Most industry professionals know that remote operations were becoming increasingly common well before COVID-19 impacted the oil and gas drilling industry. But then during the pandemic, everyone all at once drove to reduce personnel travel and visits to the rig site.
One solution for this was remote operations. A major service company recently reported that more than 80% of its jobs worldwide have a remote component, and up to 100% on a region‑by‑region basis.
Now, evolving remote operations is a firmly established trend.
It is a trend that has gone hand in hand with automation—from automation of data gathering to automation of action sequences. As the industry became comfortable with remote, in all senses of the word (real-time operating centers [RTOCs] and virtual centers), ideas started to form for future development.
A synopsis follows of findings from an industry survey of remote operations in drilling which suggests various stages of implementation.
Where Are We Going?
Established already are de-manning models such as directional drilling which encompasses measurement-while-drilling (MWD) data, mud-logging analysts, geosteering, drilling optimization, and survey quality control. This is expected to be followed by:
Stage I: Logging-while-drilling (LWD), wireline logging, cementing, and pressure pumping.
Stage II: Establishing operating protocols between RTOC and wellsite while adding mud and fluids management, which will require significantly improved mud data (real-time and at a high frequency) along with managed pressure drilling and casing running with rig crews operating with automation.
Stage III: Elevating remote decision making, enabling drilling engineers and other operating company staff to perform roles remotely.
Stage IV: A fully digitized operating system with a high degree of automation enabling remote geo‑driller (drilling the borehole).
How Will We Get There?
The new software as a service (SaaS) models in the industry are remotely enabling drilling engineers to understand more than the driller sees on their drilling control screens. This enables the industry to reimagine how operations are controlled and executed. The drilling contractors and original equipment manufacturers will need to upgrade their human‑machine interface (HMI) to advise drillers in near-real-time and with operational context.
Some decisions will be relinquished to the SaaS service user in the remote environment. The current trend is leading to critical operations being managed remotely, subject to communications capabilities and routine operations which are happening on-site requiring a view of or under the drill floor.
If operations are to be primarily run from site, it will require an operations room approach where all the drilling and well data are shared with on-site experts in one location (but probably not on the drill floor).
Drilling systems automation (DSA) has steadily progressed, especially in North America land and offshore in the Gulf of Mexico. The same is true for the North Sea. Systems include automated trajectory drilling, drilling optimization, the full cycle of drilling a stand, and wellbore protection applications.
A “fully automated” land rig is operating in the US as a comprehensive test bed for both the drilling contractor who constructed it and the operator using it. It appears to be achieving its goals of proving automation; however, further adoption is being predicted to occur on current Tier-1 rigs.
This observation infers that a purpose-built solution in the current rig market cannot compete with adopting automation (including a rig operating system) on the top-tier rigs that already exist.
Drilling is only one aspect of the well construction process; remote operations with automation will push the envelope to include other parts of well construction such as completions, wellbore intervention, and plug‑and‑abandon operations.
Expanding remote capabilities with automation into these domains will be addressed during a panel debate at the 2023 SPE Drilling Systems Automation Technical Section (DSATS) and IADC Advanced Rig Technology symposium to be held 6 March in Stavanger. The gathering will be held immediately preceding the SPE/IADC International Drilling Conference and Exhibition 2023.
Expanding the Value Proposition
The hurdle for both the advances in drilling systems and the expanded scope of automation is a clearly defined and delivered value proposition.
The value proposition to date seems to be:
- Safety (removal of personnel from the heavy machinery envelope).
- Efficiency (improvements through consistency of repetitive operations and best practices).
- Process safety (such as borehole envelope protection to reduce nonproductive time).
- Reduction of cognitive load on drillers (e.g., the routine operations such as tripping) and improved well control monitoring (e.g., influx detection).
Most recently, attention has started shifting toward wellbore quality as it impacts completion and production, which is a more holistic definition than simply a percentage of “in reservoir” and borehole tortuosity.
This potential is driven by increasing levels of interoperation between enterprise, wellsite service, and rig system solutions. Data are no longer simply fed back to the enterprise via WITSML but are blended across solutions at all levels of the operation.
This is changing the modus operandiof drilling.
Digitalization (converting business processes to use digital technologies) is expanding rapidly throughout well construction benefiting both remote centers/virtual centers and automation.
Individuals and companies are being driven into a more open world for data where sharing is becoming common and is likely to continue to expand. Sharing of data is driving organizations to shift from competing to complementing to collaborating around the data.
This transition will have a profound effect on business interactions which may cause the industry to finally accept relationships that were first conceived of back in the early 1990s.
As the automation of wellbore construction advances, it is paramount that industry professionals keep abreast of these developments through the various communications channels.
The Road Ahead
Digitalization and automation require data attributes that meet higher requirements for accuracy, latency, availability, semantics (meta data), etc. than are traditionally available from drilling rigs.
Traditional rig sensors are often very dated in their capabilities (1940s technology) and exhibit significant errors which have been measured in the order of ±20% for key data such as pit volumes, weight on bit (WOB), and drilling torque. Industry initiatives are underway to guide suppliers to maintain and calibrate these sensors such that they achieve their design capability (data verification).
As automation advances, sensors with improved attributes will need to be employed. This means that data users will need to specify the required data attributes and pay for the upgrade (data validation) or incorporate their own sensors.
SPE DSATS, along with the Wellbore Positioning Technical Section (WPTS) and the Drilling Uncertainty Prediction Technical Section (DUPTS), launched a subcommittee whose mission is to increase the awareness and understanding in the drilling community on how to describe drilling data quality and uncertainty.
This committee, led by Eric Cayeux, has also published a paper titled “Connecting Multilayer Semantic Networks to Data Lakes: The Representation of Data Uncertainty and Quality.”
The paper is free to download here from OnePetro and presents details focused on capturing the description of the quality and uncertainty of depth measurements. Use cases have exemplified how multiple stakeholders and disciplines manage, communicate, and understand the notion of wellbore depth and its relative uncertainty.
They describe how the tabulation of well survey data is typically to two decimal places when the uncertainty, at deeper depths, is in whole meters/feet and multiples thereof. This is simply inadvertent misinformation that impacts subsurface models and reservoir characterization.
In 2012, a group of DSATS members organized an SPE Technical Workshop to debate the big jump forward anticipated in DSA. We gathered 120 experts (30% non-oil and gas) in Vail, Colorado, for 5 days.
The culmination was a very forward-looking vision for DSA: “In 2025, well plans are uploaded into an interoperable drilling system that automatically delivers a quality wellbore into the best geological location, installs the casing and zonal isolation according to plan, installs the completion system according to the program, and updates remote operators and experts in real time to changes in the situation and identifies potential paths for success for the experts to input control.”
I am program manager for an industry initiative that created a DSA Roadmap aimed toward this vision. The product was developed, primarily in a virtual environment by 50 experts globally. The report is available for free download and more information can be found on the DSA website which features links to several papers and articles on the topic.
Join the Journey
It is worth emphasizing that like all SPE technical sections, DSATS is run by volunteers who are both engaged and passionate about the future of drilling.
The section’s mandate is to “accelerate the development and implementation of systems automation in the well drilling industry by supporting initiatives that communicate the technology, recommend best practices, standardize nomenclature and help define the value of drilling systems automation.”
If this sounds like an area where you may be able to contribute, consider looking at the DSATS schedule to take part in the next meeting. DSATS is open to all SPE members and holds bimonthly community meetings to issue updates and gather input from participants.
De Wardt is program manager for the industry Drilling Systems Automation Roadmap and the industry Drilling Systems Automation Body of Knowledge.
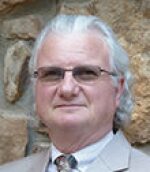
John de Wardt, SPE, is a recognized upstream global consultant delivering operations and business process improvement across the full supply chain of drilling, completing, producing, and abandoning oil and gas wells. De Wardt has 46 years of management and technical experience and has worked in 34 countries. He is a Chartered Engineer, a Fellow of the Institution of Mechanical Engineers, an SPE Distinguished Member, and Director Emeritus of the SPE Drilling Systems Automation Technical Section. Since 1994, he has focused on performance improvement (gap analysis/lean), strategic planning, and organizational redesign through facilitated bespoke programs. De Wardt previously held management and engineering positions with Halliburton, Forasol/Foramer drilling contractor, and Shell International. He is an industry thought leader who regularly presents on new and novel practices. He has authored 46 published papers and articles and led 21 industry forums, workshops, and symposiums as well as served as a committee member/session chair for the SPE/IADC International Drilling conference for 19 years. De Wardt was an SPE Distinguished Lecturer in 1995–1996 and 2020–2021.