A new SINTEF report commissioned by the Norwegian Ocean Industry Authority (Havtil) assessed risks, challenges, and uses of 3D-printed metal parts on the Norwegian Continental Shelf (NCS). The study authors cited the need for further development of standards, materials, and a qualification system for parts created through additive manufacturing (AM), also known as 3D printing. The authors also found the need for formalizing training, certification, and expertise in the AM supply chain.
The “Use of AM Metal Parts on the NCS—A Risk Perspective” study was conducted between April and December 2024 and published in January. One of the main draws of using AM, or 3D printing, is that it can significantly reduce delivery times, according to the responses from NCS operators surveyed for the report. Other benefits respondents cited included lower component costs as compared to other methods, environmental considerations, and design optimization that may yield better performance. On the other hand, there is concern that 3D printing could yield components with different performance characteristics than components manufactured through traditional methods. This is because 3D-printing methods generate a different microstructure compared to traditional methods due to the differences in heat history, the authors stated.
Because 3D printing of metal parts is a newer technology, the existing industry standards regarding the technology are “notably conservative, emphasizing stringent quality measurement and control,” the study said. There are also not enough available standards in place, supplementary requirements may be vague, and standards published by different organizations may set differing requirements for the same material, according to the study. In the energy industry, API 20S and DNV-ST-B203 are the main standards that address 3D-printed metal parts.
Unfortunately, the study noted, the lack of available standards may make it challenging to create material data sheets (MDS) for components to be used offshore. The study noted Equinor had published only one MDS for 3D printing, and it addressed valves.
Expected Use
NCS operators surveyed for the study said they expect to see a considerable increase in the use of 3D-printed metal parts in the coming years, but that it would depend on the supply chain. The planned uses would be for replacement components or spare parts, as well as production of new parts.
According to the respondents, such parts could be used in primary and secondary construction, gaskets, drilling equipment, and nonpressurized and pressurized components in utility systems. One respondent could see also using 3D-printed parts for pressure-bearing components in hydrocarbon systems, pressure-bearing components in utility systems, and pressurized drilling equipment. While NCS operators were aware that 3D-printed parts would have different properties from those made via traditional methods, they saw variation in corrosion properties as a greater risk than metal strength. The operators expect to set 3D-printing qualification requirements using API or DNV standards or using third-party certification of components.
Materials, Methods, and Properties
Materials that could be used on the NCS with existing 3D-printing methods include stainless steel alloys, steel alloys, titanium alloys, and nickel alloys. Methods for manufacturing metallic components on the NCS include powder bed fusion (PBF) using either laser beam or electron beam, directed energy deposition (DED), and binder jetting.
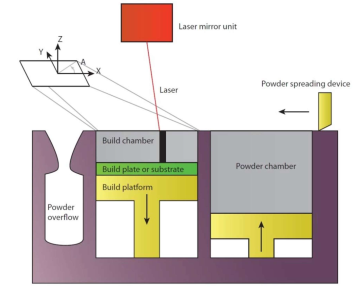
Laser beam PFB uses a laser to selectively melt metal powder by layer to create complex 3D structures while electron beam PBF operates in a vacuum using the electron beam to melt the metal powder. DED, which is used for large-scale parts and repairs, deposits material layer by layer. Binder jetting, which is used for ceramics, metals, and sand-casting molds, consists of a liquid binder being selectively deposited onto the powder bed and binding the particles together.
A current area of active and ongoing research is how processing parameters influence the component’s microstructural evolution and anisotropy, according to the study. More research has been done to characterize mechanical properties of 3D-printed items rather than corrosion resistance, which is of higher importance for offshore use, the authors said.
AM parts could fail in different ways depending on how they were created. For example, in PDF the characteristics of the powder, such as size, quality, and moisture content, all influence the final product, the study noted, while process parameters like power, scanning strategy, speed, layer thickness, and hatch spacing also factor into the ultimate microstructure.
“In particular the fatigue performance of AM metals is significantly influenced by the existence of defects such as gas porosities and lack of fusions (LOF), where characteristics such as size, shape, location, density, and distribution have shown to play key roles in the fatigue performance of AM metals,” the authors wrote.
This means, they went on to say, that considerable effort is needed to mitigate the formation of unwanted microstructures and defects, and this is typically done through process optimization and postprocessing.
The authors said AM parts should initially be used in less critical systems to mitigate risk, but that as the technology matures and the products are better understood, it may be acceptable to use an AM part that is exposed to more degradation mechanisms as a critical component.
Early Stages
The authors suggested that the early stage of AM technology is one reason for the overall lack of available education programs dedicated to the emerging technology, and that this lack may restrict the overall implementation and integration of AM into Norwegian industry. Schools exist for trades like casting, smithing, and other metal manufacturing techniques, but none currently exist specifically for AM.
The early stage of the AM industry is also a reason that supply chains may not be established. While this creates opportunities for companies to supply the energy industry, the authors suggest that untested equipment and personnel increases risk. Respondents in the survey indicated they would aim to establish frame agreements with suppliers and collaborate to increase knowledge and experience.
“Experience shows that good production standards are a result of time and ‘round robin’ cooperation agreements. SINTEF Manufacturing believes that current AM standards need to establish realistic acceptance criteria for supply chains to be easily established, while maintaining risk at an appropriate level,” the authors wrote.