There are more than 100 accumulations in the southern North Sea that are flagged as stranded fields. One of these stranded tight gas fields, the Kew field, has been developed successfully with the use of a subsea well, horizontal drilling, and hydraulic fracturing. Because this was a subsea development well, all the hydraulic-fracturing operations had to be performed with the rig in place. The utmost efficiency of the operations was paramount; otherwise, the economics of the project would be affected negatively.
Well Overview
The Kew field is a gas field, with small volumes of associated condensate, located in Blocks 49/4a, 49/5a, 49/5b, and 49/4c of the UK continental shelf.
×
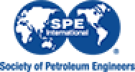
Continue Reading with SPE Membership
SPE Members: Please sign in at the top of the page for access to this member-exclusive content. If you are not a member and you find JPT content valuable, we encourage you to become a part of the SPE member community to gain full access.