Integrity management involves availability, access, and the analysis of necessary information. Even though you identify what is wrong, you need someone who is able to correct the issue and who has the correct spare part. Operators are focused on maintaining production and they prefer to conduct maintenance at planned intervals. When things start to fail, procedures exist for whom to call, how to troubleshoot, and what to do next.
The goal of a condition and performance monitoring (CPM) system is to detect irregularities and the details associated with them before a production alarm situation is reached. That way, the appropriate action can be taken to ensure equipment availability (Fig. 1).

The increase in field complexity and the decrease in the number of control room operators makes it necessary to think differently when it comes to integrity management. Integrated operations combine the operator and vendor in a common team for troubleshooting and solving issues. CPM is a solution developed by FMC Technologies to avoid unplanned production stops.
How It Works
Data collectors receive directly tagged information from subsea control systems. While the topside control system is primarily focused on production critical data, the CPM data collector also assesses equipment performance and internal housekeeping data from smart instrumentation and the control system itself. The data is also streamed to a location where the operator and the support organization can access it. The CPM software performs a combined analysis on the data stream and on historical data to present a picture of the current condition and performance of the field. All data is added to a historical database for later access. The graphical user interface is designed to help fault-finding and to enhance understanding of the condition of the equipment. The analysis process uses steady-state and dynamic models of the equipment performance to detect changes. Knowledge from the customer support organization and vendors is used to develop algorithms targeting relevant known failure modes and performance issues.
While the CPM system captures and validates all available data from the subsea and applicable topside systems, the following modules have special focus:
- The hydraulic elements of the subsea control system
- The electrical elements of the subsea control system
- Hydraulically and electrically operated valve and actuator performance
- Chokes and injection valves
- Subsea pressure and temperature sensors
- Multiphase flow meters
The analysis done by the different CPM modules is represented as a technical condition index (TCI). The TCI is a normalized value characterized as a percentage that represents the condition and performance of a given component. TCIs can also represent groups of other TCIs in which either the average or the worst-case values of the sub-TCIs represent the group. For example, a choke TCI will be based on sub-TCIs for the production performance and for the mechanical behavior of the subcomponents. By tuning the aggregation rule, the severity of an issue can be made more or less visible at the top level TCIs. This way of organizing the results makes it easier to spot incidents and find the cause at both the field level and at the level of each component’s TCI.
Case Study Examples
A field in the North Sea has been using the CPM system for about one year. During that time, the system has detected one major issue and has been a valuable tool in troubleshooting several others.
Router Module Leakage. A subsea router module is the connection point between the control umbilical and the distributed well and manifold control modules. Because of a weakness in a fiber penetrator, the pressure inside the module started to increase (Fig. 2). At installation time, the pressure was about 0.96 bar (13.9 psi), but at the time the CPM system was installed, it had risen to 1.06 bar (15.4 psi). The CPM system was able to detect and verify the problem 3 months ahead of the first sign of functional failure.
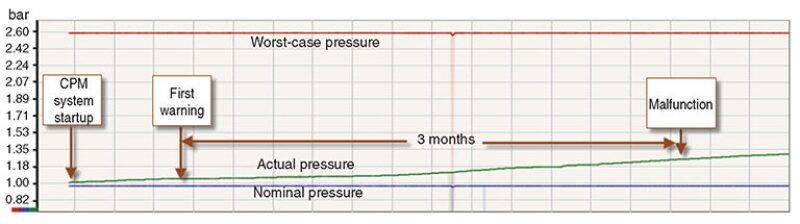
At the time when the module actually malfunctioned, the pressure had risen to 1.3 bar (18.9 psi). During the 3-month period preceding that, after the problem was first identified, the operator was able to plan for an intervention and the vendor could continue to track the severity in real time and using historical data provided by the CPM system.
Choke Issues. Chokes are critical components on a well, but are sensitive to what is being produced by the well. By using mathematical models describing choke performance at current conditions, spurious behavior can be detected before it becomes a problem.
In two specific situations, the CPM system helped troubleshoot problems with production chokes. Both had performance issues in which opening commands had little effect on flow rate. The problem was identified by using a real-time comparison between the current and as-installed performance. By correlating the information with the mechanical behavior of the choke during operation, the reason for failure was identified. One choke had a damaged cage that made the flow rate partially independent of opening, while the other choke had a partially stuck cage that did not react to opening commands.
In addition to detecting the problem by identifying the changes in performance of the chokes, the CPM system also provided the engineer with the data necessary to diagnose the causes of the problems (Fig. 3).
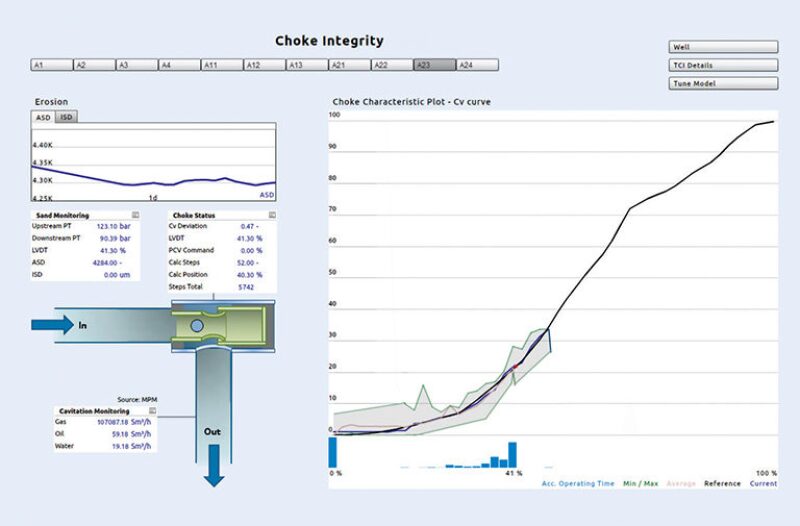
Subsea Hydraulic Control System Leakage. Topside pumps provide pressure to operate hydraulically operated subsea valves. Small directional control valves (DCV) in subsea control modules enable either pressurization or depressurization of an actuator for a given valve operation. DCVs can stop in a middle position so that the hydraulic system leaks from the supply side to the discharge side. These leaks can be so small that the discharge side flow meters do not detect the flow. This makes it challenging to identify the leak and to detect which DCV is leaking.
After an emergency shutdown, selected production wells were restarted according to normal procedures. Initially, each valve operated according to the procedure; however, after some hours the CPM system reported an abnormal consumption of hydraulic fluid. The topside low-pressure pump was running more frequently than normal. No valve had been operated since starting up after the shutdown, so the only reason that could be for this behavior was a leakage. The CPM module tracking the hydraulic consumption reported an increased consumption of hydraulic fluid, but the location was not detected automatically because of the low leakage flow rate. In the CPM system, each valve operation was logged, and by combining this information with the different DCV differential pressures, the correct valve was quickly identified and the leakage was stopped.
Diagnosing and correcting a similar problem would have taken several days or even weeks to assess and correct without the CPM system, whereas in this case, the analysis was conducted in one day and the solution was implemented the next day.
Conclusions
The benefits of CPM systems are clearly illustrated by the examples provided from the North Sea field. These examples show the importance of getting the right information to the right user as early as possible. While the topside operators in the control room focus on production, the complexity of a modern field and the amount of information available make it necessary to have separate systems and users focusing on subsea integrity management.
Issues offshore seldom emerge slowly. They most often happen rapidly, and having a tool that simplifies the troubleshooting process and helps the user quickly isolate the original cause is important. This allows for less disruptive proactive maintenance that provides operators with more confidence and trust in their equipment.
Reference
Andersen, T.M. and Rasmussen, M. 2003. Aging Management: Monitoring of Technical Condition of Aging Equipment. Paper presented at ICMES, Helsinki.