Apache found something positive to say about its huge gas-producing play in the Permian at a time when gas is selling at rock-bottom prices.
When it shut in a 14-well pad on its Alpine High play for 60 days, gas and condensate production surged. It was a rare test of whether a production break can allow water in rock near the fracture face to soak in deeper, allowing gas and liquids to flow more freely.
“The gas rate came back above the pre-soak rate and it’s actually holding in pretty flat, so it shows there was some impact and the condensate rate came in higher than the pre-soak rate,” said Dave Pursell, executive vice president of planning, reserves and fundamentals, during the company’s third quarter earnings call.
The wells were on the huge Blackfoot pad, which Apache had highlighted a year ago as a major test of the industry trend toward concentrating many wells at a single location to reduce development costs. In mid-2018, the company said the pad was producing 99 mm ft3/d, and 200 B/D of oil from 12 wells.
Based on the comment during the call, production since then has been disappointing.
“We thought, let’s take advantage of low commodity prices and initiate a 60-day soak to really understand whether it is a relative permeability issue or what is the mechanism for the underperformance,” Pursell said.
The price of doing the test was a significant decline in Alpine High production—Apache said the shut-in was a prime reason for a 30% drop in production there. But with gas prices so low, the expected upside apparently justifies the revenue delayed.
During that earnings call, Apache also said it would reduce the number of rigs working in the Alpine High play from five to two so it could concentrate on Permian Basin acreage.
Stories about the benefits of soaking have been around for a long time. As has talks about its downsides. In those cases, production was not an option, often due to lack of pipeline access or processing facilities.
Apache tried soaking on the big pad because, “a significant amount of water was pumped into a small area of the reservoir, which may have impacted well productivity,” Pursell said.
To answer that question and others, Pursell said Apache has “a team of folks working on the Blackfoot and all the multiwell pads we drilled and completed to date.”
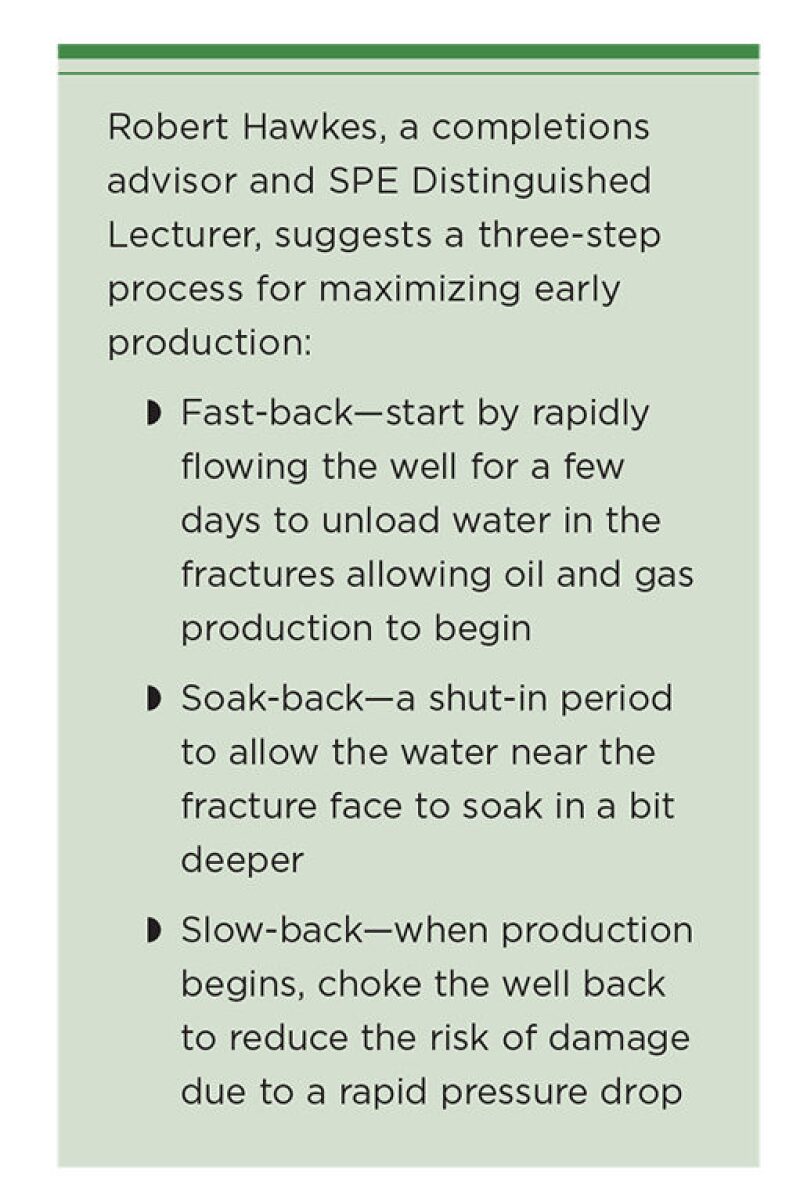
Is It Worth It?
Apache is getting in the middle of an argument over whether soaking is worth the production days lost. While it often does cause a production spurt, the gains can quickly fade and skeptics argue that soaking can cause clay-rich rocks to swell, causing damage.
Robert Hawkes, general manager at Abra in Canada and an SPE Distinguished Lecturer, has long advocated soaking. He said the industry needs to realize that water’s impact goes beyond fracturing rock and delivering sand to prop fractures.
“Water cannot be damaging or we would not be pumping so much water today. So if water is not damaging, is there a way to have water be your friend? And we are saying yes. It’s called soak-back,” said the long-time Canadian completions analyst.
Soak-back is the middle step in a three-step routine for early well production. Hawkes said it begins with a short period of rapid production, called fast-back, followed by soaking, or soak-back, and then production at a rate slowed by choking to manage gas pressure loss—slow-back.
During the shut-in period, dry, clay-rich rock sucks in water-saturated rock near the fracture face, increasing the relative permeability so that more hydrocarbons will flow. That period also gives additives in the fracture fluid time to get into the ultralight tight rock and begin to work.
The fact that only a fraction of the water pumped into productive wells comes back argues that reservoirs are capable of taking in a lot of fluid. But soaking drew little notice during the years when the formula for producing more was simply pump more water and sand and produce as fast as possible.
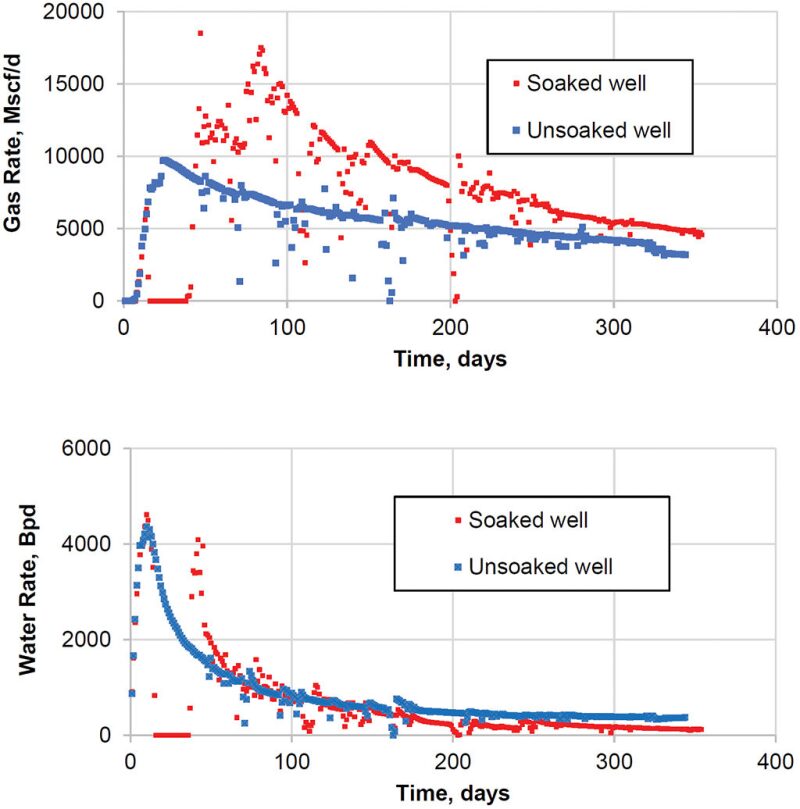
What’s the Formula?
Lately Hawkes said he has been getting some soaking questions, including one from an international oil company asking for equations it can use to model whether soaking will improve the performance of its unconventional wells in Canada.
Unfortunately, Hawkes had to tell them there are no widely accepted formulas that consider all the variables that go into answering questions such as: What is the most cost-effective shut-in period for soaking?
A technical paper based on Apache’s research work delivered at the recent Unconventional Resources Technology Conference said the company launched the project because there was not much data on the effect that soaking had on gas production from tight formations. “The selection of soaking time is still arbitrary” (URTeC 393).
When advising pressure-pumping customers, Hawkes felt the need to offer a more specific answer than it depends.
Hawkes settled on 22 days. That was chosen because “it was longer than seven days and I knew if I said a month they would call me a heretic.”
That pat answer does not satisfy Hawkes, who wants answers based on petroleum engineering rather than customer psychology. He also saw other questions about how water affects reservoir rock that need to be answered.
To fill those gaps he supported research at the University of Alberta by Hassan Dehghanpour, a petroleum engineering professor there who is also an SPE Distinguished Lecturer. His talk highlights his work on unconventional rock fluid interactions, with a focus on using surfactants during fracturing, and using soaking time to increase imbibition.
Despite years of experience showing that much of the water pumped during fracturing stays in the reservoir, Dehghanpour said it still can be hard to convince experts that water can soak a few inches into tight rock.
“Some people do not even believe that water can imbibe” in shale, he said. At a recent SPE event, one prominent petroleum engineer said, “I know the field data. It looks like water is going somewhere and producing hydrocarbons, but I cannot believe that in this nanodarcy rock.”
He said petroleum engineers often miss two additional driving forces for water suction—the force applied by dry clay-rich rock, and osmosis when there is a large differential between the salinity of the fracturing and reservoir fluid.
Hawkes is certain that reservoir rock imbibes water and that can increase production, but he is not going to promise the gains will always justify the production hit during the shut-in.
“Is soaking damaging? No. Is soaking going to make me more money? I cannot say that from a universal point of view,” he said.
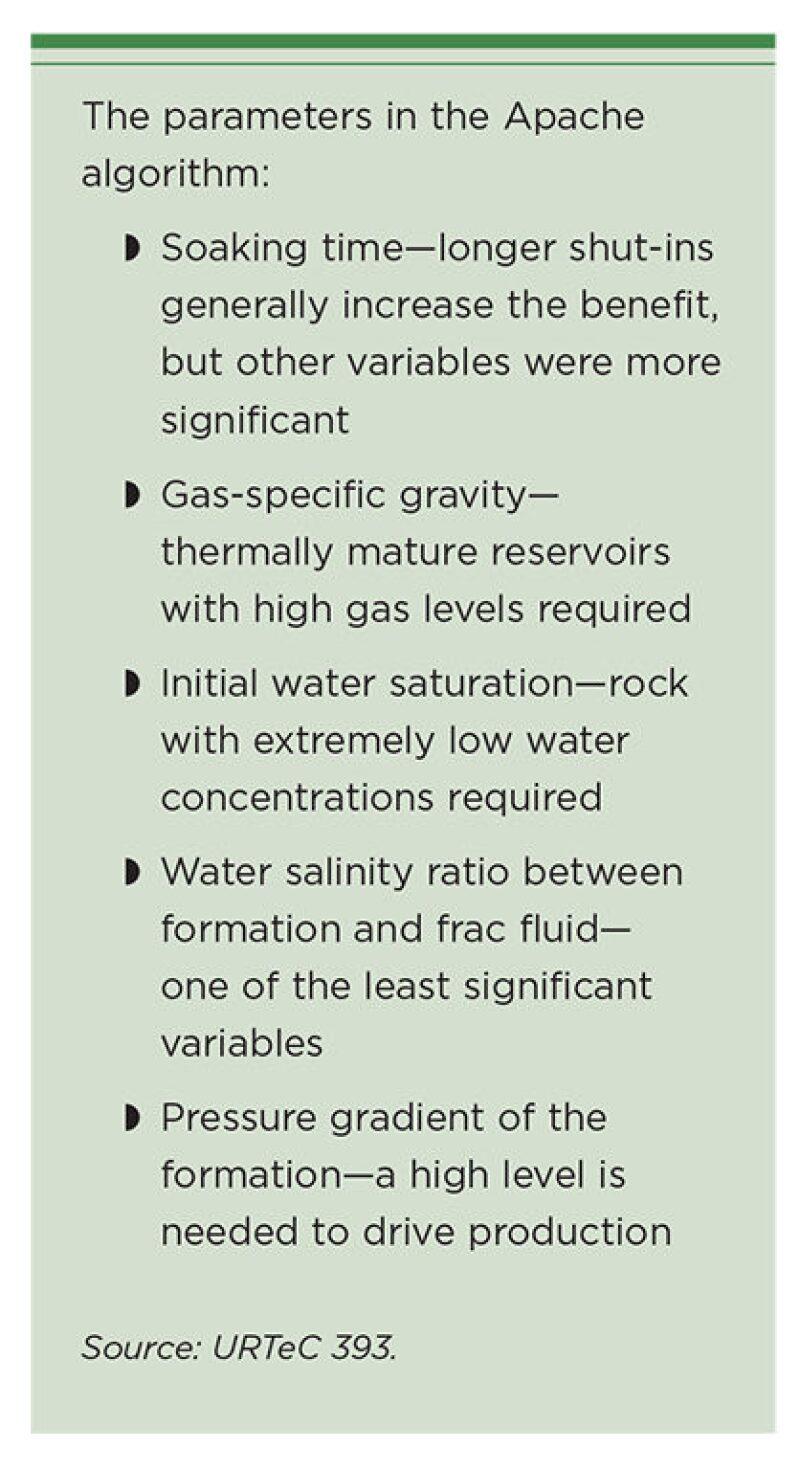
Possible Answers?
Apache is trying to answer those questions by analyzing reservoir and production data from multiple wells.
An early effort, which is not based on Blackfoot data, was the URTeC paper offering a formula for modeling the impact of soaking on a wells’ ultimate recovery. Predictions are based on a handful of variables, some related to the reservoir’s ability to imbibe fluid, and others related to the force available to drive productivity.
“Soaking will work only if the initial water saturation is low. As a result, the formation will adsorb fracturing fluid during the shut-in period. The best shale met this condition in the Marcellus and Eagle Ford” where the water saturation is near zero, the URTeC paper said.
Dry rock with a water saturation of 10% or less—is likely to imbibe. If the water saturation is high—40% or more—“soaking will have a negative effect on 50% of the wells,” according to a second Apache paper (SPE 196611), delivered at the SPE Eastern Regional Meeting.
The formula also favored formations likely to offer the pressure needed to sustain production based on high gas content and high pressure to drive production. The salinity ratio between the fracturing fluid and the formation appears less significant.
Strong numbers in key variables can outweigh weaker numbers in others. For example, the formula favors wells with high thermal maturity—mostly producing gas—less mature rock holding oil can be a candidate.
“Yes, we can soak an oil well based on other parameters like pressure and water saturation and clay content,” said Ahmed Farid Ibrahim, the lead writer who works in engineering research and development at Apache.
Only Oil Please
Production from an oil well in the Montney surged 700% after the Canadian well was shut in for seven months, according to a University of Alberta paper (SPE 194363).
While both the oil and gas flowing from the well jumped after the shut-in ended, the oil flow then sunk at a bit faster rate than before, Dehghanpour said. This disappointing result is an example of how, in enhanced oil recovery studies, “you can change the initial rate but it is really hard to change the decline rate.”
While gas gains were more durable, that is not an industry priority.
“In that particular case I showed it to one operator and said you would be producing more gas but no more oil,” Dehghanpour said. “The producer was not impressed by the gas gain, saying, ‘We don’t care, we want oil.’”
While that soaking test result did not deliver lasting gains, it is too soon to say if soaking can improve oil production based on scant data.
Explanations for why soaking effects wear off include water remaining near the fracture face, called “phase trapping”—a blockage created by a buildup on gas liquids—to the fact that big liquid molecules are simply harder to produce than tiny methane molecules.
Dehghanpour was happy to have field data, which companies are reluctant to provide, but it was not easy to tease out the soaking impact from a tangled knot of facts.
The rock in the producing zone was dry enough for soaking, but it was below a porous water zone that was the source of a lot of produced water.
Production began with 33 days of flowback followed by a two-month shut-in, five months of production on a jet pump, a seven-month shut-in for surface construction, and finally production with a gas-lift system.
During the analysis, the gas injected for gas-lift from the production was removed, but is it is hard to know what impact that had on the liquid output it was supposed to help produce. The pressure drop during the initial five months of production reduced the drive behind oil production and increased the gas produced.
Another variable was an additive—a micro-emulsion surfactant that promised to free more oil by flipping oil-wet surfaces, attracting oil—into ones that are water wet. It was also formulated to facilitate more flow through tight pores by reducing the high interfacial tension.
Its actual impact depends on whether there was still micro-emulsion in the reservoir after eight months of production. One reason Hawkes offers for shutting in a well early is it gives additives time to work into the rock before production pulls them out.
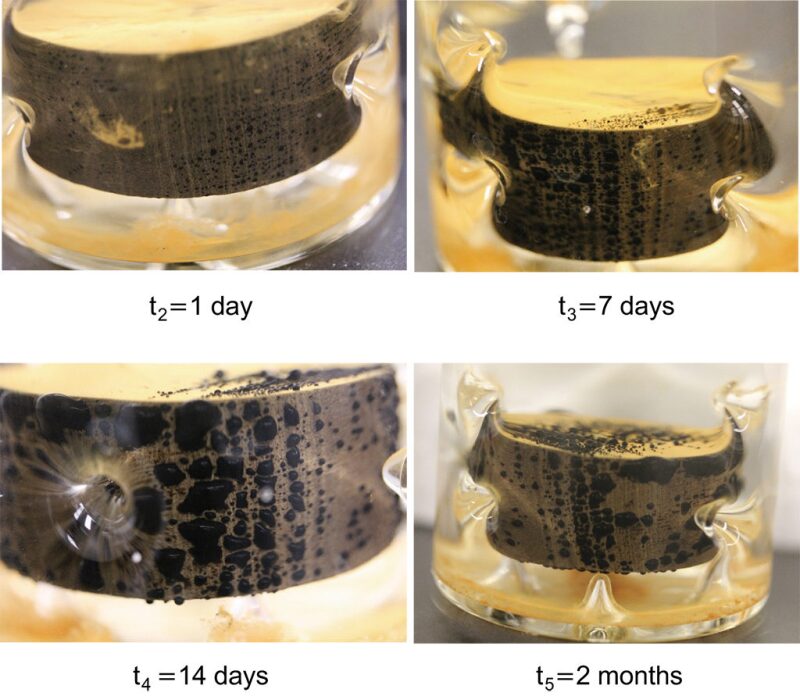
Net Present Value
Dehghanpour is working with one company to develop a method to estimate how various soaking times will affect the net present value of a well.
More data are required to create a method capable of delivering valid predictions on a broader basis. Soaking a core in a jar shows the impact water can have, but fluid in the ground does not have the same access to the rock.
Those tests show injected water with a low level of salinity can be drawn into high-salinity pores by osmosis and expel oil trapped inside.
Another set of tests plus modeling showed that the shut-in might allow more oil to flow out by significantly increasing the relative permeability on the fracture face, likely because soaking removed water blocks the hydrocarbons.
A University of Alberta study measured how much water was imbibed by a core sample in a lab test and concluded the process could be a “viable mechanism for water loss during soaking.” The intake is higher in rock with a high clay content, which can cause cracking, which might add flow paths (SPE 167713).
A Penn State core study concluded, “Formations with greater clay content are more vulnerable to damage from leak-off and are less likely to recover with increased soaking time. In fact, soaking time may exacerbate damage in very tight shales” (SPE 178640).
The lead writer on the paper, Nirjhor Chakraborty, who was then a graduate student at Penn State, said soaking can work in the right rock. “We believe that the soaking time can be a powerful tool, but one that can be quite harmful if not applied carefully and appropriately.
“My understanding is that most unconventional wells being drilled today target low clay, and relatively higher-perm rock (microdarcies or higher). Siltstones and tight gas rather than true shale in the geologic rather than engineering sense. It may be that soaking is beneficial in these reservoirs.”