Background
Field trials using a new scale-inhibitor technology that improves treatment lifetime of scale squeezes have been successfully performed in the Gulf of Mexico. Tomson Technologies, in partnership with Shell, developed proprietary nanoparticle carriers that enhance scale-inhibitor adsorption to the reservoir and control the return rate for extended periods of time. This technology results in less chemical bleed off in the initial flowback and increases the chemical retained in the reservoir, allowing for more effective squeeze treatments. Both nanoparticle-enabled phosphonate and polymer inhibitors have now been developed and successfully squeezed in the field.
Phosphonate inhibitors are widely used for squeeze treatment due to their desirable adsorption and release properties in carbonate and sandstone reservoirs. Minor changes have been made to the chemistry, but overall, the fundamentals have remained unchanged for decades. Polymeric scale inhibitors have also been developed for cases in which phosphonates are not applicable. The nano-enhanced technology provides a large improvement of treatment lifetime of 2 to 4 times (200–400%) when compared to incumbents, making this technology advancement attractive even in cases where current squeezes are considered successful.
The well selected for this case study is an offshore formation with a predominantly sandstone mineralogy (approximately 80% quartz) with 25–30% porosity and bottomhole temperature of 183°F (83°C).
Technology From the Lab to Field
A sandpack sample from the trial well was used in the laboratory to determine the adsorption and desorption properties of the nano-enabled inhibitor in realistic rock conditions. Multiple conditioning steps were used before product was injected in a sequence that mimicked field squeeze treatments. Mass-balance results from the sandpack experiment show adsorption of approximately 8 mg of polymer retained per gram of crushed reservoir rock used in the experiment. A typical rule of thumb for phosphonate-scale inhibitors (only as a comparison since this is a polymeric scale inhibitor) is 1–2 mg of inhibitor retained per gram of rock. Therefore, this is considered a large improvement on adsorption.
There are challenges associated with measuring polymers in brine as residuals; however, multiple methods, both in-house and external, were compared to ensure accuracy. The results using the nano-enhanced scale inhibitor show concentrations higher than 1 mg/L of active polymer for over 7,000 pore volume of return in the sandpack experiment.
Complete intact core experiments were also conducted with reservoir fluids and showed no formation damage during the injection of the product with regained oil permeability of 96%. Oil permeability was in the 150–200 mD range for the intact core experiments.
Third-party coreflood testing was performed with nitrified and foamed stages to ensure compatibility with the nano-enabled chemistry. No formation damage was observed with the nitrification of the stages containing the nano-enabled chemistry.
Field Application Case Study
After extensive lab validation of the product and supporting corefloods to de-risk the technology, Well A was selected by Shell to be the first well treated with the new nano-enabled extended-lifetime inhibitor.
The goal of the trial was to confirm there is no formation damage experienced when squeezing this chemical and to demonstrate increased adsorption of the nano-enabled chemistry over the conventional chemistry.
This well was a known high load-up risk and increased in water cut from less than 5% in early 2019 to 45–50% just prior to the scale squeeze; therefore, it was selected as a good candidate to de-risk the injection of the nano-enhanced chemistry.
Well A is an offshore well that has a history of scale squeeze treatments with an incumbent polymer chemistry. Seawater breakthrough was observed approximately 1 year before the nanoparticle-enabled squeeze application.
The predominant scale of interest for this well is barium sulfate (BaSO4), and the previous squeeze treatment dropped below minimum efficient concentration (MEC) in January 2020. The nanoparticle‑enabled squeeze was performed in April 2020.
A topside compatibility test with the nano-enhanced chemistry was performed prior to the squeeze job. One tote of nano-enabled chemistry was delivered to the platform and pumped through surface equipment to ensure no issues were observed with separators, pumps, seals, etc. No detrimental effect was observed from the topside test.
The squeeze was planned to compare the new results with the incumbent chemistry, so the same recipe/procedure as the previous scale squeeze was used. The product names, exact concentration, and stage volume have been removed due to confidentiality. To minimize unload risk in this well, nitrified stages were used.
- Mutual solvent (potassium chloride (KCl)+mutual solvent+biocide)
- 2Nitrified pre-flush (N2+KCl+nano-enhanced scale inhibitor+biocide)
- Nitrified main treatment (N2+KCl+nano-enhanced scale inhibitor+biocide)
- Nitrified overflush (N2+KCl+nano-enhanced scale inhibitor+biocide)
- Foamed overflush (N2+KCl+nano-enhanced scale inhibitor+biocide+foamer)
- Nitrogen displacement (N2)
Strict QA/QC protocols were used during the pump job, and samples were taken in real time throughout the pumping stages. A completed report was issued following the pump job to confirm all fluids were within the provided QA/QC specs. The squeeze treatment was followed by an 18-hour shut-in period after which the well was unloaded.
Well A was producing approximately 3,500 BOPD prior to the pump job. The well does not have a downhole gauge; therefore, treating pressure and pump rate were monitored as an indication of the pumpability of the product. During the previous nitrified scale squeezes in this well, a slight, steady increase in tubing head pressure (THP) was observed during pumping but, mirroring this squeeze, no damage was observed.
Fig. 1 shows the treating pressure during the injection of the main stage; as predicted, a slight steady increase in the treatment pressure is observed for the duration of the injection. This pressure increase can be attributed to the multistage system (N2-fluid-foam) that is present in the reservoir and which has been observed in previous squeeze jobs in this well.
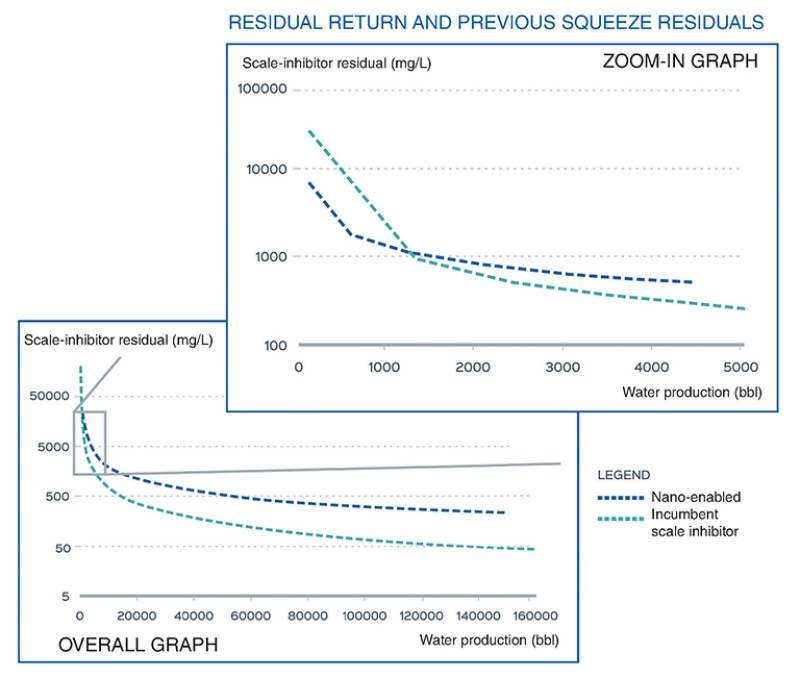
There were no indications of damage throughout the pumping of the nano-enabled inhibitor squeeze. Well tests before and after treatment show that the nano-enabled chemistry did not cause impairment on the well, as shown in the table. Following the squeeze with the new nanoparticle-enabled scale inhibitor, oil rate regained to pre-squeeze levels. Water cut followed the pre-squeeze increasing trend, increasing along the same slope as in the past 12 months and showing no change in the oil/water ratio.

Post-Squeeze Flowback and Residual Analysis
Samples for residual analysis were collected and shipped to three different labs to verify the residual concentration. Residual analysis to date is shown in Fig. 2. The graph shows flowback up to 160,000 bbl where concentration of the nano-enabled inhibitor was substantially higher than the incumbent chemistry at every stage, providing superior protection from scale formation.
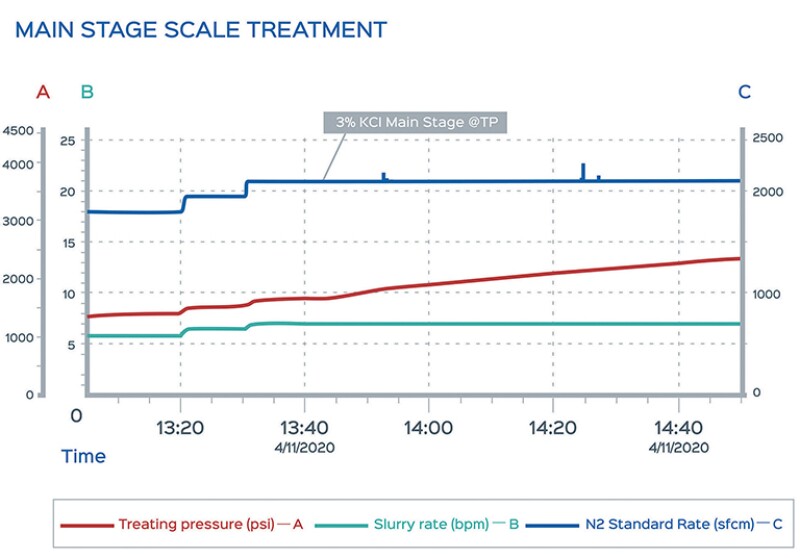
In addition, the nano-enhanced scale inhibitor shows lower amounts of chemical lost in the initial flowback period. Traditional squeeze inhibitors typically lose around one-third of the treatment in the initial flowback period, leaving only two-thirds of the injected product to be effective for treatment. One of the mechanisms of the nano-enabled chemistry is to improve adsorption of the scale inhibitor into the rock, which in turn maximizes the mass of available inhibitor for long-term treatment.
This result from the field trial validates multiple laboratory results showing increased adsorption of the inhibitor into the reservoir material, which can be directly correlated to extended treatment lifetime.
Conclusions
The first nanoparticle-enabled scale squeeze job was successfully performed. This field trial performed in Well A confirmed there was no formation damage experienced during the application of the nano-enabled chemistry. This case study shows the results of a successful deployment of the new chemistry that was developed for this specific purpose between Tomson Technologies and Shell and scaled up by Group 2 Technologies. Flowback samples analyzed showed increased adsorption of the chemical into the formation, and residual concentration will continue to be monitored. Excess inhibitor mass available in the reservoir could indicate a significantly longer squeeze lifetime, as seen in multiple laboratory experiments.
Due to the successful de-risking of the nano-enhanced technology performed in this well, other trial wells have since been performed using nano-enhanced scale inhibitors, both polymeric and phosphonate chemistries, that show significant improvements in scale squeeze lifetimes, currently averaging an increase over incumbent lifetimes of 290% (2.9 times).
This case study shows the first-of-its-kind nanoparticle inhibitor deployment in an offshore well.
Tomson Technologies will continue to develop other nanotechnology-enabled chemicals that significantly improve the performance of existing production chemicals. Multiple other applications for this technology have been identified by operators and are being investigated currently.
Bringing the Chemistries to Market
Tomson Technologies is an independent technology development company that partnered with Shell GameChangers for the development of a nanoparticle-enabled scale inhibitor chemistry. In 2014, Tomson proposed to the Shell GameChanger team the idea of nanoparticles to be used as carrier vehicles to improve attachment and control the release of inhibitors. The project was approved, and a nano-enabled polymeric scale-inhibitor product was developed. Subsequent scaleup from lab bench to manufacturing was performed by Group 2 Technologies in conjunction with Tomson Technologies. Extensive compatibility testing in collaboration with Shell allowed for trial wells to be approved in the Gulf of Mexico (GOM) region for this technology.
Shell operations funded a follow-on development of a nano-enabled phosphonate-scale inhibitor which has been successfully developed, scaled, and field trialed in both west Texas and GOM wells. Other technologies in development include nano-enabled asphaltene inhibitors as well as other scale inhibitors for specific applications such as high-calcium and high-temperature wells.
Tomson Technologies has partnered with Group 2 Technologies to bring these chemistries to the market. Group 2 focuses on bridging the gap between laboratory-developed technologies and successful scaleup, manufacturing, and field application.

Paula Guraieb is vice president of Tomson Technologies with over 10 years’ experience in project management for new technology development related to oil and gas production. She has a background in chemical engineering and environmental engineering.
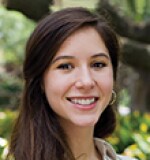
Victoria Brooks is a chemical engineer supporting Shell operations. She is focused on supporting and deploying new technologies in a way that balances operational constraints with innovative opportunities.
Ji-young Lee is a production chemist and a subject matter expert for inorganic scale in Shell, supporting upstream production globally while working on developing new technologies for scale control.
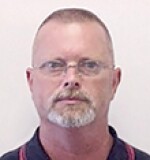
Jay Weatherman recently retired from Shell where he served as a chemical engineer for offshore operations. He has more than 30 years of experience and was closely involved in development and adoption of this technology.
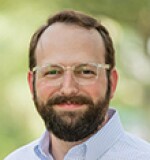
Ross Tomson is president and founder of Tomson Technologies. He is an entrepreneur focused on delivering exceptional innovation and value to the energy industry across the full life cycle of energy production.