Emissions are in the air and in the headlines every day. Whether the discussion is on human health impacts of pollution, greenhouse gas (GHG) emissions and their impact on climate change, or the misleading performance of a diesel engine, the bottom line is there is a global focus on emissions.
Emission discussions are also in the forefront of the oil and gas industry. In 2012, the US Environmental Protection Agency (EPA) mandated new emission rules for our industry dealing with volatile organic hydrocarbons (VOCs), hazardous air pollutants (HAPs), and, most recently, methane. On 18 August, the agency proposed additional measures (EPA 2015) that supplement the earlier regulations and that “together will help combat climate change, reduce air pollution that harms public health, and provide greater certainty about Clean Air Act permitting requirements for the oil and natural gas industry.”
The rules have set limits on emissions. If they cannot be captured, the emissions must be combusted at a 95% destruction efficiency at a minimum. Destruction efficiency is not as extensive a measure of performance as combustion efficiency; however, the move to performance-based legislation is a positive one and will most certainly lead to improved air quality and a healthier relationship with communities in close proximity to oil and gas development. Within the US, various states have or are in the process of enacting legislation specific to their local situation, on the proviso that their requirements are not weaker than the federal rules.
In Colorado, for example, much of the industry activity occurs in the vicinity of communities. The state regulator is moving toward mandating devices that not only combust efficiently, but also fully enclose the combustion to eliminate the visibility of the flare. It is also spot inspecting facilities with special cameras that detect uncombusted hydrocarbons, which are a clear indicator of poor performance. Companies that are emitting uncombusted hydrocarbons will be subject to considerable fines.
North Dakota has put a rule in place that the industry must find an acceptable method of using a significant, measurable portion of a well’s associated gas, or oil production from that well will be capped.
There are other situations in which the new EPA requirements, combined with state rules, will result in improved operations.
The existing 2012 EPA legislation covered natural gas wellsites, production gathering and boosting stations, natural gas processing plants, and natural gas compressor stations. The proposed EPA legislation requires the reductions of methane and VOC emissions from hydraulically fractured oil wells and extends the emission reduction targets downstream covering equipment in the natural gas transmission segment.
In view of this regulation, two questions are central to the emissions issue.
- Is there a technology that can deliver results cost-effectively and address the community concerns about emissions?
- Is it possible to comply with the new rules in the current low oil and natural gas price environment?
Venting and Flaring
In the early days of petroleum exploration, associated gas was not considered a useful product because of the difficulties in transporting it to markets and the low price it received. As a result, gas was simply burned off at the well or vented into the atmosphere. Unsophisticated means for combustion continued from the early years and well after the first patent for the flare stack was submitted by Exxon Research in 1951.
Even today, flaring and venting continue in locations where local markets and gas transportation infrastructure are lacking, or where the gas itself is of low volume or contaminated with other incombustible gases and therefore uneconomic and impractical to conserve. We are unfortunately again in a period of low oil and gas prices, hence any technology solutions have to make economic sense.
Venting of natural gas, especially methane, the key constituent of natural gas, has a significant impact on air quality and climate change. Natural gas contains VOCs and HAPs, which affect air quality and human health. According to the EPA, methane is the second most prevalent GHG emitted from human activities in the US, and nearly 30% of these emissions come from oil production and the production, transmission, and distribution of natural gas.
The global warming potential (GWP) of methane is 25 times greater than that of carbon dioxide (CO2), and the venting of methane releases more than nine times as much CO2 equivalent GHG on a tonnage basis.
This also shows the impact of combustion efficiency on the amount of GHG emitted from methane combustion, especially poorly combusted gas. Quantification of the GHG emissions during gas flaring is difficult because the measurement of the efficiency of a flare is problematic. The ultimate efficiency of a flare is governed by many factors: composition and heat content of the gas; size of the entrained liquid droplets in the gas stream; direction of the wind, especially if the gas is blown away from the ignition source; velocity of the gas at the flare tip, etc. All these factors are continuously changing, hence there is no single efficiency number that can be applied universally.
For this reason, the EPA has taken the approach of encouraging improved and measurable combustion technology that can be tested to show a destruction efficiency of 95%. The ability to measure performance and address the problem with facts creates a comfort level for communities that express concerns about the health impacts of oil and gas emissions. Public concerns have delayed industry activity and/or caused requests for moratoriums on oil and gas activity. Measurable performance standards create clarity and help develop the social license to operate.
Certain industry participants have also taken the initiative to find the best way of conducting their projects that exceed regulatory requirements by using the best available technology or best practices. In all cases, new technologies are used to effect performance changes, gradually replacing practices that have a negative impact on the environment and/or the communities that live in close proximity to oil and gas developments.
Increasing Combustion Efficiency
Technology not only exists but is readily available that combusts at 100% combustion efficiency. This efficiency measures the device’s ability to reduce hydrocarbons to CO2 and water vapor. Waste gases and associated gas with oil production that is impractical for conservation are combusted to the extent that the impact on environment is significantly reduced.
From the public perspective, this type of combustion results in no odors or visible smoke because of its high efficiency. Regulating agencies have in place a measurable technology that can be audited for performance. Although this seems a place where all jurisdictions should strive to be, only the US has incorporated such performance measures into its requirements. For example, if the 2011 uncontrolled methane emissions of 6.2 Bcf from hydraulically fractured oil well completions (EPA 2014) were cleanly burned at 100% combustion efficiency, GHG emissions from this source would be reduced by 89% at a cost of less than USD 0.40/ton.

Similarly, a business case can be made in dealing with VOC emissions and pollutants known as air toxics, in particular, benzene, toluene, ethylbenzene, and xylene (BTEX) resulting from natural gas dehydration. These pollutants are reduced to benign CO2 and water vapor through clean, efficient combustion technology using 60% to 80% less fuel gas than a traditional flare, thereby significantly reducing GHG emissions and operating costs. The reduction in operating costs typically delivers a payout in fewer than 6 months on the capital investment.
Our analysis has indicated that based on the estimated 38,000 dehydrators in operation in the US, GHG emissions can be reduced by approximately 340 million tons at a cost of less than USD 1.65/ton over a 10-year period while providing an effective solution to VOC and BTEX emissions. Additionally, some clients are using the waste heat from the combustion process to keep the water in vapor form, thus eliminating condensing equipment, water storage, and trucking and disposal costs.
Taking a holistic approach highlights an opportunity to use the waste heat generated from clean combustion for process, building heat, or water vaporization/treatment. If the natural gas is of sufficient quality and volume, then it could also be used to generate power with reciprocating engines for the site or the grid. If the volume or quality of the gas is poor, then the waste heat from clean combustion can be used to generate site power with an organic Rankine cycle engine.
Additionally, there is an opportunity to thermally treat the wastewater stream with the waste heat generated from the combustion of the associated gas. Typical wells that are not served by the pipeline infrastructure may produce in the order of 50 B/D of oil, 250 B/D of water, and 150–200 Mscf/D of associated gas. Even at elevated oil prices, the economic operation of such a well will be challenging. As oil prices drop to below USD 50/bbl, the water handling expense alone will exceed the oil revenue. This is the case when relying on trucking and deep well injection of the produced water.
Although there are elaborate methods to desalinate the entire stream, the economics are not yet suitable for this type of well. Using the excess thermal energy from the associated gas combustion under careful, controlled conditions, up to 85% of the produced water volume is vaporized. The remaining 15% of the original volume is carefully diverted to storage and then disposed of by deep well injection. By reducing the volume, the economics of flowing this well just became positive. This method requires combustion with a device whereby the heat is contained and able to be transferred effectively. Note that the 85% water volume in this example is returned to the ecosystem instead of being lost to deep well injection.
To rephrase, this combustion technology is able to use waste heat to drive water, a valuable resource, into the environment where it will become part of the water cycle and be available for future use.
Of course, the combined heat and power (CHP) is also readily accessible to technology providers that generate and are able to control heat. In short, a better way of doing things leads to a number of positive options.
For the sake of discussion, let us say that your oil well is burning associated gas and the landowners nearby are complaining about black smoke and odors. You have just decided to purchase a new combustion device. After 3 months of better air quality and no complaints, you decided that you would like to manage your produced water differently. You currently spend USD 2,100/day for water transportation and disposal and you can rent a vaporizer at USD 1,100/day. This well generates USD 900,000 yearly in oil revenue, and you have just added USD 300,000 yearly to this well’s bottom line without even looking into replacing the diesel generator with a CHP option.
Emission regulation will continue as the public becomes increasingly concerned with the potential health impact. The rules continue to get more stringent. The challenge for our industry is to find ways to effectively comply with the measures, especially in this low oil price environment. We believe the rules create clarity for both the industry and the community and will enable meaningful discussions toward creating the social license to operate.
There is a strong business case for change. Doing things more efficiently will cost less, and moving projects forward without public delays will also see oil production flowing sooner. It is a matter of knowing which technologies are available to resolve these new challenges. Technology is already here to provide for regulatory compliance, improved air quality, social acceptance, and true economic value.
References
EPA. 2014. Oil and Natural Gas Sector: Hydraulically Fractured Oil Well Completions and Associated Gas during Ongoing Production. US Environmental Protection Agency, Office for Air Quality Planning and Standards, Washington, D.C. (April 2014).EPA. 2015. EPA’s Air Rules for the Oil & Gas Industry. Proposed Climate, Air Quality and Permitting Rules for the Oil and Natural Gas Industry: Fact Sheet. US Environmental Protection Agency, Washington, D.C. (18 August 2015).
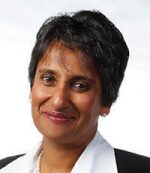
Audrey M. Mascarenhas is president and chief executive officer of Questor Technology. She has worked in the energy and environment industry for more than 33 years, starting her career with Gulf Canada Resources. At Questor, she has focused on technology solutions to eliminate flaring and venting and the opportunity to utilize the energy for power generation and water treatment. Mascarenhas served as an SPE Distinguished Lecturer during 2010–2011 and currently serves on SPE’s Distinguished Lecturer Committee and Communication & Energy Education Committee. She holds a BS degree in chemical engineering from the University of Toronto and an MS degree in petroleum engineering from the University of Calgary.
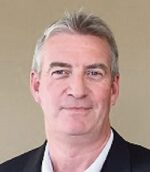
John Sutherland is chief operating officer (COO) of Questor Technology. He joined Questor in 2008 and was instrumental in developing the company’s engineering and technical solutions team. Sutherland became COO in 2014 and, prior to that, held technical and managerial positions during his 26-year career with various exploration and production companies and the Alberta provincial energy regulator, AER. He is a graduate of the British Columbia Institute of Technology and the University of Calgary with degrees in mechanical engineering.