In this study, a numerical simulation workflow was established based on comprehensive modeling of a time-lapse stress field, hydraulic fracturing simulation, natural fractures, and other weak interfaces to analyze casing-deformation mechanisms of shale gas horizontal wells during the multistage hydraulic fracturing process. The authors write that they aim to guide the prediction of, and provide mitigating solutions for, casing-deformation risks while improving stimulation efficiency.
Introduction
The burial depth of deep shale gas reservoirs in the southern Sichuan Basin is approximately 3500 to 4500 m. These have complex geological conditions with developed faults and fractures and high in-situ horizontal stresses. During multistage hydraulic fracturing operations in horizontal wells, establishing an effective prediction method for casing-deformation risks in these reservoirs is a challenge.
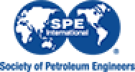