NOV’s pressure control research and development (R&D) laboratory is in a tall factory building with a row of large, thick-walled booths used to test how blowout preventers (BOPs) perform at extreme temperatures and pressures.
During a tour, NOV’s R&D Lab Manager Roger “Dale” Brown made a point of stopping to open a small electrical box. Nearly all of the 24 slots inside were filled with cartridges, each about the size of a deck of cards. The circuits inside them allow engineers to gather whatever sort of data they need from BOP tests and send it along to NOV’s central data recorder.
The box is a tangible sign of the industry’s growing appetite for data as it seeks ways to reduce risk, increase efficiency, and pare costs. For Brown, it represents a big change from how things were done just 5 years ago, when the only data available often were just printouts of spreadsheets and graphs of pressure test data stored in a file folder.
Having a deep pool of data is “like a different set of glasses,” he said, adding that, “I am asking questions I never asked before.”
At a time when sales of stacks of subsea well control equipment as tall as an office tower are all but dead, BOP makers such as Cameron, GE Oil & Gas, and NOV are all working on developing digital tools to address pressing problems facing customers.
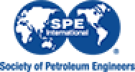