The context of last year’s Well Integrity Technology Focus was the repurposing of existing oil and gas wells for carbon storage, flow-wet material conformity, and associated integrity risks. Typically, oil and gas producing wells are abandoned toward the end of their life cycles with reservoir pressures depleted compared with the virgin pressures. Carbon capture and storage (CCS) projects, however, present different operating conditions.
First, the pressurized containment sites have a higher life expectancy, say, between 50 and 100 years. Second, the containment pressure is possibly higher than the virgin pressure. The overpressure limit is dependent on several factors, especially the caprock sealing capacity. It goes without saying that CCS storage in wells requires long-term integrity (i.e., for the entire project life cycle). It is well-known that barriers such as cement and casings deteriorate over time. Deterioration of barriers may be accelerated by chemical reaction with carbon dioxide or thermal cycling. Hence, these storage sites could present unique life-cycle integrity risks perhaps never experienced by the oil and gas industry.
To further explain the scenario, a possible breach of the confining strata resulting in pressure communication to the overburden means CO2 finding its way through the deteriorated well barriers of any active or shut-in well, resulting in CO2 ingress to the upper formations; groundwater contamination; or, in a worst-case scenario, appearance at the surface. Therefore, one of the important subsurface aspects of a CCS site is the presence of two seals (i.e., primary and secondary), with sealing capacity of both caprocks characterized robustly. Lack of double barriers or improper characterization of these confining strata could present a scenario wherein CO2 flows into overburden (i.e., above the caprock). The wells’ outer annuli then could become a potential path of least resistance for CO2 to migrate further up.
Such situations can defy the primary objective of CCS projects and can require mitigation with proper attention to detail following the “as low as reasonably practicable,” or ALARP, principle. The scenario discussed is unique and complex and requires continuous managing and monitoring of CCS storage sites. Furthermore, the role of artificial intelligence and automation is seen as imperative during the operational stage of the project.
In addition to the primary paper selections synopsized here, three SPE papers focusing on artificial intelligence and machine learning as tools for well integrity management are recommended as alternates for further reading.
This Month’s Technical Papers
Engineered Materials, Machine Learning Enhance Carbon Storage Well Integrity
AI-Based Well-Integrity Monitoring Shows Promise
Study Sheds Light on Optimization of Well-Diagnostics Investigation
Recommended Additional Reading
SPE 212479 Improve Well Integrity Using an Annular Barrier AI Toolby Eirik Time, Equinor, et al.
SPE 211537 Transforming Production-Phase WIMS to a Game Changer Smart Well Integrity Monitoring System With Real-Time Automated Engineering Analyticsby Mohammed Jasem, ADNOC, et al.
SPE 216600 Paradigm Shift in Well Integrity Management Through the Use of Autonomous Wireless Well Intervention Robots by Julio Q.M. Guedes, Ouronova, et al.
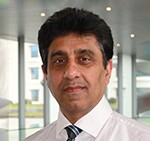
Sandeep Dhawan, SPE, is a principal well engineer at WellPerform in Denmark. A drilling engineer specialist, he has led high-pressure/high-temperature (HP/HT), extended-reach drilling, and deepwater projects in geographical areas such as the UK, the Danish and Norwegian North Sea, the Middle East, Africa, and South Asia. Before joining WellPerform, Dhawan worked as principal drilling engineer and subject-matter expert in well design at Maersk in Copenhagen. He is a core group member of Shell E&P for the Drilling Engineering Manual standard (DEM1) and authored the first HP/HT casing design standard for Maersk in Denmark and Wintershall DEA in Germany. Dhawan has been an active member of SPE since 1990 and has written several SPE papers.