The development of compact topside processing plants for floating, production, storage and offloading (FPSO) vessels is a growing industry trend that can reduce operating and capital expenditures over the life of the vessel, a researcher and scientist said recently.
Related Article Challenges in the Design of Separators |
Rene Mikkelsen, technology manager for Brazil of separation systems at FMC Technologies, said the company has designed a compact inline separator weighing about 440 metric tons, which is about 40% lighter than a traditional separation vessel. The smaller, lighter vessels could reduce both operating and capital expenditures on FPSOs. The findings were part of a technical paper, titled “Development of a Compact Topside Processing Plant,” that he presented at the 2013 SPE Annual Technical Conference and Exhibition in New Orleans.
The industry has gradually introduced compact separation technologies over the past decade in response to the need for debottlenecking facilities in mature fields. In many cases, a compact unit was needed for a congested processing plant. A smaller separator negated the need for major reconstruction at existing facilities, Mikkelsen said.
So far, more than 50 of FMC’s inline units have been deployed over the past 10 years. Although the industry has acknowledged the advantages of compact separation technologies, the lack of data regarding their performance, flexibility, and reliability has so far slowed their use in newer fields, he said.
FMC studied the existing inline separators and found that the compact technologies built at existing facilities have proven reliable. “We went to the oil operators and asked them what was their experience with these facilities,” he said. The study found that the installed inline separators have operated for a cumulative total of 65 years with no major incidents. “So far, we haven’t had any failures in these technologies,” Mikkelsen said.
Given the reliability of the compact technology, a major operator asked FMC to design a unit that could be used on FPSOs. The space and weight savings can make them more economical to operate in offshore developments, which will account for a growing number of the world’s production in the coming decades. The goal was to develop a smaller and lighter process facility that can be used on future FPSOs. The operator required a separator with higher efficiency and availability, and the ability to handle feed with a high carbon dioxide content. Reductions in capital and operating expenditures were also desired.
FMC has collaborated with a major oil operator to develop a compact, reliable, efficient topside gas/oil water processing plant. The designers combined inline, ultra compact separation technologies with optimized vessel designs to achieve a flexible and reliable processing plant for future FPSO vessels, Mikkelsen said. “It is a brand-new concept and design,” he said.
The design envisions a hybrid solution, which includes the benefits of a compact design and the operational flexibility of a traditional separator, Mikkelsen said. The unit is capable of handling crude and natural gas streams, and produces four streams: natural gas, crude oil, water and sand. Table 1 shows the process conditions for which the compact facility has been designed.
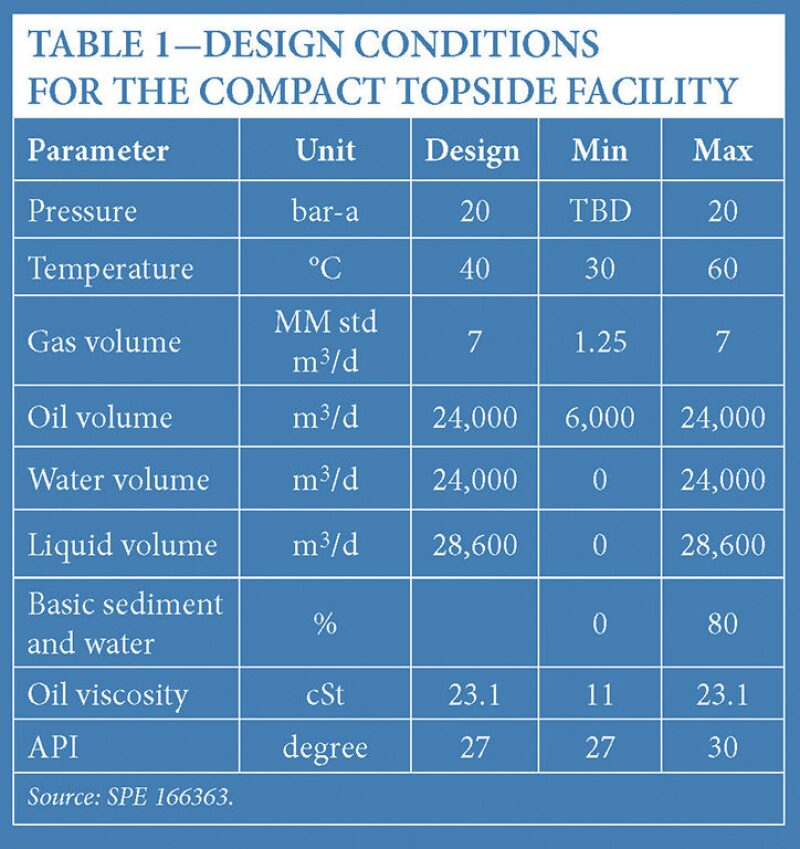
The facility consists of three separation and treatment modules for gas, oil, and water. The oil treatment scheme must produce oil that meets export requirements. The water treatment module must produce water of suitable quality for discharge, and the gas treatment scheme must meet sales specifications or the requirements for reinjection.
The compact separator has one principal separator, the freewater knockout unit (Fig. 1). From there, an emulsion of oil and water goes into two stages of treatment. The system uses an inline deliquidiser to remove the liquid from a predominantly gas stream and a degasser to remove the gas from a predominantly liquid stream. Both technologies induce a spin on the incoming stream, which forms a gas core surrounded by a liquid film in the separation section downstream.
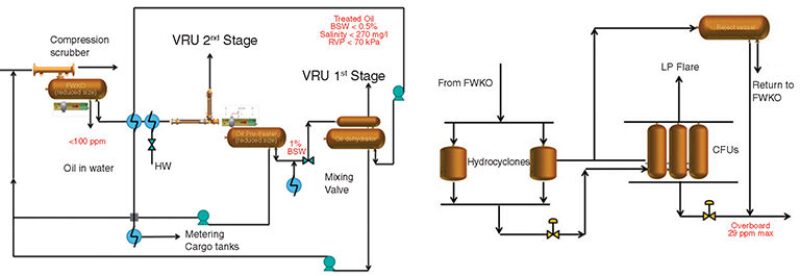
A compact flotation unit gives the water its final stage of polishing, making it clean enough to discharge overboard. The unit injects gas from the gas plant to form bubbles, which pull particles out of the water. Mikkelsen said that in practice, any gas stream could be used for the same purpose.
FMC concluded the conceptual phase in April and it is now qualifying the system with the operator. An extensive round of testing is currently under way. The operator wants to have the units ready by 2017, which is a relatively short timescale for a new technology, Mikkelsen said.
For Further Reading
SPE 166363 Development of a Compact Topside Processing Plant by Rene Mikkelsen, FMC Technologies, et al.