TL;DR:
- Incomplete combustion: Occurs when there’s insufficient oxygen for fuel to burn fully, leading to emissions of methane (CH4), carbon monoxide (CO), soot (carbon particles), and other harmful pollutants instead of just carbon dioxide (CO2) and water vapor.
- Causes: Incomplete combustion can result from equipment malfunctions, poor maintenance, or suboptimal operating conditions, all of which disrupt the ideal fuel-air ratio.
- Detection with continuous monitoring: Methane and CO sensors can detect incomplete combustion by monitoring elevated levels of these gases, helping identify and address issues in real time.
Understanding Incomplete Combustion
Incomplete combustion is a significant source of CH4 and CO emissions in the oil and gas industry. Due to the environmental and health impacts, the industry faces increased scrutiny from regulators and the public to reduce these emissions. Continuous- monitoring technologies present a solution by detecting and addressing emissions issues in real time, ensuring better environmental compliance, improved safety, and operational efficiency.
Complete fuel combustion requires a sufficient supply of oxygen to ensure all the fuel burns fully. If the fuel mixture is too rich (i.e., excess fuel) or if the oxygen supply is otherwise limited, incomplete combustion occurs. This leads to the formation of CO, soot, and other partially oxidized compounds (e.g., CH4, nitrogen oxides), rather than the more environmentally benign CO2 and water vapor produced by complete combustion (Fig. 1).
Qube devices offer superior detection of incomplete combustion compared to optical gas imagers (OGI) because they utilize multiple metal oxide sensors specifically designed to detect gases such as CO and CH4. In contrast, monitoring techniques that rely on thermal gradients, like OGI, are less effective at detecting incomplete combustion due to the minimal temperature differential between the emissions and the background exhaust.
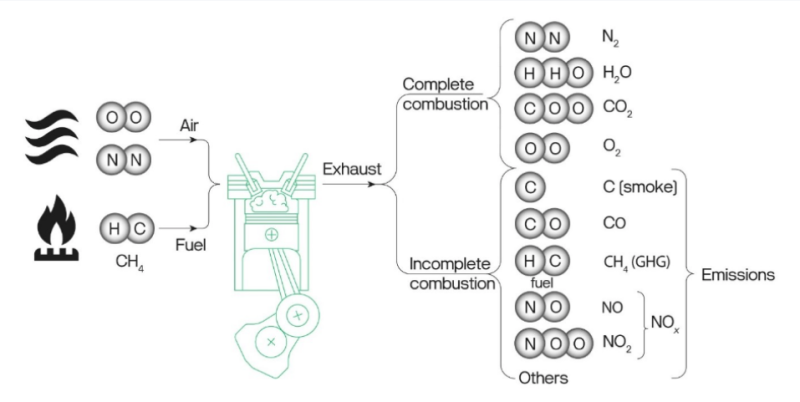
How Incomplete Combustion Happens
Incomplete combustion can occur due to several reasons.
- Equipment Malfunctions: Issues such as faulty spark plugs, clogged air filters, or malfunctioning fuel injectors can disrupt the optimal fuel-air ratio, leading to incomplete combustion.
- Poor Maintenance: Regular maintenance is crucial for ensuring all components in equipment are functioning correctly. Neglect can result in conditions (e.g., clogged filters, blockages, and leaks) that impact the fuel-air mixtures.
- Suboptimal Operating Conditions: Operating equipment under extreme conditions, such as high or low temperatures, can affect the combustion process, leading to incomplete combustion.
The Impact of Incomplete Combustion
The byproducts of incomplete combustion pose environmental and health risks.
- Methane Emissions: Methane is a potent greenhouse gas with a global warming potential of about 29 times more than that of CO2.
- Carbon Monoxide: Carbon monoxide is a colorless, odorless gas that can be lethal at high concentrations.
- Soot and Particulate Matter: Incomplete combustion generates soot (black carbon), which is harmful to both the environment and human health. Soot particles can penetrate deep into the lungs, causing respiratory issues and other health problems. Environmentally, soot contributes to poor air quality by absorbing sunlight and warming the atmosphere.
Continuous Monitoring With Qube Technologies
Qube Technologies offers a robust solution for detecting, quantifying and managing emissions through advanced continuous monitoring (Fig. 2). Qube’s devices support sensors for CH4, CO, CO2, and nitrogen dioxide (NO2), which can be used as a proxy for combustion efficiency (i.e., complete vs. incomplete combustion).
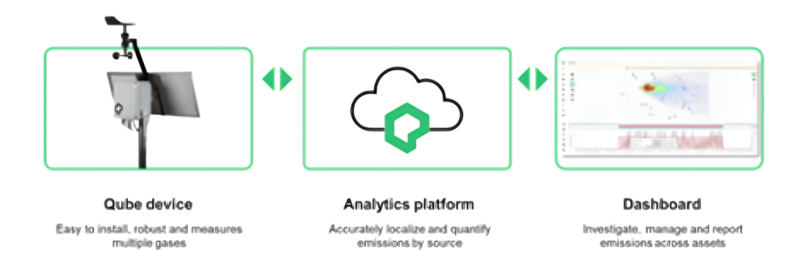
Case Study: Using Qube Sensors To Identify Incomplete Combustion at a Customer’s Site
Background: Qube deployed continuous-monitoring devices with CH4 and CO sensors throughout a customer’s natural gas processing facility. The Qube sensors detected elevated emissions—specifically, increased CO concentrations—and reported this data to the customer via Qube’s dashboard.
Challenge: The customer needed to identify the primary source of increased emissions among several potential sources at the facility.
Investigative Analysis: The customer conducted a thorough investigative analysis of potential emission sources, including:
- Flares: Investigated for proper combustion at the flare tip to ensure minimal unburned hydrocarbons.
- Line Heaters: Examined for appropriate fuel-air ratios and heater efficiencies.
- Heater Treaters: Checked for correct operation including temperature differentials and maintenance records.
- Compressors: Performed detailed exhaust sampling and sensor data analysis.
Solution: Qube Technologies’ detailed CO sensor readings correlated with increased CH4 rates and concentrations, indicating incomplete combustion. Exhaust sampling confirmed the high emissions were due to incomplete combustion at the compressors. Specifically, the investigation identified Compressor 2 on the west side of the site as the primary source of elevated emissions. These findings led the customer to expedite capital project repairs, including adjustments and tuning of the fuel system to optimize combustion efficiency.
Outcome: Qube’s early detection and the customer’s subsequent investigation and interventions resulted in a 61% reduction in methane emissions at the site, thus demonstrating the critical role of precise diagnostics and tailored technical interventions in managing and reducing emissions.
Learn more about Qube Technologies here.
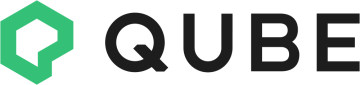