Over the past few years additive manufacturing (AM) technology has grown in popularity as companies explore its potential. Applying layer upon layer of polymers can create objects of almost any shape and geometry guided by design files, and now, recent developments have made it possible to print metal parts and components, making it a potentially disruptive innovation for the supply chain.
AM has already had an impact on other industries such as aviation—Airbus agreed in October to a deal to manufacture polymer parts for use on its A350 XWB aircraft—and now, as oil and gas companies look to adopt AM into their supply chain management, service companies are breaking through with new machines and processes that may facilitate larger-scale production of parts and components in the future. In addition, a new guideline has been established to help bridge the gap between the quality assurance of parts created by an AM process and those created through traditional manufacturing processes.
Additive Manufacturing Qualification
This past November, DNV GL published its first classification guideline for the use of AM in maritime and oil and gas. The guideline was designed to bridge the gap between the quality assurance of parts and components created by an AM process and those created through traditional manufacturing processes by creating a clear pathway for AM certification. The guideline serves as an umbrella document that establishes the overall framework process for qualification and certification of AM products and further points to other DNV GL specific services/documents that are relevant in assessing every parameter that will impact the final product, from the materials used to the actual printing and post-processing.
Brice Le Gallo, DNV GL’s regional manager for Southeast Asia and Australia, said the lack of a guideline was one of the more significant hurdles for more widespread adoption of AM processes. Because there are currently only a handful of AM standards, companies often conduct their own testing to ensure integrity of the equipment, parts, and components. The cost and time needed to conduct these tests deters wider adoption. In addition, AM processes typically incur higher material and machining costs than conventional manufacturing. He said the new guideline will help provide a blueprint that may encourage further adoption.
“Today what we see is that the level of adoption in these industries, maritime and offshore oil and gas, is still quite low. One of the areas where we can really help the industry get the level of adoption increased is on the qualification side,” Le Gallo said. “This is one of the most important hurdles. We think that by bringing appropriate qualification frameworks to the industry, we will see an important increase in the level of adoption. This would then lead to greater volume, which in turn would lead to costs going down.”
The guideline listed some of the challenges involved in qualifying and certifying AM processes and components:
There is a lack of information related to material properties, and a lack of experience and scientific knowledge of AM processes compared to conventional manufacturing.
Risk assessment based on statistics of large-volume historical data does not apply to AM production.
AM processes have a less integrated processing route compared to conventional manufacturing.
Secrecy exists about technology and software/algorithm sources.
Directionality and heterogeneity of AM products can lead to further challenges for certification and testing.
A lack of product responsibility and uncertainty of quality control still exists.
Despite these challenges, companies are still looking to AM as a vehicle for the significant change of certain production and distribution activities. DNV GL received approximately 100 comments from around 160 companies that were asked to comment on the draft guideline. Principal guideline author Sastry Kandukuri said due to the constructive feedback received, it took approximately 2 months to incorporate these comments into the guideline and publish the document.
Kandukuri, a principal specialist of materials for 3D printing and additive manufacturing at DNV GL, said that while multiple processes have been developed for AM, DNV GL chose to focus on the two dominant processes—powder bed fusion (PBF) and directed energy deposition (DED)—in writing the guideline.
With PBF-based technologies, thermal energy selectively fuses regions of a powder bed. Thermal energy transferred from a laser, electron beam, or infrared lamps activates the system, and the powder bed is in an inert atmosphere or a partial vacuum to provide shielding of molten metal. An energy source (either a laser or an electron beam) scans each layer of the already-spread powder to selectively melt the material per the part’s cross section obtained from a digital model of the part. When one layer has been scanned, the piston of the building chamber moves downward while the piston of the powder chamber moves upward. This cycle is repeated layer by layer until the part is completed.
DED processes melt material as it is being deposited. They are predominantly used for metal powders or wire feedstock, but they can also be used for polymers and ceramics. Powder is fed continuously into a molten pool on a previously deposited layer, which is then melted to obtain good metallurgical bonding between successive deposited layers
Fusion-based technologies are ideal for individual parts with fine details, shapes, and contours that are complicated to replicate. They require a longer build time than DED technologies but can achieve higher complexity and a better surface finish, which requires minimal post-processing. In addition, several components of an individual part can be built together. DED technologies are better for companies producing larger build volumes, or companies looking to process at relatively high deposition rates.
Kandukuri said it was important to find an alternative to conventional AM qualification methods that managed the uncertainties related to the implementation of new technology in cases where fitness for purpose could not solely be relied on by demonstrating compliance with relevant standards, guidelines, and recommendations.
“The process makes it possible to identify and analyse the risks associated with new technology and provides evidence that it is suitable for its intended use,” he said. “It can play an important role in increasing the confidence in the new AM technologies and facilitate a faster, more efficient, and more reliable deployment of materials and components.”
In addition to the guideline, DNV GL recently opened its Global Additive Manufacturing Center of Excellence in Singapore, which will serve as an AM R&D hub for the oil and gas, offshore, and marine sectors. In a statement announcing the new center, DNV GL said that the facility will be a “global competence and service delivery center for assurance and advisory services in 3D printing and allied technologies.” It will invest in competence development and will work with local research institutes and industry stakeholders to advance AM adoption through this center.
Through the center, DNV GL is running a collaboration with Sembcorp Marine, SIMTech, and NAMIC to develop and certify laser-aided AM technology in fabricating large-scale structures for newbuild vessels in Singapore.
Siemens Gas Turbine Blades
The implementation of AM parts and components in offshore oil and gas is still at a nascent stage, but some companies have developed processes that may soon have an impact. Early last year, Siemens completed its first full-load engine tests for gas turbine blades using AM technology.
Siemens produces several gas turbine units suitable for use on a floating, production, storage, and offloading (FPSO) facility, such as its SGT-600 and SGT-700 models. Jenny Nilsson, manager of design for additive manufacturing at Siemens and the team lead for the gas turbine blade project, said AM can help alleviate the time and cost issues involved with conventional manufacturing methods. The project team reduced the period of time from the design of a new gas turbine blade to its production from 2 years to 2 months.
Also, she said AM has an added benefit of allowing for greater design flexibility, which can be valuable in manufacturing different variants of the blade before validation. She said Siemens can now manufacture the hardware of different designs and not have to rely solely on simulations.
“With traditional manufacturing, we have boundaries for which angles we can use, which wall thicknesses we can use, and so forth,” Nilsson said. “This is much different from the boundaries that we have for the 3D printing technique. We have a larger freedom of design. We can create more complex geometries, much thinner walls, and much different structures that we simply cannot cast traditionally. It is ‘complexity for free’ as we say sometimes, meaning that we can manufacture many types of very advanced geometries for these types of parts.”
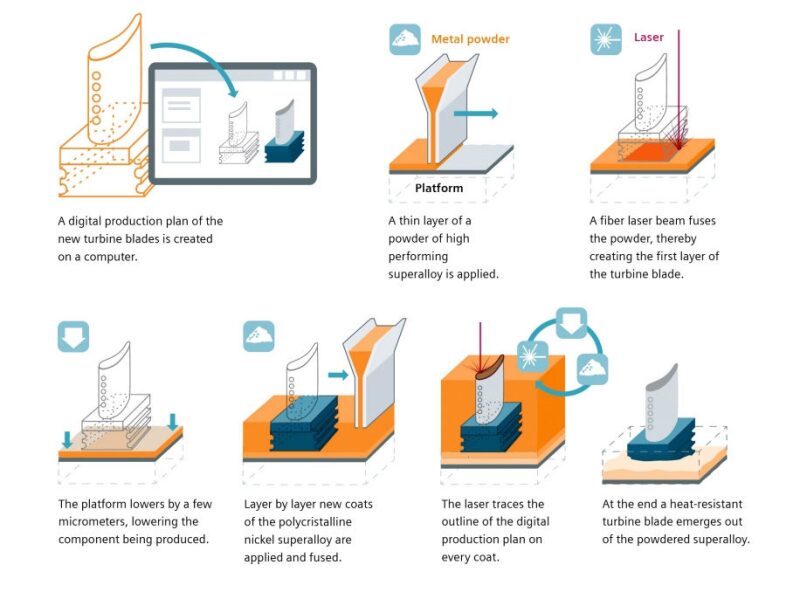
Fig. 1 outlines the process for printing the turbine blades. A digital production plan of the blade is created on a computer, after which a thin layer of a powder of polycrystalline nickel-based superalloy is deposited. A fiber laser beam fuses the powder to create the first layer of the turbine blade, and additional layers of the superalloy are then applied and fused until the blade is completed. The turbine blades were installed in a 13-megawatt SGT-400 type industrial gas turbine and were able to withstand the high pressures, extreme temperatures, and centrifugal forces that arise during operation.
The project team required 18 months to develop the process chain, from the design of individual components, the development of materials, new methods of quality control, and the simulation of component service life. Christoph Haberland, an expert in additive manufacturing for Siemens Power and Gas, said the project team had to essentially start from scratch. It had to identify material that could be processed by 3D printing and could withstand high loads and high temperatures. It also had to design appropriate simulation models for turbine blades and establish quality control procedures.
“Pretty much, we had a blank box in front of us when we started this project, and we had to consider all of the effects before we were allowed to put the blades into the engine,” Haberland said.
The blade design features a revised internal cooling geometry that Nilsson and Haberland said will help decrease the time needed to reduce metal temperatures during operation. Nilsson said efficiency improvement is one of the key drivers for the project.
“When we can manufacture this by 3D printing, we can have geometries that cool more efficiently. We can cool our turbine parts more efficiently, thus we can have a more efficient gas turbine. We can also, by producing these new geometries, improve our fuel flexibility. We can get better at combusting different types of fuels,” she said.
GE’s Project ATLAS
GE has been at the forefront of AM technology for oil and gas operations over the past few years through its GE Additive Division. Recently, the company launched the Project ATLAS (Additive Technology Large Area System) program to develop large additive machines suitable for industries such as aerospace, aviation, and energy, and in November the company unveiled its first BETA machine from the program. Developed over a 9-month period, the machine is a meter-class, laser PBF machine developed to provide manufacturers of large parts and components with a scalable technology that can be configured and customized to specific industry applications.
The BETA machine utilizes a gantry-based architecture. Chris Panczyk, a project leader at GE Additive, said that, while typical powder bed fusion systems print in the entire build area, fill the build area with powder, and treat the area almost homogeneously in terms of airflow and powder distribution, the BETA machine manages airflow, powder, and the laser printing locally, moving that local area around the print volume using a gantry.
Even though the build volume is 1.1 m×1.1 m×0.3 m, the technology behind the BETA machine is infinitely scalable. Panczyk said GE has seen customer demand for larger machines with z-axis capacities of 1 to 1.5 m.
“There are no other physical barriers other than the size in which we can get things like gantries and other things like that,” Panczyk said. “What we’re excited about is that it’s a completely scalable technology and we’re already working on follow-on machines that are larger than this.”
GE said in a statement that the first BETA machines are being evaluated by a small group of the company’s internal customers, and more will be made available for delivery in 2018. Panczyk said the machines the company have built are largely committed and there is a lot of additional demand, so the company is engaging both the customers who have expressed interest and other companies who may be a fit for the technology. He described the BETA machine as a vehicle for learning what the market needs out of a large-format AM platform.
“We’re vetting the customers who have interest,” he said. “Based upon their product need, and based upon their experience and various other factors, we’re determining if they’re good candidates for a BETA machine. If we think they’re good candidates and they’re interested in this, then we will go forward with them. That’s what we’re in the process of doing now, working out some agreements.”
For Further Reading
DNVGL-CG-0197, Additive manufacturing—qualification and certification process for materials and components. 2017. Oslo: DNV GL.