Despite possessing some of the world’s largest shale-gas resources, China is likely in 2020 to have produced less than half of the 30 Bcm per year in shale gas that the government set as a goal in its latest Five-Year Plan. While such a small volume may make shale production seem inconsequential to China’s overall energy balance, it is clear that when it comes to developing unconventional hydrocarbons, China is playing a long game.
With regard to shale alone, a 2013 US Energy Information Administration study noted that China has the world’s second-largest technically recoverable shale-gas resources at an estimated 1,115 Tcf; the US is first with 1,161 Tcf. Even more to the point, China is one of only four countries (including the US, Canada, and Argentina) that produce commercial volumes of both shale gas and of tight oil.
But it is the lack of efficient technologies and infrastructure that stand in the way of China besting the US and creating its own “shale revolution.” China’s most attractive reserves occur in remote, mountainous areas where, in some cases, shale resources can lie as deep as 3500 m.
In separate papers presented in October during the 2020 SPE Russian Petroleum Technology Conference, the China National Petroleum Company (CNPC) detailed new technologies it is applying to meet some of these challenges.
Paper SPE 202066, coauthored by subsidiaries of CNPC, Downhole Service Company and CCDC Petroleum Drilling & Technology Company Ltd., details the application of enhanced-hydraulic-fracturing technology (EHFT) to raise the effective stimulated reservoir volume (SRV) in the Sichuan shale basin. A second paper (SPE 202062), coauthored by CNPC and Halliburton, offers a case study in tight-oil production in Daqing employing an intensive fracture-cluster-completion strategy using a microemulsion flowback technology.
The Spice in Sichuan Shale
China boasts three shale basins (Sichuan, Tarim, and Yantze), but its principal development focus is in the southwestern province of Sichuan, which holds half of the country’s shale reserves. In developing fields such as Weiyuan, Changning, and Jiaoshiba, producers target the Ordovician Wufeng-Silurian Longmaxi formation. The total proved geological reserves of these three gas fields exceeds 500 Bcm, the authors noted in their paper.
To develop infrastructure supporting industrial-scale operations and to introduce and test new technologies to raise shale output, China has established several national pilot demonstration areas. One of those is the Weiyuan national shale demonstration area in south Sichuan, where the authors quote an annual production of 2.5 Bcm.
Staged horizontal fracturing is the main technology used at Weiyuan and other Chinese shale fields as producers strive to expand the fracture extension area, increase the reconstruction volume, and improve the productivity of single wells.
An analysis of production data from Weiyuan showed, however, that the long-term conductivity of fractures is limited because the length and height of supporting fractures are short. Thus, because of the limited volume of reconstruction, production decreases rapidly and efficiency suffers as pressure declines.
CNPC quoted data from Weiyuan that reveal the average estimated ultimate recovery (EUR) of a single well is 71 to 90 MMcm, and the average recovery rate of a single well is 20.4 to 28.8%. Based on the actual situation of the block of wells, the hyperbolic decline analysis method is applied to analyze the single well with good production continuity: the first-year production of class-I wells decreases by 60.3%; the first-year production of class-II wells decreases by 66.1%; and the first-year production of class-III wells decreases by 67.6%.
EHFT to the Rescue
To resolve these problems, CNPC and its partners implemented an EHFT that optimizes the performance parameters of fracturing fluid and matches different modes of proppant injection. These modes are classified in four major patterns, including modes of proppant injection in long/short slug type and densifying proppant injection in long/short slug type.
The technology enables real-time regulation and control, thus promoting production of a batch of high-yield wells.
The process starts when a pumping plan is made to fit the design goal, based on an evaluation of brittleness and mineral composition plus the interpretation of the results of the natural fracture. The table shows the pumping plan of well A. Then, the modes of proppant injection are adjusted and optimized in real time through the construction curve and microseismic data during fracturing. The hydraulic fracture propagates along the dominant channel during the fracturing process and while there is a risk of the fracture communicating with the adjacent well, the fracture-control technology of multicluster perforating can effectively avoid it.
Through field application, the authors drew these conclusions:
- For reservoirs with high clay content, high-viscosity fracturing fluid is recommended to improve the fracture width and reduce the complexity of construction; modes of proppant injection in long slugs of low concentration can control the construction scale, improve quality of proppant per meter, establish continuous fracture support and improve the long-term conductivity; modes of proppant injection in short slug type can control the fluid loss and avoid the occurrence of complex conditions, which is especially suitable for reservoirs with natural fracture.
- In the process of fracturing, the combination of various modes can achieve good results through real-time analysis and judgment.
- The effectiveness of EHFT is verified by construction parameters, fracturing curve, and microseismic monitoring. The construction scale (total volume of fracturing fluid) is reduced by 10%; quality of proppant per meter is increased by 10–20%; the fluctuation range of construction pressure is controllable/small; and the SRV and microseismic events are significantly increased.
- The test production of well A, which is the highest in Weiyuan, is 712000 m3 with this technology.
EHFT is suitable for the complexity of shale-reservoir reconstruction. Multiple modes of real-time control can reduce the occurrence probability of complex conditions, improving the effective SRV and achieving efficient fracturing. Most importantly, the technology is feasible and effective at reducing costs and increasing production efficiency, the authors concluded.
Daqing Case Study: Tight Oil
Regarding tight oil, CNPC offered the Russian conference a case study (coauthored with Halliburton) on Daqing, China’s largest oil field and one of the country’s oldest. Considering that Danqing has been on stream since 1960, CNPC has had to develop ever-tighter reserves to maintain production. The case study targets Block Long26 and its outskirts of tight-oil wells, located in the unconventional reservoir Song Liao basin in northeast China.
In the paper, CNPC and Halliburton lay out an alternative fracture completion method and enhanced-flowback technology to improve the efficiency of the fracture-completion strategy and post-stimulation flowback. This reduced operational time and related costs.
Optimized fracture-cluster spacing length was determined based on the operational-time efficiency and engineered-fracture-completion design. Laboratory testing was performed to select fluid recipes, and field trials were performed for the correlated custom-made microemulsion technology, which enhanced post-fracture flowback to shorten operational time and increase the return-on-investment ratio and production. Field results and post-fracture-completion production are promising, the authors concluded.
As regards the formation properties of the target pay zone, the reservoir properties of Block Long26 vary. Average porosity is 11.5%, ranging from 10 to 15%. Average permeability is 0.34 mD, ranging from 0.1 to 0.5 mD. However, the outskirts have less promising reservoir properties, the case study noted.
Within Block Long26 and its outskirts, dozens of horizontal wells have been drilled, most of which are cased hole, using a two-cluster fracture-completion strategy. The table presents typical well-fracture-completion information.
Plug-and-perforation (PnP) fracture and PnP net fracture are the names of major completion methods used with fewer openhole multistage (OHMS) fracture completions. Average fracture perforation cluster-spacing length for a single-treatment stage is between 60 and 180 m; the major ones are 60 and 80 m. Single-stage pumped sand volume varies from 0.38 to 1.06 m3/m, and pumped fracture-fluid volume varies from 5.14 to 16.62 m3/m (total volume of fluid and sand pumped divided by lateral length). After stimulation, daily oil-production rates vary from 0.5 to 9.3 tons, and water cut also varies. The flowback percentage varies as well.
Several post-fracture-completion production surveys have been applied in the Daqing field, Block Long26. The most popular completion strategy applied in this field involves using less than three perforation clusters in each fracture stage, applied using multiple, horizontal fracture stages, with longer and (normally) much greater fracture spacing length, thus requiring fewer fracture-cluster treatments along the horizontal laterals. After stimulation, normally, additional days are necessary to observe the oil drop showing; thus, alternative flowback technology is necessary to enhance post-stimulation flowback to help improve the return-on-investment ratio.
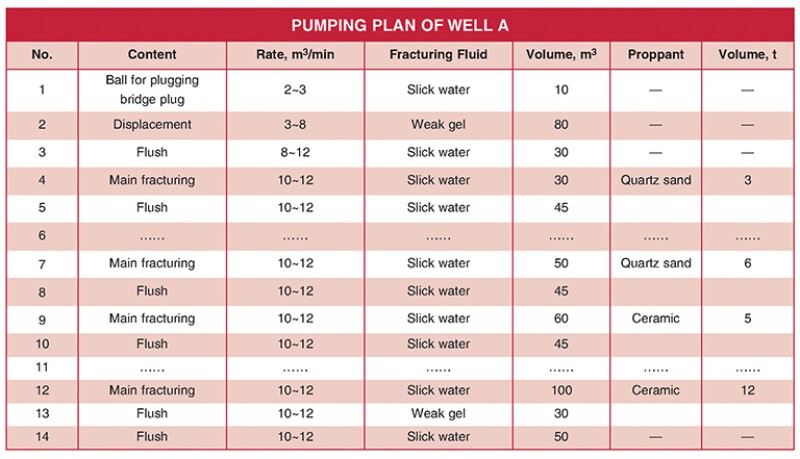
Discovering a Better Way
Limited-entry-fracture and/or extreme-limited-entry-fracture technology were part of the intensive fracture-cluster-completion strategy to benefit fracture completion and production. Field operations involved doubling the current perforation and fracture clusters in one fracture stage. Laboratory methods were used to select the appropriate microemulsion additives to form a fracturing-fluid recipe to aid oil production and enhance flowback.
Typically, to produce reserves economically in tight-oil reservoirs with low permeability, horizontal wells are necessary with multiple-stage hydraulic fractures located transversely along the laterals. Block Long26 and its outskirts are among the most important tight-oil reserves in the Daqing field. This formation has low permeability and low pressure and porosity values.
In Block Long26 and its outskirts, previous fracture-completion strategies that have been employed are OHMS fracture completions and cased-hole multistage fracture completions. Only cased-hole multistage intensive fracture completions are discussed in the paper. The completion strategy applied in this case study application involves more intensive perforation clusters and cluster-spacing length in one fracture stage, which provides improved completion and production, both economically and technically, for the entire well, the paper noted.
Microemulsion flowback technology discussed in the paper refers to a custom-selected-fluid recipe using microemulsion mechanisms to “wash out” the oil adhering to the rock surface and aid flowback, which helps increase production with less damage to the reservoir.
To help improve the efficiency of the fracturing treatment, applying and integrating limited-entry and other techniques can be used as part of an intensive fracture-cluster completions strategy. For the intensive fracture-cluster strategy discussed, the initial perforations were targeted where friction loss was 1,500 to 2,000 psi. Because perforation friction is dynamic during fracturing, the operator maintained a minimum perforation friction above 1,500 psi and more than six fracture clusters within each stage.
The authors cited Crump and Conway (1988), who recommended a higher differential pressure in their discussion of an extreme-limited-entry technique. With respect to the intensive completion strategy discussed, the target was to evenly divert fracturing fluid to all the fracture initial points (intensive clusters) within a single treatment stage. To achieve this, a specially designed perforation strategy to maintain friction pressure was necessary. Secondly, considering dynamic status during the entire fracturing operation required the use of diverter technology. Thirdly, it was important to ensure the maximum surface-pumping rate was achieved without exceeding the allowable surface-treating pressure with so many fracture clusters.
During fracturing, normally, perforation rounding and diameter erosion occur when sand/proppant-laden fluid passes through. Some authors have recommended increasing the pump rate during the operation to maintain perforation friction, as operationally practical during the operation. Lagrone and Rasmussen (1962) discuss that the best results are obtained by maintaining maximum friction during the treatment.
To achieve such perforation goals, it was more practical to pump a diverter to maintain friction with more fracture clusters. Another consideration was that, because there was less fracture-cluster-spacing length, some of the fracture clusters initiated later did not take fracturing fluid. Therefore, pumping diverter was one of the more practical operational considerations that, combined with a good engineering design, helped achieve a better limited-entry-fracturing application. Lastly, ensuring the maximum surface pressure allowed was considered to help ensure the operation was executed smoothly.
In this case study, data history from offset wells was used to investigate the following:
- Well performance with varying cluster spacing within one fracture stage and the entire lateral.
- Workable cluster-spacing length within one fracture stage and the entire lateral.
- Number of perforation holes and perforation clusters within one fracture stage.
To develop an improved flowback method, a laboratory study was performed of the necessary materials to aid fracture-fluid-additive selection and optimize the fracture-fluid recipe. Reservoir characteristics were considered, such as formation oil, produced water, formation rock-drilling cuttings, and others related to alien materials, to describe the stimulation fracturing water, fracturing additives, and proppant.
Nanofluid materials and chemical additives were used during laboratory testing to create a workflow loop. Column flow tests, emulsion-breaking tests, fracturing-fluid and formation-fluid compatibility tests, water analysis, and X-ray spectrometry analysis were all used to help develop an in-house microemulsion flowback technology.
Field-operation trial results showed a good correlation with the in-house-engineered solution. Compared to previous completion strategies, the intensive fracture-cluster-completion strategy is better from a field operations performance perspective. Also, field trials demonstrated that the specified microemulsion technology helps improve well production and flowback.
The authors concluded that they had successfully developed an alternative completion method for Block Long26 and its outskirts. The paper demonstrates that well-prepared, in-house-engineered solutions are valuable for improving the efficiency of field operations. Laboratory tests, field trials, and data analysis were integrated to develop microemulsion flowback technology to help improve post-fracture-treatment flowback.
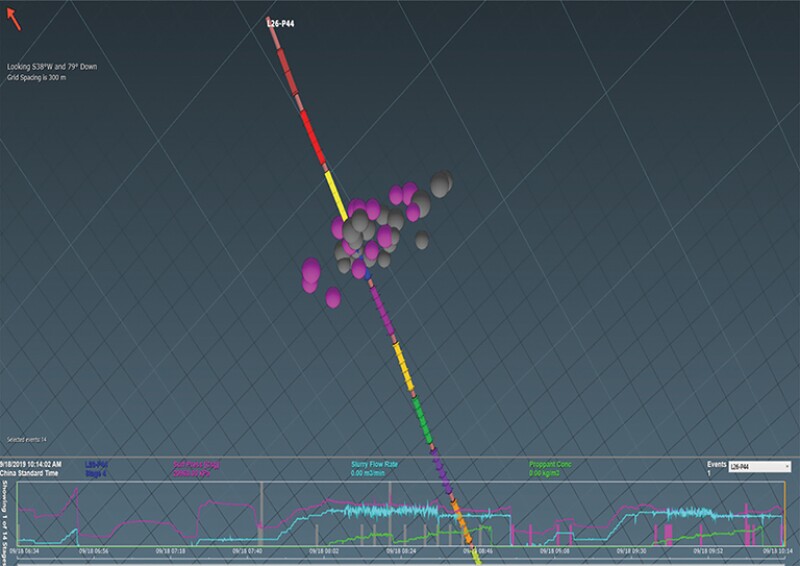
For Further Reading
SPE 202066 Fracturing Technology of Real-Time Control Guarantees Highly Efficient Exploitation of Shale in Weiyuan Gas Field, SW China by L. Zeng, Y. Zheng, and L. Zou, Downhole Service Company, CCDC, CNPC.
SPE 202062 Intensive Fracture-Cluster-Completion Strategy Using Microemulsion Flowback Technology in a Daqing Tight-Oilfield Application: Case Study by X. Yang, B. Qiu, D. Qi, et al., CNPC Daqing; and S. Zhou, Z. Wang, and R. Han, Halliburton.
SPE 15474 Effects of Perforation-Entry Friction on Bottomhole Treating Analysis by J.B. Crump and M.W. Conway.
API-62-182 Better Completion by Controlled Fracture Placement Limited-Entry Technique by K.W. Lagrone and J.W. Rasmussen. Paper presented at the Drilling and Production Practice, New York, New York, January 1962.