The Environmental Protection Agency (EPA) and numerous states are introducing new emissions regulations which impact oil and gas producers. Additionally, under the pressure of stakeholders, the producers are committing themselves to decarbonize their operations. A large portion of these emissions occur at oilfield production sites. To eliminate these emissions, Pioneer Energy created a new type of skid‑mounted production facility. The technology was deployed on a pad in Weld County, Colorado, and demonstrated elimination of emissions, improved operational efficiency, and an increased crude yield of 11.3%. If adopted by the industry, this solution can dramatically reduce the emissions and carbon footprint of oil production.
The Challenge
There are five populated areas in the US that the EPA currently designates as Severe Ozone Nonattainment Zones. The Denver Metro and Front Range area, which also encompasses most of the Denver-Julesburg (DJ) Basin, is one of these areas, and the EPA is currently working to include the Permian Basin as a sixth nonattainment zone. Oil and gas producers are actively seeking solutions to drill and produce wells while significantly reducing pad-level emissions to achieve attainment. Strategies currently being employed include eliminating crude storage tanks, eliminating natural gas actuators, and consolidating processing from offset pads, each of which offer incremental improvements but do not address the whole problem. Current production facilities use passive means to separate the oil, gas, and water. This incomplete separation results in gas remaining in the crude, and when this gas leaves the crude, it results in fugitive emissions.
The Solution
To address this challenge, Pioneer Energy developed an active separation process called the Emission Control Treater (ECT) as seen in Fig. 1 above. The ECT receives wellhead fluid and uses a combination of heat and gravity in a closed-loop process to separate water, oil, and gas. The system sorts the hydrocarbons much more efficiently than traditional processes, resulting in crude which is completely stabilized, containing no flash gas. An additional benefit is that crude molecules that would be left in the gas instead remain in the crude, increasing its volume. By eliminating the flash gas, and through process electrification, pad emissions are eliminated. Pipeline-quality crude oil is output from the ECT and can be directed straight to the Lease Automatic Custody Transfer (LACT) unit or surge vessel if buffer capacity is needed for the crude midstream provider.
The ECT is emissions-free when run on grid power, contains no gas-venting actuators, and replaces nearly all existing production facility equipment, including high-low pressure separators (HLPs), vapor recovery units (VRUs), gas busters, vapor recovery towers (VRTs), and storage tanks. It is capable of bulk processing and when assembled in parallel with multiple skids, the ECT system can accommodate a wide range of production profiles.
Weld County, Colorado, Pilot Program
Pioneer Energy contracted with Bayswater Exploration and Production to conduct a pilot of the 500 B/D ECT on an eight-well pad in Weld County, Colorado (Fig. 2). The pilot’s objective was to demonstrate continuous operation of the system on an actual production site while demonstrating the key advantages including elimination of emissions, increased crude yield, and simplified operations.
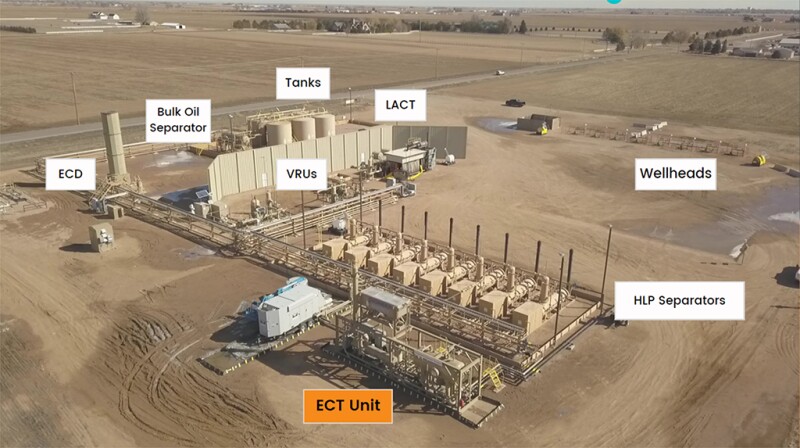
The ECT was connected in parallel with the existing infrastructure, with flow diverted to the system during the pilot operation. The ECT discharged the stabilized oil into the site’s existing bulk oil separator. Following the bulk separator, the crude moves into atmospheric storage tanks and finally to the LACT. A VRU on site also compressed any low-pressure gases evolving from the bulk oil separator and gas-lift compressor knockout.
Data were monitored and collected from various points across the site during the test. One crucial measurement was the pressure inside the bulk oil separator. During conventional operations, flash gas in the crude oil will escape in this vessel, causing its internal pressure to rise. Once it reaches a predefined pressure, the VRU activates and extracts any vapors. These vapors are compressed and sent to the gas sales line.
Composition samples were obtained from several points in the process. These included the stabilized crude at the output of the ECT to determine Reid vapor pressure (RVP), and the sales gas before and during ECT operation to assess the efficiency of the stabilization process and crude volume increase. To determine operational efficiency, frequency of the producer’s field team site visits and the uptime of the site were assessed before, after, and during the pilot.
Results
The ECT was in operation for a total of 28 days during the pilot test, producing nearly 3,600 bbl of pipeline-quality crude oil from seven of the eight wells on site during the pilot. The eighth well continued flowing through its HLP.
The temperature of the unit was adjusted throughout the pilot to test the impact on crude oil RVP. Fluid samples were periodically analyzed and confirmed that the RVP of the crude could be manipulated to achieve the customer,s desired output. An RVP of 12 psia and lower was achieved and held consistently at the ECT discharge.
During the pilot, the pressure inside the bulk oil separator was observed to be consistently lower than what is typically observed, indicating that the crude oil produced very little vapor. This was confirmed with VRU data which showed a 50% reduction in utilization compared to normal operations. We attributed the remaining evolved vapor to the production from the eighth well whose flow continued to be processed by the site’s HLP, and the injection of unstabilized knockout liquids from compression and various points around the site directly into the bulk oil separator. In a complete ECT implementation, these knockouts will be directed instead to the ECT’s inlet for processing and stabilization.
The pilot operated during the coldest time of the year in Colorado when temperatures routinely dropped to below freezing. Before and after the pilot operation, the gas-lift compressor experienced downtime due to the cold weather, resulting in the operations team having to perform maintenance activities on an almost daily basis. Even in these extreme conditions, while the ECT was operational, the number of operations team site visits was limited to a couple of checkups, and the gas-lift compressor did not shut down even once, greatly improving the operational efficiency of the pad.
Third-party compositional analysis of sales gas showed a reduction of energy content from 1,400 to 1,322 BTU/ft3, indicating that crude molecules had been sorted out of the gas and into the crude. This translated into a crude volume increase of 11.3%.
Conclusion
The pilot demonstrated the ECT is a viable solution for wellpad emissions reduction and increased crude oil sales. Enhanced separation and electriciation resulted in systematic elimination of emission sources, elimination of routine flaring of tank vapors, improved operational efficiency, and simultaneously resulted in an 11.3% increase in crude volume. Operational efficiencies observed included improved uptime of the site’s gas-lift compressor and reduced field crew presence on the pad. The pilot proved that by adopting this technology the industry can dramatically reduce its emissions and carbon footprint while improving the bottom line.
Pioneer Energy will be conducting additional trials for operators in other liquids-rich basins in the coming months with potentially larger capacities. Additional design configurations include 250, 1,000, and 2,000 B/D systems which can be installed in parallel to achieve the desired initial production volume.
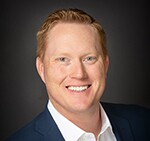
Tyler Pittenger has over 18 years of experience in oilfield completion services, entrepreneurship, and business ownership. He spent the bulk of his career in oil and gas well stimulation operations in Wyoming, Texas, and North Dakota, and holds a BS in chemical engineering from Montana State University.
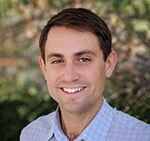
Anthony Maltese is a dedicated and collaborative operations manager with over a decade of experience managing dynamic projects in the oil and gas industry. He served in roles as a fracturing and stimulation field service manager and deployment manager for a large oilfield service company and holds a BS in chemical engineering from Montana State University.
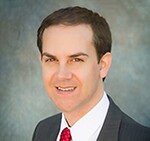
Joseph Palaia IV has been leading Pioneer Energy’s pursuit of business in the flare-gas capture and modular hydrocarbon processing space since 2014, negotiating and closing both domestic and international deals. He holds a BS in electrical engineering from New Jersey Institute of Technology and an MS in nuclear science and engineering from MIT.