Hydrogen sulfide (H2S) production has in recent years become a mounting issue facing operators and midstream companies in major US basins.
At present, H2S production appears to be random and poorly understood. As such, H2S is considered by many to be an unpreventable nuisance and one that is largely addressed by treating the dangerous gas at surface before putting it to a sales line.
This article highlights impacts of H2S, possible sources, and a successful case study of a completions operation designed specifically to prevent H2S production in North Dakota’s Williston Basin.
H2S and Its Impacts
H2S is a colorless gas known for its pungent “rotten egg” odor at low concentrations. It is extremely flammable, highly toxic, poisonous, and corrosive. H2S is commonly encountered during the drilling and production of crude oil and natural gas, as well as in wastewater treatment, utility facilities, and sewers.
H2S is well-known for its significant health and safety risks, along with substantial financial implications in the event of an accidental release.
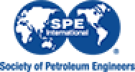