The Golden Pass LNG Export project is a $10 billion facility upgrade of the existing liquified natural gas (LNG) terminal in Sabine Pass, Texas. By updating it from an import terminal to an import/export terminal, the facility will help power the world with clean LNG.
Zachry Group was selected to construct the facility which will have an annual production capacity of 16 mtpa of LNG. In addition to needing to meet its capacity goal, the team had to collaborate with an international project team, including the engineering team in Japan, the fabrication team across 18 countries, and the construction team on the US Gulf Coast. When the COVID-19 pandemic limited travel, the team needed capabilities that traditional collaboration methods could not provide.
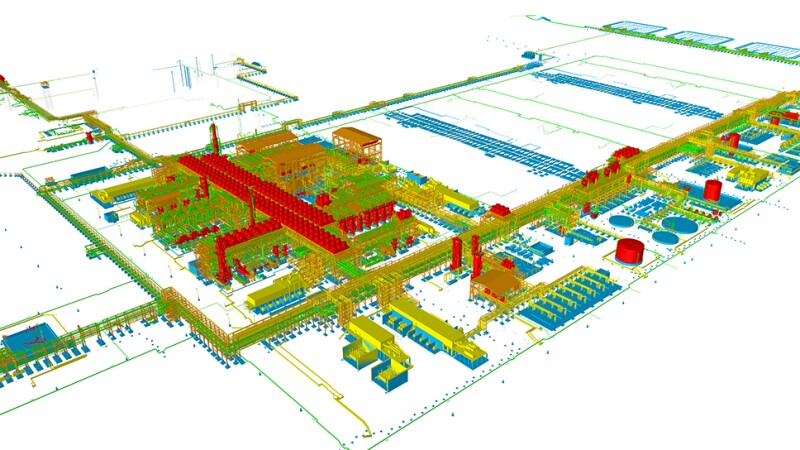
Connecting a Global Project Team
Given the sheer magnitude of the project, the team recognized they needed advanced 4D modeling to visualize construction planning, streamline collaboration, and digitalize project delivery. In addition to the thousands of people involved in the project, the team would be installing millions of pieces of equipment and material, all sourced from global suppliers. The construction team would also be installing more than 1.9 million ft of pipe. The team sought software that would give them the full visibility and deep project insights needed to complete this facility.
Developing Digital Construction Simulations
Having used Bentley solutions for more than a decade, Zachry chose SYNCHRO as its solution. It began by creating a proof of concept of 4D planning with SYNCHRO 4D, allowing the team to collaborate on construction workflows and streamline communication from months to weeks. With SYNCHRO AWP, Zachry leveraged Advanced Work Packaging to improve visibility on project performance throughout the entire project life cycle, removing the need for slow and error-prone manual methods. When COVID-19 lockdowns stopped all travel, they used the 4D software to keep project schedules continuously up to date. Additionally, they created spatial maps for contextual representation of the laydown areas available to the project team and generated a 4D animation of laydown material arrival and departure. These animations provided the team with a real understanding of laydown capacity at any moment in time, as well as the ability to proactively mitigate any associated risk.

Saving Thousands of Hours While Mitigating Risk
Using these applications, Zachry saved 29,050 resource hours for scheduling and 120,000 resource hours on work package development. By establishing a construction digital twin during design and linking models to the schedule, it improved coordination and eliminated travel during pandemic restrictions, reducing congestion and mitigating risks to workers. The integrated digital solution helped leverage data in a connected data environment and optimizing collaboration and communication to make the right decisions at the right time.
The facility is expected to be operational in 2024.