Real-time monitoring of pollutant, toxic, and flammable gases is important for health and safety during petroleum-extraction and -distribution operations. Currently, many methods exist for detecting such gases, but most sensors suffer from slow response times, high power consumption, high costs, or an inability to operate in harsh conditions. This paper demonstrates a small, low-cost, low-power, highly sensitive nanomaterial-based gas sensor specifically targeted for the detection of hydrogen sulfide (H2S).
Introduction
Current personal monitors for H2S are typically electrochemical-based sensors because of their low power consumption, relatively small size, and satisfactory selectivity. However, electrochemical cells typically have fairly slow response times and are prone to degradation or errors at extreme temperatures and humidity. Semiconducting-metal-oxide (SMO) sensors have fast response times and simple interface electronics and can operate in harsh conditions, making them a mainstay of industrial monitoring. However, the power required to operate a conventional SMO sensor is typically hundreds of milliwatts. Therefore, operation of a handheld monitor using conventional SMO sensors is not feasible for long-term monitoring. To overcome this problem, the authors have fabricated very-low-power microheaters and functionalized them with tungsten oxide (WO3) nanoparticles to create an H2S sensor suitable for long-term battery-powered operation.
Description and Application of Equipment and Processes
Microheaters. Two types of microheaters are used in this research. The first is a commercially available microheater. This microheater uses a serpentine platinum heater sandwiched between a thin silicon nitride membrane on the bottom and a silicon oxide membrane on the top. Two gold electrodes provide electrical contact to the sensing layer. The second type of microheater was designed and fabricated at the University of California at Berkeley in the Center of Integrated Nanomechanical Systems. This microheater uses a suspended polysilicon bridge as the heater. The heater is isolated from the sensing layer with a thin silicon layer above and below the heater. Two platinum electrodes on top of the heater bridge provide electrical contact with the sensing layer.
Nanoparticle Functionalization. The WO3 nanoparticles used in this study were suspended in isopropanol by means of ultrasonication and deposited on the microheaters by spincasting or dropcasting.
Sensor Measurement. The WO3-nanoparticle-based microheater sensors are measured by use of a source-measure unit (SMU). One channel of the SMU is used to apply a voltage to the microheater and measure the current. The other channel is used to apply a voltage to the nanoparticle sensing layer and measure the current through the sensing layer. Data are collected with open-source instrument control software.
Gas Delivery. The sensors are exposed to a gas stream of varying analyte concentration by means of a custom-made gas-delivery system. Using mass flow controllers, the gas concentrations are diluted from a target-gas cylinder balanced in nitrogen with air, which was cleaned and dried in-line through activated-carbon filtration and pressure-swing adsorption dryers before dilution with the target gas. The humidity of the gas stream is controlled by a controlled evaporator mixer. The concentration of H2S was monitored by use of a reference sensor.
Presentation of Data and Results
Nanomaterials, especially metal-oxide nanomaterials, have been inventively researched for sensing applications because of their large surface-area/volume ratios, which enhance the effect surface reactions and adsorption have on their electrical properties. Nanostructured materials also have the beneficial capability of being heated to high temperatures using very little power. Previous research has shown that WO3 nanomaterials perform well as a sensor for H2S. However, as with most metal-oxide sensors, the sensors must be heated to obtain sufficient sensitivity and response times. Therefore, the authors constructed WO3-nanoparticle-based microheater sensors for detection of H2S.
The first microheaters used in this study were made using the commercially available microheaters. As shown in Fig. 1, the sensor comprises a microheater (upper left) that is functionalized with WO3 nanoparticles (upper right). As shown in the lower portion of Fig. 1, when the sensor is exposed to 50 ppm at 25°C, the sensor response is very small and slow. However, when the microheater is heated to 300°C, the sensor responds in seconds and the response magnitude is more than 500 times that at room temperature. This microheater requires approximately 40 mW of power to be heated to 300°C. While this is an order of magnitude smaller than the power required by conventional SMO sensors, it is still too large for long-term battery-powered operation. Therefore, to minimize the power consumption of the device, the sensor is operated on the basis of heat pulses instead of continuous heating.
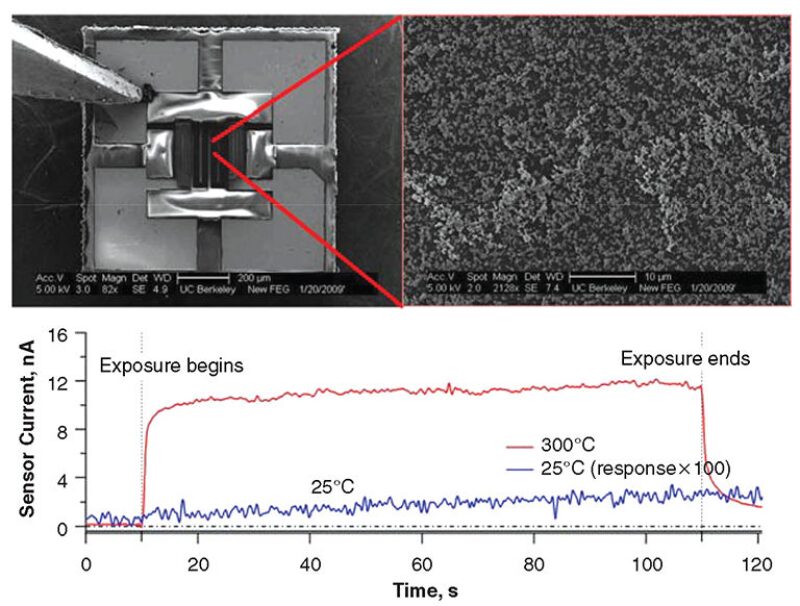
Operating the microheater with heat pulses has decreased the power consumption to less than 10 mW, meaning that a standard AA battery would last for approximately 2 weeks. While this is a great improvement over conventional SMO sensors, an operational lifetime of months to years is more desirable.
The microheater devices designed and specially made for this project were fabricated by use of conventional photolithographic- and microelectromechanical-system processing techniques. Instead of using platinum as the heater element, polysilicon was used. Because polysilicon is more resistive than platinum, smaller structures could be made that are able to dissipate higher power density. Dissipation of a higher power density allows for much-more-local heat dissipation, thereby allowing only a very small structure to be heated. Because a smaller structure is being heated, the overall power consumed to reach a certain temperature will be smaller. An SEM image of the polysilicon microheater is shown in Fig. 2. The polysilicon microheater is sandwiched between two thin silicon nitride layers. The microheater shown in Fig. 2 has a gold/platinum thermocouple (left trace in the microheater bridge) and platinum electrodes separated by 2 µm for measuring the to-be-deposited WO3-nanoparticle network. The power required to heat these polysilicon microheaters to 300°C can be as low as 1.5 mW.
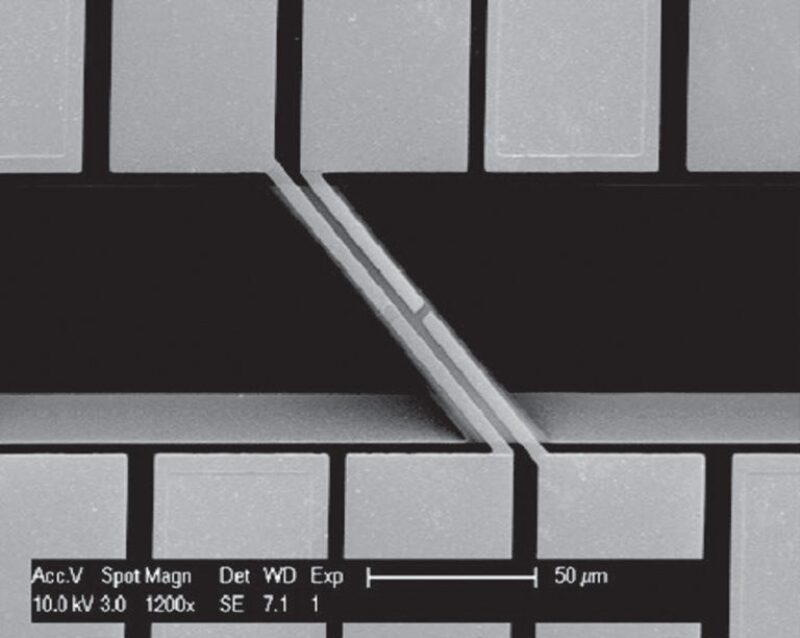
The microheater nanoparticle-based sensor described here shows a dramatic decrease in power consumption vs. commercial SMO sensors. However, the thermal response time of these small polysilicon-based microheaters has been measured to be only approximately 30 microseconds. This feature has enabled a further reduction (of 1 second to 1 millisecond) to the heat-pulse time, while maintaining reasonable sensor response.
This microheater has a peak power consumption of approximately 18 mW to attain a temperature of 300°C, which is the optimal operating temperature for this sensor. The 1-millisecond heat pulses are applied every second, giving an average power consumption of only 18 µW. This level of power consumption approaches the range of electrochemical sensors but with a much simpler method of fabrication and assembly and a much smaller form factor, while being composed of robust, high-temperature-compatible materials.
While the response of the sensor for the ultrashort heat pulses is not as fast as with longer heat-pulse durations (response of approximately minutes, not seconds), this mode of measurement could be used to monitor the environmental conditions. If the sensor conductance begins to respond rapidly in the first few seconds after exposure, the heat-pulse duration could be increased. When the heat-pulse duration is increased, the response time is decreased.
This progress in decreasing the heat-pulse duration from 1 second to 1 millisecond in monitoring mode decreases the power so significantly (to approximately 10 µW) that a single coin cell battery would last for more than 4 years. For heat-pulse durations of 100 milliseconds (i.e., in measuring mode), a coin cell battery would provide more than 2 weeks of continuous measurement. The fact that the average power consumption of this microheated sensor has reached the microwatt regime means that new applications of embedded sensors can emerge.
Prototype Integration
In order to use the nanoparticle-based sensor described, it must be incorporated into a system that can interface to the sensor and communicate with other devices or networks. This system would ideally be low power, small, portable, and accurate. Working toward this goal, the authors designed a system to measure and control the nanosensor and display the data locally as well as transmit the data wirelessly for interpretation either by a nearby user with a WiFi-enabled device or at a central analysis center in another location. The prototype sensing system that was designed and built (shown in Fig. 3) has many capabilities. The prototype has sensor multiplexing capabilities, allowing it to measure up to 12 sensor channels, four of which have high-voltage capabilities, and up to four thermocouples. It can communicate through WiFi to external devices such as smart phones. A separate onboard radio uses the 802.15.4 protocol, which can be used to configure these prototypes into a mesh network of environmental monitors. The prototype also has an audible alarm, a liquid-crystal display, power and user-input buttons, and wireless antennas that dramatically improve communication range. It is also packaged into a National-Electrical-Manufacturers-Association-rated enclosure and has robust, sealed connectors, making it ready for field testing.
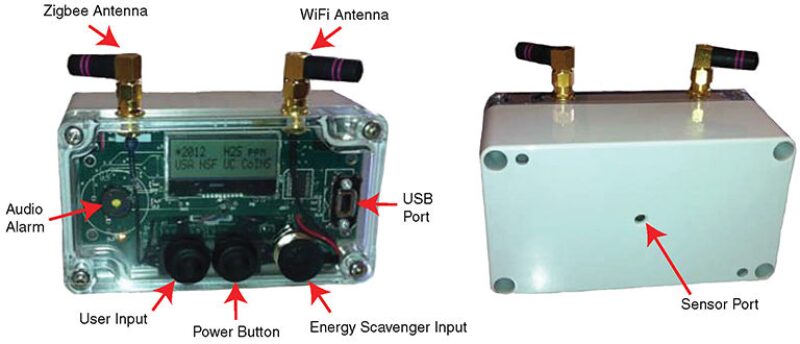
These features enable the prototype to act as a standalone monitoring station that can communicate directly with commercial wireless devices, such as smart phones and computers, without the need for intermediate networks or devices.
The measurement scheme for the nanoparticle-based H2S sensor has been optimized, and the sensor measurement accuracy and noise are comparable to accuracy and noise data taken with expensive, state-of-the-art source meters, but at a fraction of the cost. Fig. 4 shows data captured directly from the sensing system. Note that, in addition to the raw sensor conductance, the sensing system also sends calibrated sensor data in units of parts per million (solid red line) to the computer. Fig. 4b shows data taken by use of a currently commercial source meter. The prototype has the measurement capabilities of rather expensive scientific equipment but with many more features, including wireless communication, data interpretation, and sensor multiplexing.
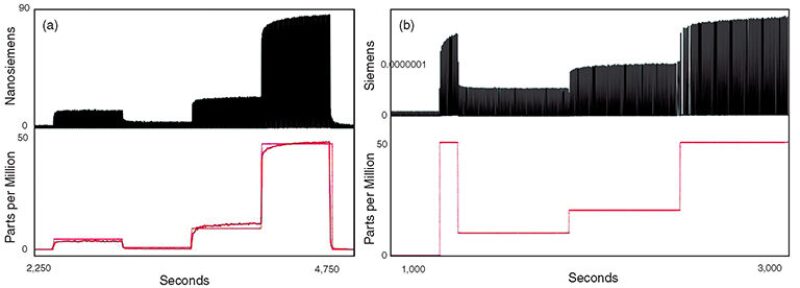
This article, written by Special Publications Editor Adam Wilson, contains highlights of paper SPE 166544, “An Innovative Wireless H2S Sensor Based on Nanotechnology To Improve Safety In Oil and Gas Facilities,” by Marco Piantanida, SPE, Maurizio Veneziani, and Roberto Fresca Fantoni, Eni, and William Mickelson, Oren Milgrome, Allen Sussman, Qin Zhou, Ian Ackerman, and Alex Zettl, University of California at Berkeley, prepared for the 2013 SPE Offshore Europe Oil and Gas Conference and Exhibition, Aberdeen, 3–6 September. The paper has not been peer reviewed.