The variables defining drill-bit performance cover a lot of ground. There is a lot of attention given to cutters studding diamond drill bits, but just as important are what is in the rest of the drillstring and the decisions made by the driller.
Companies looking for an edge in drilling performance are working on building tougher drill bits and better ways to control them to avoid destructive moments.
“To make a bit last longer, we have to look at the larger picture and take a systems approach to everything,” said Chris Charles, director of technology at Baker Hughes Drill Bits product line.
Below is a sampling of ideas, many of them presented at the recent IADC/SPE Drilling Conference and Exhibition in Fort Worth, Texas. It shows the range of possibilities from work performed by companies in the field.
Rotating Edge
When a drill bit is running, a relatively small part of the circular diamond edge on top of the tungsten carbide base is coming in contact with the rock as the bit rotates.
Schlumberger’s Smith Bits changed that fact of life with a new design that allows a cutter to rotate while drilling by placing it within a specially designed housing. The Onyx Roll Cutter 360 design is supposed to allow drill bits to stay sharp longer by constantly changing the cutting surface.
In a test by Chesapeake Energy in the Granite Wash reservoir, where the abrasive rock is hard on drill bits, the median life span for the rolling cutter was 1,152 ft, compared with 819 ft for the fixed ones, according to an SPE paper. This compared the results for 45 runs by the rolling cutter and 232 for the fixed ones in a formation with highly variable rock. While the rate of penetration was slightly lower—the median rate of penetration was about 9% less for the rolling cutters—the efficiency was improved by the reduction in the time lost changing drill bits.
A second study cited in the paper compared the performance on 4,500 ft laterals in the unconventional play straddling the border between Oklahoma and the Texas Panhandle. It said the new design lasted about 30% longer and penetrated slightly faster. In one well, only five of the rolling cutter bits were needed, down from seven to nine PDC bits in comparable wells.
The rolling cutters were located at key locations on the drill bit, which otherwise used fixed cutters. The rolling cutters were as reliable as fixed cutters, and the added cost of the new design is “not excessive when compared to the benefit,” said Robert Ford, product champion for Schlumberger’s Smith Bits, who presented the paper at the drilling conference.
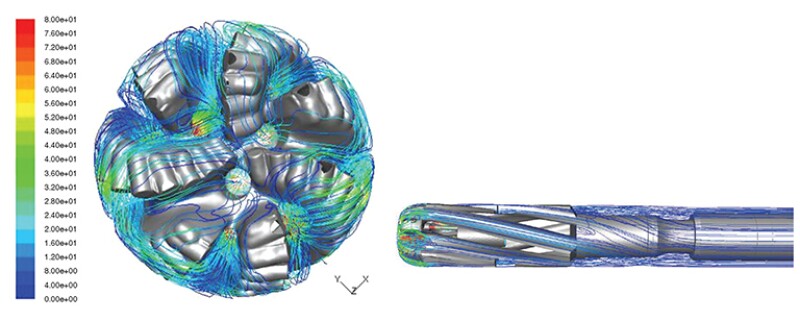
Hard Bodies
The drive to speed drilling by modernizing is leading drillers to add new, more powerful rigs that are leaving their mark on the bodies of drill bits.
“We are getting a lot more energy to the drill bit than in the past and that is having an impact on the drill bit itself,” said Rob Arfele, the manager for fixed cutter drill bits at Halliburton. The large volume and pressure of the drilling fluid used to cool the cutters and clean away cuttings from faster-penetrating bits are also eroding the bodies of fixed cutter bits, shortening their life span.
“We are having to come up with more erosion-resistant body materials,” Arfele said. The starting point is the makeup of the metal used, seeking to increase the strength of composites made up of carbides held together by copper-based binders, which represent about 70% of the heads used. The rest is made of steel, which performs better in certain sticky well environments.
There is also more attention on managing fluid flows to ensure the velocity is sufficient to cool cutters and clear away debris, without eroding the metal around them, which can lead to them falling out. Halliburton is doing computer simulations using computational fluid dynamics, which is also used for tracking flow of air over aircraft wings or water over boat hulls, to visualize how a bit will perform.
Designs based on these insights have had a domino effect of putting a premium on improvements in foundry techniques to allow flexible production of more complex shapes to meet a wide range of customer requests.
Durability matters because the value of fixed cutter heads depends on how many drilling runs it can handle. While the cutters are usually replaced after a single run—the distance varies based on the toughness of the rock, with a 1,000 ft run being a good run in one and a bad performance in another—the heads can last for 100,000 ft of drilling.
Real Data
A lot of formulas have been written to determine how weight, torque, and revolutions per minute maximize drilling performance.
Achieving optimum levels is another thing. What is known is the measures observed on a drilling rig, such as weight on the bit, revolutions per minute, and torque, are significantly different than what is seen by the bit. As the drillstring gets longer, the power at the face of the bit goes down. Another variable is that the drillbit is moving through rocks whose properties vary unpredictably. Instruments are being developed to measure what goes on the drill bit, and wired drillpipe is available, but real-time downhole monitoring has a way to go.
“Without that (real-time drill bit data), there will always be some level of speculation about what is happening downhole,” Arfele said. But the service companies are working to reduce that level of uncertainty by developing sensors that can be placed as near the drill bit as possible for an electronic device to gather better data.
Baker Hughes has recently upgraded a device that fits inside the shank of the drill bit—the threaded tube used to attach the drill bit—adding the ability to measure the torque and weight on bit to its original function, vibration monitoring. It tracks torque and the weight on the bit by measuring the various strains on the shank, said Jason Habernal, product development engineer at Baker Hughes Drill Bits.
Data recorded in the device, which records data that is analyzed after the bit is pulled, is used to see how decisions above affect performance below. Work by Baker Hughes found that the force applied by powerful drives on a drilling rig can be reduced to the horsepower found in a Smart Car in a long horizontal wellbore.
This matters because a failure to apply enough weight on a bit can lead to periods of vibration, and too much can cause it to stick and slip, either of which can quickly cause damage. Better measures of how a driller’s decisions affect bit performance can be used to learn how to drill later wells more efficiently.
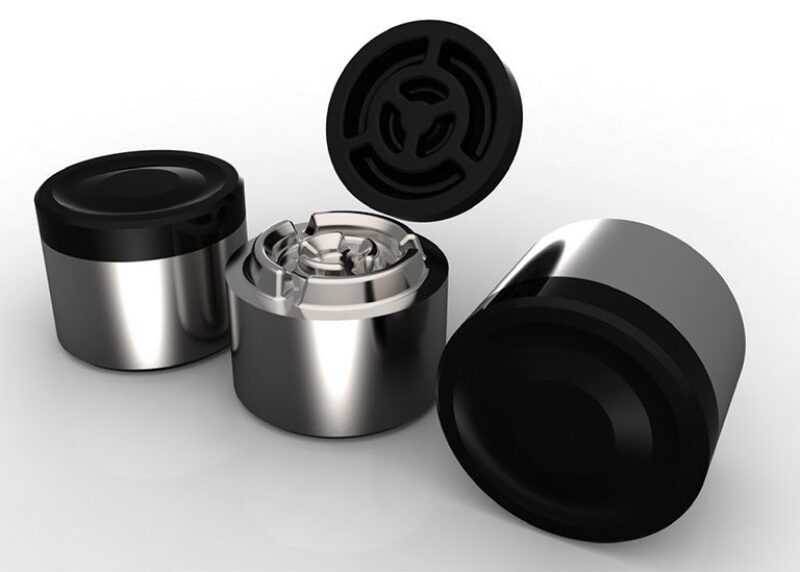
While a good driller will adjust for power losses downhole, the force added to make up for losses requires judgment calls. Some of the same data is gathered by logging tools, which can send data back in real time, but moving the point of measurement back 100 ft results in significantly different results, Habernal said.
Mega Variables
There is a mind-boggling number of drill bit designs. When Baker Hughes set out to create a new bit selection software program, it found more than 6,000 unique possibilities in its product lines.
In the past, it tried, and failed, to create advisory programs to make it easier to match the physical characteristics of the bits with a customer’s needs with results that led it to try a different approach.
The problem is that the number of variables is too long. It could start with the shape of the head, number of cutters, their location, their depth, the angle of the cutters, the metal used to make the head, the hard facing to protect it, and continue from there.
“There are hundreds of features on a bit you can name. It is so complex trying to figure out” how it will perform, said Charles of Baker Hughes. Instead, the company has created a database ranking its offerings based on “how bits perform, not on their features.”
Adding to the difficulties is the many possible interactions when features are altered. Change two things and there is a chance they will cancel each other out, said Chaitanya Vempati, product development engineer at Baker Hughes Drill Bits.
The new system is an answer to customers seeking technical justification for bit choices. Baker Hughes’ rankings mix expert opinions with 10 years’ worth of company data on laboratory tests, field performance, and computer simulations.
Criteria rated include aggressiveness, which determines how fast a bit can drill in favorable conditions, but that trait can be a negative in some rocks; how efficiently it can clean out cuttings; its lateral stability; and durability. Rankings have been based on comments by expert users, past performance-based lab testing, simulations, and field experience. This will be updated as new data comes in.
Coming this summer, the system will be available as an app for mobile devices.
Indented Cutters
The cutters on a PDC bit can be compared with teeth, and Baker Hughes has introduced a design that appears to build on the analogy. It recently introduced a cutter with a depression in the middle of the normally flat table of polycrystalline diamond compact, making the “nonplanar cutter” design rather like a molar.
The goal is to lessen the friction by narrowing the contact area of the rock it is cutting, reducing the heat that can cause the cutter surface to self-destruct. Laboratory testing showed that reducing the surface area of the contact area lowers the temperature by an average of 40% while reducing the force applied by 10%, according to an SPE paper. Temperature matters because a major cause of diamond cutter failure is high heat.
“It is a better cutting edge that lasts longer because we are keeping it cooler longer,” said Anthony DiGiovanni, the scientist doing diamond research at Baker Hughes, who presented a paper on the new design at the conference.
Based on testing in two formations with highly variable rock, the nonplanar cutters were able to drill from 12% to 37% farther, and could also drill faster, with a 10% to 15% increase in the rate of penetration.
For Further Reading
SPE 157039 The Trick Is The Surface—Functionalized Nanodiamond PDC Technology by Soma Chakraborty, Anthony DiGiovanni, Baker Hughes, et al.
SPE 168004 In-Situ Analysis of the Microscopic Thermal Fracture Behavior of PDC Cutters Using Environmental Scanning Electron Microscope by Guodong (David) Zhan, National Oilwell Varco, et al.
SPE 167956 Constructing Difficult Colony Wash Lateral With Innovative Rolling Cutter Technology Improves Drilling Performance by Greg Bruton, Chesapeake Energy, Mark Smith, Smith Bits/Schlumberger, et al.
SPE 16800 Innovative Non-Planar Face PDC Cutters Demonstrate 21% Drilling Efficiency Improvement in Interbedded Shales and Sand by David Stockey, Anthony DiGiovanni, Baker Hughes, et al.
SPE 167917 Characterizing Drilling Applications and Bit Designs Using Common Responses Improves Bit Selection Outcomes by S. Craig Russell, Chaitanya Vempati, Baker Hughes.