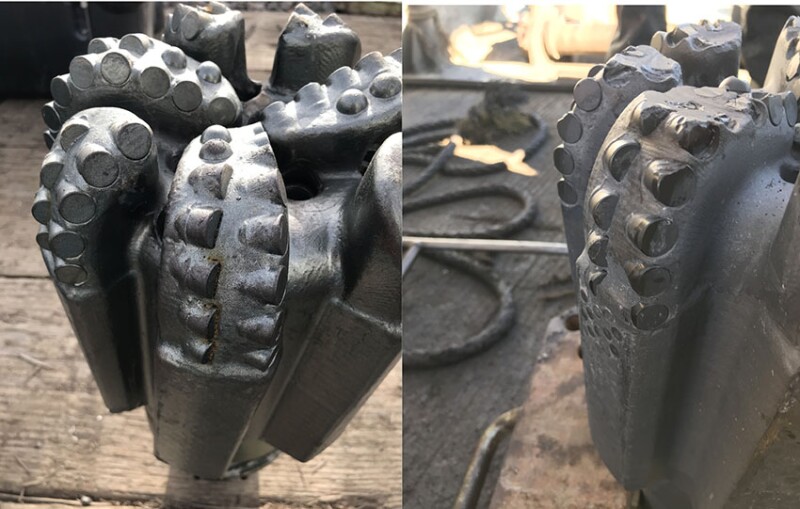
Go Slower?
During the test they modeled drilling data to create programs to warn the driller of drilling dysfunctions that can be detected and mitigated before serious damage has been done. But with interfacial severity, that is not an option.
This forced the drilling team to focus on risk reduction while drilling. That required backing away from their prime tools for going faster, and at the same time increased the risk of bit damage due to other problems, such as bit sticking and slipping.
When faced with repeated cases of sudden drill-bit death, rather than setting the weight on bit (WOB) at the structural limit set by the manufacturer and using bits with aggressive cutters to maximize the rock removed per rotation, they lowered the settings to the “survival level.”
The thinking behind this is: “When you come into the strength transition, you’re not as deeply embedded,” Noynaert said.
At The Geysers, “in the payzone we’re running, relatively speaking, a very low weight,” Noynaert said, adding, “We’re not close to the structural limit of the bits.”
This is in line with the thinking of Calpine Corp., which operates The Geysers. Its bits last from 20 to 30 hours and make up to around 500 ft on a good day. The goal is to minimize early failures of their sealed roller-cone bits, particularly incidents where hardware becomes stuck in the hole, Noynaert said.
Based on The Geysers bit-life table (Fig. 1), the test results were well short of that standard. The paper said as they plan the next well “bit runs will be investigated in more detail to improve performance in the next project well.” It offered a likely explanation: “The variability in run length could be due to similar variability in fracture distribution within the reservoir.”
In the oil business, data about where extreme rock strength transitions are likely to be encountered has been used to create drilling roadmaps telling drillers where they need to proceed cautiously.
A 2018 ExxonMobil paper about managing interfacial severity in the Permian said drilling plans need to reflect that limit: “The maximum penetration per revolution that can be achieved in a given formation.”
In The Geysers, the perils in the production zone have not been mapped.
Based on Calpine’s experience, certain rock types are more prone to having fractures. However, within these large areas, there is no information on where damaging fractures are likely to occur.
“You could drill 500 ft and not see any fractures. Or you can see a fracture every 5 ft. There’s no way to predict that,” Noynaert said.
Even at a low WOB, “you’re still shearing off a fair amount of cutters,” Noynaert said.
They will be asking bit makers for drill-bit designs that are better able to take these hits and keep going. Service companies are likely to have some suggestions since they have been working with oil companies on dealing with the problem.
However, there is an economic limit to the challenges service companies are willing to take on because The Geysers is just a slice of the tiny geothermal submarket. Selling a geothermal idea that requires a significant engineering budget will require also solving a problem for a broader market.
As The Geysers’ drilling team neared 9,000 ft, they had one last drilling idea to test—a percussive hammer. Drilling by repeated smashing has been around since the earliest days of oil drilling, but it not used often in the oil business today because rotary drilling is faster.
It was tried at the bottom of the air-drilled section. It was chosen because it can operate effectively without drilling fluid, and is effective on the sort of hard, brittle rock found there. Three compressors were used to power the off‑the-shelf unit that was modified to handle the extreme heat.
It was used to drill the last 40 ft of the borehole. Its speed peaked at 20 ft/hr. Over the last 10 ft of that run, the WOB was reduced to limit oscillations. After an inspection, the Geysers paper reported that “there were no visible signs of damage.”
For oil drillers, that’s proceeding at a snail’s pace. But, if it could keep that rate up for 2 or 3 days, the time saved replacing bits might justify the patience required.
Noynaert said the percussive hammer is likely to get another look. But he noted its slow pace required long run times downhole, increasing the risk of failure for any device with moving parts.
And it was clear he really wants to find a way to do it better than using a slow-but-sure approach.
For Further Reading
Evaluation of Physics-Based Limiter Redesign Drilling and Alternative Bit Design at The Geysers by Peter So, Justin Wriedt, and Stephen DeOreo, Geysers Power Co.; Mitch Stark, Stark Industries; John McLennan, Milind Deo University of Utah; Samuel F. Noynaert, Texas A&M University, et al.
Simulating Lost Circulation Treatment at Geothermal Conditions and Comparing the Efficacy of Different Materials Utilizedby William Kibikas, Matthew Ingraham, and Stephen J. Bauer, Sandia National Laboratories; Seiji Nakagawa, Chun Chang, Patrick Dobson, and Timothy Kneafsey, Lawrence Berkeley National Laboratory; and Abraham Samuel, Geo Energize.
SPE 199599 Maximizing Drilling Performance Through the Delaware Basin Brushy Canyon and Interbedded Formations by Fred E. Dupriest, Samuel Noynaert, and Tyrell Cunningham, Texas A&M University; and Marcus Rendon, Noble Energy.
SPE189608 Drilling Interbedded and Hard Formations with PDC Bits Considering Structural Integrity Limits by Paul Pastusek, ExxonMobil Development Co; Derek Sanderson, XTO; Andrius Minkevicius, Zachary Blakeman, and Jeff Bailey, ExxonMobil Development Co.