Ultra-high-pressure/high-temperature (HP/HT) wells are currently being drilled in the Gulf of Mexico on the shelf and in deep water. Many of these wells have a total depth in excess of 30,000 ft, where reservoir pressures and temperatures approach 30,000 psi and 500°F, respectively. There are currently few packer-type devices that are considered fit for service in these applications. This paper gives an overview of the latest developments in how advanced finite-element-analysis (FEA) tools are used to verify, optimize, and validate ultra-HP/HT completion and production tools.
Introduction
The classification of HP/HT reservoirs has varied over time. In the past, HP/HT fields were attributed to any condition of greater than 10,000-psi pressure and greater than 300°F temperature. But over the last 20 years, equipment has become widely available for pressures below 15,000 psi and temperatures lower than 350°F; therefore, those fields were no longer classified as HP/HT fields. HP/HT conditions were defined as having pressures between 15,000 and 20,000 psi and temperatures between 350 and 450°F. Ultra-HP/HT conditions were defined as having pressures between 20,000 and 35,000 psi and temperatures between 450 and 550°F. Fig. 1 is the visual representation of the latest HP/HT designations, which were reached by common agreement among oil operators and service companies.
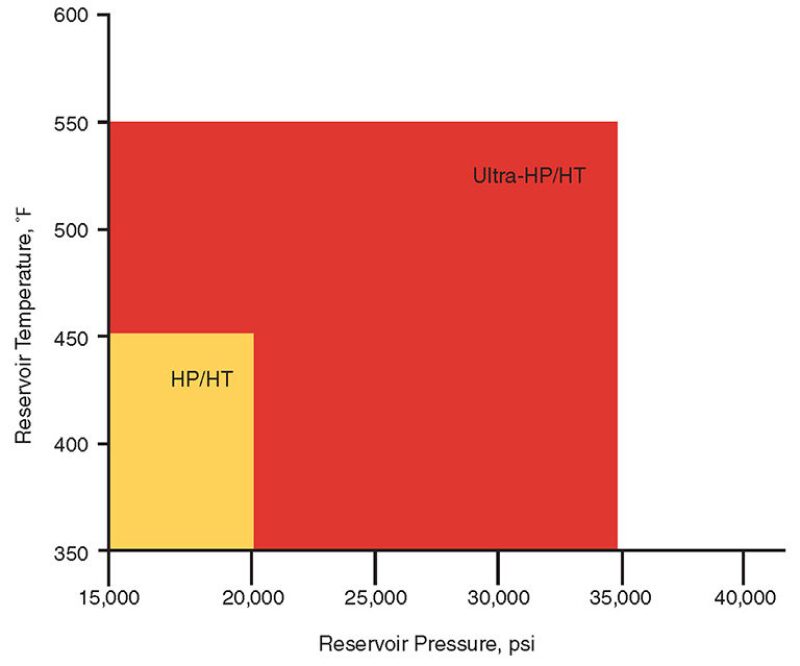
There are several technological challenges that must be overcome for downhole service and completion tools to operate successfully in the ultra-HP/HT environment.
- The first challenge is the lack of effective design-verification codes; the realm of ultra-HP/HT is new territory (for a discussion of existing codes, please see the complete paper).
- The second challenge is that there are fewer options for elastic sealing and metallic material for ultra-HP/HT well completion. Ultra-HP/HT fields are always associated with environments that have severely negative effects on elastic and metallic material. Fluoroelastomers are normally chosen because of their superior chemical resistance and flexibility at temperatures up to 450°F. Nitrile was the choice material before fluoroelastomers were available. Fluoroelastomers and nitrile are not applicable as bridge-plug and packer-seal elements at temperatures exceeding 450°F; the elements become pasty, making them extremely difficult to contain with an antiextrusion system. Recently, perfluoroelastomers have been quantified to be used as sealing materials at temperatures greater than 450°F. These stay physically and chemically stable up to 550°F; however, perfluoroelastomer is very expensive compared with conventional seal materials. Nickel alloy was always chosen as the structural material for ultra-HP/HT completion tools, because it has great mechanical strength, excellent ductility, and good corrosion and cracking resistance; however, elevated temperatures (greater than 450°F) could have a dramatic effect on yield strength of the materials. Yield strength is reduced as much as 10% or more in ultra-HP/HT conditions.
- The third challenge is that some operators are now requiring service companies to test ultra-HP/HT completion tools in as-rolled production casing, in addition to maximum machined-casing inner diameter (ID). As-rolled casing is never perfect, and the casing ID profile could vary as much as 0.070 in. in some casings that were measured. In addition, as-rolled casings that come from the operator’s stockpile are corroded, and ID surface defects such as pits and crevices are often visible. This poses the biggest challenge in seal-system design. A conformable and robust backup system for the rubber-seal element has to be well-designed to provide 360° support to prevent element extrusion. This necessitates conducting a comprehensive optimization to reduce development time and high material costs.
Material Selection and Characterization
One of the greatest challenges in ultra-HP/HT completion-tool development is seal-system design, which usually involves elastic and ductile metallic materials because of the limited choice of elastomers that can function at 500°F temperature and in harsh chemical environments. Perfluoroelastomer was chosen as the elastomer seal element because it has the highest temperature rating and it is stable up to 550°F. Perfluoroelastomer was also tested up to 50 days with various well fluids at 500°F, and the change of mechanical material properties met the International Organization for Standardization (ISO) acceptance criteria. Stress/strain curves of perfluoroelastomer at various temperatures, such as 250°F and 500°F, have been characterized by a certified material laboratory. Bulk modulus, thermal-expansion coefficient, uniaxial compression, and tension stress/strain curves have been measured. Nickel alloy C276 was chosen as the seal element carrier and backup system because it excels in all aspects in terms of mechanical material properties and chemical stability in ultra-HP/HT corrosive environments. It has greater than 40% elongation, enabling it to conform well to irregular casing ID when used as a seal-element backup ring to prevent element extrusion. It also has good performance in corrosion and cracking resistance.
Design Verification and Optimization
New elastomers and metallic materials have to be identified and used to break through to the bottleneck in ultra-HP/HT completion-tool development. New design-verification and optimization methods integrated with multiple disciplines in a systematic approach must be adopted to reduce development cost and time to market.
In such an integrated method, -linear-elastic analysis, elastic/plastic analysis, thermal/mechanical coupling, and 3D multibody contact are embedded in every level of the design, and serve as the primary tools for design verification and optimization. This method has proved effective in the development of ultra-HP/HT bridge plugs (500°F; 25,000 psi) and permanent production packers for as-rolled casing (470°F; 20,000 psi).
Component Design. Axial Buckling. Most components in the completion tools are long tubing strings, and often those tubing strings encounter the axial loading more or less during the operation cycles. A tubing-component design with protection against axial buckling has to be satisfied. First, the highest axial compressive loading must be identified. Second, numerical analysis for buckling must be conducted. For simple tubular geometry, there is no significant difference between theoretical calculation and FEA. However, there is no available theoretical formula for the tubing component with section thickness change, cut-out features, and so on. It can be analyzed only by FEA. Fig. 2 above is an example of a critical-buckling calculation for a tubing component with various section areas.
Thermal/Mechanical Coupling. Thermal/mechanical coupling has to be conducted by linear-elastic analysis or elastic/plastic analysis. This procedure addresses two questions. First, how much does the tubing size change because of temperature variance from ambient temperature to 500°F? Size increase and prestress caused by thermal expansion negatively impact the collapse and burst ratings of the tubing that encounters downhole pressure. Second, are expanded components interfering with surrounding components and resulting in malfunction?
Collapse and Burst Under Combined Loadings. The conventional method of designing components to withstand both collapse and burst under combined loadings has been ineffective in designing ultra-HP/HT completion and production tools. A new approach that integrates design of experiment and stochastic study is used for collapse and burst under combined loading.
Subsystem Design. The most critical subsystems in an ultra-HP/HT completion and production tool are the slip system and seal system.
Slip-System Analysis. A reliable slip system is critical to a packer- or bridge-plug-type completion tool. First, a slip system will expand against the casing during and after setting. A good grip on the casing will prevent damage of the seal system. If a seal shifts up and down during pressure reversal, the seal element will be scratched and leaking can result. Additionally, a slip system provides hanging support to the tail pipe after the production packer.
Seal-System Analysis and Optimization. The seal system is an essential part of an ultra-HP/HT completion system. To reduce cost and time, elastic/plastic and hyperelastic FEA was relied upon heavily for design verification and optimization. To be considered as a viable design, the following criteria were met:
- The equivalent plastic strain in the metal insert and maximum elastic/plastic strain in the seal were measured in all models. The equivalent plastic strain in the metal should not exceed the maximum allowable plastic strain, and the maximum elastic strain in the seal should not exceed the maximum allowable strain. All maximum predicted strains for metal inserts and seal materials were measured in the section of material characterization.
- The seal had to set with the minimum required setting force, then withstand specified differential pressure from above and below, with combined tensile and compressive loading from the boost load acting on the tool without packing-element extrusion.
During the seal deployment, the thermal/mechanical-coupling FEA was run to check the following:
- Were the backup rings severely stressed? If so, the backup ring has to be redesigned to accommodate thermal-expansion force during deployment.
- Does the maximum seal outer diameter (OD) exceed the gauge-ring OD? If so, we must modify the seal design to ensure no damage is induced to the seal element during deployment from surface to bottomhole.
The process was repeated until an optimum seal design was achieved. Then a 3D multibody-contact FEA model including as-rolled casing, seal-element system, swage cone, and setting collet was set up to identify the minimum setting force. The 2D FEA model assumed the casing ID was perfectly circular, and the 3D multibody-contact FEA model accounted for the as-rolled-casing ID profile with as much as 0.070-in. deviation from nominal-ID dimensions.
For this ultra-HP/HT seal system for as-rolled casing, the setting force is much higher than it is for a conventional seal system. Consequently, it could cause the setting component to buckle. It is essential to run elastic/plastic buckling analysis on the setting component to ensure it is strong enough to resist buckling during setting and thereafter.
System-Integrity Verification. Dog-leg analysis and noise, vibration, and harshness analysis have to be performed to verify the system integrity and thus determine any potential risks during deployment and production. Design verification and optimization were built into multiple levels; on each level, thermal/mechanical-coupling, elastic, elastic/plastic, and hyperelastic analysis was conducted extensively.
Test Validation
Two products that went through design verification and optimization processes were an ISO 14310 V0-rated 500°F, 25,000-psi permanent bridge plug (Fig. 3) and an ISO 14310 V3-rated 470°F, 20,000-psi permanent production packer for as-rolled casing. For each product, component-level tests and subsystem-level tests were conducted on major load-bearing sections. Then, full-scale assembly tool tests were conducted.

The 500°F, 25,000-psi permanent bridge plug underwent two types of tests:
- It was tested in maximum casing ID with nitrogen as the medium. The maximum temperature was 500°F. Maximum-temperature swing and multiple pressure reversals were applied on the bridge plug. It passed multiple V0 qualification tests per ISO 14310/API 11D1.
- It was tested in as-rolled casing with water as the medium. The maximum temperature was 500°F. Maximum-temperature swing and multiple pressure reversals were applied on the bridge plug. It passed multiple V0 qualification tests per ISO 14310/API 11D1.
The 470°F, 20,000-psi permanent production packer was tested in as-rolled casing with water as the medium. The maximum temperature was 470°F with temperature cycles (470/300/470°F) and multiple pressure reversals in addition to combined tension or compressive loading per ISO14310/API 11D1. It passed modified V3 validation.
This article, written by JPT Technology Editor Chris Carpenter, contains highlights of paper SPE 166231, “Design Verification, Optimization, and Validation of Ultra-HP/HT Completion and Production Tools,” by Guijun Deng, James Doane, Antonio Ruffo, SPE, Goang-Ding Shyu, and Scott Collins, SPE, Baker Hughes, prepared for the 2013 SPE Annual Technical Conference and Exhibition, New Orleans, 30 September–2 October. The paper has not been peer reviewed.