You’ve read it in the editorials of JPT or heard it preached from the podium at one of the industry’s technical conferences over the years: The oil and gas industry is notoriously slow to innovate and adopt new technologies.
But what if it just wasn’t so?
Since 1999, the slow-moving oil and gas industry has only managed to push the needle from 75 million B/D to more than 102 million B/D—a remarkable 36% increase in global supply.
This growth came in spite of what turned out to be fairly valid concerns openly expressed by many a quarter century ago that all the so-called “easy oil” had been discovered.
Much of the world’s new supply indeed flows out from complex and/or difficult-to-access reservoirs that in 1999 were far from the minds of most. This includes the rise of the North America’s tight oil and gas plays, the deepwater sector, and a myriad of other megaprojects from Sakhalin to Kashagan to Manifa that have each pushed the petroleum engineering envelope to new limits.
This is to say that the year 1999 represents an interesting turning point in the industry’s technological journey. It was a time when industry professionals, along with the rest of the word, were wondering what changes a new millennium would bring.
As it turned out, many of the key technologies that made the aforementioned developments and others possible were just emerging in 1999 but the impact they would soon have was hardly clear.
1999 is also a useful signpost because odds are, the time that has passed since represents the majority or the entirety of your career—this is your defining era.
According to our data, the average age of SPE membership in 2022 was 48. This would make the average member a 24-year-old back in 1999 which suggests that most of those reading this were at that point still in petroleum engineering school or just getting their feet wet in the industry.
It’s also the case that 1999 was the last time JPT editors took the opportunity to celebrate the publication as it turned 50 years old that year.
Now, as JPT welcomes its 75th anniversary, we are once again reflecting on the progress that’s filled the pages of this publication.
As I thought of ways to commemorate the moment, one of the ideas that came to mind was a list of the most impactful technological developments to arise since our last big birthday bash. To keep the exercise focused I considered only those technologies which have led to some significant change in the core disciplines of drilling, completions, and reservoir engineering.
Lists are nothing new to us and, in fact, my late father penned one several years ago for JPT.
Steve Jacobs, an offshore roughneck turned oilfield entrepreneur and lifetime SPE member, acknowledged that list making is a tricky business in a guest editorial written about his top 10 all-time great oilfield technologies back in 2010.
His way of measuring a technology’s impact boiled down to how hard it would be for the industry to live without it. The biggest pitfall of the exercise, though, is that there are always a few technologies left off that warrant reconsideration.
“But,” as my father wrote, “that is the fun of compiling such a list—discussing and arguing which ‘players’ should make such an all-star, all‑time ‘team.’”
With that, and in no particular order, I present my selection of the top 10 technological breakthroughs of the past quarter century.
1. Hydraulic Fracturing and Horizontal Wells
This will not be a surprise, but no list of this sort would be complete without paying homage to the tandem of multistage hydraulic fracturing and horizontal wells. Major credit is owed to the technology for reversing the decline in US oil production and propelling it from 5.9 million B/D in 1999 to almost 13 million B/D today—not to mention its contribution to making the US the world’s top gas producer.
The unprecedented growth in unconventional oil and gas production that began in the US has since spread well beyond and today includes major tight-oil and (mostly) tight-gas projects of various maturities across Canada, Argentina, China, and Saudi Arabia.
It must also be mentioned that the advent of modern hydraulic fracturing has led to a Cambrian explosion in surface and subsurface technologies—all designed to scale and improve the practice. Suffice to say, the completions sector has witnessed the most transformation among all of the industry’s major engineering disciplines in the past 25 years.
2. Deepwater Exploration
The growth of the deepwater sector is among the most impressive aspects of the past 25 years. In 1999, with the future of this sector still not guaranteed, deepwater production in the US Gulf of Mexico surpassed that of the shallower shelf projects and never looked back.
The limits of technology back then meant wells could only be drilled in water depths of around 6,000 ft—now considered by some to be the threshold of “ultra deepwater”—whereas today’s most capable assets can drill in waters twice as deep and expectations are that 13,000-ft drilling depths will soon become possible.
Many key advancements have made this possible including everything from the design of drillships and semisubmersibles to new subsea electronics, blowout preventers, and an innumerable cast of other high-pressure/high-temperature technologies. While still holding a relatively small share of global production at around 6% in 2022, the deepwater sector is poised for continual growth this decade and, according to some projections, may exceed 17 million BOE/D of production by 2030.

3. Automated Drilling
The advance of this technology arena is one that many were calling back in 1999 and we think the prognosticators of the past are owed credit, albeit progress has been less linear than most expected. The ultracompact, robot-like “rig of the future” that some saw coming and hoped to bring to market never fully materialized.
The industry has instead witnessed a gradual shift towards integrating advanced automation software with existing rig technologies and control systems. Led by a global cadre of passionate experts, the result is a nuanced but ever-improving form of automation. With some prototype exceptions, the modern rig is considered a partially automated, highly monitored machine but in most cases human oversight is still playing a crucial role. This may fall short of the grand vision, but early adopters of even basic elements of automation have shown that the technology shaves days and many millions off drilling campaigns. Furthermore, this space appears to be maturing as it delivers higher orders of automation with each passing year.
4. Fiber Optics
While many people foresaw the rising importance of downhole sensor technology in 1999, not many were referring to fiber-optic cables which have mainly been used to detect sounds (acoustics) and temperatures that can be deciphered into key diagnostic points. Uptake for downhole fiber optics has largely been driven by the North American unconventional sector which has come to rely on it for high-resolution visualizations of fracture dynamics.
The data has revealed with stunning precision how fractures often grow hundreds of feet above a well or intersect with adjacent wellbores during frac hits. The adoption of fiber optics has helped calibrate fracture and reservoir models while displacing the use of legacy technologies such as microseismic surveys.
The emergence of disposable fiber has further lowered the cost barrier and operational complexities. We are also seeing the use cases for fiber expand into production profiling, leak detection, and it may be possible to use fiber strain data as a proxy for downhole pressure. All of this only points to the continued adoption and innovation of fiber technology.
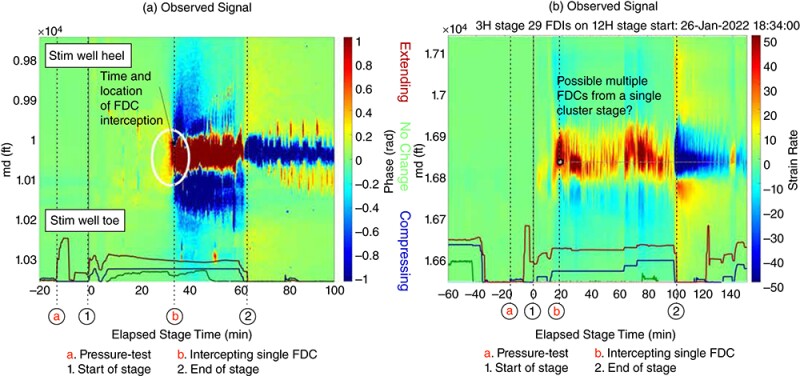
5. Seismic Processing
Advancements made in 3D seismic acquisition and imaging have directly led to major offshore discoveries around the world. This includes Brazil’s pre-salt reservoirs which were not discovered until 2006. Today, these projects represent most of Brazil’s 3.5 million B/D—barrels that would likely never have seen the light of day without a series of critical improvements.
From multi-azimuth surveys to wide-azimuth and eventually full-azimuth surveys, these developments have allowed operators to overcome many of the biggest challenges associated with imaging complex geologies. Many other newer discoveries are owed to the combination of advanced algorithms and computing technologies that by the end of the past decade achieved a massive milestone for the sector by drastically reducing the time it takes to process seismic data from many months to a few weeks or days.
We’ve also seen 4D seismic using ocean-bottom nodes deliver massive value to large offshore projects by revealing the shifting profile of reservoirs as they are produced year after year. The latest iteration of the 4D concept has led to permanent reservoir monitoring (PRM) which involves laying hundreds of miles of fiber-optic cable and acoustic receivers on the seabed—making them the industry’s largest data acquisition systems.
6. Advanced Fracture Modeling
Among the many developments to emerge from the rise of modern hydraulic fracturing is a step change in fracture modeling. The impact of this development is hard to quantify but it has enabled the sector move beyond the constraints imposed by software codes originally designed with conventional rocks in mind. The shale revolution was launched using software that predicted symmetric bi-wing fractures that proved to be too simplistic to rely upon.
By contrast, the latest generation of models account for far more geologic and geomechanical complexity to simulate fracture networks that are more realistic. And as the models have improved and become more believable, they have enhanced the value operators see in running data acquisition and diagnostics programs which creates a positive feedback loop that further enhances model accuracy. As a result, we have seen more and more operators point to calibrated model results as major drivers of decisions such as well placement, well spacing, and total well count per section—all huge determinants of a project’s outcome.
7. Rotary Steerable Systems (RSS)
Introduced to the oil and gas industry in the late 1990s, uptake of RSS was hampered by reliability issues. The industry has largely conquered its growing pains, however, and the technology is advancing along with the wider trend of automation in drilling.
While used in the vast majority of offshore drilling campaigns, perhaps the most significant area of adoption for this technology has been in the onshore horizontal drilling sector in North America where RSS has struggled to shed its reputation as a nonessential luxury. However, thanks to cost reductions and improvements in the technology, RSS has increasingly displaced the use of conventional directional assemblies and is estimated to be used in about 30% of new wells in the onshore US arena.
The embrace of RSS by both onshore and offshore drillers has been a key enabler behind remote directional drilling operations that allow a single driller in an office to oversee operations on multiple rigs at a time. RSS is also considered a critical component to furthering automated drilling efforts.
8. Perforations
The words “more sand and water” could sum up one of the biggest advances made by the unconventional sector in its effort to increase productivity. But maybe what we should really be celebrating is the science that’s gone into making better perforations which drink in all those super-sized volumes of sand and water. Improvements include more reliable and effective “perf guns” and shape charges but the advances go beyond the tools themselves.
Intense industry efforts over the past decade have enabled operators to identify the optimal parameters regarding perf size, orientation, and the number of perfs per fracture stage. These are all understood today as critical factors that can decide the fate of a well and as a result have led to the embrace of concepts like the limited and “extreme-limited” entry which increase perforation efficiency and overall production.
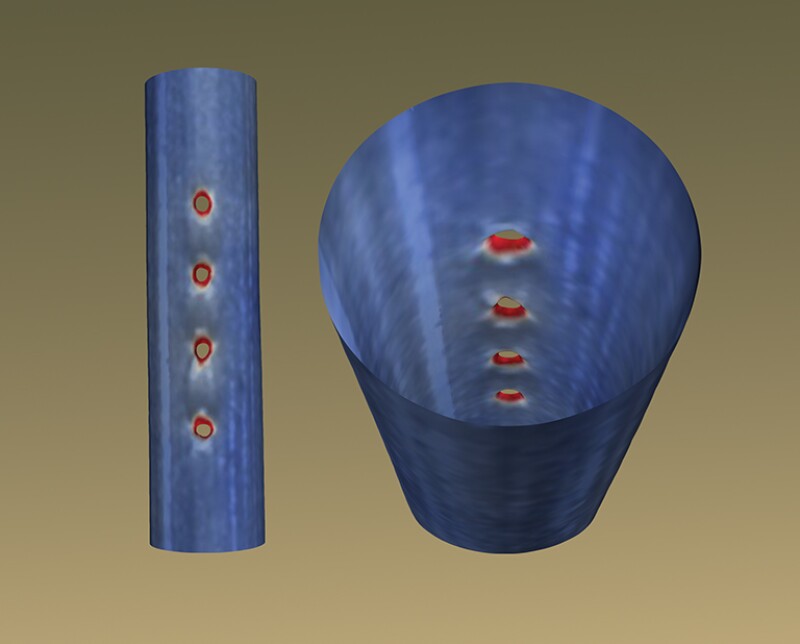
9. Reservoir Characterization
There are few things more critical to success in this business than understanding the rock that you are drilling into. On this front we have seen a number of notable developments that span both the relatively low-cost thresholds of the onshore market and the high stakes of the offshore sector. This includes the adoption of microfluidic technologies that have developed into faster and improved pressure/volume/temperature (PVT) analysis which is viewed as critical to predicting long-term reservoir performance.
Geochemistry has enjoyed a revived interest in the onshore unconventional sector as a way to determine which layers of shale-rock oil and gas are actually being produced from, which aids with well spacing. Other recent breakthroughs include machine learning models that can predict gas/oil ratios in real time based on mud gas returns which is an innovation used mostly offshore today. Bleeding-edge research may soon make it possible to use drill cuttings to access reservoir fluid properties—a breakthrough that would open the door for PVT analysis on every single well.
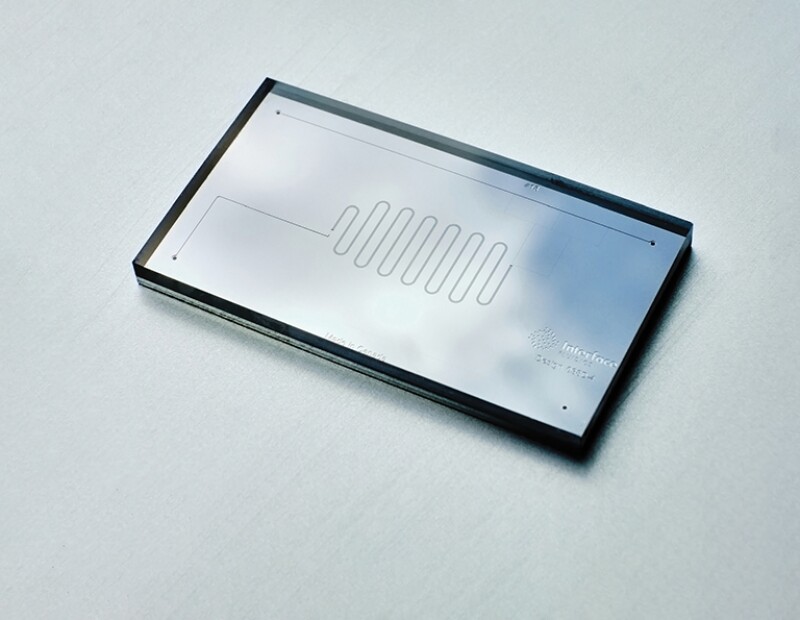
10. Extended-Reach Drilling
One technology that quite literally embodies the industry’s ability to push the limit is extended-reach drilling (ERD) which is often used as a way to access offshore reserves from an onshore drilling site.
The complex and costly method is for many synonymous with ExxonMobil’s and Rosneft’s now severed joint venture at Sakhalin Island. The project began claiming world records in 2007 with the drilling of a 7-mile-long well. Several more would follow including a 9.3-mile-long well drilled in 2017.
The ERD techniques pioneered in Russia’s Far East have now been embraced in the Middle East, especially in Qatar, Saudi Arabia, and the UAE.
In 2022, UAE’s ADNOC set a new ERD record with a 50,000-ft (9.4-mile) well, exceeding the Sakhalin record by 787 ft.
Drilled from an artificial island, the well was the result of many technological advances coming together including gyro-equipped RSS, geosteering, high-speed measurement while drilling, advanced logging while drilling, vibration sensors that protect bottomhole assemblies, batteries that last for almost 3 weeks, and limited-entry stimulation techniques.
There you have it. I believe that the industry would find it very difficult to maintain global supply or add to it going forward without each of these areas of advancement. And as the prognosticators that came before me have done, I wonder what will be on such a list in another 25 years.
I imagine that by then AI will have matured to become an inextricable contributor to all areas of the business. Other promising developments that appear to just be getting underway include megascale carbon sequestration, enhanced geothermal systems, direct lithium extraction from oilfield brine, and the introduction of oilfield robots that will displace the need for human field operators.
And of course, there is likely to be a breakthrough or two that none of us are able to foresee in 2024.