Piloting an inspection drone around oil and gas assets presents certain challenges, but using one to make direct contact during nondestructive testing (NDT) requires technology that hasn’t existed.
Operators like the idea of using unmanned aerial vehicles, or drones, to inspect oil and gas assets because doing so means humans aren’t conducting dangerous inspections at heights or in confined spaces. It also has the added benefit of removing the time and costs associated with scaffolding.
While the state of the art in drone inspections has improved significantly over the years, difficulties remain around establishing stable contact between the drone and the target inspection surface as well as precise positioning. This leaves high-definition cameras as one of the major tools in drone-based inspections. Many existing solutions don’t combine the dexterity, sensor options, and control systems needed for NDT inspections by drones.
Speaking during February’s International Petroleum Technology Conference in Dubai, Tommaso Borzone, a robotics engineer at EniProgetti, said Eni’s engineering arm worked with Eni and the University of Naples to conquer the twin challenges of using an inspection drone to conduct NDT through direct contact with the asset and immersive stereoscopic vision using a monocular camera.
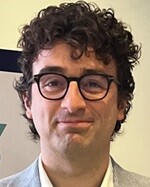
The NDT is performed with a robotic arm that has 5° of freedom and uses an ultrasonic probe to measure thickness of metal surfaces while a 3D first-person view (FPV) camera system provides the drone operator with stereoscopic vision with an automatic vergence-compensated zoom for enhanced depth perception during remote inspections, Borzone and his co-authors wrote in paper IPTC 24802.
The prototype system, based on a commercially available drone, has been tested in both indoor and outdoor applications.
Aerial Robotics
The drone has an omnidirectional propulsion system, a lightweight robotic arm, and sensors. The reduced weight of the robotic arm ensures the drone can maneuver during inspections without becoming overburdened, according to the paper.
The 1.5-kg robotic arm has a high level of dexterity, the authors said, and it can accommodate 1 kg of payload, which is sufficient for NDT tasks. The arm has a 6-axis force and torque sensor. The arm’s end effector features a commercially available ultrasonic test (UT) sensor that can acquire and process surface measurement data using a piezoelectric probe (Fig. 1). A flange on the tip of the end effector interfaces with the surface. A coupling gel on the probe guarantees high-quality measurements, Borzone said.

The arm control is “where the novelty comes in,” Borzone said. For effective NDT testing, the probe must exert a “specific amount of force against the surface” and flying objects are “intrinsically not stable,” he added.
The drone system provides real-time force feedback control as well as impedance control for safe contact, he said.
One of the challenges in using a drone to touch the surface of an asset has been the resulting change in the drone’s center of mass as the robotic arm moves, Borzone said. The system uses dynamic balancing to adjust the position of the batteries to maintain stability, the authors wrote.
Operator Interfaces
The drone operators—one to pilot and one to take measurements—use virtual reality (VR) headsets and receive real-time measurements and positioning data. The operator wearing the VR headset can move the gimbal with a simple head movement.
The camera is encased in a 3D printed housing (Fig. 2). The camera has adjustable horizontal alignment to maintain balance and improve stabilization. The gimbal’s aluminum body is internally wired for power and communication, enabling communication during continuous pan-axis rotation, according to the paper. The wireless communications link can stream full high-definition video with less than 1 ms of latency. Control data received from the operators running the ground equipment include movement data from the VR helmet and joystick commands for zooming the camera lens and gimbal orientation, the authors wrote.
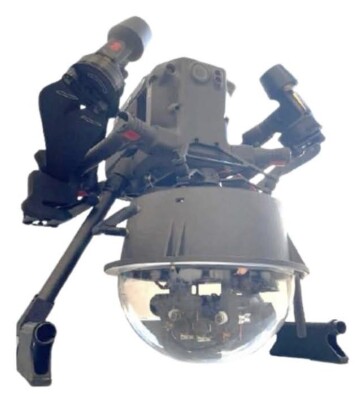
One of the novel things about the system, Borzone said, is that it uses a field-programmable gate array (FPGA) board to process the stereoscopic camera signals and synchronize them for automatic vergence compensation before transmitting the video feedback to the operators on the ground. According to the paper, the vergence correction adjusts the camera alignments dynamically, ensuring a clear and consistent 3D view as the zoom level changes and allowing for comfortable viewing of the video stream.
At the outset of an inspection, the operator can choose a point of interest for NDT using the video stream received at the ground station and guide the end effector of the drone in a Cartesian space using a joystick, according to the paper. The 3D points in that area make it possible for the drone to position itself close enough to permit manipulator operations, the paper said. An automated docking routine handles the drone’s position during the inspection. The UT sensor on the end effector of the robotic arm measures the thickness of the material at the point of contact, the authors wrote. But, for that to happen, there must be a vacuum between the end effector and the surface, so an electric pump applies a viscous gel to the tip to ensure proper adhesion and reliable measurements, they wrote.
Testing the Prototype
Borzone said the NDT platform was first tested in an indoor environment where there was no global positioning system (GPS) available for the drone to use (Fig. 3). That inspection allowed the team to see the robotic arm in action, he said.
The drone inspected a mock-up of an industrial asset guided by simultaneous localization and mapping algorithms to enable precise localization and mapping, the authors wrote.
The indoor test confirmed the system’s reliability and robustness, Borzone said.
“During the tests, the manipulator moved smoothly toward the surface, guided by an impedance controller to ensure stable contact. The system consistently applied the desired interaction force of 3.5 N, enabling the UT sensor to provide precise surface measurements. Two consecutive trials yielded highly consistent thickness readings of approximately 0.019 m, validating the system’s precision and reliability,” the authors wrote.
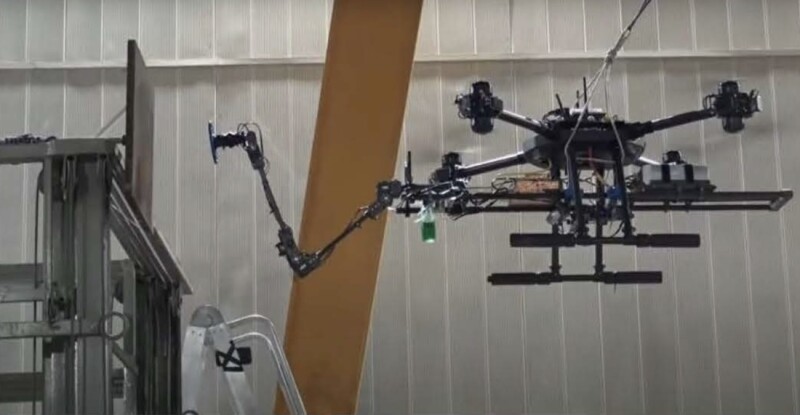
After success in the indoor environment, the team tested it on a storage tank outside. During this test, Borzone said, the drone was cabled for safety.
“You don’t want to break your prototype during testing activities,” he said.
The authors said the drone was able to take multiple measurements during the outdoor mission.
There are some challenges, however, particularly for use outside, they noted. One area the team expects to address in the future involves mapping and localization algorithms. The team also plans to explore the use of alternative sensors for more robust outdoor performance.
Borzone also noted that the current system is semiautonomous, with humans managing much of the inspection mission from afar.
“We want fully autonomous operations,” he said.
For Further Reading
IPTC 24802 Drone-Based Solutions for Asset Integrity: Development of NDT Drone and 3D FPV Payload for Asset Remote Testing and Inspection by R. Campaci, EniProgetti; S. D'Angelo, PrismaLab and Università Federico II di Napoli; T. Borzone, L. Madia, and M. Favaretto, EniProgetti; V. Lippiello, PrismaLab and Università Federico II di Napoli/Neabotics; and A. Vignali, Eni