Recently, a new structure located in northwestern Kuwait was drilled and tested with a deep-drilling rig. Formations in this deep structure have very low porosity and permeability. During short-term testing, wells produced oil and gas with, unexpectedly, the highest hydrogen sulfide (H2S) content of any reservoir so far discovered in Kuwait. Because the reservoir was rated as high-pressure/high-temperature (HP/HT) and sour, it was a challenge to test the wells safely and successfully.
Introduction
Jurassic carbonate reservoirs in Kuwait fields are deep, low-permeability, and HP/HT and generally contain sour volatile oil/condensate and gas. Formations containing these deep reservoirs are tight and naturally fractured carbonates. Najmah (NJ), Sargelu (SR), Upper Marrat, Middle Marrat, and Lower Marrat are the five formations proved to hold hydrocarbon-bearing reservoirs. NJ and SR formations are tighter than the three Marrat formations.
The NJ formation consists of limestone at the upper part and shale at the bottom. The SR formation consists mainly of shale and limestone. Both are naturally fractured reservoirs, so fractures play an important role in production. The Marrat formations consist mainly of limestone, occasionally with streaks of anhydrite at the top and with streaks of shale at the bottom. The core analysis of the Middle Marrat formation shows that dolomitization plays a major role for matrix-porosity enhancement, which is responsible for good reservoir character.
As part of an exploration strategy, a new structure in northwestern Kuwait was drilled to deep Jurassic formations. This new structure is a northwest/-southeast-trending doubly plunging anticline and is intersected by a number of longitudinal- and transverse-fault sets. Earlier, a significant discovery of light oil and gas from the new deeper structure was made from an unsuccessful Paleozoic well through re-entry. After the discovery of light oil and gas, three more exploration/delineation wells were drilled to confirm the reserves potential of this structure. Some of the wells are located near the crest of the structure, whereas some are 1.5 km from the crest (Fig. 1).
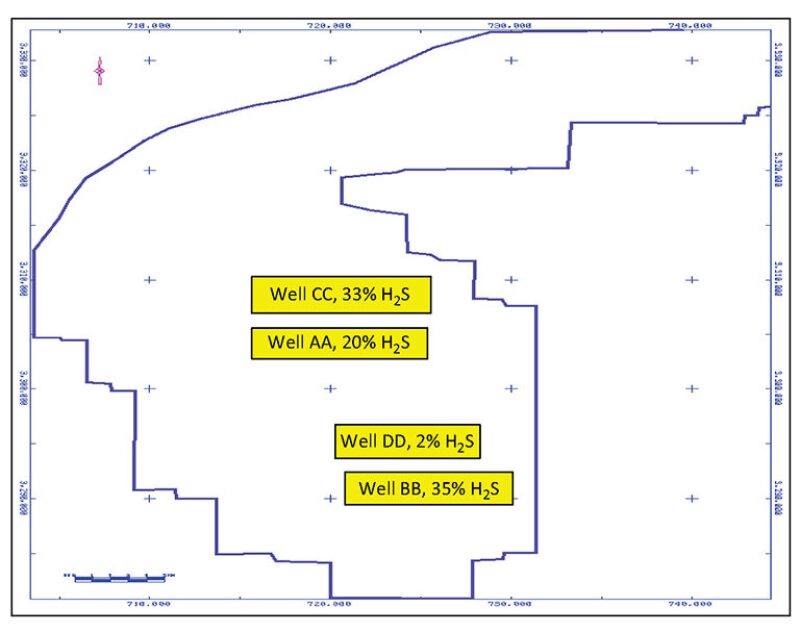
During initial short-term well testing, all wells in this new structure showed positive indication of oil and gas potential. The Marrat, NJ, and SR formations were tested. The Middle Marrat formation showed a positive indication of oil and gas potential, whereas NJ and SR did not show encouraging results.
H2S, a highly toxic and dangerous gas, is present in almost all Jurassic reservoirs in Kuwait, with the concentration normally in the range of 0.5 to 10%. But during testing of the Marrat reservoir, an unexpectedly high H2S concentration was observed (20 to 35%). High H2S levels and HP/HT conditions are the main challenges in testing and completing the reservoir safely. For a review of subsurface and surface equipment used in these tests, please see the complete paper.
Deep-Well Drilling
A deep-drilling rig with 3,600-hp capacity was deployed to drill deeper Jurassic formations (13,500 to 17,500 ft) in this new structure. Recently, three wells targeting deep formations were drilled without many complications. Additionally, one ultradeep well drilled earlier for exploring Triassic/Paleozoic formations was used successfully to test Jurassic formations in this new structure. For standard casing settings designed for the drilling and completion of deep wells, please see the complete paper.
The pore-pressure equivalent of the NJ and SR formations is 16 to 18.8 lbm/gal, and that of the Marrat formations is 14 to 16 lbm/gal. Because of pore-pressure difference and more fractures in the NJ and SR formations, a 7⅝‑in. liner is usually run to isolate those formations, and then the Marrat section was drilled in 6½-in. hole and a 5½-in. liner was run for isolation.
17- to 20.5-lbm/gal oil-based mud was used to drill the 12¼- to 6-in. hole section (13,500 to 17,500 ft). During drilling, self-flow and a number of gas kicks were observed in almost all wells. To control kicks, mud weight was increased to more than 20 lbm/gal. To stabilize the loss-and-gain situation, many cement-squeeze jobs were carried out (with intermittent use of lost-circulation-material pills). Sometimes these unstable downhole conditions did not allow the recording of openhole logs.
For identification of real-time presence of fractures in the deep reservoir, a flowmeter was installed during drilling. This flowmeter was a flowline sensor that uses advanced technology (compared with conventional flow-paddle sensors) in detecting real-time fractures.
Cement-evaluation logs recorded in deeper sections showed very poor cementation behind the casing along the zones of interest in most of the wells drilled in this new structure. Cement repair was attempted in some of the wells, but there was no improvement. In spite of this, production tests of deeper sections were carried out.
Major Challenges/Concerns
Drilling Mud. The deep, high-pressure, naturally fractured formations are drilled with heavyweight mud (16 to 20 lbm/gal), which caused severe formation damage.
Perforation. A deep-penetration gun suitable for HT applications is required for perforating HP/HT wells.
H2S. The presence of H2S concentrations up to 35% in the reservoir fluid and the possibility of surface H2S leaks pose a significant risk to personnel and equipment. Suitable sour-service equipment and dedicated H2S safety equipment are required. Special-alloy materials are required to test and complete the high-H2S-concentration well safely.
Well Killing. Bullheading would require extremely high operating pressures and may not be feasible in a tight formation. Suitable annulus-pressure--operated -reverse-circulating valves are required in the test tool. Heavy muds in the annulus can cause difficulty in operating annulus-pressure-operated tools because of solids settlement, and this may prevent pressure transmission to the tools.
Hydrates. Hydrates can block pipelines and interrupt production. Even if the production is dry, water will condense in the gas as it depressurizes and cools while flowing to the surface. There is thus a risk of hydrate formation, and even a partial blockage would be a serious concern because of the high pressures involved.
Testing Operations
Deep-drilling rigs or workover rigs are used to perform well-testing operations in deep-reservoir zones of interest. The drillstem-testing (DST) technique was used to test all exploratory wells.
On completing well preparation, the target intervals were perforated in underbalanced or overbalanced conditions by use of wireline- or tubing-conveyed perforation. A retrievable DST string consists of two circulating valves, memory gauges, and a packer run on a premium-connection tubing string to the target zone. The string will allow communication between the tubing and annulus. The isolation between tubing and casing was achieved by setting a retrievable packer on the production casing or using a seal assembly in the polished-bore receptacle (PBR).
After perforation, a cleanup flow was performed to determine prestimulation flowing parameters. Pressure/volume/temperature (PVT) samples were captured during the initial flow period. If there was no flow, then coiled tubing was used to displace existing well fluid with diesel to achieve drawdown. Coiled tubing was used in all the wells to spot acid because the injectivity from the surface could not be established. Breakdown acid was used to create initial flow from all deeper formations. The main acid stimulation was performed to improve the productivity index of the carbonate formation by matrix stimulation. On completion of the main acid stimulation, the well was cleaned up again. A main flow was performed by flowing the well through different chokes. PVT samples were captured again during the main flow period. On completion of the main flow period, the well was shut in for a short buildup to obtain information on reservoir characteristics such as permeability and skin. The well was killed by activating an annulus-operated circulating valve, and then the DST string was retrieved to the surface. The tested object was isolated with a squeeze packer. The Marrat formation was tested with a PBR assembly in 5-in. liner, and the NJ and SR formations were tested with a retrievable packer in 7⅝-in. liner.
Fluid Characterization and Reservoir Interpretation
Fluid samples have been collected successfully per the procedure discussed previously from the two tested wells, and PVT analyses have been carried out. Basic PVT properties and H2S content of the fluid at different conditions obtained from the studies are given in Table 1.
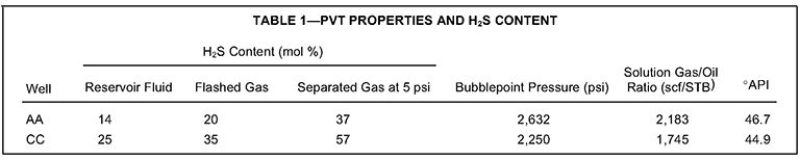
Health, Safety, and Environment (HSE)
The Kuwait Oil Company (KOC) is fully committed to ensuring the health and safety of its people and protecting the environment. KOC’s Health Safety Environment Management System provides the framework for managing all activities.
As discussed previously, high H2S content was encountered during production testing of deep reservoirs. All sour oil and gas produced during testing was flared to the atmosphere through a burner/flare. SO2 is the combustion product of H2S, and it is likely to be present during flaring operations at a drillsite. Continuous monitoring of H2S and SO2 has been performed for the safety of work-site personnel and the nearby public. All applicable safety equipment is installed on-site before starting the job and is tested along with operational equipment.
The following gas-detection/-monitoring and breathing equipment was available at test locations during short-term testing of wells:
- Personal H2S detectors carried by all personnel while on duty
- Fixed monitoring systems
- Perimeter-area gas-deduction system
- Self-contained breathing apparatuses (SCBA)—for 10- and 30-minute durations
To handle any emergency during sour-well testing operations, skilled safety personnel were available with masks at all times. Personnel were also trained in H2S handling, SCBA use, and HP operations. All personnel working on location are equipped with H2S monitors, activated if H2S levels reach 10 ppm.
Results
Four wells were tested in this new structure. The first well in this structure produced 20% H2S, thought to be the highest H2S at that time. When another well was tested, H2S concentrations of up to 35% were found, the highest H2S levels discovered in the state of Kuwait to date. Three wells produced 20 to 35% H2S concentrations out of four wells tested, and one well produced with 2% H2S. All high-H2S-concentration wells were tested successfully; however, the flow period and main acid stimulation in the extremely sour wells were restricted to short durations for safety reasons.
This article, written by JPT Technology Editor Chris Carpenter, contains highlights of paper SPE 167647, “Challenges in Testing and Completion of Highly Sour HP/HT Reservoirs in the State of Kuwait,” by Y. Al-Salali, H. Al-Bader, V. Duggirala, M. Ayyavoo, P. Subban, A.R. Al-Ibrahim, and A. Rajkhowa, Kuwait Oil Company, prepared for the 2013 SPE Kuwait Oil and Gas Show and Conference, Mishref, Kuwait, 7–10 October. The paper has not been peer reviewed.