The stage is set to begin making “green” hydrogen from the world’s abundant supply of seawater. But whether this niche-within-a-niche can stand on its own and become a competitive energy source remains uncertain.
Today, only about 1% of manmade hydrogen is considered to be green, and not a single atom of it is produced offshore.
In the offshore concept, the green label will be earned by splitting the hydrogen out of desalinated seawater with electrolyzers that run on renewable wind energy.
This represents an opportunity for oil and gas companies to not just lower their carbon footprints, but to leverage billions of dollars’ worth of existing offshore infrastructure.
Their platforms can host the electrolyzers. Their pipelines can transfer the product to shore. They may even be able to power their offshore facilities using the hydrogen produced at sea.
Offshore producers should also have no problem finding a market. PriceWaterhouseCoopers said in a report from last year that green-hydrogen exports could be worth $300 billion annually by 2050, supporting some 400,000 jobs globally.
However, the first set of offshore pilots are still in planning mode. It will take a few more years to assess the results once they start up. That means we may not know if offshore hydrogen is commercially viable until decade’s end.
Some of the biggest barriers that must be overcome were highlighted by a panel of leading hydrogen experts at the recent Offshore Technology Conference (OTC) in Houston.
Green Hydrogen in the Red
“The major hurdle is still the cost,” explained René Peters. “The cost of hydrogen production with electrolysis is still extremely high compared to gray- and blue-hydrogen production.”
Peters is the business director at the Dutch technology group TNO which is one of a dozen partners trying to launch PosHYdon, the pilot for offshore hydrogen production. Startup is expected by early 2023 on a normally unmanned oil and gas platform operated by independent oil and gas company Neptune Energy.
Peters’ comments on cost were not relegated to the offshore aspect since all green hydrogen is made onshore today. In terms of tipping point for profitability, these are the relevant benchmarks.
- Green hydrogen costs range from $6/kg to more than twice that, depending on the price of the renewable-energy input.
- Grey hydrogen, produced via steam methane reforming (SMR), is the carbon-intensive incumbent whose price of $1/kg to $2/kg must be matched.
- Blue hydrogen, which is SMR combined with carbon capture and storage, costs from $5/kg to $7/kg.
The PosHYdon project may be groundbreaking, but it offers no immediate pathway to competing with grey hydrogen on a cost basis. It is merely a steppingstone.
Located just 8 miles off the Dutch coast, Neptune’s platform was installed in 2013 to produce up to 15,000 B/D from the Amstel oil field.
The long-term ambition is to use offshore wind directly, but that would have cost too much for this pilot. However, the platform is fully electrified from shore which means it has an indirect connection to an offshore windfarm. Data from that farm will be used to simulate the variable supply that would be available to the electrolyzer in a real-world scenario.
That centerpiece—a 1-MW electrolyzer inside a shipping container—will sit on the topside where it will ingest desalinated seawater and pump out 400 kg/D of hydrogen. For perspective, 1 kg of hydrogen holds about the same energy in a fuel-cell vehicle as 1 gal of gasoline does in a conventional vehicle.
And with an estimated price tag of €10 million (about $11.7 million), Peters acknowledged that the pilot “is quite expensive,” especially given the relatively small size of its electrolyzer.
Running the bill up are things like power connections, a system to inject the hydrogen into a gas line, and all the design and safety studies for the untested approach.
PosHydon also reveals the need for government help, at least at this stage. Initially, first hydrogen production was hoped to be achieved by the end of this year. But that had to be pushed back since the project needed to find more Dutch partners to secure a €3.6 million subsidy from the Dutch government which was awarded in July.
This underscores that projects reliant on public financing may have extended timelines. To the point, PosHYdon may lose its distinction as “the world’s first green hydrogen plant.” This comes as a separate pilot was announced off the coast of France with a target startup in 2022. It now claims the “world’s first” title.
With all of this said, Peters pointed out that PosHYdon “is definitely not a commercial project, it’s a learning project,” meant to test the feasibility and gain offshore experience.
His hope is that the pilot clears the way for others that will achieve economies of scale. Among other things, that will require electrolysis plants of at least 100-MW input capacities, or even up to 1 GW. (More details on the PosHYdon pilot can be found in OTC 30698 and this JPT synopsis.)
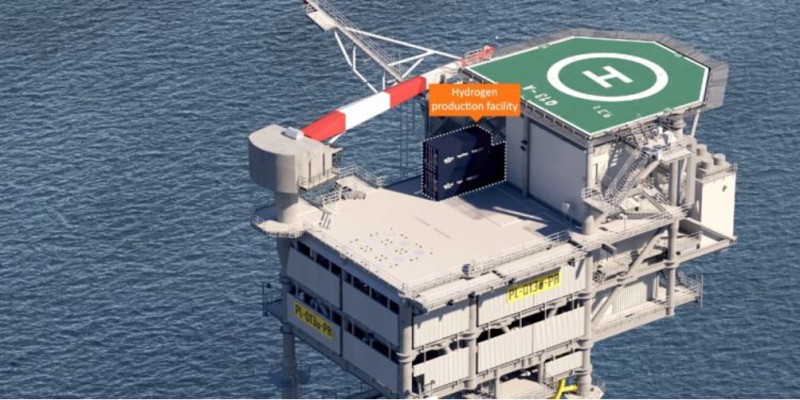
Bigger Means Cheaper
To drive costs way down, one of the things that the entire spectrum of green hydrogen, not just offshore, needs most are larger electrolyzers.
The rule of thumb used today holds that electrolyzers cost around $1,000/kW—or $1 million per MW. Some hydrogen supporters expect to see that price drop to around $300/kW in the next couple of years and then down to $100/kW by late decade.
Even at such a huge discount, Eric Miller, a senior advisor with the US Department of Energy (DOE), told attendees at OTC that it is only “a necessary but not sufficient condition for achieving $1/kg of hydrogen.”
The technology many are counting on to make green hydrogen competitive is called polymer electrolyte membrane (PEM) electrolysis. Though it is not the cheapest option, PEM electrolysis is the most amenable to running at variable loads. This is very important if you want to run them off intermittent power sources like sunlight or wind.
Most of today’s biggest commercial PEM units, called stacks, have input power limits of 5 MW and 10 MW. That’s not bad given that less than a decade ago, “big” was around 250 kW, said Miller.
Both then and now, to go bigger, hydrogen producers have simply taken a modular approach by grouping electrolyzers together.
“That’s fine for a while,” added Miller. “But, when you get into the 100-MW or a gigawatt scale, that’s a whole new technology.”
The near-term potential for PEM electrolyzers is to at least increase their output density. Miller said this would create “more compact, lower-footprint systems,” which “certainly have an advantage in offshore, remote constructions.”
Factory Mode Also Needed
In addition to more powerful and/or efficient electrolyzers, the way they are made is in need of an overhaul.
For David Edwards, the hydrogen energy champion at industrial gas supplier Air Liquide, this may be the most important point.
“The success of green-hydrogen production at scale requires us to have almost orders-of-magnitude reduction in capital costs of the electrolyzer system,” he said.
It sounds daunting. But Edwards was firm that it is entirely possible.
He said electrolyzer makers are already moving away from “boutique stack manufacturing in small shops” and toward roll-to-roll and assembly-line techniques.
While it is early days for this shift, he cited the advancement of solar-panel manufacturing as an example of where things may be headed. Since 2010, the cost of utility-scale solar installations has dropped by 82%, thanks in large part to manufacturing improvements.
Air Liquide has tied part of its future to all this coming true after it acquired a minority stake a couple of years ago in a company called Hydrogenics. The firm, majority-owned by engine manufacturing giant Cummins, claims to be the first-to-market with scaled-up electrolyzers.
In January, Hydrogenics and Air Liquide completed the installation of what they say is the largest electrolyzer plant on Earth. The 20-MW plant (made of four 5-MW units) is powered by 99% renewable energy and located onshore in Bécancour, Québec.
Automated production facilities are also on the agenda. The International Renewables Energy Agency said in a recent report that robotic automation represents “a step-change cost reduction” that enables production lines to churn out gigawatts of electrolyzers annually.
One example is Norwegian electrolyzer maker Nel, which is supplying the electrolyzer on the PosHYdon pilot. This year the company finished its first automated production line. The upgrade is part of Nel’s ambition to lower green hydrogen costs to $1.50/kg by 2025 and achieve a 2-GW annual capacity at its facility in Herøya, Norway.
Additionally, electrolyzer makers are looking to shed costs on the various component pieces through standardization. Some of the big-ticket items this will impact include water purification systems, transformers, compressors, gas processors, and cooling systems—all of which represent at least half the cost of most electrolyzers.
Marrying Up Wind Power and Pipelines
Another cost component, and arguably just as important as all others, is the cost of the wind power.
In January, Rystad Energy used this point to throw cold water on the offshore hydrogen concept when it described current costs as “a showstopper.” The consultancy said using about half the power from a 1-GW windfarm would result in a green-hydrogen price of €5.10/kg ($6/kg).
In other words, taking production offshore may help companies achieve a net-zero carbon status but it also appears to have a net-zero impact on the unattractive economics. Rystad acknowledged that more competitive auctions for windfarms and advances on electrolyzer technology could improve the outlook.
Nevertheless, there is a big carrot here for windfarm operators to consider joining forces with hydrogen production.
Peters noted that North Sea windfarms are running out of near-shore real estate and will need to move further offshore in order to ensure grid balance. “That really poses a bottleneck to the further growth of offshore wind beyond 2030,” he said.
These so-called far-offshore windfarms will face increased costs as their power cables to shore must be longer. This could be mitigated, though, by coupling future installations with hydrogen production.
Peters pointed to a map during his remarks at OTC showing the extensive network of pipelines in the North Sea that terminate at points inside the Netherlands, the UK, Germany, and Denmark.
What TNO and others are proposing is that these pipelines start to be thought of as power cables. Peters said the biggest trunklines could each hold 10 to 20 GW of power potential in the form of flowing hydrogen.
This would also lower the cost for onshore power stations that convert the direct current voltage coming from the windfarms into alternating current, which is what the grid runs on.
There are concerns over pipeline compatibility, though, since hydrogen causes embrittlement in steel. However, Peters said some of the latest studies show that under the right conditions (i.e., pressure, temperature, and the pipeline metallurgy) that much of the existing infrastructure will be suitable for hydrogen transport.
On the high end, it is believed that about 20% of hydrogen can be mixed with natural gas in a conventional pipeline before problems arise.
In the PosHYdon project, hydrogen will flow into a pipeline at a maximum 10% concentration in the natural gas stream to a hub platform. From there, the hydrogen will flow to Rotterdam in a larger multiphase line at a 1% concentration.
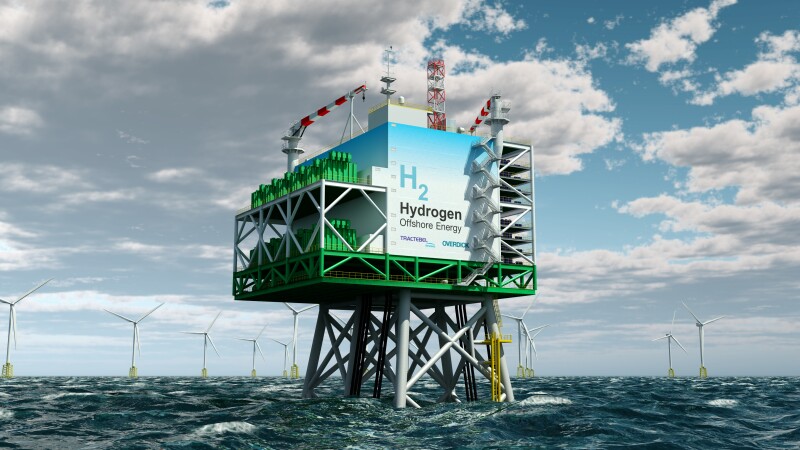
New Infrastructure and Innovation
Existing infrastructure does help lower the capital requirements for hydrogen production—to an extent.
Beyond the North Sea, others including Saipem in Italy’s Adriatic Sea are considering the reuse of oil and gas platforms to house the electrolyzers. But while existing infrastructure can lower capital requirements, it also places a constraint on the size of the hydrolysis plants that can be used.
For instance, the PosHYdon project was limited to a 1-MW electrolyzer because of available space on the platform’s topside and its crane’s weight limit.
Even if bigger platforms are chosen for future projects, there is still the strong likelihood that scaling up to 100 MW and beyond will require dedicated, purpose-built facilities. One such proposal is Belgium engineering firm Tractebel Engie’s design for a 400-MW green-hydrogen platform.
Dedicated platforms are just one of the ideas swirling around. In February, the Danish government approved plans to build two manmade “energy islands,” one in the Baltic Sea and one in the North Sea, to house hundreds of wind turbines. The concept is still in the study phase, but the islands would likely be large enough to also accommodate electrolysis plants.
Whether retrofitted or installed on new facilities, yet another idea is to mix green hydrogen with ammonia. Ammonia is a proven “carrier” of hydrogen energy which allows the clean-burning gas to be transported as a liquid.
Today, ammonia is primarily used around the world to make fertilizer and treat wastewater. But with hydrogen attached, it has the potential to become the next bunker fuel for the world’s maritime fleet, which is in need of sulfur-free alternatives.
It could also be used to power offshore facilities, limiting the need for electrification as a way to decarbonize. This idea was also submitted at this year’s OTC by oil and gas technology firm NOV.
In OTC 31294, NOV outlines a concept for subsea storage tanks that will be filled with liquid ammonia laced with green hydrogen.
For a platform running on 20 MW of power and about 100 km from shore, NOV estimates around $250 million in certification costs. Opting for subsea green ammonia storage instead may cost about half that figure.
Windfarm operators could also benefit here by having the ability to convert their excess generation into an easily stored energy source.
However, NOV acknowledged that its cost projections are probably a bit too optimistic. They do not include the fact that its proposed technology, which is undergoing trials, needs further investment to become realized, nor do they consider the cost of wind power and ammonia feedstock.
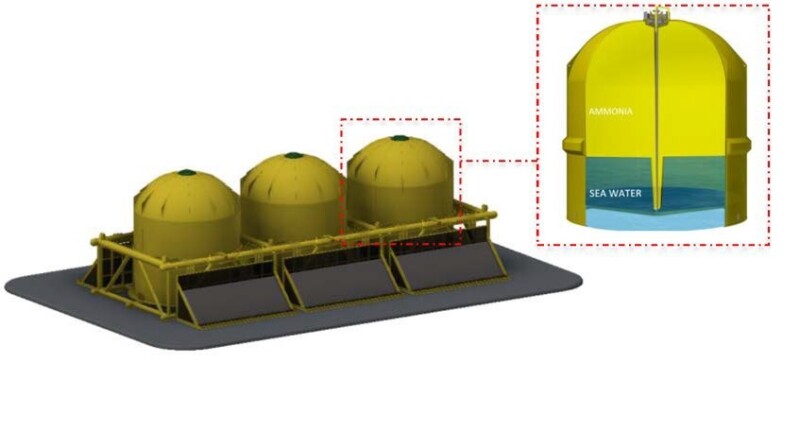
For Further Reading
OTC 30698 Offshore Hydrogen Production in the North Sea Enables Far Offshore Wind Development by Rene Peters, TNO; Jacqueline Vaessen, NexStep; Rene van der Meer, Neptune Energy.
OTC 31294 Subsea Liquid Energy Storage—The Bridge Between Oil and Energy/Hydrogen by Kristian Mikalsen, NOV.