The accelerated deployment of renewable wind sources far offshore creates challenges in transporting large amounts of energy. An alternative being considered currently is energy transport through molecules in the form of hydrogen (H2). The objective of the PosHYdon project, the first offshore hydrogen production plant, whose conception and development are detailed in the complete paper, not only is to build up experience with the production of H2 in an offshore environment, but also will be a test platform for innovative power-to-gas (P2G) technologies and integrated systems.
Introduction
The industry requires the ability to test system concepts in a realistic environment on a pilot-scale size. While several units up to 10 MW are being tested onshore, existing electrolyzer technology to convert power to H2 has not yet been applied offshore. However, many suppliers are developing innovative concepts and are scaling up to larger units.
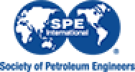