Leveraging technologies from a flow-assurance simulator, a Python application programming interface (API) toolkit, open-source machine-learning (ML) packages in Python, and a commercial visualization dashboard, the complete paper proposes a series of work flows to simplify model deployment and set up an automatic advisory system to provide insight as a means of justifying day-to-day engineering decisions. The complete paper discusses this methodology and provides a case study of its implementation, although this synopsis concentrates on the former.
Background
The authors identify four steps necessary for a valid network model that can describe production-system fluid-flow behavior accurately and support day-to-day decision making. These four steps, detailed in the complete paper, include the following:
- Well-model building and matching
- Well-basis gas lift evaluation
- Network modeling
- Gas-lift-optimization scenarios
Work Flow Objective
The objectives of creating an automated, intelligent production-network-optimization work flow include the following:
- Minimize risk for data-quality issues caused by human error
- Quicken pre- and post-deployment stages of the work flow, thus saving time and resources
- Increase the functionality of a digital-oilfield work flow, including adding a production-surveillance dashboard, extracting publicly available temperature data from a weather-service API, and adding an ML autocalibration work flow
Theoretical Basis
Multiphase Steady-State Flow Simulator. A commercial flow simulator is used to simulate multiphase flow simulation throughout the production system from the reservoir to the surface facilities to enable comprehensive production- (and injection-) system analysis. By the term “steady state,” the authors mean that the mass flow rate is conserved throughout the system, with no accumulation of mass in any system component.
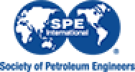